A new high quality runway surface has been laid at Bremen City Airport. This has provided a much-needed replacement at the airport as the old runway was laid over 20 years ago and was suffering from cracking and potholes.
Laying the new surface required the airport to be closed, with the work having to be carried out in a tight time schedule. Contractor Heitkamp Erd- und Straßenbau was brought in to carry out the work as the firm had experience in runway rehabilitation projects having carried out pavemen
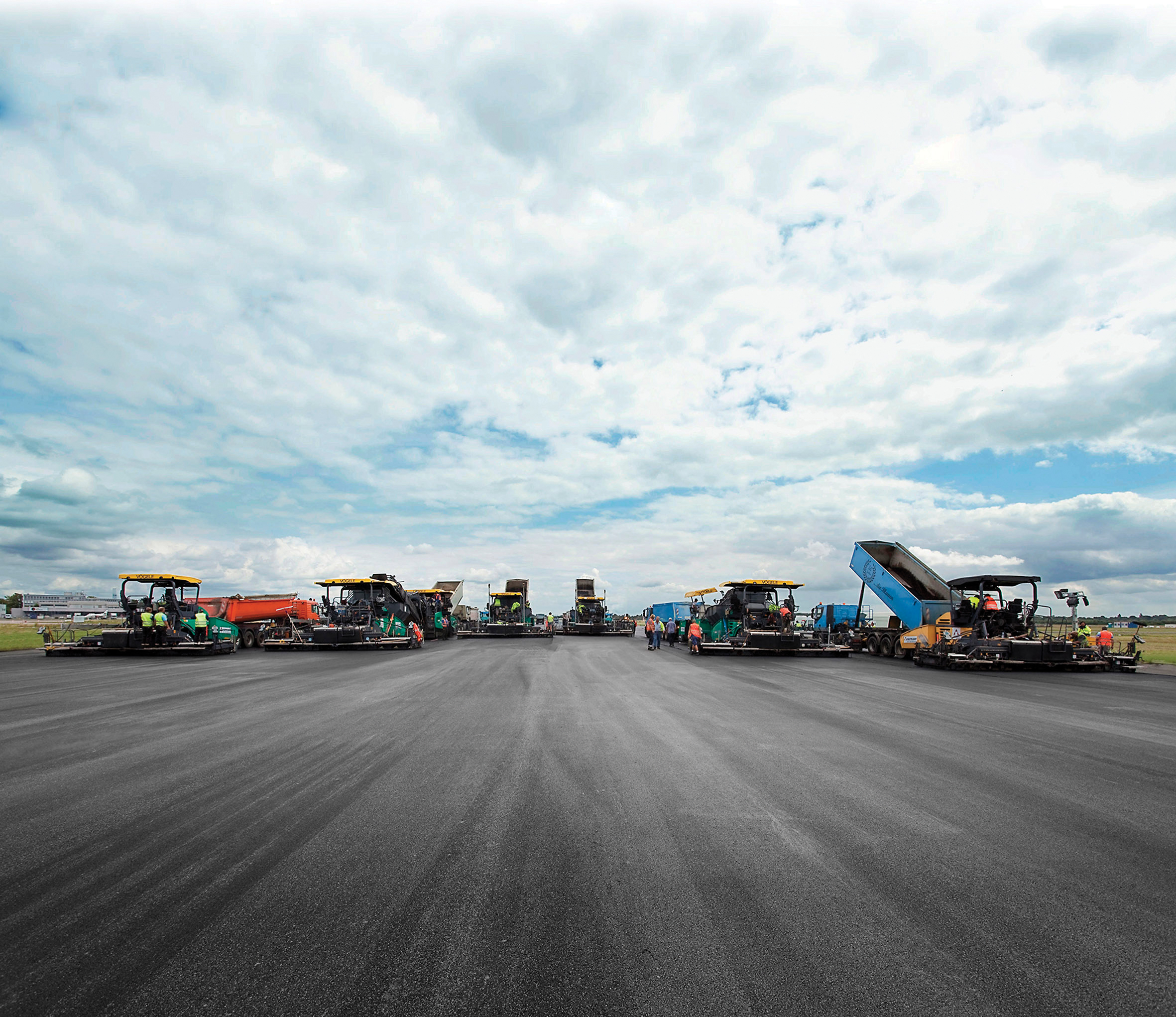
Efficient fleet operation meant that Bremen City Airport had its runway repaved with a high quality surface within the tight closure period
A new high quality runway surface has been laid at Bremen City Airport. This has provided a much-needed replacement at the airport as the old runway was laid over 20 years ago and was suffering from cracking and potholes.
Laying the new surface required the airport to be closed, with the work having to be carried out in a tight time schedule. Contractor Heitkamp Erd- und Straßenbau was brought in to carry out the work as the firm had experience in runway rehabilitation projects having carried out pavement rehabilitation at Zweibrücken Airport.At Bremen the contractor’s first task was to use its
The paving work required effective logistics, with up to 60 trucks being used to deliver a continuous flow of asphalt to the site from the asphalt plant. Some 19,000tonnes of binder course was used, with this being laid to a depth of 80mm by three
The combination of the compaction effect from the screed, the hot-to-hot joints and also the use of the Vögele 3D Navitronic Plus control system, helped ensure a good quality binder layer. The sophisticated Navitronic system used existing survey data for paving the two inner strips, optimising the profile accuracy as well as ensuring the surface was even. The system can control paving width, layer thickness and the longitudinal direction automatically.
The contractor then used six Vögele pavers to lay the wearing course in echelon, a combination of Super 1800-2 and Super 2100-2 machines. These laid the 40mm thick layer in paving widths of 7.5m, again using the hot-to-hot method. The high quality paving requirement called for the contractor to achieve an evenness of 3mm over a longitudinal distance of 4m, as well as to locate the necessary rain channels with high precision.
To ensure rainwater can drain effectively, the inner strips were paved with a transverse slope of 1.5%, while the outer strips were provided with a slope of 1%. All six of the pavers used Vögele’s Niveltronic Plus system for automated grade and slope control, with Multiplex Skis featuring sonic sensors to calculate a mean value and level out any irregularities in the base.
Providing a constant flow of asphalt into the paver helps with continuity and quality so the contractor employed material feeders for this task. Two of the latest Vögele MT3000-2 offset material feeders and two of the earlier Vögele MT1000-1 feeders were employed for this task. The MT3000-2 feeder can supply 1,200tonnes of mix/hour and also holds up to 40tonnes of material, allowing it to supply up to two pavers at a time using its pivoting offset conveyor.
Using this fleet of equipment the contractor was able to remove the old runway surface and replace it with a new high quality pavement that met the required specifications within a 149 hour closure window, just as planned.