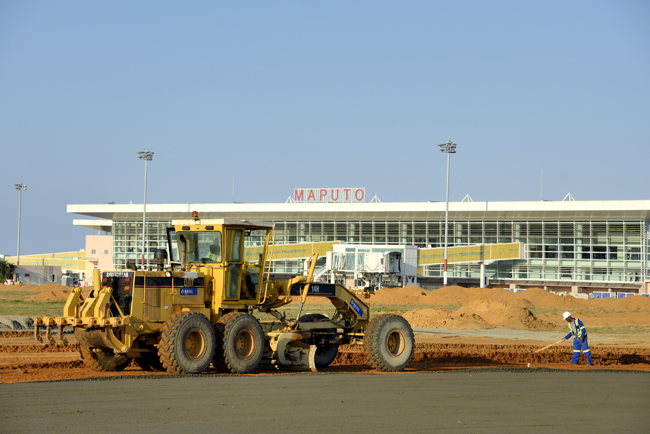
The project was needed as the existing runways were suffering from cracking and had longitudinal profiles that no longer met ICAO requirements. To address these problems, the construction work required laying new asphalt surfaces on the airport’s two runways and taxiways. In addition, the construction team laid 30,000m2 of concrete slab for aircraft parking, as well as building a new fuelling system and installing improved a lighting system on the runways and taxiways.
The project was carried out in partnership with the
The airport’s main runway measures 3.6km-long by 60m-wide, while the secondary runway measures 1.4km-long by 36m-wide. Both runways, as well as the taxiway links, had to be resurfaced with minimum 70mm-thick layers.
However flights to and from the airport were not interrupted as the construction work was carried out over a two years period, with much of the milling, paving and compaction duties having been carried out at night.
The existing runway and taxiway surfaces were removed using milling equipment, prior to the paving and compaction machines being used. Two BOMAG BM2000/60-2 milling machines with 2m-wide drums were used to plane the original runway surfaces. These planers removed the old surface layers in one pass, using Trimble total stations supplied by SITEC to provide accurate guidance and optimise the cutting process.
The contracting team used then BOMAG BF800C pavers featuring S50 screeds set to widths of 2.5-7.5m, with the machines working in echelon to allow hot to hot paving for better bonds. Compaction was carried out meanwhile using BOMAG BW141 AD-50 and BW202 AD-50 tandem rollers and BOMAG BW24 RH pneumatic tyre rollers.
The milled cuttings were not used as aggregates for the asphalt mix applied to the runway surfacing. However, this material was recycled and was used instead for the airport’s perimeter road as well as in the surface course for the shoulders of the secondary runway.
The asphalt was produced using Marini-Ermont TSM15 and TSM17 plants and delivered to the pavers using a fleet of large tipper trucks. The plants delivered three asphalt grades for the base, binder and surface courses, with the last utilising advanced polymer modified bitumen (PMB) technology.