Increases in flight numbers from the Frankfurt Hahn airport have resulted in necessary improvements to the facility, including new runway surfaces. The former German military airbase has been used as a civilian airport since 1993 but is now Germany's fifth largest air cargo hub and handles some 40,000 flights/year.
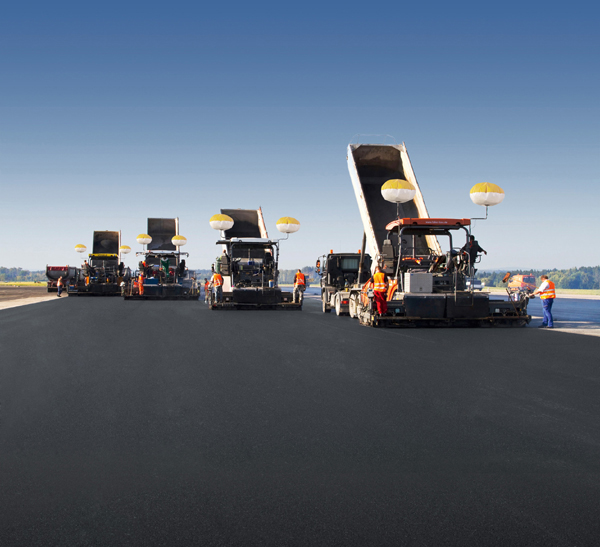
A team of Vögele pavers working echelon was used to place the new runway surface and this helped ensure a good quality bond between joints for a better quality finish and a longer working life
Increases in flight numbers from the Frankfurt Hahn airport have resulted in necessary improvements to the facility, including new runway surfaces. The former German military airbase has been used as a civilian airport since 1993 but is now Germany's fifth largest air cargo hub and handles some 40,000 flights/year. Coupled with the effects of a harsh winter, the runway was in need of resurfacing so a team of machines, including six 1194 Vögele pavers and numerous other machines from the 364 Wirtgen Group, was brought in to handle the job.
The first section of the runway was upgraded in April 2010, while the Icelandic ash cloud held air traffic in check. Later in the year, the six Vögele pavers and other machines were brought to the site to finish the rest of the runway. The airport had other improvement plans too. During the break in flights, the aim was to replace the navigation beacons, carry out work on the drainage system and repair the edges of the runway, with all the work having to be completed more or less simultaneously.
High-precision work at maximum speed was required, as the aim was to minimise disruptions to flight operations. The contract for rehabilitating 65,000m2 of runway was awarded to a consortium comprising the contractors2710 Bopparder Asphaltbau, 2711 Thomas Bau, Faber and Asphaltbau Hunsrück. The team had no more than three days in which to complete the job. This called for numerous operations to be carried out simultaneously, with logistics a key part of the project.
The equipment fleet deployed for the project included seven milling machines, six pavers and a host of rollers. There were also numerous lorries supplying mix, as well as vehicles from companies carrying out the other construction tasks. The seven Wirtgen milling machines started the runway repair by removing the wearing course and binder course to a depth of 140mm. The milling machines were given a four-hour head start in order to prepare enough of the runway for asphalt paving. This allowed the first four pavers to set to work while the milling machines were still busy on other sections. Two Vögele SUPER 2100-2 pavers worked alongside two Vögele SUPER 1800-2 machines and all four machines were fitted with the TP-2 extending screeds, featuring tamper and two pressure bars. The pressure bars came in useful for achieving the high pre-compaction of the base course required for this job. At Frankfurt-Hahn Airport, the paving team was also able to take advantage of the capability of having the high compaction system switched on and off as required.
Grade and slope control was a challenge as the runway had to be even and free of irregularities. The paver operators used Vögele's NIVELTRONIC Plus system, which was combined with multi-cell sonic sensors referenced from the edges of the previously paved strips. Equipped with high compaction screeds and multi-cell sonic sensors, the four pavers placed the new binder course and wearing course in strips, 5-6m wide and hot to hot. As work progressed, a total of six Vögele pavers were in operation and these laid roughly 14,400tonnes of mix for 90mm binder course and 8,400tonnes of mix for 50mm wearing course.
Logistics were important and the continuous supply of asphalt by the truck fleet was vital to the project, while228 Hamm rollers played a crucial role in the compaction duties. However, despite the complexities of the project and the large working crew required, the work was finished one hour ahead of the set 67.5 hour schedule.
The first section of the runway was upgraded in April 2010, while the Icelandic ash cloud held air traffic in check. Later in the year, the six Vögele pavers and other machines were brought to the site to finish the rest of the runway. The airport had other improvement plans too. During the break in flights, the aim was to replace the navigation beacons, carry out work on the drainage system and repair the edges of the runway, with all the work having to be completed more or less simultaneously.
High-precision work at maximum speed was required, as the aim was to minimise disruptions to flight operations. The contract for rehabilitating 65,000m2 of runway was awarded to a consortium comprising the contractors
The equipment fleet deployed for the project included seven milling machines, six pavers and a host of rollers. There were also numerous lorries supplying mix, as well as vehicles from companies carrying out the other construction tasks. The seven Wirtgen milling machines started the runway repair by removing the wearing course and binder course to a depth of 140mm. The milling machines were given a four-hour head start in order to prepare enough of the runway for asphalt paving. This allowed the first four pavers to set to work while the milling machines were still busy on other sections. Two Vögele SUPER 2100-2 pavers worked alongside two Vögele SUPER 1800-2 machines and all four machines were fitted with the TP-2 extending screeds, featuring tamper and two pressure bars. The pressure bars came in useful for achieving the high pre-compaction of the base course required for this job. At Frankfurt-Hahn Airport, the paving team was also able to take advantage of the capability of having the high compaction system switched on and off as required.
Grade and slope control was a challenge as the runway had to be even and free of irregularities. The paver operators used Vögele's NIVELTRONIC Plus system, which was combined with multi-cell sonic sensors referenced from the edges of the previously paved strips. Equipped with high compaction screeds and multi-cell sonic sensors, the four pavers placed the new binder course and wearing course in strips, 5-6m wide and hot to hot. As work progressed, a total of six Vögele pavers were in operation and these laid roughly 14,400tonnes of mix for 90mm binder course and 8,400tonnes of mix for 50mm wearing course.
Logistics were important and the continuous supply of asphalt by the truck fleet was vital to the project, while