New Australian bridge for capital
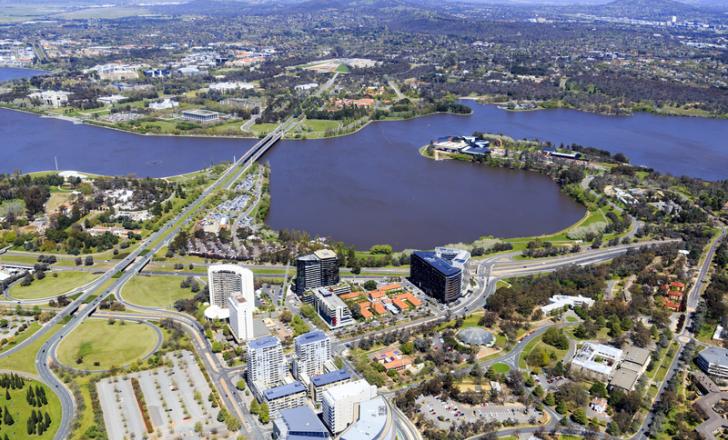
Drivewyze gets data boost from one.network

SWARCO sets up live-lane running in Germany
Earthmoving advance from K-Tec
Made by the KA Group, the firm says that its Land Levelers are the largest capacity drag box blade scrapers on the market. K-Tec’s pull-graders help contractors score a perfect grade on construction haul roads with these effective machines. A smooth haul road allows for faster cycle times and less structural damage for maintaining equipment. The K-Tec 1411 Flex leveler has a 4.3m-width and can drag up to nearly 9m³ of material.
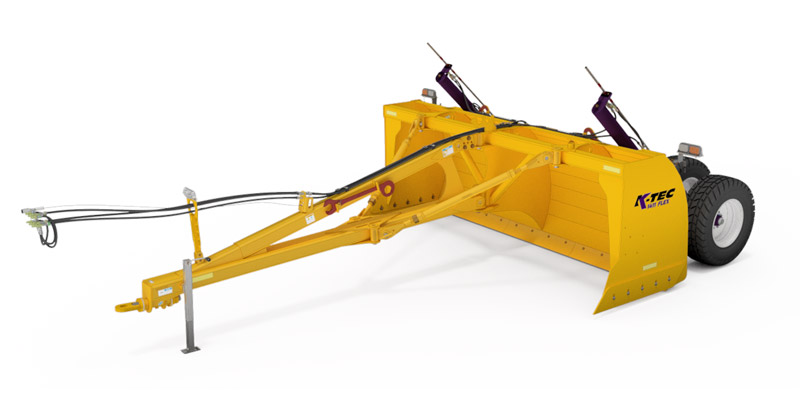
Rokbak’s new haulers launched in the US
“Rokbak is seeing huge demand for its RA30 and RA40 articulated haulers in the US,” says Robert Franklin, Rokbak’s director of sales – Americas. “The US is leading articulated hauler demand globally with huge infrastructure spend. There is a lot of construction activity at the moment around house and road building, so we are keen to meet with customers and discuss how the RA30 and RA40 can help with these projects.”
Booth F8926
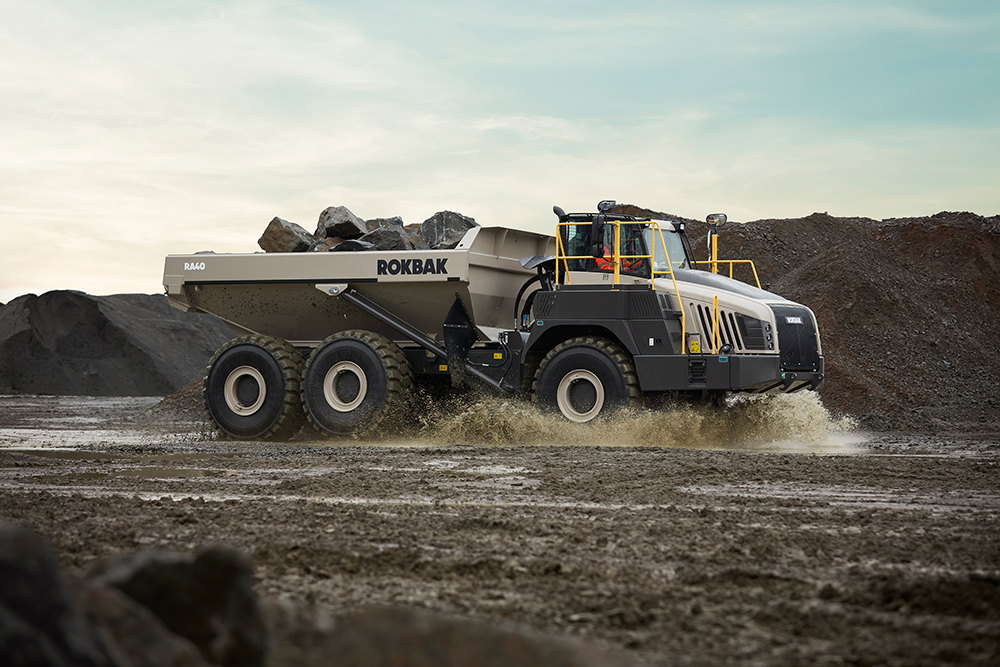
Advanced diesel-electric crusher drive from SBM
SBM’s mobile plant range comprises 12 track-mounted JAWMAX jaw crushers and REMAX impact crushers, capable of 250–800tonnes/hour production. The plant range shares the same innovative drive concept, with fewer hydraulics ensuring fewer failures, lower maintenance and parts inventory costs, and higher availability, says SBM. Overall savings from running the plants can be 40-75%.
SBM is also introducing its new REMAX 600. Based on the SBM hybrid concept, the new 600tonnes/hour impact crusher will soon pave the way for "autonomous crushing", says the manufacturer. Extensive sensor technology, including cameras, records and evaluates the feed material as well as intermediate and end products. In real-time, those values reach centralised digital labs at SBM, where they are further analysed. Necessary adjustments are then made on the ‘digital twin’ of the working machine and re-transmitted directly to the REMAX 600 in the field.
Booth F8926
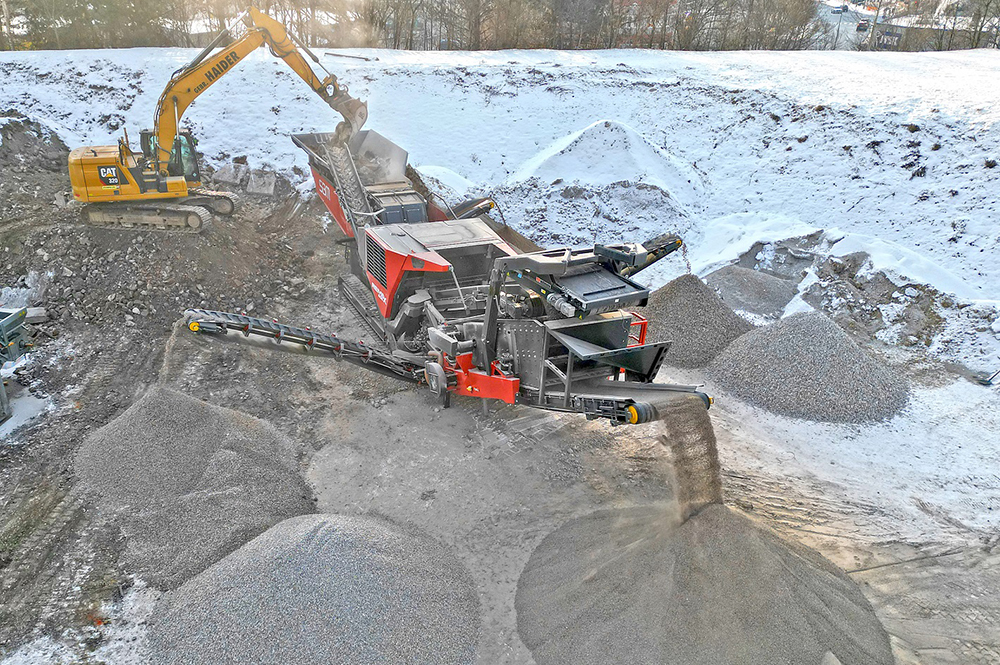
Ammann Company Profile
Ammann compaction equipment is engineered to provide both high-quality results and low ownership costs. This is done through innovative compaction technology that extends product life and reduces maintenance needs.
Ammann asphalt-mixing plants are world renowned for their performance, efficiency, high-quality mix output and innovative recycling processes.
Ammann America is the North American subsidiary of Ammann, a global company based in Langenthal, Switzerland.
An abundance of power in a compact package
Ammann’s soil compaction product line welcomes its most compact single-drum roller yet.
The Ammann ARS 30 Single Drum Roller, at a weight of 3 tonnes and a drum width of 47.2 inches (1200mm), is the lightest and smallest roller in Ammann’s soil compaction product line. The innovative no-rear-axle concept makes the roller compact and facilitates a lower engine location that improves the center of gravity – maximising maneuverability, stability and traction.
The machine is suitable for a wide range of materials and is extremely flexible – particularly given smooth or padfoot drum options. Its dimensions enable easy transport between jobsites.
Despite its size, the roller provides high compaction output through a strong single-stage vibratory system and two frequencies.
Other benefits:
- Intuitive control
- Maintenance-free drum, drive and articulation joint
- Cab or open platforms
Ammann America
1125 SW 101st Road
Davie, FL 33324
USA
+1 954 493 0010
Ammann.com
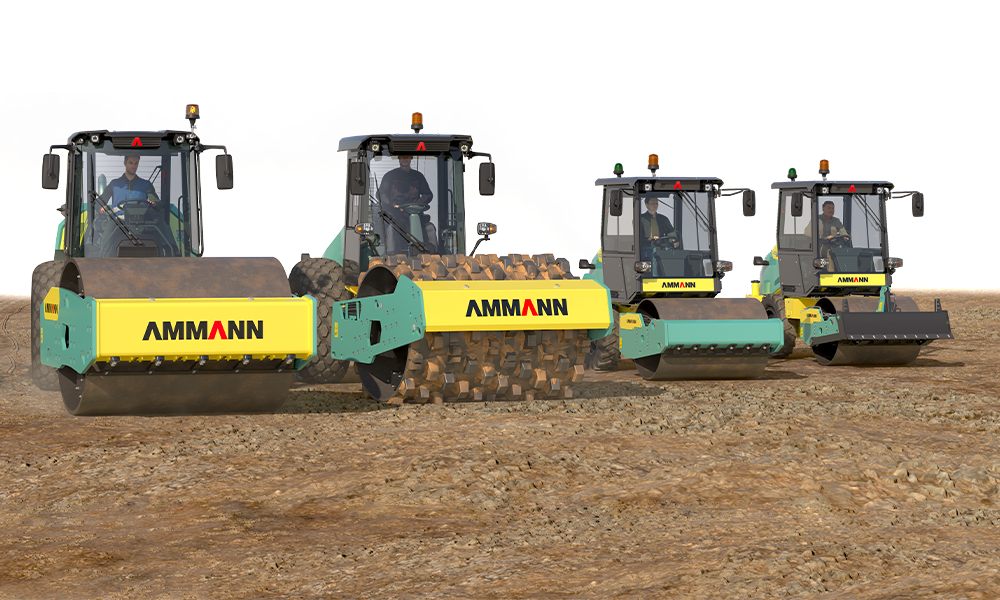
Peru priority PPP project planned
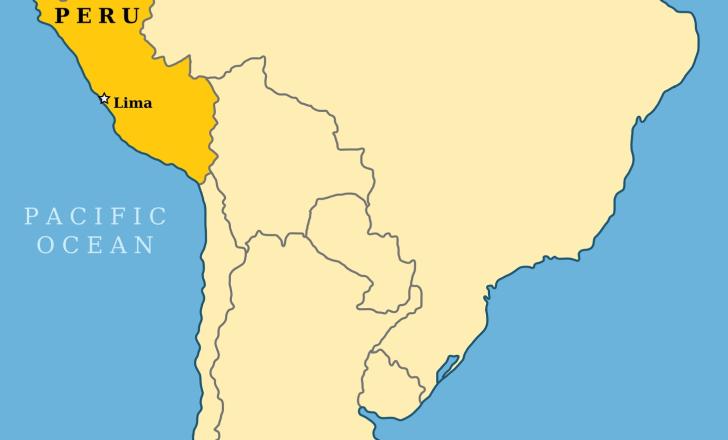
Improvements for UK road link
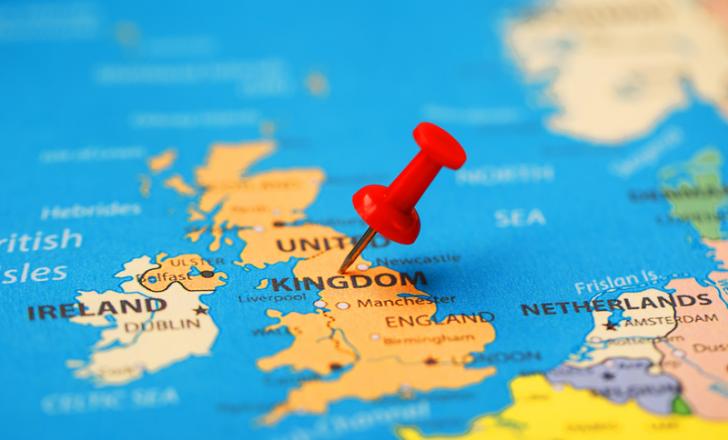
Hydrogen engines for production in 2025

Productive and versatile screening from Kleemann
The powerful mobile screen has been designed to meet demand for use in challenging conditions in different application areas. The firm says that the model benefits from clever plant design and versatile conversion options. It can deliver optimum material flow in natural stone and recycling applications. The large range of screen surfaces and the simple setting of screening parameters make it possible to adapt the MSS 802i EVO to different application conditions. If a fine final product is to be screened from particularly coarse feed material, the plant can be converted speedily from three to two final grain sizes. Further plant advantages include its ease of operation due to its intuitive control and ease of access to machine components. The machine also benefit from the novel H-DRIVE system with the option of an external power supply for emissions-free working.
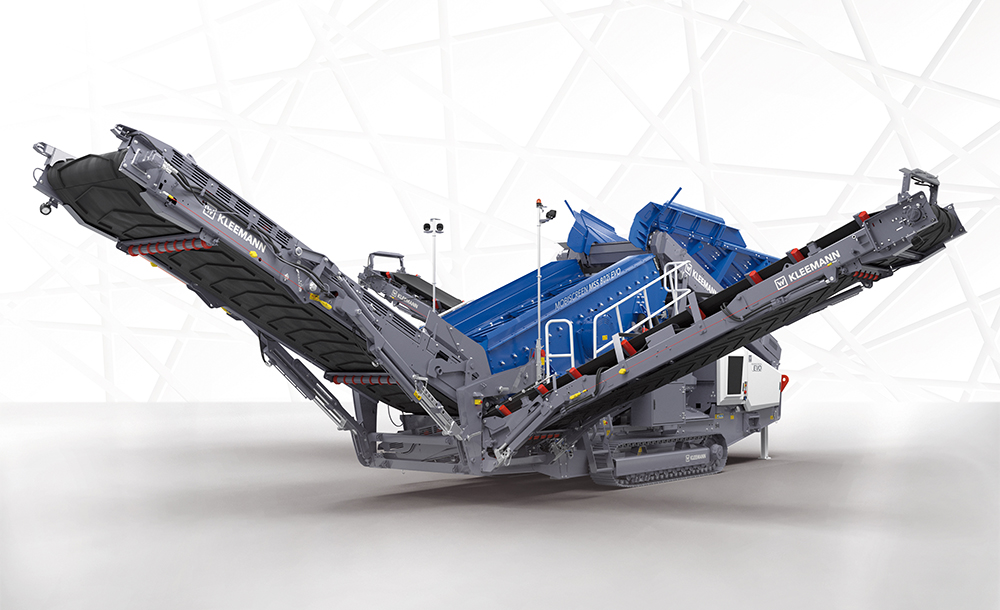
Versatile Cobra crusher from EvoQuip
Barry O’Hare, EvoQuip business line director, said: “More than 40% of our machines are used in a recycling application. The Cobra 230R impact crusher, for example, can be run in reverse. This is a really useful feature for recycling sticky materials like asphalt.” EvoQuip says this shows that the brand is well-positioned to meet the demands of a growing recycling industry in North America.
Booth S5435
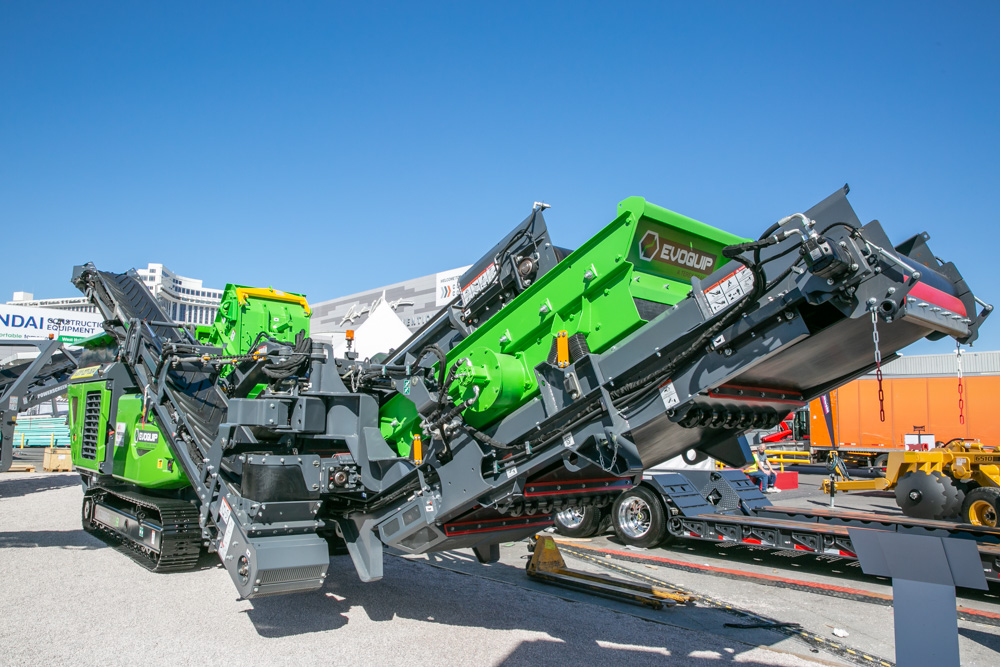
Easy does it with GSSI’s PaveScan RDM 2.0
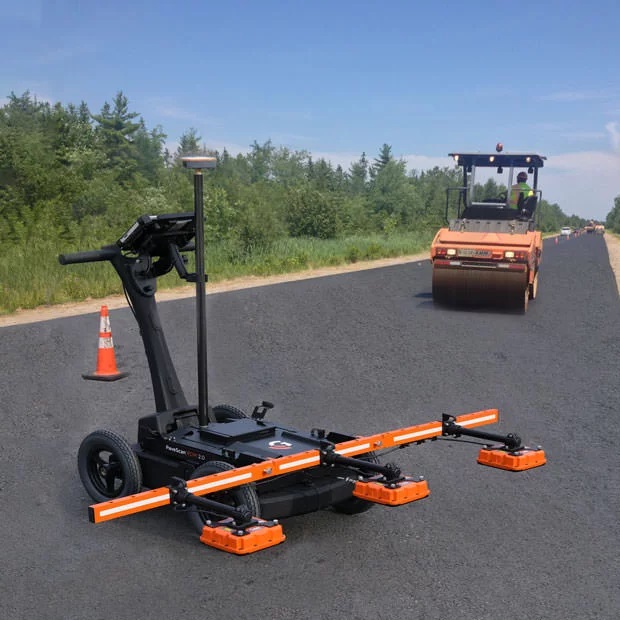
Road works planned for Germany
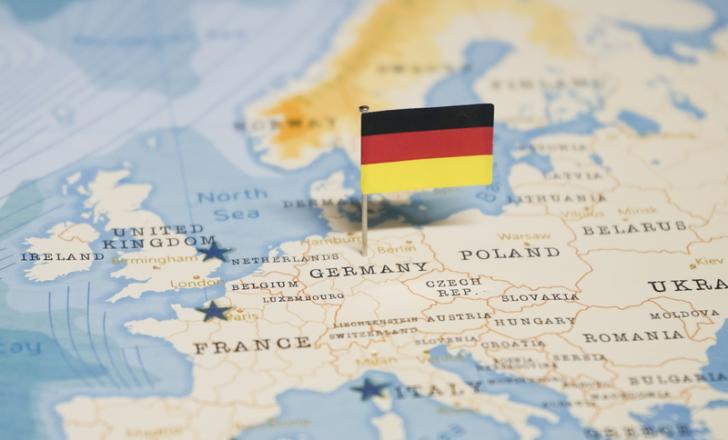
Slovakia’s sluggish highway works in 2023
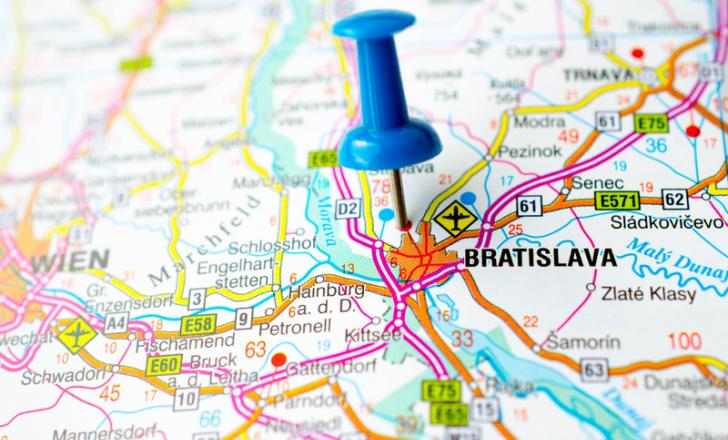
Keestrack is launching its new impact crusher in North America
The R5e can process up to 400tonnes of material/hour and is very mobile and transportable in one piece. The double-deck pre-screen is said to ensure perfect screening. The material can be stockpiled by side conveyors or via the crusher bypass. The impact crusher is driven by a 200kW electric motor and drives the rotor with an extremely high mass moment of inertia, giving high productivity and stability. The two-deck precision screen can be placed in a closed circuit.
The R5e has a drop-off engine/gen set which can go either on the machine's chassis or the machine, connected with a power cable. Placing in a less dusty and vibrant environment, it functions as a backup when no connectivity to the grid is available. Connecting several machines to a single drop-off engine/gen set results in huge savings, as there is only one engine/gen set to run and maintain. Maintenance is also safer and easier when the engine is placed at ground level.
The R5e uses, on average, 173kW when powered full electric or around 40litres/hour when driven via the drop-off diesel engine/gen set.
Booth C31386
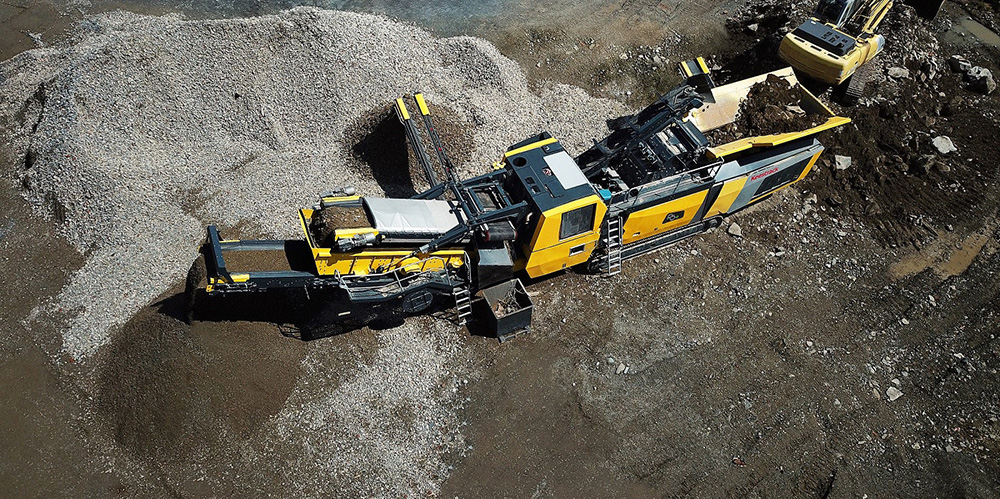
WJ’s ThermoPrint set for more UK road trials

Innovative cone crushing from Metso Outotec
The firm is also launching the latest version of the Lokotrack LT120 – one of the most efficient mobile jaw crushers in the market for demanding quarry and contract crushing applications. The LT120 features the proven Nordberg C120 jaw crusher and is equipped for optimised performance and extended wear life. It includes the Planet Positive hybrid composite MX jaw dies, a rock breaker, rubber lining in the feeder, a belt cleaning set for the long main conveyor, the latest intelligent crushing solution, and the new Metrics digital remote monitoring platform.
Meanwhile, Metso Outotec’s aftermarket solutions help quarries and contractors reduce cost per tonne and decrease their energy consumption and carbon footprint. With the OEM quality parts and digitally powered services, Metso Outotec can optimise the performance and uptime of aggregates-producing equipment at every phase of the production lifecycle.
And Metso Outotec Metrics enable a wide range of services targeting improved performance, availability and equipment lifespan for different aggregates applications.
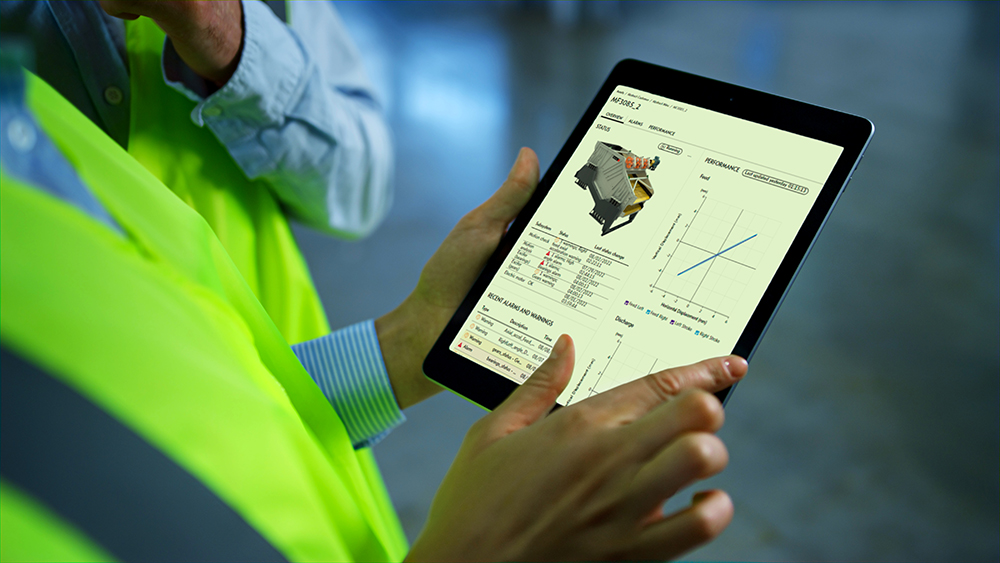
Senegal road works underway
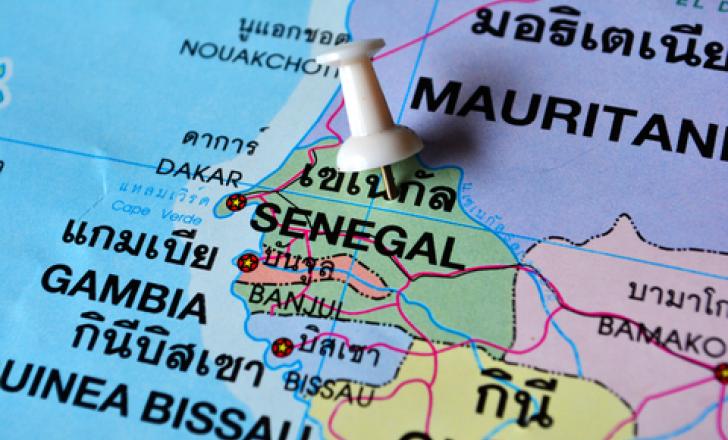