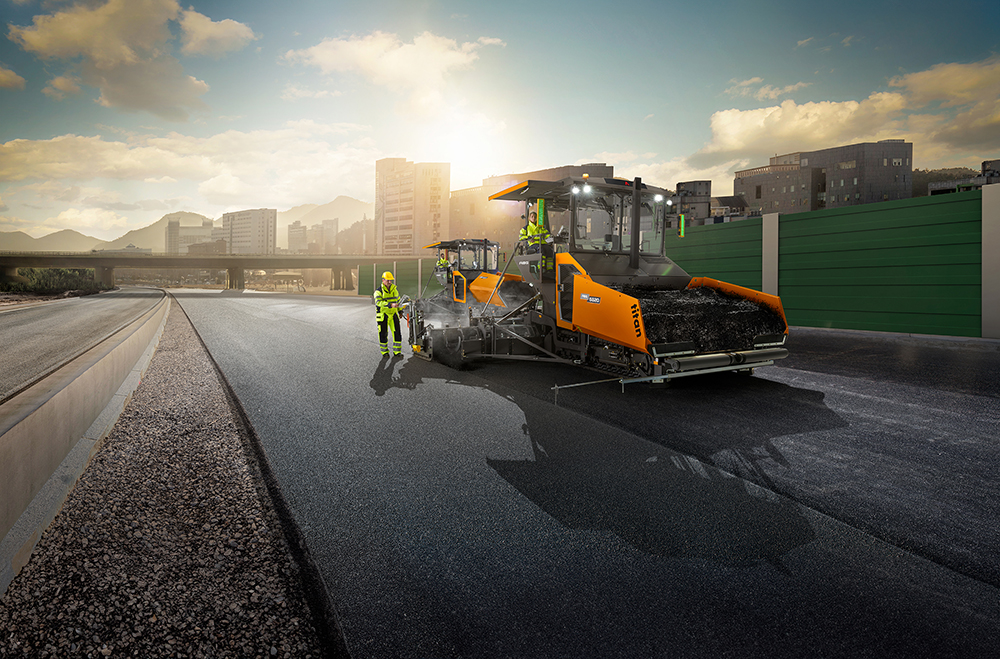
ABG Pavers from Ammann offer real advantages on the jobsite. A few of these benefits in particular deserve more detailed explanations.
Double-tamper technology
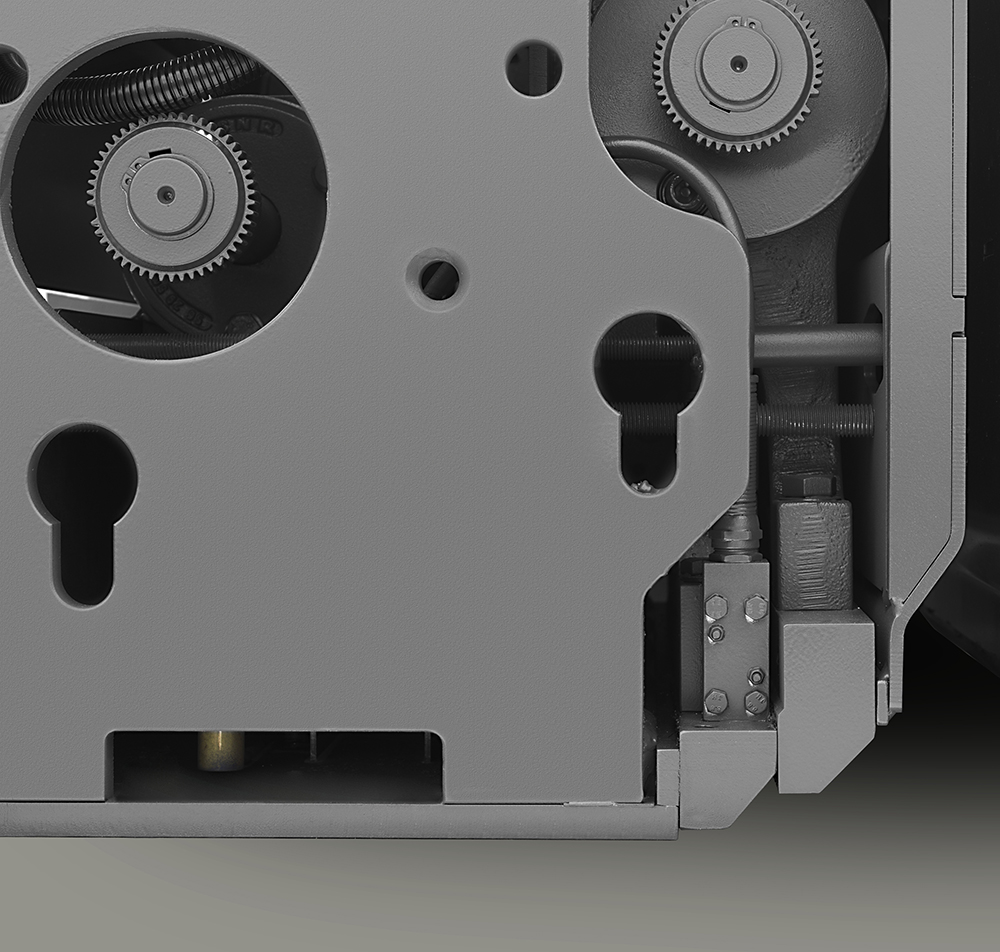
ABG screeds with this technology offer optimal pre-compaction that reduces the number of compactor passes needed. Every pass that is eliminated lessens fuel burn, emissions and wear of the compactor.
The process delivers a 5% to 7% higher degree of compaction than a single tamper. An ability to reach up to 98% Marshall density dramatically reduces the number of necessary compaction passes.
As the name implies, double-tamper technology means the material is struck by two tampers. ABG screeds differentiate themselves by tamping the material twice before it reaches the screed baseplates.
The first tamper strikes the material in front of the screed, redistributing the mix as needed. The second tamper hits the mix again, also in front of the screed, assisting pre-compaction and further ensuring uniform density distribution, even with varying layer thickness.
The material is already pre-compacted and level before reaching the baseplates. Therefore, the baseplates simply provide the finishing touches that support exceptional pre-compaction and smoothness.
Double-tamper screeds have proven successful in a variety of applications. They include paving base, binder and wear courses; granular materials; roller-compacted concrete (RCC); and cement-bound materials (CBM).
The tampers, and the pre-compaction they bring, are also invaluable in applications where traditional compaction methods are difficult to conduct. Examples are the laying of asphalt-sealing surfaces on dam slopes, and on circuits with high banks for testing and racing.
e+ screed heat
An ABG paver with e+ screed heat does not require a running engine to generate electric power. Instead, the screed can be heated directly from the grid or from a power pack brought to the jobsite.
This technology provides a significant reduction in CO2 emissions every shift. It is estimated that CO2 emissions can be reduced by 1.2 tonnes per paving season when using the e+ screed. (The exact amount depends on a number of conditions.)
Among the benefits:
• There are no local CO2 emissions during heating as the screed is warmed from the grid or battery pack without running the paver’s engine.
• The screed is powered by clean, renewable energy.
• Up to 1200 kg1 CO2 can be saved per machine per season.
As is so often the case, the sustainable efforts create financial gains, too.
• Electric heating is quiet, allowing work to begin earlier in noise-sensitive locations.
• The screed is hot when crews arrive, enabling workers to begin paving immediately.
• An estimated 488 idle hours per year can be eliminated. (This is calculated based on 130 shifts per year, with a five-person crew, and 45 minutes of preparation before the start of paving.)
• Fewer running hours for the machine means higher resale value.
• The lower hours also extend engine life and reduce maintenance costs.
Screed tensioning device
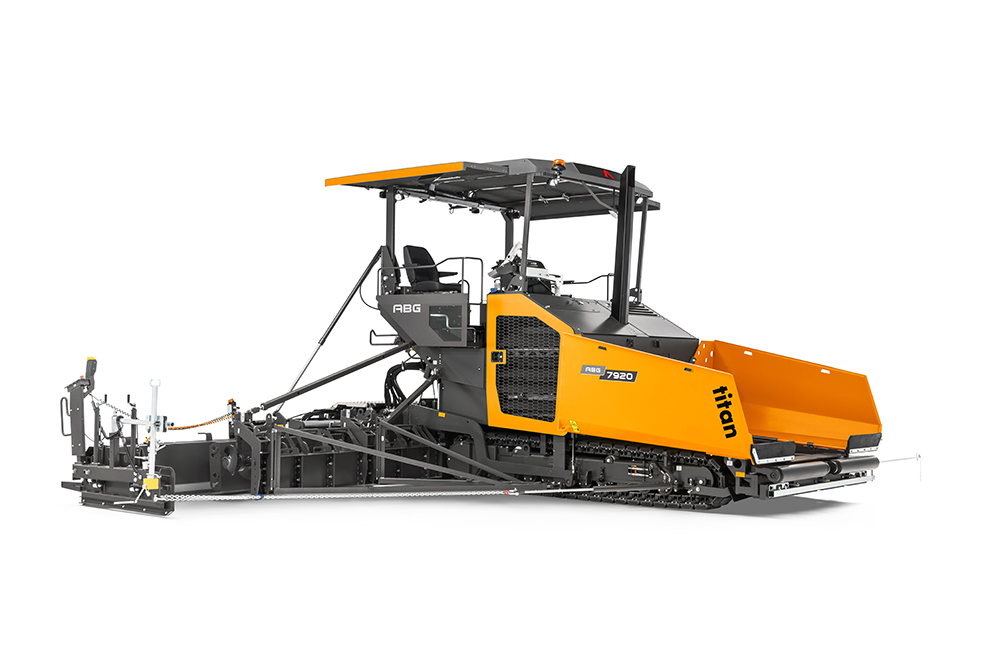
Screeds are subject to torsion when paving at challenging widths. If not addressed, the ends of the screed can twist, which can lead to uneven layer thicknesses and poor results.
The ABG screed tensioning device is designed to prevent this issue. Hydraulic cylinders apply pre-defined levels of tension under high material load, countering forces that could otherwise cause twisting.
The patented tensioning device, which can adapt to varied screed widths, provides consistency across the entire width of the screed, ensuring a consistent angle of attack.
Ride leveller for wheeled pavers
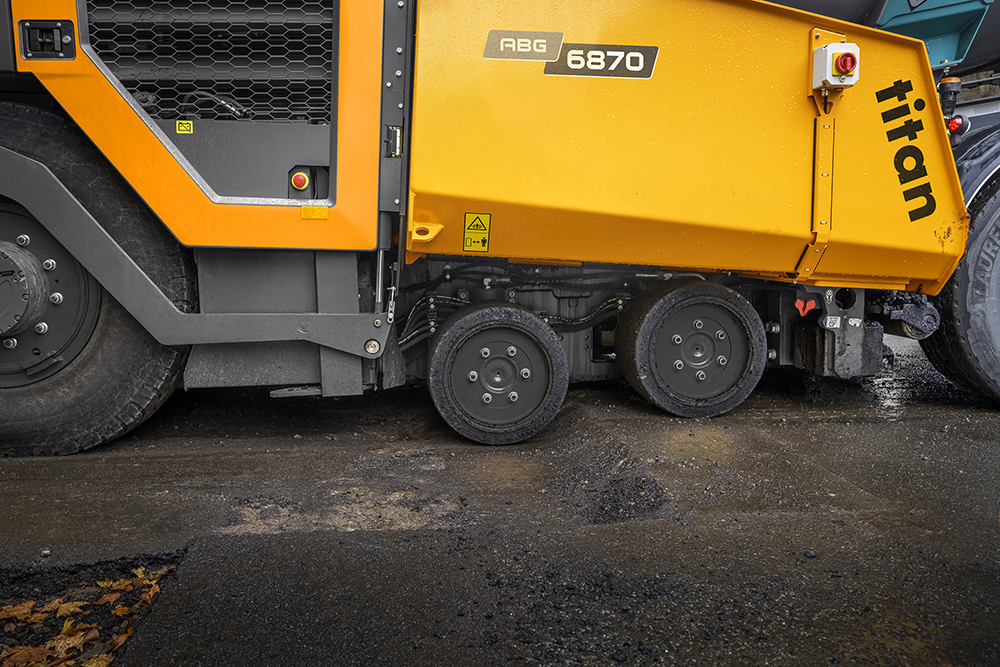
A stable undercarriage is a prerequisite for smooth paving. Improperly balanced undercarriages can cause the tow point to overreact to changes in height, resulting in an uneven mat.
This is not much of a problem with tracked pavers, which have long undercarriages that level out these inconsistencies. Tracks don’t react to each and every bump as wheels do.
This led to the development of the unique ride leveller system, which provides wheeled pavers with additional machine stability.
Rear wheels are fixed to the frame and therefore cannot provide the flexibility to compensate for any unevenness in the ground.
Each front wheel is linked to the frame with hydraulic ride levellers. The levellers are all connected by hoses and share hydraulic fluid. If one wheel moves because of a surface irregularity, the hydraulic fluid flows to the other ride levellers. This minimises the impact on the tow point, and ultimately the mat.
The hydraulic ride levellers also enable better traction in poor or uneven ground conditions and improve the front drive performance.
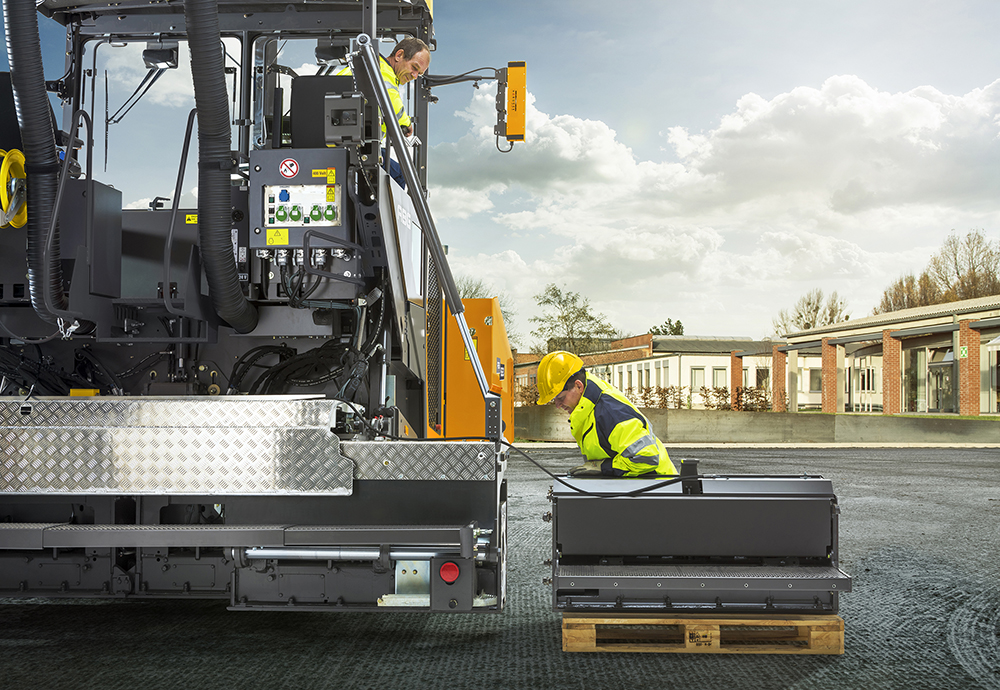
Anti-climbing lock and screed load device
Breaks in paving are rarely desired, but they are inevitable. The challenge is ensuring the new mat is smooth when paving resumes.
For pavers at more manageable widths, the ABG anti-climbing lock is effective at preventing bumps. When paving restarts, the anti-climbing lock cylinders work to eliminate uneven surfaces that can arise. The lock applies pressure to the screed to prevent it from being raised by cooling material. Once engaged, the function works automatically for a few seconds every time the drive lever is moved from neutral to forward to improve quality and evenness.
Sometimes widths are more extreme, and ambient temperatures are colder, making the mix harder to compact. In these cases, the optional screed load device provides a smooth start. The function is similar to the anti-climbing lock, but the effect is on the entire screed.
Unique quick-coupling
Crew members can quickly add or remove Variomatic screed extensions with the ABG quick-coupling system. The changes require no special tools and bolts don’t have to be removed.
With the system, unique clamping cylinders secure the extension to the screed. Each cylinder has an internal spring that creates clamping force. Hydraulic pressure can offset the force, and the extension can be easily attached or removed.
Content produced in association with Ammann