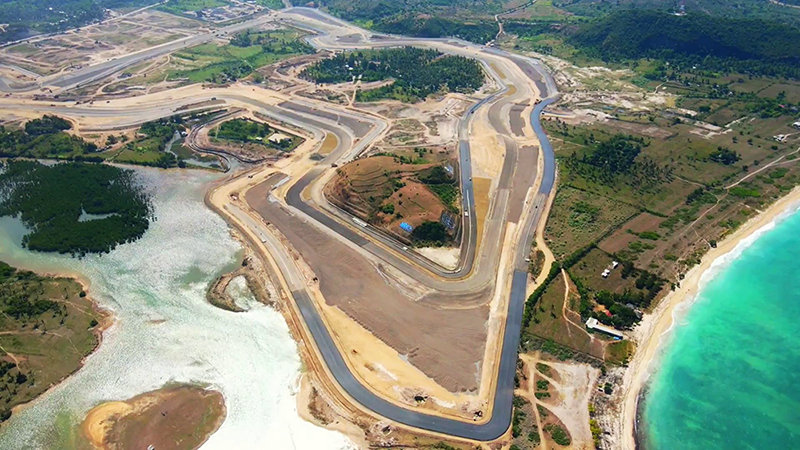
On the still quiet tourist island of Lombok, work on the Pertamina Mandalika International Circuit is in full swing. After completion, the circuit will be one of the most exciting tracks in the motorsport world. The first street circuit in motorcycle racing since 1977 is set to host the Indonesian MotoGP motorcycle race next year (see box, The fast lane). As many as 150,000 visitors are expected on any given racing weekend when the circuit is complete and running international events.
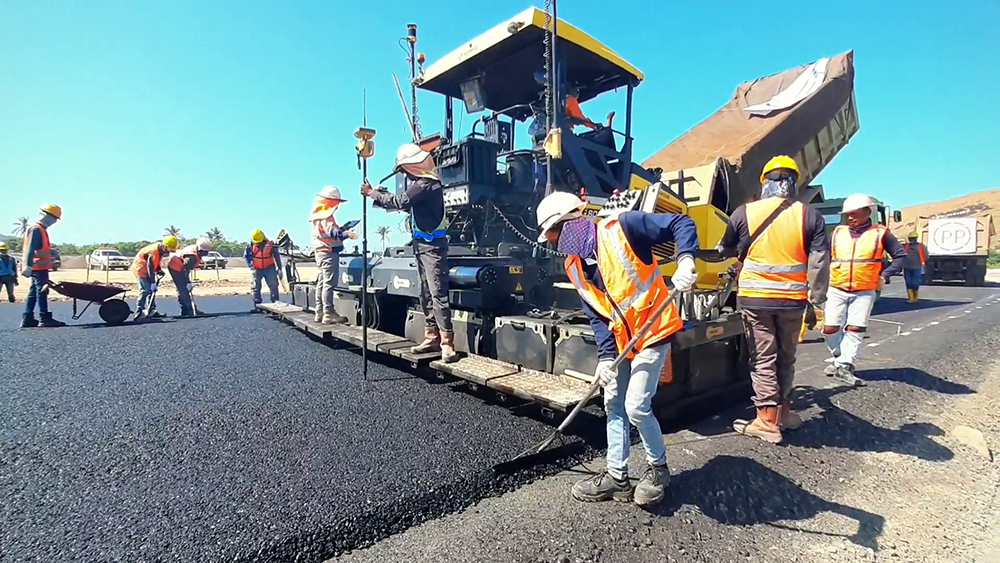
Bahraini company Mrk 1 Consulting and Roadgrip Motorsport were commissioned by the Indonesian Tourism Development Corporation to design, build and manage the circuit. The track, with few elevation changes, was designed by Mrk 1 to be a partially closed racing circuit where part of the track will be open as a public road during non-racing events. It is sometimes classified as a street circuit. Even so, the track surface has to meet the highest international racing circuit standards, as it is crucial for ensuring optimum grip and even wear on the tyres of competitive motorcycles.
The loads exerted on the asphalt during a race are tremendous. In the top motorcycle racing classes today, top speeds of over 360kph are reached. At such high speeds, overpressure is generated in front of the tyre and underpressure behind it. The heated tyres develop an adhesive effect that pulls the material upwards. It's like “hitting it with a hammer at the front while using a vacuum cleaner at the back”, as once explained by Hermann Tilke, a German civil engineer, the developer of many international circuits including Sepang International Circuit, China’s Shanghai International Circuit, Istanbul Park Racing Circuit and Spain’s Valencia Street Circuit.
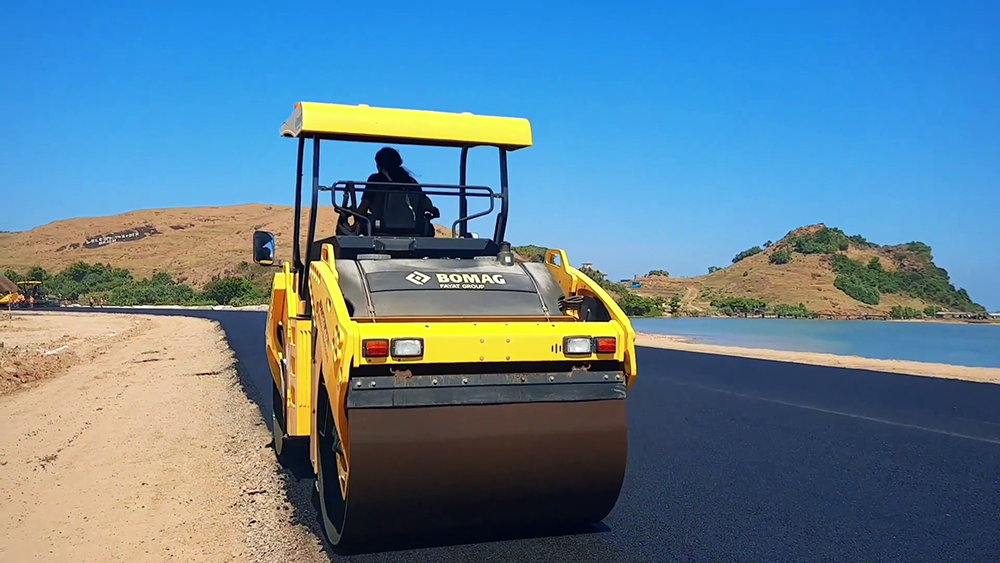
Given these exacting demands on the finished surface, the contractor opted for Bomag machines for paving and compaction of the asphalt for the entire circuit, including the verges, run-off zones and service roads. The greatest challenge is that the track must continue to meet all future demands placed upon it - competitive racing and high-volume public traffic - so the asphalt must be geared towards durability for smoothness and longevity.
Given the extremely high speeds of racing motorbikes, even the slightest unevenness results in less tyre grip that could increase the risk of serious accidents. To fulfil all the specifications, the optimum paver settings for evenness, degree of compaction and surface texture were first determined on a test section. In Mandalika, for example, a surface evenness of +/-5mm was required for the bearing and binder course, measured over a distance of 4m. The tolerance for the wearing course was even lower, at +/-3mm.
The local paving team was supported throughout the project by Bomag Singapore's team and also experts from Bomag distributor United Tractors in the Indonesian capital, Jakarta. Also on site were Lintec & Linnhoff asphalt manufacturing plants from the Indonesian heavy-equipment and services company Presisi.
80mm bearing course

Two Bomag BF 800 C pavers were used to install the bearing course. With their combination of high productivity and flexibility, these all-rounders were selected for both their high-quality and efficient road construction. Equipped with Bomag assistance systems and options, they greatly simplify the job for the operator and the perfect the entire paving team. For example, the operator has all-weather protection from not only the heavy downpours of rain, common and frequent in the region, but also from intense sunshine. The operator’s performance is aided by technologies such as Bomag Ecomode, an intelligent control system that keeps the engines in the optimum rpm and power range at all times, thus reducing fuel consumption and keeping noise levels to a minimum.
Although the system was not part of the project’s specification requirements, the pavers were equipped with components for 3D levelling. This eliminates the need for stringline tensioning, which is costly and time-consuming to set up. Instead, the machine's three-dimensional position is measured with a total station. One side of the screed is then controlled in 3D in position and height; the height of the other side of the screed is determined by the cross slope, which is also specified in the project data.
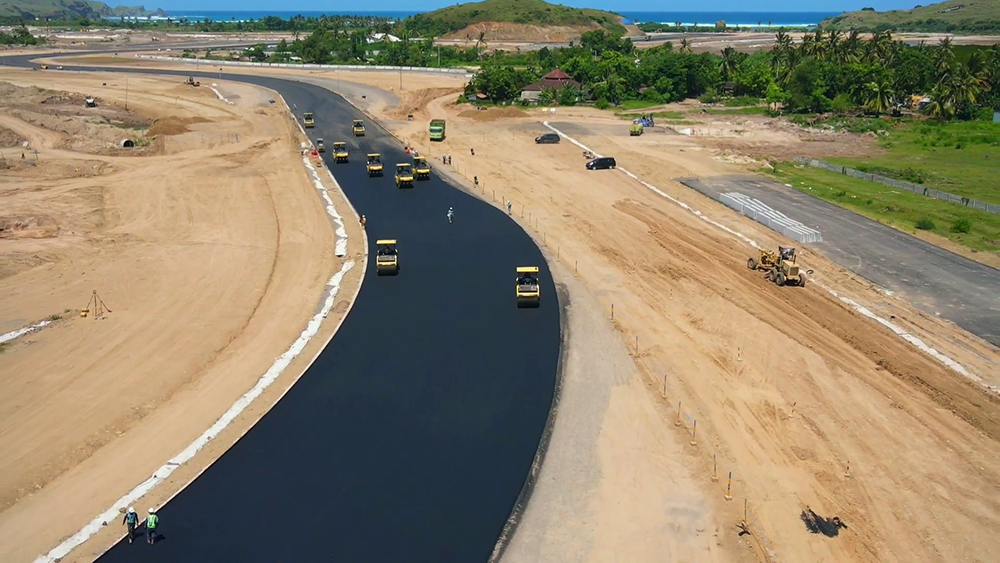
The use of 3D control systems offers great advantages, especially when paving banked curves. They allow the designs of the track layout to be implemented with exceptional precision. This highly accurate paving makes the surface especially even and reduces material consumption. Furthermore, where there is no stringline tensioning, it cannot cause any interference or inaccuracy - yet another factor that increases the paving quality and operational safety while speeding up completion of work. The 3D measuring and levelling systems are flexible in their use and compatible with all Bomag high-performance screeds.
To reduce the number of longitudinal joints, the client decided to use only two pavers side by side instead of the usual three. To achieve this, two screed extensions of 750mm each were used per paver, giving each a maximum working width of 9m. Extending the screed was easy, thanks to Bomag's Quick Coupling system because it enables short and safe set-up times without time-consuming bolting. Furthermore, Bomag pavers are equipped with heavy-duty screeds and extra-long screed plates that also ensured excellent pre-compaction and particularly even paving.
60mm binder course
A two-paver configuration was used for the binder course in phase 2. Meanwhile, a third paver was deployed to pave the wide curves as well as to establish the connection to the pit lane. One of the biggest challenges, however, were two sharp bends in the track layout. This section required detailed planning to ensure continuous asphalt paving without interruption.
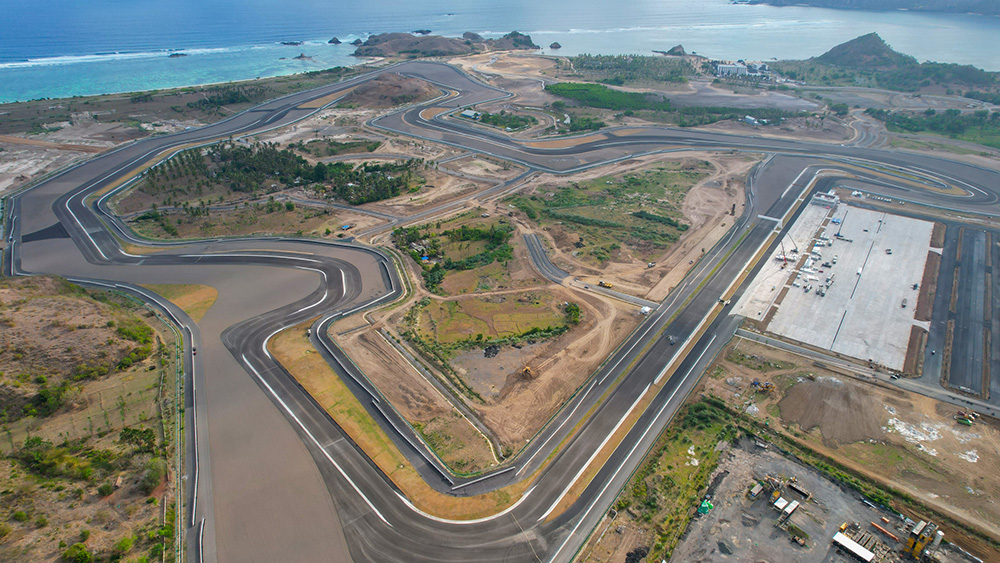
Here, too, paving was no problem for the two BF 800 C pavers because they offer an optimal view of the machine’s edge, hopper, auger and screed. The control panel and seat form an adjustable unit. All switches are arranged logically and ergonomically. This allows the operator to concentrate on what really counts: continuous and smooth asphalt paving.
In phase 3, the surface course consists of stone mastic asphalt (SMA mix) with polymer-modified bitumen. Coarse aggregate Tau stone from Palu, central Sulawesi – famous for its hardness – was used. But for the underlay asphalt, stone from North Lombok and East Lombok was used. Around 7,000 tonnes of Palu stone were transported in two stages for the asphalting. In addition, cellulose fibre additives from Germany were used to help bind stone and asphalt. Meanwhile, the limestone filler was brought in from Ponorogo and Probolinggo in East Java.
Paving took place in five segments to minimise the amount of the transverse joints. The sections were also defined precisely in order to meet the aesthetic requirements of the track. A three-paver configuration was used for this phase. It took five days to complete the entire surface course. Thanks to the hot-on-hot echelon paving method and the use of three pavers, the longitudinal joints are invisible. When paving hot-to-cold, there is the risk of joint failure, the biggest cause of early failure on asphalt in roads.

High temperatures are the secret to success in the paving process. Bomag pavers are equipped with Bomag Magmalife technology. All the heating rods are cast in an aluminium block. Aluminium's outstanding thermal conductivity enables significantly shorter heat-up times and thus faster operational readiness of the pavers and their crews. Another advantage is even heat distribution.
In phase one and two, the asphalt was compacted with Bomag BW 161 AD-4 articulated tandem rollers and BW 24 RH pneumatic tyred rollers. During the first two passes, the tandem rollers were used directly behind the pavers for static compaction. Next came two low-amplitude passes. Then it was the turn of the pneumatic tyred rollers.
For compaction of the surface course, only tandem rollers were used. This was due to the mix and to achieve the surface as required. These rollers ensured an optimum surface quality and the required degree of compaction of at least 98%. Surface texture was IRRA <0.9, meaning the pavement macrotexture had to reach not less than a 0.9mm after construction.
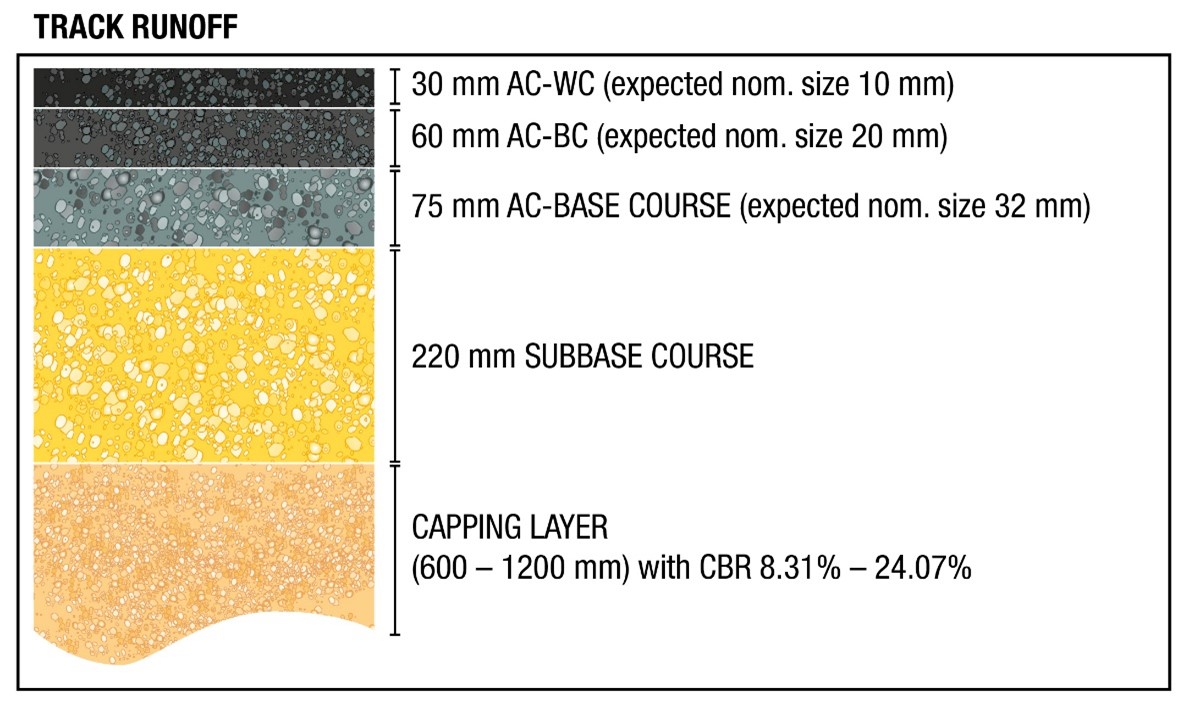
Thanks to the rollers' Bomag Economizer technology, there were no unnecessary passes. The system shows the degree of compaction on a display, enabling the operator to achieve the best compaction results. For the degree of compaction of the binder course, the test lab measured values of 98.9% (left-hand side of the track), 99.2% (centre of the track) and 99.1% (right-hand side of the track). There was also a non-nuclear density asphalt test on site.
At the end of the day, upwards of 76,000 tonnes of asphalt were laid and paving productivity was between 150–250 tonnes per hour. With the paving now complete and work forging ahead on other infrastructure, the Mandalika circuit is ready for its first races in front of very enthusiastic and much appreciative Indonesian racing fans.
For a video of Bomag's work on the track, click here.
Technical detail and information was supplied by Johannes Schröder, Bomag’s head of marketing with responsibility for dealer marketing, application training and business development in Southeast Asia and Pacific, including Korea, Japan and Taiwan. Schröder has been with Bomag since 2015 and is based in Singapore. He holds an engineering degree from Aachen University in Germany, a Masters in Engineering from Tsinghua University in China and an MBA from College des Ingénieurs in France.
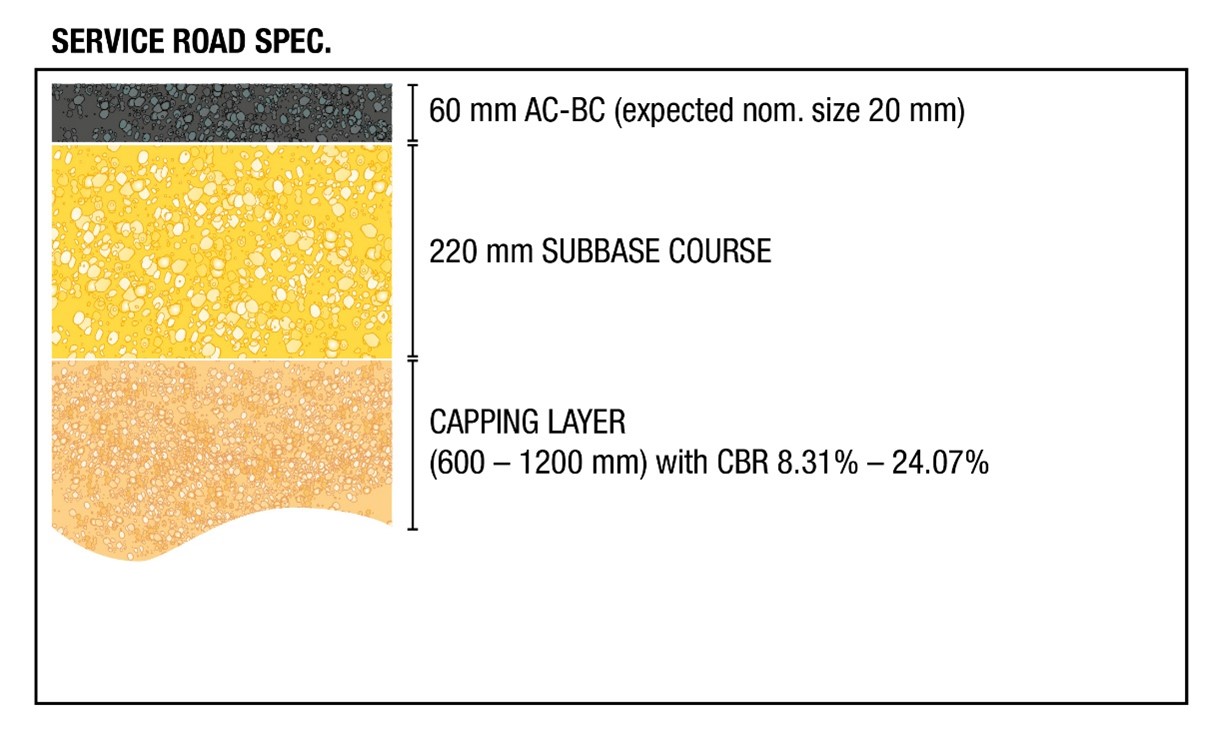
*Bomag is headquartered in Boppard, Germany, and is now part of the French Fayat Group. The company has more than 60 years’ experience facilitating the efficient and responsible expansion of road and transport infrastructures, focusing on earth and asphalt rollers, planers, pavers and walk-behind compaction technology. Bomag also offers an extensive and complete portfolio of stabilisers or recyclers and machines for refuse compaction as well as innovative digital services for the networked construction site. These include intelligent compaction control systems, such as Asphalt Manager - introduced as far back as 2001 - Ion Dust Shield technology for reducing fine dust pollution during cold milling and, currently, cloud services for intelligent real-time documentation on the construction site. Bomag has six branches in Germany and is globally active with 12 independent subsidiaries. With its 2,200 employees worldwide and a sales and service network of over 500 dealers in 120 countries, the company offers its customers a competent and responsive service on site. Bomag builds its machines in its own production facilities in Europe, China and the US: www.bomag.com
The fast lane
In late 2018, the Indonesian government signed a deal with French group Vinci Grands Projets for the construction and development of the Mandalika racing circuit and supporting facilities, as well has hotels. The course is officially the Pertamina Mandalika International Circuit, named so after Indonesia’s state-owned oil and natural gas mining company, Pertamina.
The 4.3km circuit, in the Mandalika resort area in the Central Lombok Regency of West Nusa Tenggara province, covers around 120 hectares. It is, in effect, a purpose-built race track that will incorporate some existing public roads. These will be closed off and used for motorsport events and then re-opened for normal traffic. The circuit complex will eventually include the construction of hotels and other facilities but because the track is set in a sensitive natural environment, the government has set aside a 3,000-hectare conservation area around the track. This area, with many native species, will be accessible for low-impact activities only, such as cycling or hiking in order to minimise damage to flora and fauna.
Indonesia held MotoGP - grand prix-level motorcycle racing events - in 1996 and 1997 as well as several World Superbike events from 1994 to 1997 at the 4km-long Sentul International Circuit in Bogor on the island of Java. The US$3 billion Mandalika circuit is billed as one of the so-called “10 New Balis” initiative announced by Indonesian president Joko Widodo in 2017. The goal is to build tourism hubs across the country to attract both foreign investment and tourists in areas that need economic support.
The track itself has 11 right turns and six left turns. Around 40 pit garages will be built as well as seating for more than 50,000 people in covered grand stands and standing room for up to 138,000. As of April, most of the track paving was completed but much work remains to be done on the pitlane, paddock area and other infrastructure that support international moto-sport events such as MotoGP. Despite this, Dorna, the organiser of international motorcycle racing, said the Mandalika circuit will host its first international event, the 2021 MOTUL FIM Superbike World Championship season finale later this month. The MotoGP, now scheduled for some time in 2022, will be the first such event in Indonesia since 1997.
For a fly-by of the race track taken by a drone in early April, visit: https://www.youtube.com/watch?v=0bYkZYUxW-s
Mrk1 Consulting
Mrk1 Consulting has designed dozens of international motorsport circuits around the world, including the Formula One street circuit in Baku City in Azerbaijan. In partnership with RoadGrip Motorsport Indonesia (RMI), Mrk1 Consulting has been instrumental in the development of the world’s first, purpose-built street circuit to host MotoGP. The Mandalika Grand Prix Association (MGPA) appointed Mrk1 to undertake the detailed design of the track as well as appointing Mrk1 staff in key roles on the project, including the interim chief operating officer. In addition, RMI and Mrk1 will provide the core operational team and event management services for a number of international events each year.
Front row of the grid
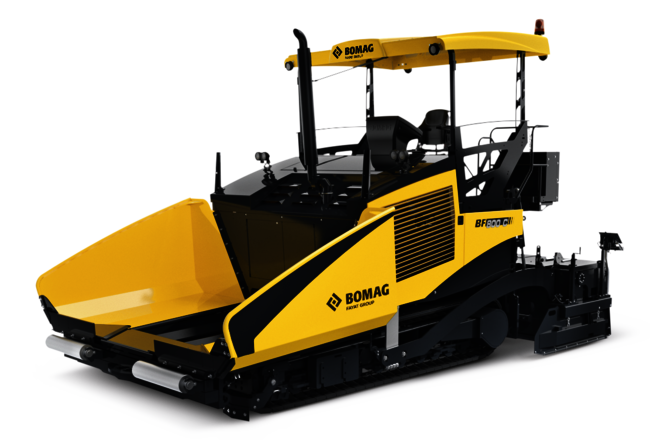
In pole position is Bomag’s Highway Paver BF 800. It comes equipped with 135kW engine, a weight of 21 tonne and a laying capacity of 800 tonnes per hour. Its big brother BF 900 offers 160kW of power, 22 tonne weight and 900 tonnes per hour laying capacity. Both can be extended to a working width of 10m. In addition:
- Proportional control of the augers and conveyor belts by means of ultrasonic sensors;
- Load control system for the screed;
- Easy and safe transportation through the hydraulically lowerable roof and fast screed fixing;
- High precompaction of up to 95% by means of an infinite vibration and tamper frequency;
- Longest crawler tracks guarantee best traction;
- The innovative ECOMODE, MAGMALIFE, QUICK COUPLING and SIDEVIEW ensure optimal safety and costefficiency;
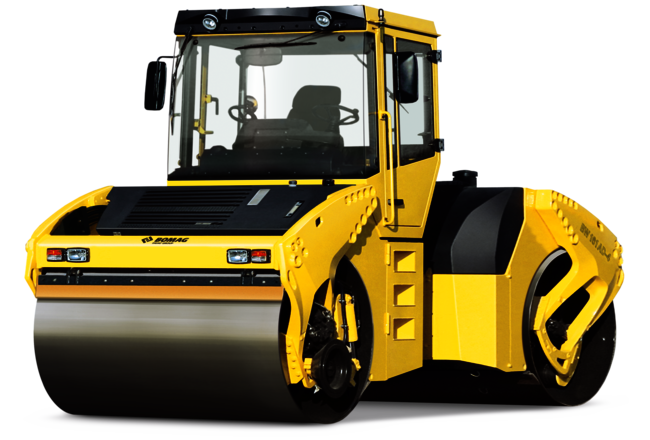
Bomag’s BW 161 AD-4 articulated tandem roller has many standard features. These include:
- Automatic vibration operation;
- Individual vibration control;
- Crab steer right/left 170mm;
- Operator's platform with two steering wheels;
- Two travel levers with integrated switches for vibration, one for crab steer right/left and one for edge pressing roller;
- Battery disconnect switch;
- Two amplitudes/two frequencies;
- Back-up alarm.
Meanwhile, the options are many, including a back-up alarm system, sun roof for the cabin, edge cutter, folding scrappers, a pressure sprinkling system with two pumps and the BOMAP compaction navigation with GPS.
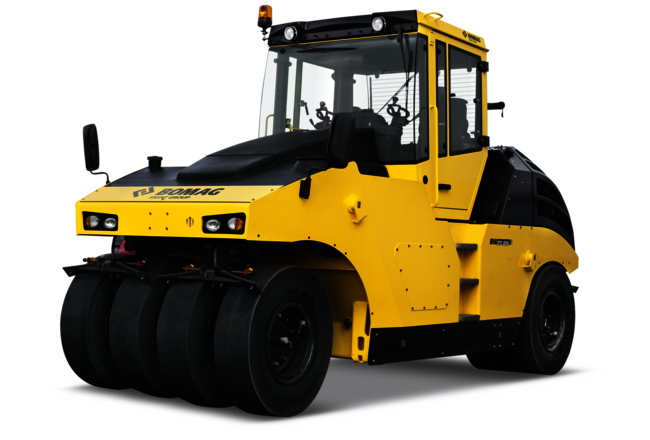
Bomag’s BW 24 RH pneumatic tyred rollers offer maximum uniform compaction, thanks to two steering pivots with axle and wheel-hub oscillation. The machine fully adapts to uneven surfaces and there is an automatic tyre-inflation system to between 2 and 8 bar. To ensure flexible weight adjustment, there is a large 3.5m³ ballast compartment and drainage for an optional water ballast. It is powered by a reliable Deutz engine and includes two hydraulic motors, two multi-disc brakes for parking and a dynamic service brake.