Traffic Group takes command
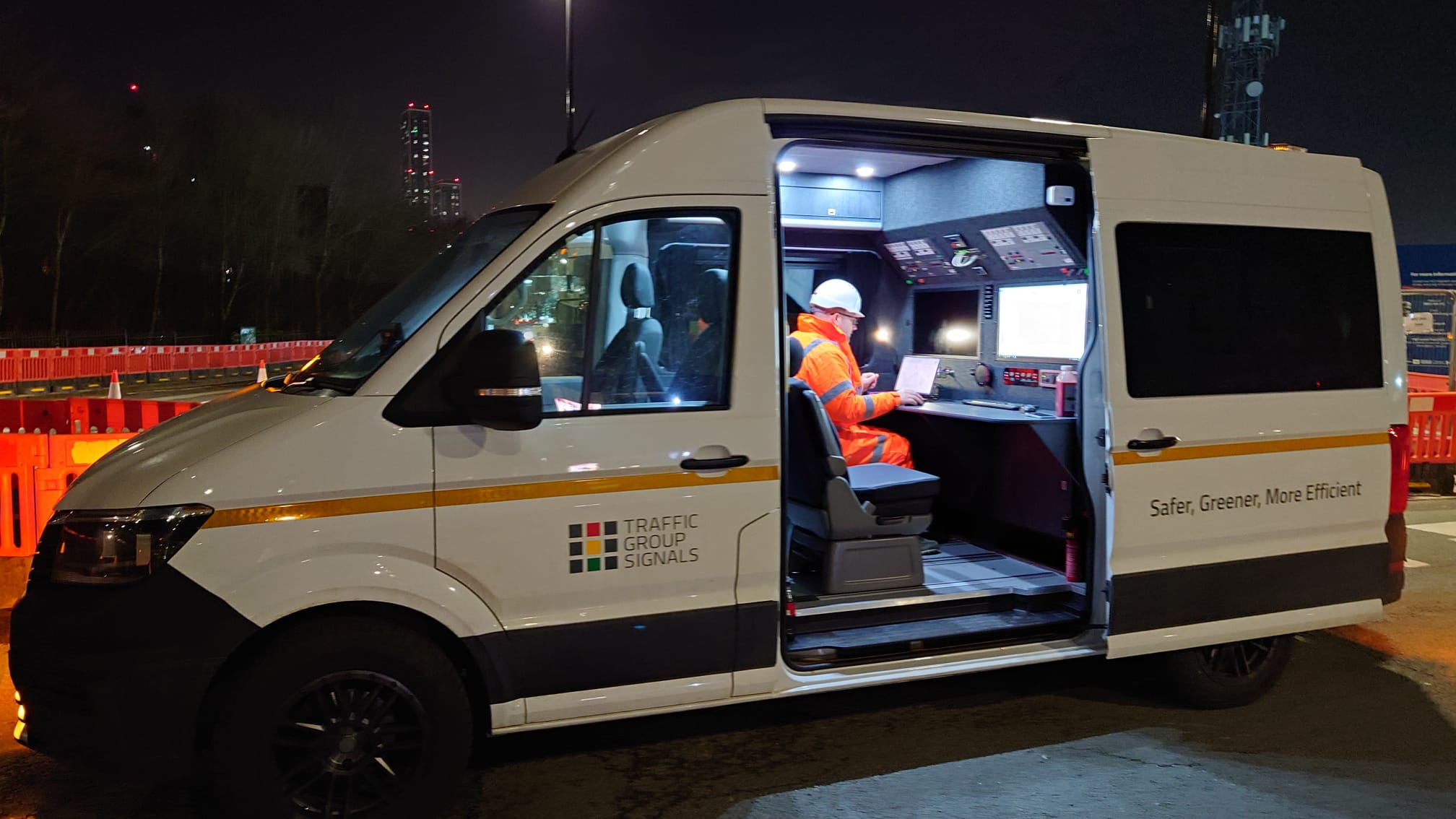
Patch it up with Secmair, Nu-phalt, Jetpatcher
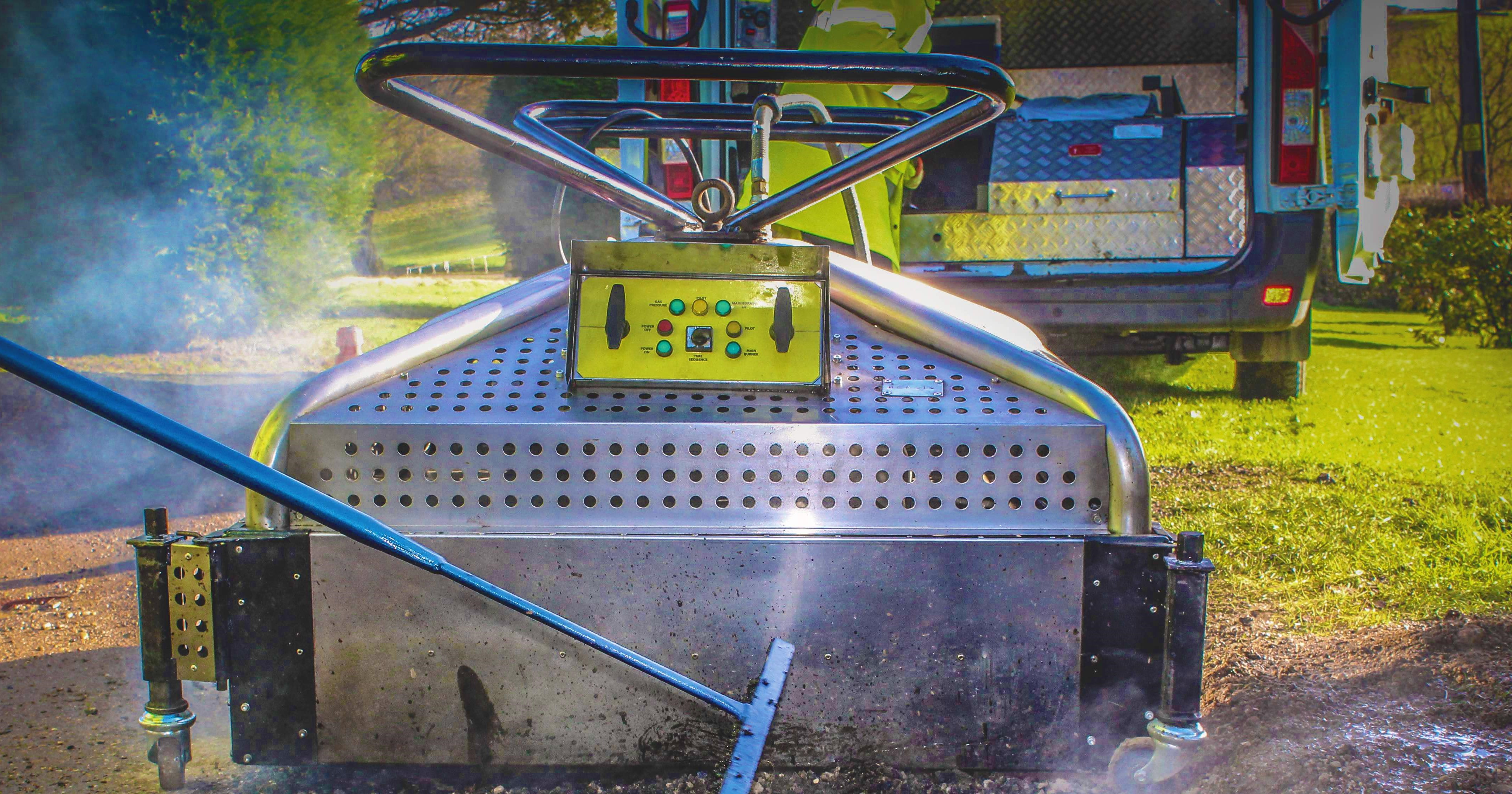
New roads for China’s Sichuan and Hebei provinces
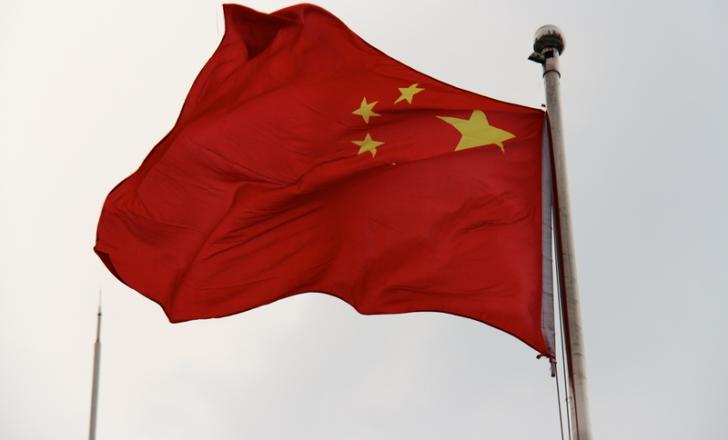
Defining sustainability and building a better world with Cummins, Trimble, and Volvo
For Cummins, sustainability is all about “the most efficient transfer of energy into power,” a goal that the US engine giant has spent its entire history working towards. Volvo wants to help “build a world we all want to live in,” and Trimble likes to think about “transforming the way the world works.” It all sounds very aspirational but, with sustainable technology taking centre stage, it’s happening now.
XenomatiX launches XenoTrack Dual Lane
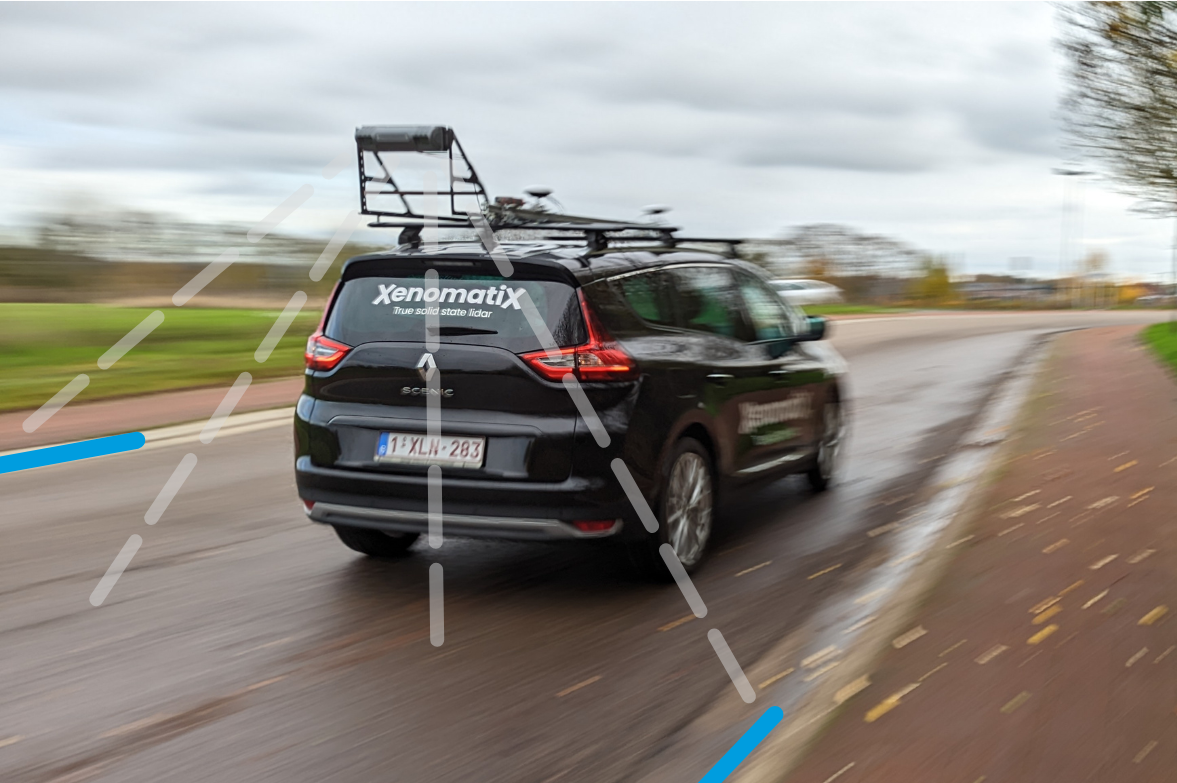
Nynas and Shell in Hanson UK bio-binder trial
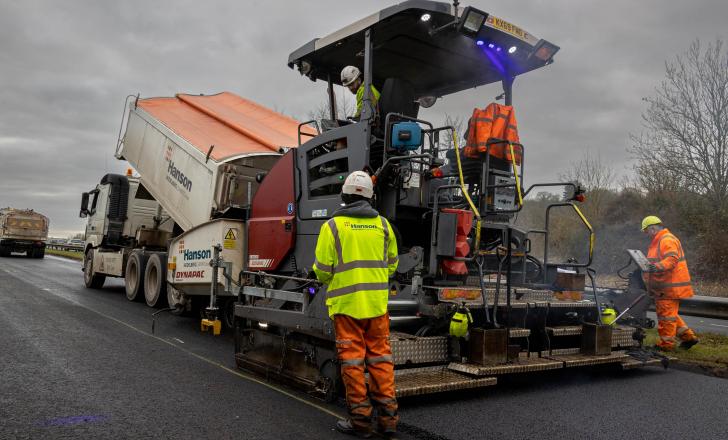
Ammann Mobile Asphalt Plant Built for NA Market
The ACM Prime provides the quality control benefits of a high-capacity plant yet comes in a fully mobile package. The main plant fits on two, two-axle trailers – and remains on them upon arrival and during operation. When it’s time for relocation, the trailers are simply attached to trucks and moved.
The new ACM Prime is a continuous plant that is “100% mobile,” meaning accessories such as tanks, RAP feeders, self-erecting storage silos and the control house are also on wheels. With previous models, some of these elements were stationary.
The shift to 100% mobility is in response to the needs of the North American market, where fast and effortless relocation is essential to many businesses.
All components are manufactured in the U.S., with the exception of the trailers, which are sourced from Latin America. The U.S. manufacturing ensures quality and eliminates supply chain issues.
Many start-up asphalt plant manufacturers utilise the ACM Prime because it gives them the flexibility needed to reach new customers. The cost of this compact plant is also less than a traditional stationary plant, making it easier for small businesses to enter the market.
More established businesses use the ACM Prime because of its mobility, convenience and small footprint upon arrival.
The plant is ready to work quickly. It arrives assembled, and plug-in components make setup extremely fast.
While the ACM Prime is highly mobile, it produces high-quality mix. The plant has successfully manufactured mix for airport runways, where quality is of the utmost importance.
Production capacity is 180 U.S. tons per hour with 5% moisture. Mixing times are adjustable, based on the recipe and desired output. The plant can utilise RAP, produce warm mix, and incorporate filler, fibers and other additives.
The Ammann as1 Control System is the brains of the plant. The proprietary system is highly advanced, yet extremely intuitive. It helps improve quality while reducing material waste and energy consumption.
A proven, reliable and robust fieldbus system is included.
Fuel efficiency is another benefit. Heat exchange is optimised between hot gases generated by the burner flame and aggregates. Enclosed gaskets between the dryer and chamber are well insulated. Air pressure is controlled inside the drum and burner – and dryer and burner settings are precise to minimise fuel burn.
The ACM Prime Plant is built for long life and reliability. A low-pressure, gentle cleaning process reduces bag wear. Engineering ensures easy access for service and maintenance.
Content produced in association with Ammann
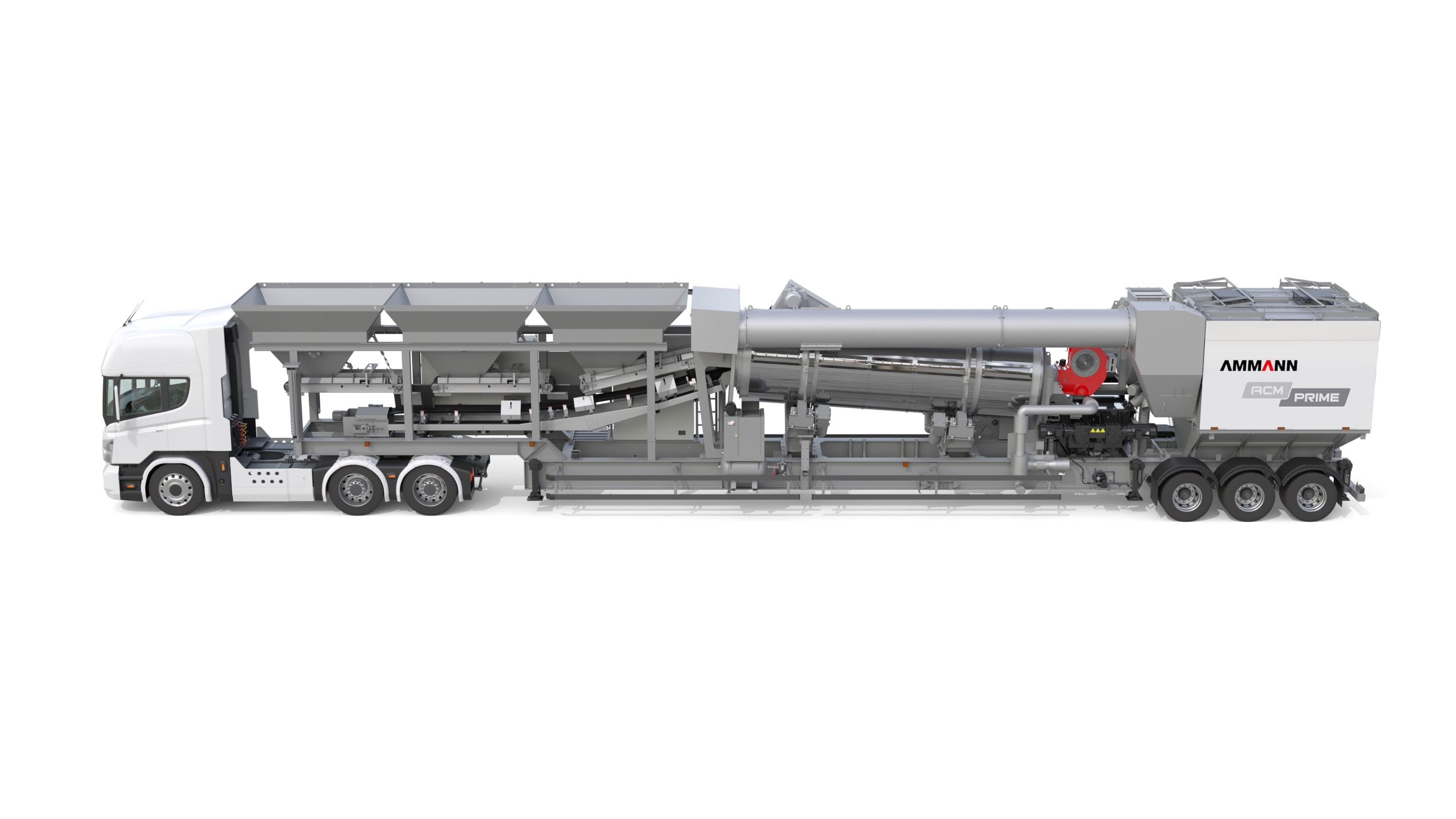
European construction machine sales remain strong
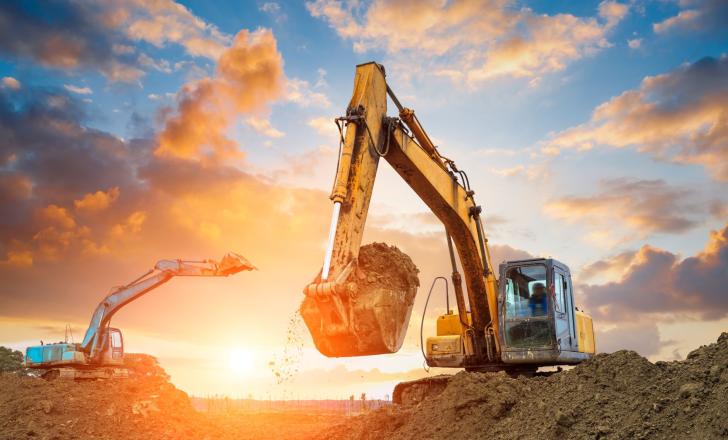
Approval for UK road contract
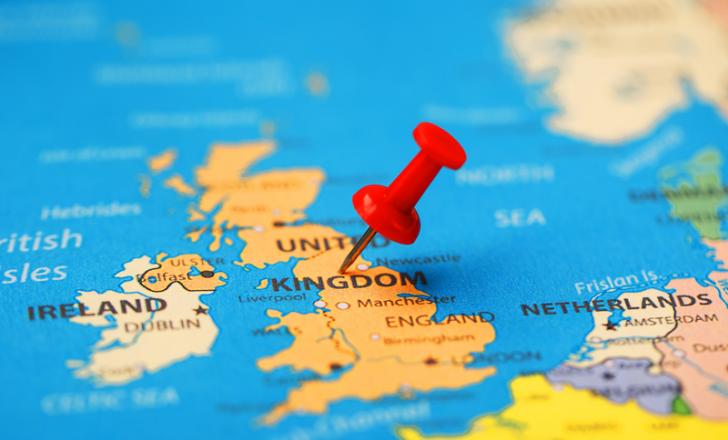
Jetpatcher: patch it right first time
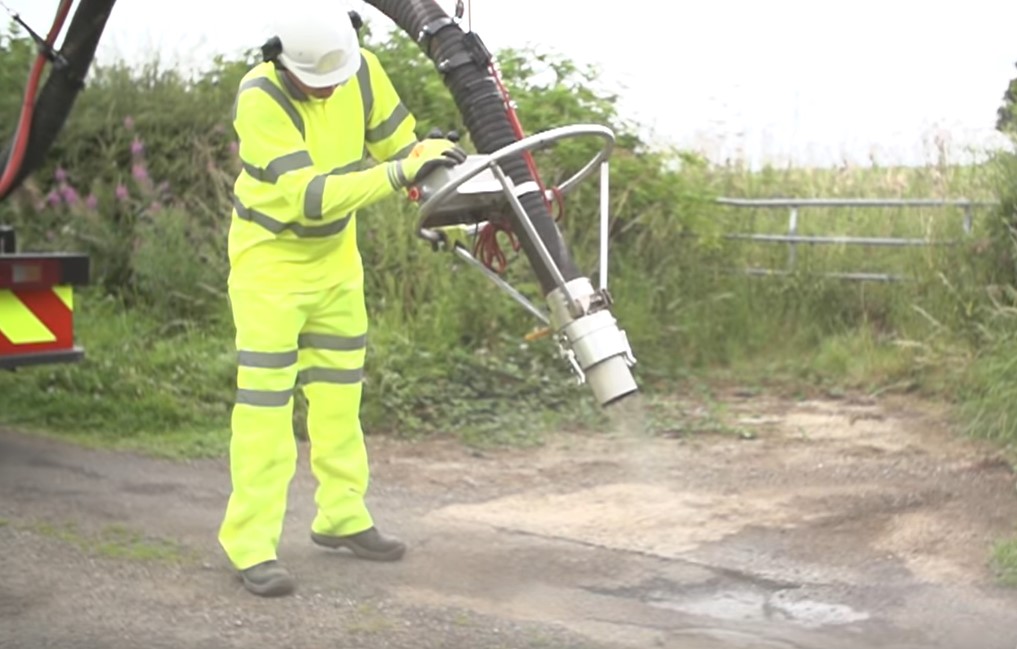
Vietnam coast road planned for Ben Tre Province
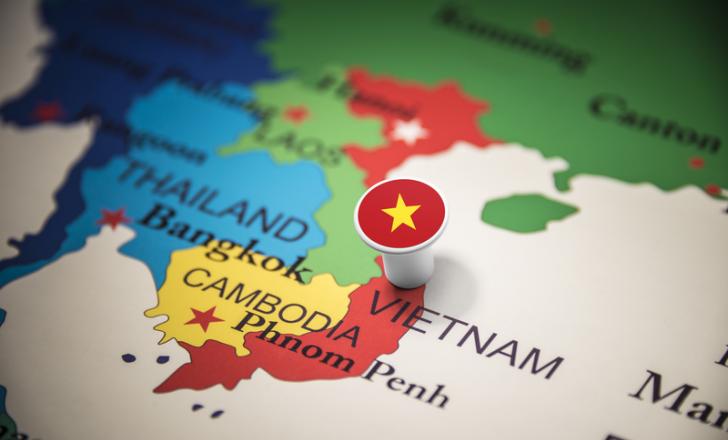
Road safety improvement needed for Morocco
Hydrogen engines from Hyundai
The firm has completed the design of its hydrogen ICE unit, an 11litre class engine that produces a power output of 300kW and a torque of 1700Nm at 2000RPM. It meets the Tier 5/Stage 5/Euro 7 regulations which require the emission to be 90% reduced to the current level to meet Zero CO2 (below 1g/kwh) and Zero Impact Emission (Zero Emission in EU).
Hydrogen engines are powered by low-purity hydrogen, making them durable, economical and energy-dense, which makes them the most suitable engine system for mid-to-large-sized vehicles and vehicles for long distances. A single charge of 10 minutes enables a distance of up to 500km, and HDI says that the units are 25-30% more economical than fuel cells or battery packs when vehicle price and maintenance costs are considered.
HDI plans to leverage its existing engine technology and facilities to reduce costs and accelerate commercialisation. The new hydrogen engines will be installed on commercial vehicles such as trucks and large buses, and construction equipment for validation by 2024, and full-scale mass production is planned for 2025.
HDI is also introducing EV battery packs and plug-in full hybrid powertrains so that customers will have power options.
Booth S84044
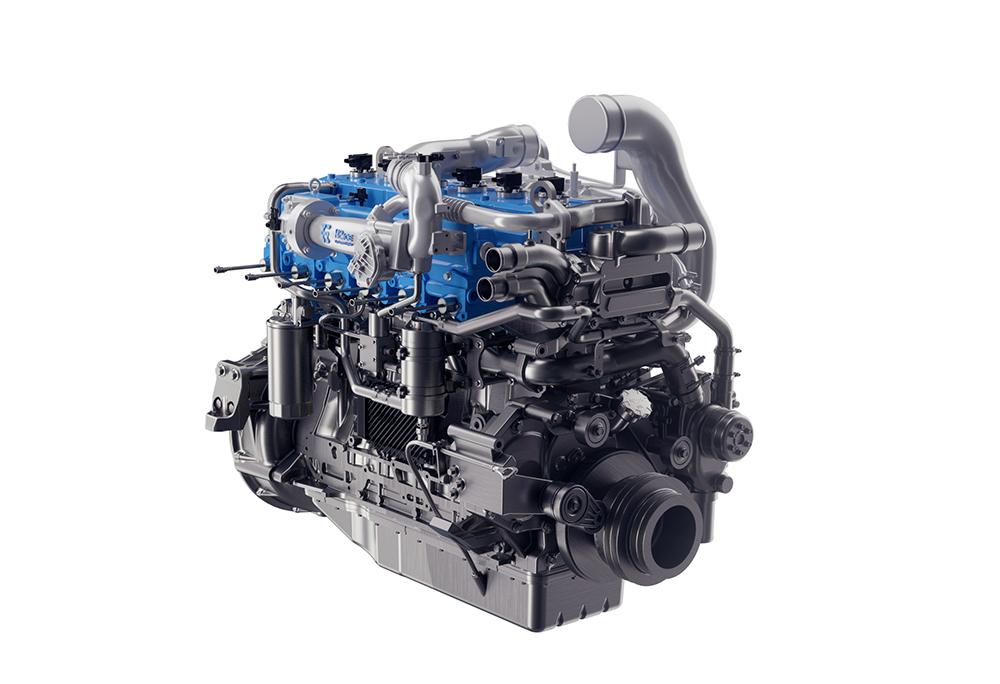
Uganda expressway development project proposed
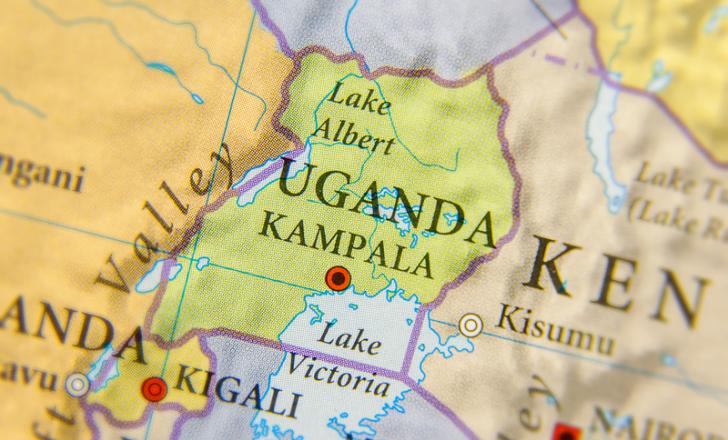
Golden Gate upgrade works
Improving Rutting with Sripath’s PGXpand® PMB-Mixes
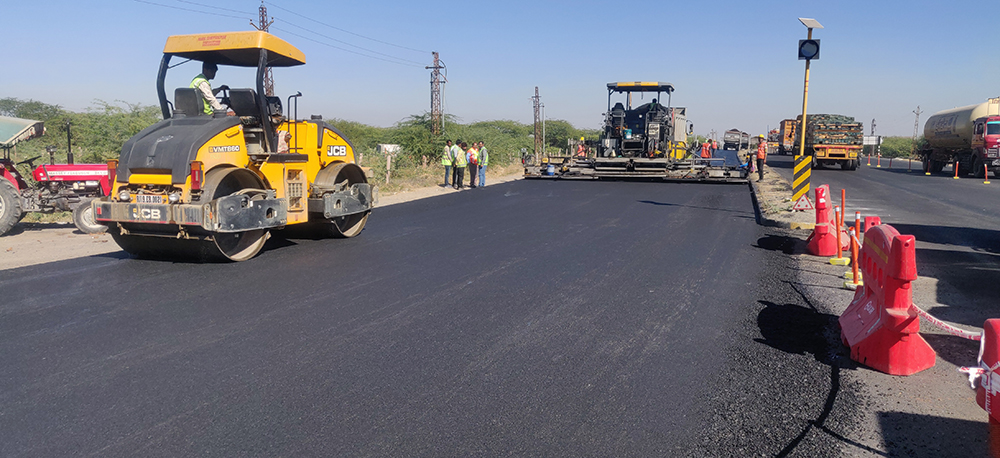
Ammann unveils its most compact single-drum roller
The ARS 30, with a working width of 1200mm (47.2 inches), is suitable for compacting a wide range of materials and can be even more flexible given the smooth or padfoot drum options. Cab or open platforms are available.
Engine power output is 43.2 kW (58 Hp). The engine meets the latest emissions standards (US EPA Tier 4f / EU Stage V).
Fuel consumption is an exceptional 5 litres (1.32 US gallons) per hour. That efficiency and a large fuel tank of 98 litres (25.8 US gallons) mean a roller need only be fuelled once every three working shifts.
Advanced engineering and years of industry expertise are behind the development of the drive system. The drums, designed and manufactured by Ammann, are high quality and extremely durable.
The strong single-stage vibratory system and two different frequencies supply compaction power of 37 kN and 68kN.
ECOdrop
Customers appreciate that the drums are designed to be maintenance-free as part of Ammann’s ECOdrop philosophy. The focus of ECOdrop is to reduce the volume of fluids required, make service points extremely accessible – and make all new products more environmentally friendly.
ECOdrop on the ARS 30 offers:
Improved fuel economy and lower fuel consumption due to available EcoMode.
A maintenance-free vibratory system with lifetime grease bath instead of oil bath.
A lifetime maintenance-free steering joint with bearings placed in cage storage.
No drive gearboxes – and therefore no gear oil is needed.
No-rear-axle
The innovative no-rear-axle concept separates Ammann ARS Single Drum Rollers from the competition. Elimination of the rear axle makes the rollers more compact and enables a lower engine location that improves the centre of gravity – which provides better stability, even on slopes.
Intelligent Compaction
Also available for installation is the ACEforce system, which enables operators to easily monitor compaction progress. The Intelligent Compaction system shows the actual kB value on the display, significantly reducing the time required to achieve maximum compaction.
Other key machine features include:
- A standard twin-lock drive that improves traction and reduces slipping of axles. This fully automatic traction control system is activated without electronic controls.
- A new articulated joint that further boosts drive performance, stability and manoeuvrability.
- An operator station with a wide-opening entrance that provides unrestricted access to the spacious, quiet cab.
- A multi-functional control display that is located on the main dashboard, making it easy for operators to monitor.
- An engine compartment that is easily accessible, with a heavy-duty design that protects all major components during operation.
Click here for the download sheet
Click here to find out more at ammann.com
Booth S5455
Content produced in association with Ammann.
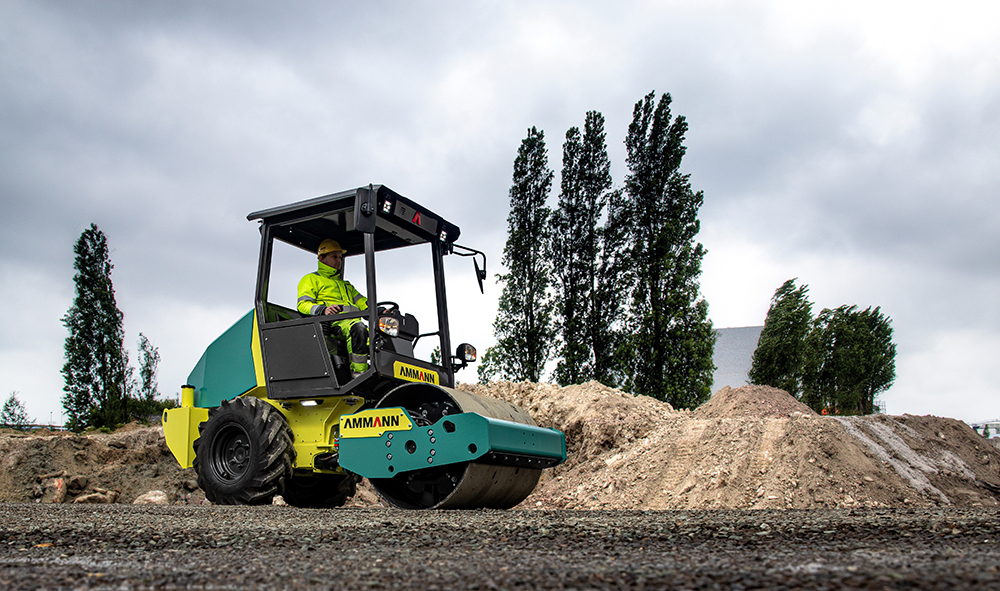
RoadVista launches StripeMaster 3
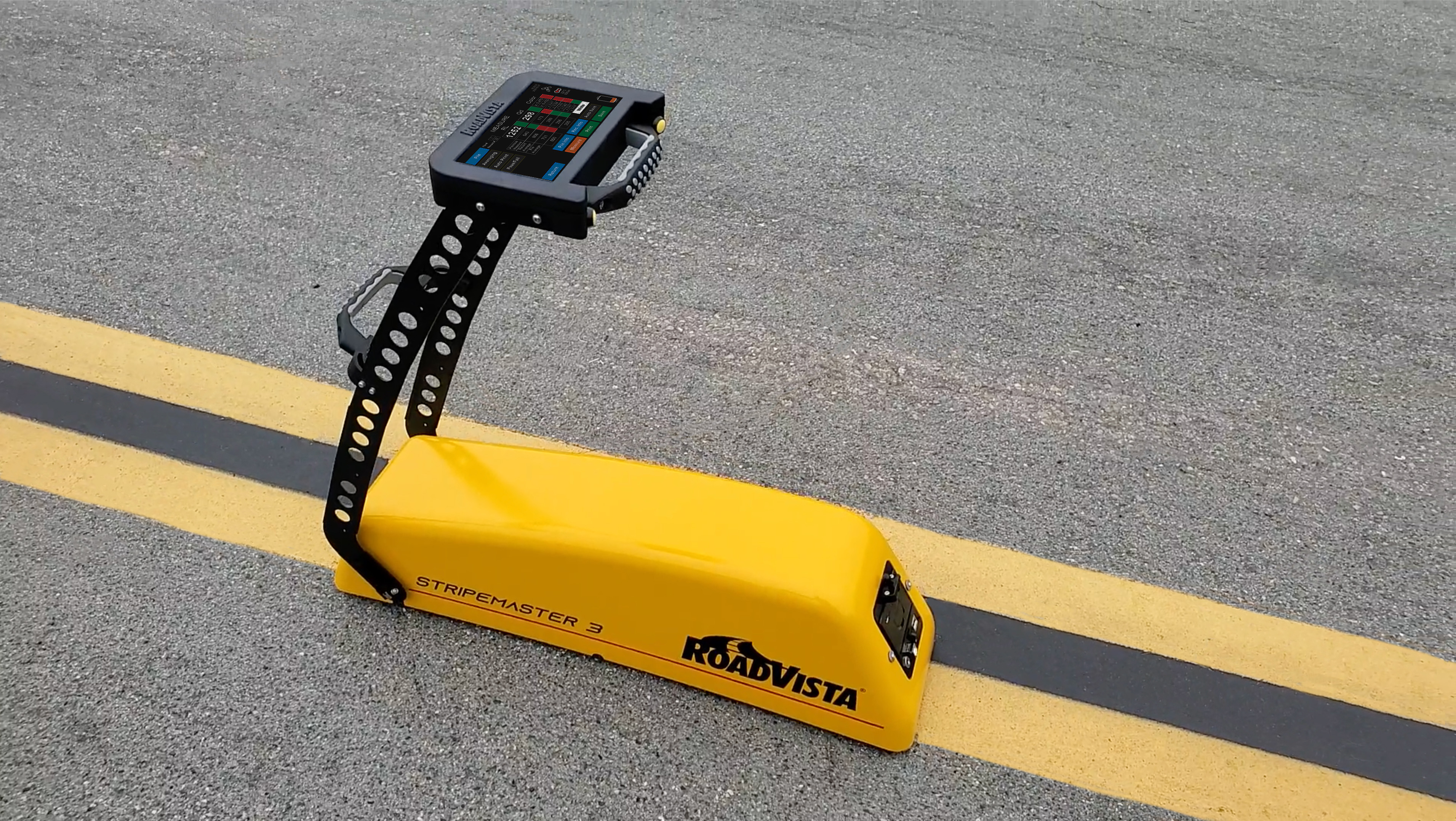
Dust control from Superior
The new Skirting System retrofits to any brand of existing structure with little or no field fabrication. Two sets of adjustable legs aid in this universal installation. Additionally, easy to adjust clamping mechanisms are used in place of nuts and bolts to hold skirtboard rubber tight against the belt. An optional stilling zone is available to accelerate the settling of dust while material is moving inside the system.
Superior’s Modular Skirting System is sold in 1.5m sections for conveyor belt widths up to 1.728mm. Along with 250-tons of other products, this new Skirting System will be shown in at CONEXPO-CON/AGG 2023.
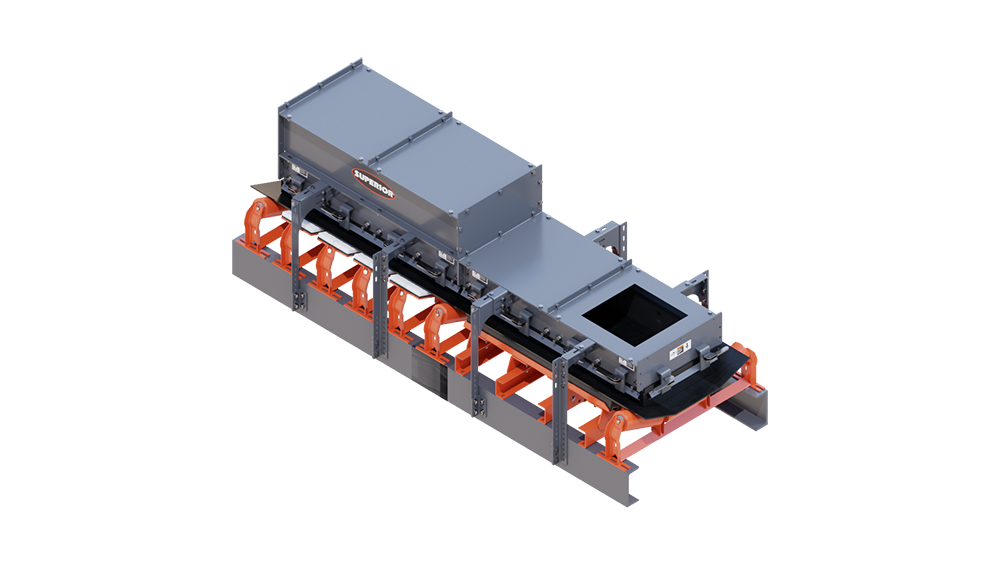
Advanced laser scanner from Leica Geo Systems
Using a tablet, customers can quickly, easily and accurately capture and scan features and dimensions of sites and structures that would otherwise be dangerous or inaccessible for humans. Advanced obstacle avoidance and the ability to determine optimal scan routes make the BLK2FLY an effective aerial reality capture solution for civil engineering companies. The flying laser scanner documents heavy construction sites with improved accuracy and detail, safety and efficiency.
Booth N12325
