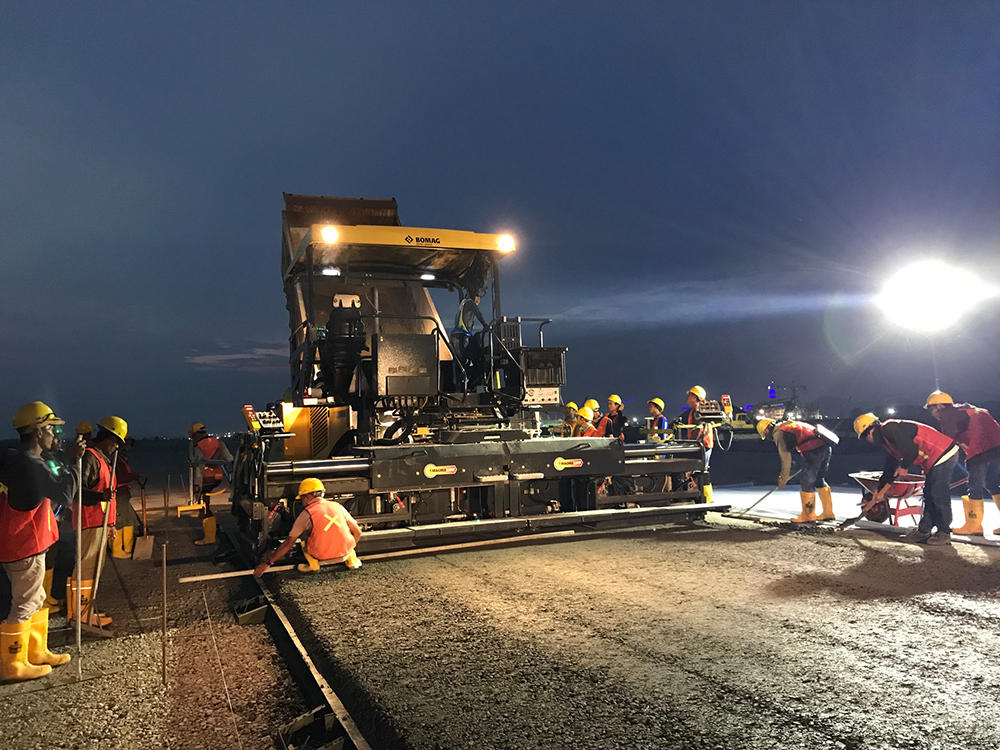
Demand has grown at PDG since it became operational with a capacity of 2.2 million passengers/year in 2005. By 2018 the airport was handling up to 4.2 million passengers/year, so plans were drawn up to expand capacity. A new terminal was planned, along with further improvements to the rest of the airport, boosting capacity by an additional 1.2 million passengers/year.
Minangkabau International Airport is located 23km from the centre of the city of Padang on Sumatra, Indonesia’s biggest island. The facility is owned and managed by PT Angkasa Pura II and the firm awarded a contract to PT PP Tbk to carry out the upgrading work.
In addition to building the new terminal, the work improvements required resurfacing of the main runway. Measuring 2,750m in length by 45m wide, the runway covers an extensive area, requiring considerable planning to ensure the work ran smoothly.
The first major task was to mill off the top 100mm of the old runway surface, as it was showing signs of wear. This then had to be replaced with a new 100mm layer of asphalt.
But the milling and paving job was made more complicated as the airport was still operational during construction. This meant that all of the construction work had to be carried out at night after air traffic control had closed the runway.
Machine checks and final preparation were conducted in the parking area while waiting for clearance to enter the runway to ensure that they were in good operating condition.
The state-owned contractor, PT PP Tbk used construction equipment from BOMAG to carry out the resurfacing works for this airport runway refurbishment project, having had good experience with the brand at its Soekarno-Hatta International Airport contract.
The company used an extensive fleet of BOMAG machines including a BM 2000 / 60 milling machine and two BF 800 C asphalt pavers. The fleet also included an extensive fleet of compaction machines from BOMAG, with four twin drum asphalt compactors, of which two were BW 203 ADs and two were BW 161 AD-4s, and seven BW 24 RH rubber tyred compactors. But due to the time-sensitive nature of the runway resurfacing project, speed and productivity were crucial to successfully completing the project on time.
The BOMAG machines proved productive and the milling machine, the BM 2000 / 60, carried out accurate cutting and quick removal of the distressed asphalt surface.
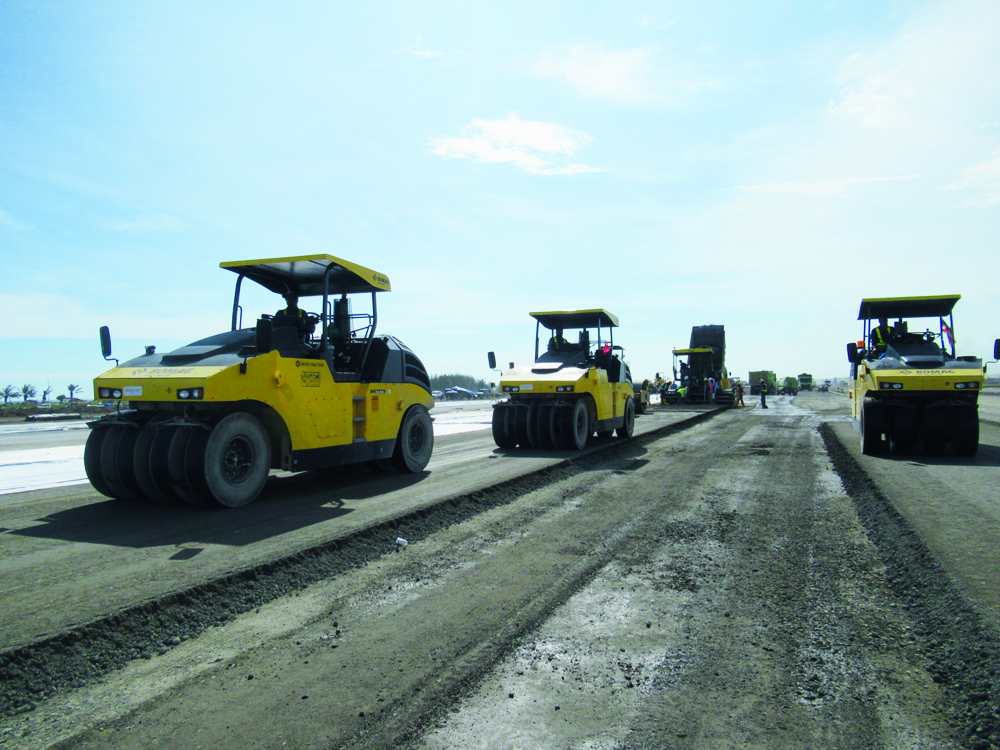
The paver BF 800 Cs laid new mats of 5m width with smooth, consistent and even surface achieving high pre-compaction rates. In combination with the use of the rollers the contractor was able to achieve the 98% compactionrequirement, a formality after final compaction with the BW 161 AD-4 and BW 24 RH units. The final compaction finish was then delivered using the rubber tyred BW 24 RH units.
Meanwhile, the New Yogyakarta International Airport (NYIA), also known as Kulon Progo International Airport, was built to replace the Adisutijitpo International Airport.
The Adisutijitpo International Airport only has a capacity of 1.2 million passengers/year but has been coping with up to 7.2 million passengers/year. Located at the Temon district of Kulon Progo Regency, the airport serves the Yogyakarta Special Region in Java, Indonesia.
The new airport is run and managed by PT Angkasa Pura I and work has been carried out on the facility by the contractor PT PP Tbk.
The firm selected a fleet of BOMAG equipment for the construction of a cement treated base course (CTB) for the runway. Measuring 3,250m in length by 60m wide, the CTB layer required a 200mm depth for the main taxiway and a 3omm depth for the taxiway shoulder.
The total volume of material placed was around 39,000m3, with a required density of 98% and a requirement for final compaction to be completed within 45 minutes. To ensure quality, one field thickness test was carried out/250m2, with one field density test/1,000m2.
For this job, the firm opted for BOMAG equipment to carry out the CTB construction at the New Yogyakarta International Airport’s runway. The firm used two BF 800 C pavers, four BW 161 AD-4 tandem rollers and four BW 24 RH pneumatic tyred, rollers. The firm set up 50m by 5m stretches with stringline and formwork in preparation for the CTB layer construction. Using the equipment, the target compaction requirement of 98% maximum dry density was achieved consistently throughout.