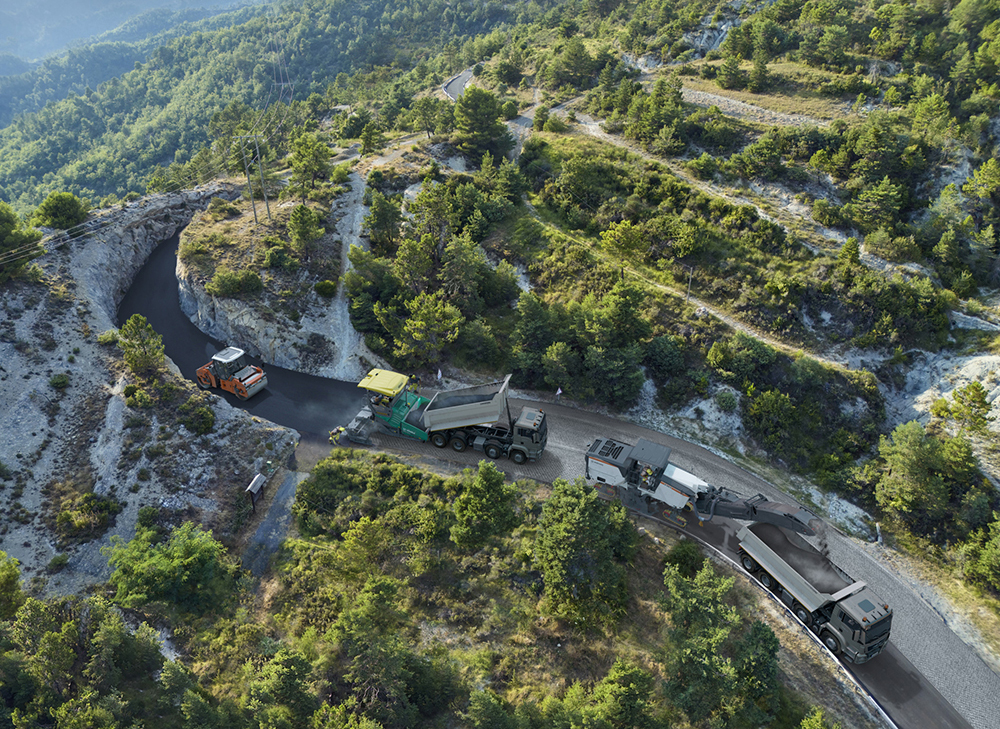
Maximising a machine’s uptime, allocation of resources the most efficient way, completing projects on schedule and ensuring the quality of results are nowadays major factors that decide whether a company can run its business successfully or not. This is amplified by the fact that the labor-intensive construction sector is affected by a global shortage of skilled workforce like few other industries and has to meet far-reaching requirements for quality, documentation, and sustainability. With the existing resources, it is becoming increasingly difficult to meet the demands and deadlines, and at the same time guarantee the continuous analysis of the executed projects. WIRTGEN GROUP addresses these issues by not only being an expert in road construction, but also in building bridges – to a connected world that ensures the best possible efficiency in the use of resources though digital transformation of their customers productions systems. WIRTGEN GROUP defines production systems as the paradigm shift from machine-centric approaches to a holistic view on projects by including all machines or machine combinations – as well as digital solutions – involved in the execution of a jobsite.

To achieve this goal, WIRTGEN GROUP strives not only to be technology leader in the field of machine construction, but also in the adaption of digital applications which ensure that their customers can use their machines with maximum efficiency.
To find out more click here.
Evolution of existing solutions and adaption of recent technologies
With solutions such as WPT Milling – the Performance Tracker for WIRTGEN cold milling machines – or Smart Compaction for HAMM rollers, there are already well-established products in the market that help WIRTGEN GROUP’s customers to increase their efficiency and profitability. In its strategy for digital transformation WIRTGEN GROUP addresses all stakeholders involved in the processes which includes machine operators, dispatches and workshop manages as well as site managers and managing directors.
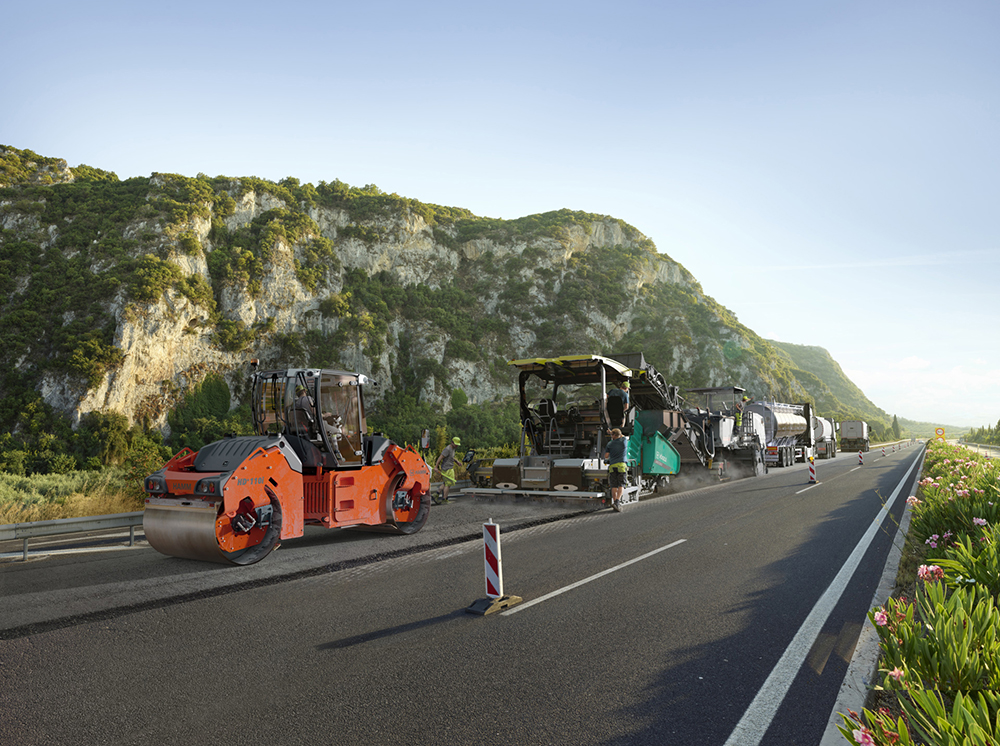
WIRTGEN GROUP’s three pillars of digital transformation
A holistic view on a jobsite offers the greatest potential for optimisation and is therefore one of the most important levers for increasing productivity and efficiency. By interconnecting all machines, systems, and processes involved in the entire construction process, digitalisation unlocks its whole potential. WIRTGEN GROUP is focusing on three pillars to support their customers in the digital transformation of their production systems: Connected Support, Jobsite intelligence and Smart Automation.
Connected Support: the combination of fail-safe machines and optimised maintenance and service concepts to achieve reliable predictability of the operation at the lowest operating costs by getting active before issues occur, identifying problems quickly, and by making service activities and costs plannable.
Jobsite Intelligence: making fact-based decisions by using real-time insights in the entire construction process. Therefore, WIRTGEN GROUP enables their customers to gain a continuous overview of jobsite workflows and processes.
Smart Automation: intuitive interfaces, assistance systems and automation ought to lead to lean processes and the ability of the existing personnel to focus on the essential and productive tasks of their work.
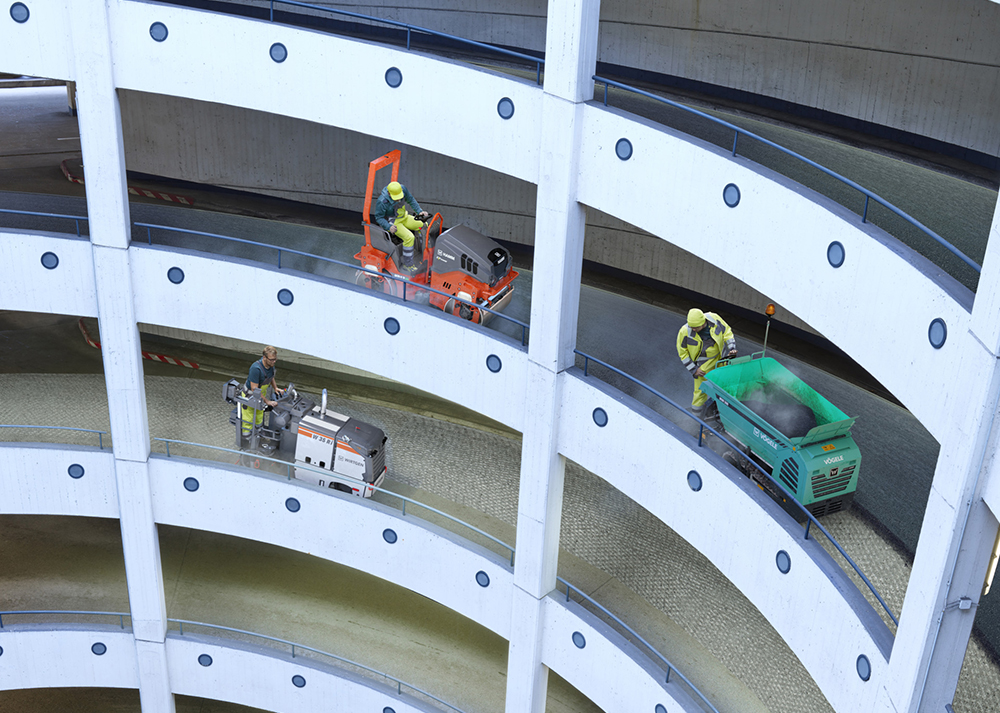
The John Deere Operations Center™ as the Nucleus for Equipment and Jobsite Management in Road Construction
The John Deere Operations Center™ has been an established tool in the agricultural sector for more than ten years. Following the positive experience from the agricultural market and strong demand from the road construction market, the tool has recently also been introduced to the construction industry. The web based solution is the central platform to manage whole fleets and jobsites in one place and is available both as website and as mobile app solution. It offers a holistic view of construction projects and enables users to monitor projects and machines in real-time. This includes information about the machine utilisation, the machines position and condition, consumption data such as fuel, as well as insights into the progress of a construction project.
By being a central hub of information, the John Deere Operations Center™ is a central tool for planning, monitoring, maintenance, and analysis. Integrated maintenance plans make it easier to plan service intervals and help to improve availability and value retention. With performance monitoring for cold milling machines, the jobsite progress can be continuously monitored, and material consumption predicted. Relevant performance data help dispatchers optimise machine utilisation and productivity and can be used as comparative values for the planning of future projects while the continuous documentation of location and machine status allows a consistent analysis of the machine operation.
Additionally, all compatible machines from other manufacturers can be integrated into the John Deere Operations Center™ in the future which will enable customers to digitally manage and maintain their entire fleet.
To find out more click here.
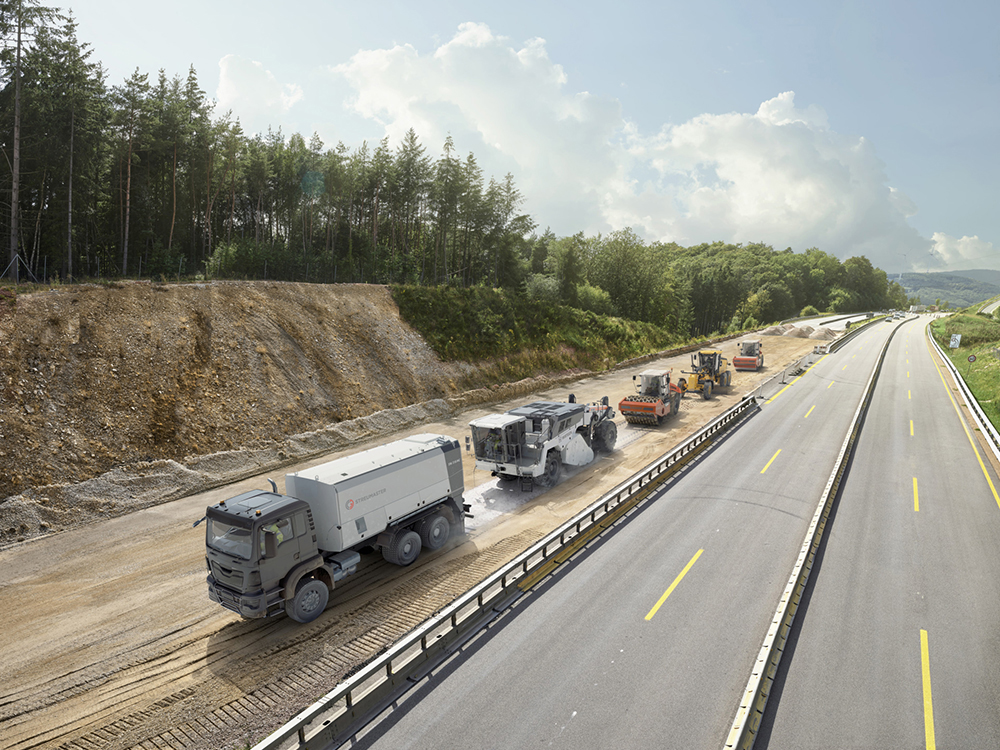
Content produced in association with Wirtgen Group