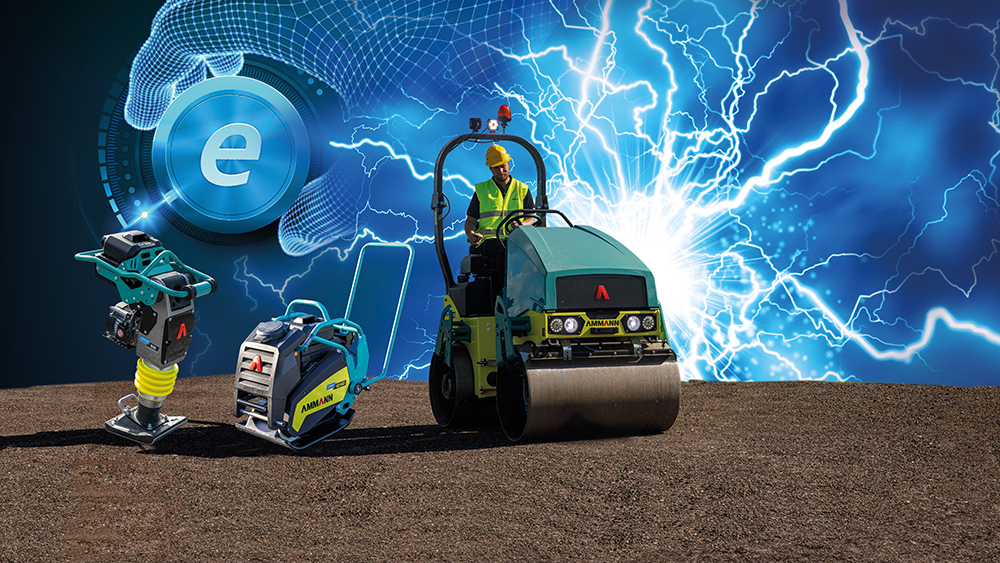
After all, machines that are sustainable but not productive will never make their way into the fleets of the customers and rental houses who get the work done.
Ammann delivers on its sustainability promise by:
• Developing electric-drive machines with ZERO emissions
• Low noise level emitting by a machine during operation
• Electric-drive and vibration system with integrated recuperation technology (eARX 26-2)
• Providing non-electric engines that can burn clean, alternative fuels
• Reducing the volume of required fluids
• Extending the life of products
Below are some of the sustainable, high-performance products Ammann offers.
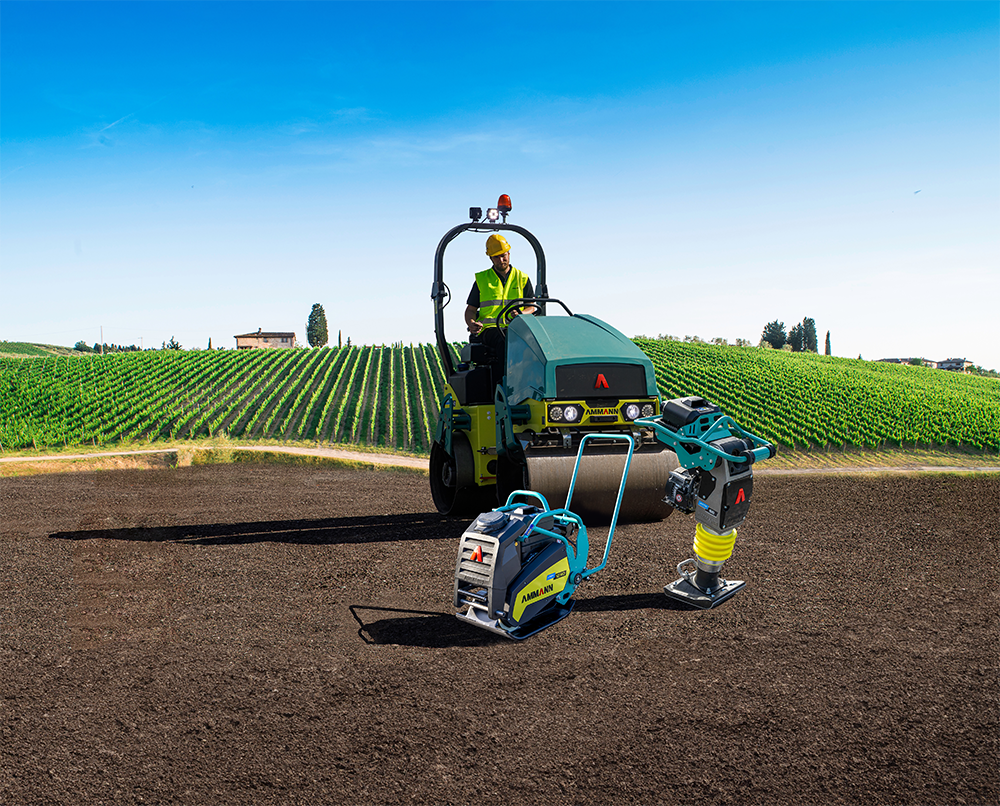
E-drive Light Compactors
The Ammann eATR 68 Rammer and eAPF 12/40 and eAPF 12/50 Forward Moving Vibratory Plate Compactors are electric-drive machines that generate zero emissions. An e-Drive also means there are no fuel or oil filters to purchase or dispose of.
This e-Drive light compaction equipment dispels the notion that power must be compromised when using an electric machine. The e-Rammer has centrifugal force close to its petrol counterpart, while the e-Plate equals the output of the petrol machine. This is accomplished through advanced engineering that makes the most of the power provided and ensures compaction force is properly directed to the surface, not the operator.
The e-Drive APF remains a good climber, with gradeability of 30% and maximum incline of 20% to all sides. Speed for both electric and petrol versions is 0-20 m/min (65.6 ft/min).
Successful e-Drive machines start with an advanced battery pack. Ammann’s battery pack for light compactors charges quickly – and holds its charge, too. The battery can be charged overnight to maximise capacity the next day. If needed, it can be charged for a shorter period during a shift and then quickly returned to work.
The same battery pack powers both the Ammann e-Plate and e-Rammer – and likely additional Ammann machines in the future. This provides convenience and promotes uptime.
The light compactors utilise lithium iron phosphate (LiFePO4 ) batteries, which maximise safety. The batteries and their advanced management system are particularly robust and resistant to high temperatures, overcharging, and mechanical damage.
Protecting operators
• The most important sustainability efforts are those that provide safety. All machines feature intuitive controls that help keep operators safe.
• The standard guide handle on many Ammann plates is isolated to minimise hand-arm vibration (less than 2.5 m/sec2). The vibration levels are so low that safety codes do not require documentation of operator hours.
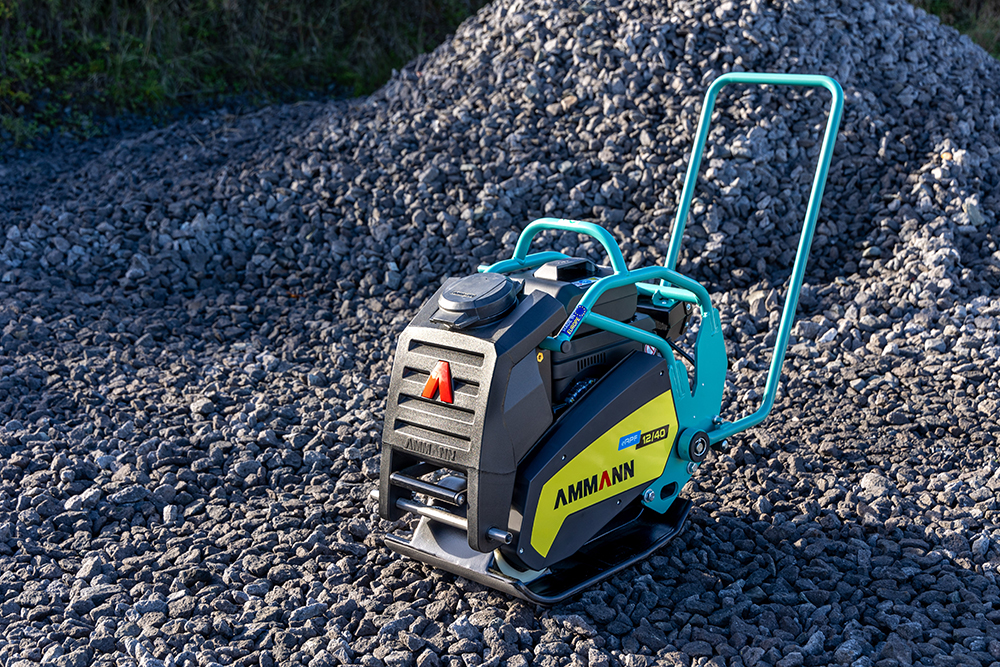
The eARX 26-2 Light Tandem Roller
The fully electric Ammann eARX 26-2 Light Tandem Roller is a game-changing machine. A diesel engine is replaced with a fully electric drive and unique vibratory system. The result is zero direct emissions, reduced levels of CO2 and a smaller carbon footprint.
The absence of a combustion engine makes the eARX 26-2 extremely quiet during operation. Sound levels reaching the operation station are 46% less than with a diesel version.
The innovative powertrain concept eliminates almost all hydraulic components. The ecological impact is also lessened – and total ownership costs are significantly reduced.
The eARX 26-2 is equipped with a powerful battery pack with electric motors for the main drive and vibratory circuits. Gone are the conventional combustible (diesel) engine, hydrostatic drive and cooling circuits.
Key is the advanced 48-volt battery pack with a capacity of 600 Ah/31,5kWh. The pack’s LiFePO4 technology is unique because each internal battery cell is independently protected. This makes the entire pack flame-resistant, increasing safety.
The LiFePO4 battery is characterised by a long lifespan and a high number of charging cycles. The battery is likely to last for the life of the machine.
The roller’s technology provides extended operation on a single charge. Depending on the jobsite and the demands on the machine, an eARX26-2 can operate up to 18 hours without having to recharge. This means the machine must only be charged once per typical working day, usually at the end of the shift (depending on jobsite conditions).
All electric drive and vibratory motors are equipped with a recuperation mechanism as standard. When the machine stops, or when vibration is turned off, the electric motors continue to generate power – and send it to the main battery to increase charge.
The battery can be recharged via the recuperation process during machine operation – or with chargers when the machine is not operating.
Charging is fast, easy, and requires no special tools. Two charging systems are available:
• On-board charger – 12 hours charging time (from 0% to 100% battery capacity)
• External charger – 3,5 hours charging time (from 0% to 100% battery capacity)
The operator can continuously monitor battery charge level. An automatic alert is sent via the multi-functional display when charge falls to 10%. If the level drops to 3%, the system automatically disengages the vibrator to conserve power for machine travel to a charging zone.
Ambient operating temperatures are another important advantage. The temperature ranges are wider than Li-ion batteries and other common technologies. LiFePO4 batteries can operate below the freezing point – specifically from -10° C (14° F) – and up to 60° C (140° F).
Electric drive motors also bring more precise control to the vibratory unit. This enables frequency control that is unique to the market. Vibratory settings can be adjusted from 55 Hz to 66 Hz for high-quality, efficient compaction output.
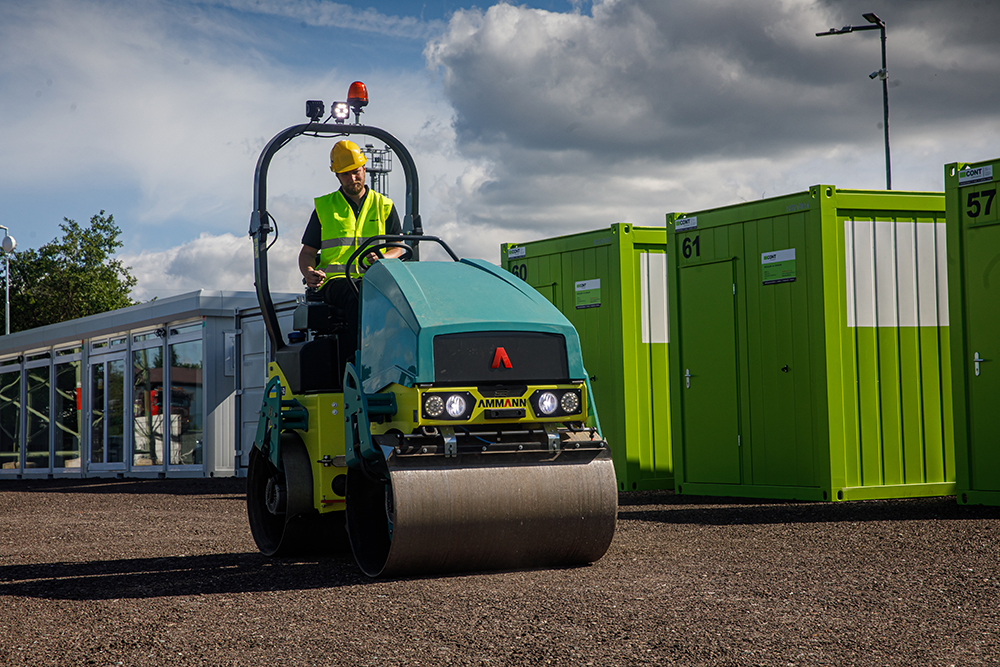
ECOdrop Initiative
Of course the Ammann product line is not entirely comprised of electric drive machines. We have also taken efforts to incorporate sustainable improvements across our product line through the ECOdrop initiative.
ECOdrop starts by maximising engine efficiency, which trims both emissions and fuel costs. ECOdrop also involves reconfiguring key systems and components to minimise the operational fluids required to run them. This results in lower costs for both acquisition and disposal of the fluids.
Extending machine life
Ammann machines are built with durable components that extend life, once again making the most of the resources used to manufacture them. Their advanced engineering also reduces the wear that can result from less efficient machines.
A closer look at one specific product, the Ammann ARS 70 Soil Compactor, highlights the key features and benefits. With ECOdrop, the ARS 70 has seen a reduction of:
• 22% in fuel consumption
• 26% in the required hydraulic fluid
• 10% in the needed vibratory system fluid
ECOdrop also incorporates alternative fuels, including hydrotreated vegetable oil (HVO). The fuel has been approved for use in all Ammann diesel-burning machines.
HVO reduces gas CO2 emissions by up to 90%, with no additional costs. It is a biofuel made from waste, such as animal fat or processed vegetable oils. It is classified as a renewable diesel and renowned for having a longer shelf life than other biodiesels.
Every 1000 litres of standard diesel fuel burned produces ca. 2640 kg of greenhouse gas CO2, compared to just 260 kg of greenhouse gas CO2 for every 1000 litres of HVO burned.
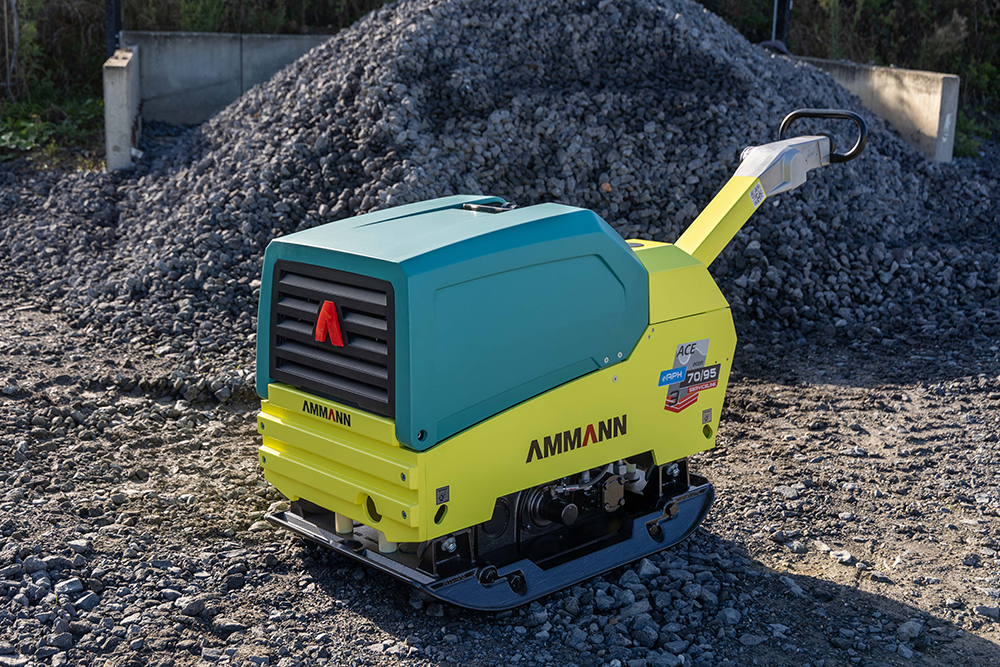
Built for rental
Ammann machines are great fits for rental houses because of their intuitive control, extended maintenance intervals and performance.
Manufacturing machines that are desirable for rental fleets also advances sustainability. Contractors who rent machines can make the most of products that have already been manufactured. This reduces the use of raw materials and energy that would be required to produce new compactors.
Renting equipment also enables businesses to easily scale operations up or down, preventing them from purchasing equipment that might sit idle for extended periods.
Content produced in association with Ammann