Indeco is on the acquisition trail after a record-breaking year for sales in the US
The firm is now looking to expand its facilities in the US to meet the strong demand for equipment. The site is also used to manufacture a number of items such as mounting brackets for hydraulic hammers and hydraulic compactor attachments.
In addition, Vitulano said Indeco is looking for a suitable business acquisition to add to Indeco’s portfolio. “We are scouting for an acquisition, a small company with a good product, (one) that has maybe been undercapitalised.”
With the firm having had great success in the compact breaker market in the US, Indeco is also looking to widen its product offering for more compact demolition tools such as cutters for use on mini excavators. Vitulano said that he believes this offers considerable business potential for the future.
On another note, Vitulano said that Indeco is now achieving its first sales of breakers into Japan, a significant success given the strength of Japanese hydraulic breaker firms in their home market. However, he said that entering the South Korean market with the Italian breakers has so far proven considerably more challenging.
Looking ahead in terms of technology, Vitulano commented that Indeco is monitoring the development of electric construction machines very closely. “We should think to the future when machines go electric,” he said.
However, with regard to electric actuation of units such as breakers, there are major technical challenges to be overcome according to Indeco’s chief engineer, Alessandro Ciccolella. “There is no loss in power as electric machines are very efficient,” he said.
Ciccolella questions the ability of electric actuation systems to cope with the massive mechanical shock loads transmitted in units such as breakers. While the firm has been carrying out research into electric actuation, Ciccolella does not believe there will be any quick electric breaker breakthroughs in the near future.
Booth W43257
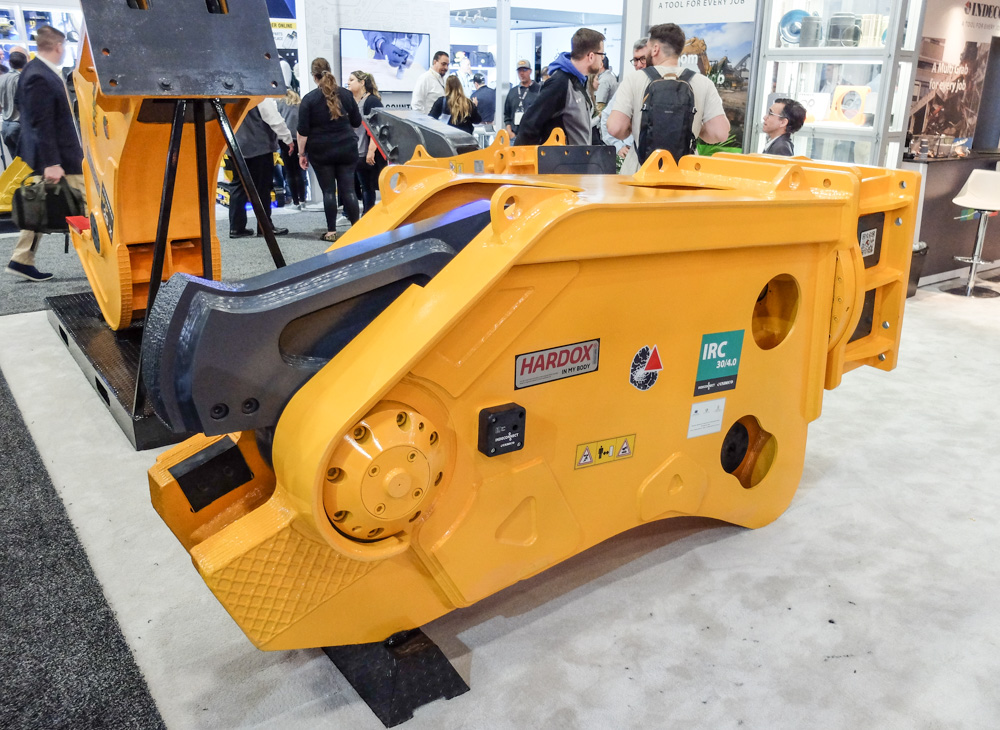