An airport in Germany has seen the use of very innovative asphalt paving techniques, with the use of dual-layer, hot-to-hot working. The method was used to meet a very tight schedule for the runway rebuilding work, while also delivering the high quality required.
Two InLine Pave trains from Vögele were used at Rostock-Laage Airport to lay a new surface and binder course. The operation was innovative as the process used both hot-to-hot, echelon paving as well as dual layer, hot-on-hot working. Using this
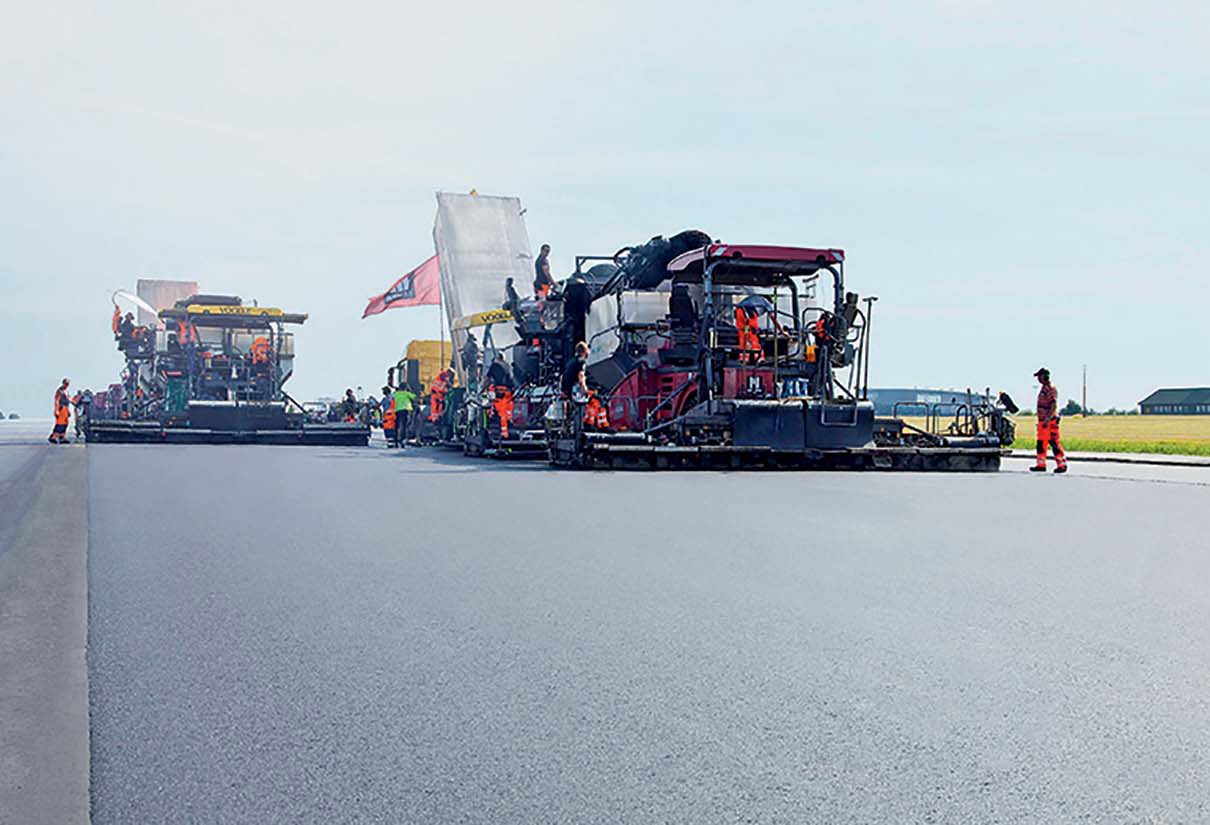
The two paving trains worked in echelon to ensure a good asphalt joint
An airport in Germany has seen the use of very innovative asphalt paving techniques, with the use of dual-layer, hot-to-hot working. The method was used to meet a very tight schedule for the runway rebuilding work, while also delivering the high quality required.
Two InLine Pave trains from1194 Vögele were used at Rostock-Laage Airport to lay a new surface and binder course. The operation was innovative as the process used both hot-to-hot, echelon paving as well as dual layer, hot-on-hot working. Using this innovative operation allowed the Kemna Schwerin Tief- und Straßenbau, to complete its job within a record short timescale while also delivering high paving quality.
The need for the fast runway replacement had become crucial. First bubbles and then cracks had formed on the 2.5km runway at Rostock-Laage Airport and there was concern that small pieces of asphalt would break off, with potentially serious results. Small objects just 4mm across can be sufficiently large to cause major engine damage to an aircraft, with the risk of failure on take-off. This meant that large sections of the 2.5km-long runway had to be resurfaced as quickly as possible, in order to minimise flight disruptions.
Using two InLine Pave trains working alongside each other offered the chance to finish the work quickly, while also delivering the critical specification required. Bernd Kanscheit, an engineer at engineering consultancy Mecklenburgisches Ingenieurbüro für Verkehrsbau, Germany explained, "Firstly, InLine Pave gives you an excellent bond between layers – which prevents bubbles from forming. Secondly, the InLine Pave surface is very dense and low in voids, so neither water nor de-icing agents can cause damage. Thirdly, we benefit from the very high compaction of the binder course in the InLine Pave process. It is higher than in conventional paving. That's particularly important to us here. After all, the characteristic load profile of the take-off and landing runway means we cannot expect post-compaction by vehicles".
In addition to the requirements for the asphalt, other features of the dual-layer paving method also made it a suitable selection. This method allowed the binder and surface course to be laid in one pass, increasing productivity. And with the paving being carried out during potentially cool autumn weather, the retained heat of dual-layer paving also helped ensure effective compaction before the mat cooled. Once the go-ahead was given, the contractor had 10 days in which to mill off the 95,300m2 centre portion of the take-off and landing runway, lay the asphalt with a new profile, apply all the required markings and clean the whole surface. Flights at the airport, which is for both military and civilian use, were suspended during this period.
Four2395 Wirtgen W 210 milling machines were used to remove the asphalt. The Kemna team began to lay a level regulating layer of asphaltic concrete while the milling work was still going on. Using two SUPER 2100-2 Vögele pavers, the team paved a layer 4–8cm thick to provide water drainage and with a slope angle of 1.5% to each side. The grade and slope control was carried out in the longitudinal direction by scanning tensioned wires. Meanwhile, Kemna was also working hot-to-hot with the Vögele pavers. A quasi-jointless strip with a width of approximately 15m was laid on both sides, starting from the middle.
Using dual-layer paving allowed a thin surface course of just 2.5cm instead of the more usual 4cm to be used, as the method allows effective bonding with the binder course underneath. "We based our measurements of the surface course on the requirements of the German terms and guidelines for the construction of asphalt roadways (ZTV Asphalt StB). The operators of the airport were delighted with the savings this delivered in terms of surface course material," Kanscheit explained. Minimising the costs of future maintenance operations was also the reason for another technical requirement set by the airport. The runway was to have no longitudinal joint for 10m to the right and left of the middle, "because experience has shown that the maintenance intervals are the longest then," said Kanscheit.
Kemna completed the paving with two InLine Pave trains in just three days. On the first day the teams, each consisting of two pavers and a material feeder, worked in parallel on the outside edges of the landing runway, with each laying a 7.5m-wide strip. The second day saw the binder and surface courses being laid hot-on-hot and hot-to-hot. Starting from the middle of the runway, a 15m-wide compact asphalt pavement was constructed in a single pass. On the third day, the final asphalt strip, 15m wide, was laid on the opposite side in the same procedure.
The whole job took 10 days, with the contractor laying 17,700tonnes of asphalt in just three days.
The changes in the pave widths of the screeds were achieved as Vögele equips its InLine Pave trains with extending screeds allowing widths of 3-8.5m. This enabled Kemna to lay about 5,900tonnes of asphalt on each of the three successive working days while meeting the high-quality requirements of the customer. "The hot-to-hot joint is as good as invisible", said Torben Eymer, engineer and site manager. Planner Kanscheit added, "Samples show that there are no structural irregularities in the binder at the joint. And that's exactly what's required."
An important role in the paving process was played by material transfer equipment. A Vögele PowerFeeder MT 3000-2 Offset unit was used to supply asphalt to the pavers. With a paving speed of about 4m/minute and a paving width of 7.5m, the offset material feeder delivered some 400tonnes/hour of material to the pavers, of which about 280tonnes was for the binder course and 120tonnes was for the surface course. The offset material feeder was also of benefit for laying the 3.4m shoulder. "If the mix had been delivered directly by a lorry, the existing edge of the surface up to the shoulder would certainly have sustained damage. Thanks to the pivoting conveyor, the lorries were able to drive alongside,” said site manager Eymer.
Two InLine Pave trains from
The need for the fast runway replacement had become crucial. First bubbles and then cracks had formed on the 2.5km runway at Rostock-Laage Airport and there was concern that small pieces of asphalt would break off, with potentially serious results. Small objects just 4mm across can be sufficiently large to cause major engine damage to an aircraft, with the risk of failure on take-off. This meant that large sections of the 2.5km-long runway had to be resurfaced as quickly as possible, in order to minimise flight disruptions.
Using two InLine Pave trains working alongside each other offered the chance to finish the work quickly, while also delivering the critical specification required. Bernd Kanscheit, an engineer at engineering consultancy Mecklenburgisches Ingenieurbüro für Verkehrsbau, Germany explained, "Firstly, InLine Pave gives you an excellent bond between layers – which prevents bubbles from forming. Secondly, the InLine Pave surface is very dense and low in voids, so neither water nor de-icing agents can cause damage. Thirdly, we benefit from the very high compaction of the binder course in the InLine Pave process. It is higher than in conventional paving. That's particularly important to us here. After all, the characteristic load profile of the take-off and landing runway means we cannot expect post-compaction by vehicles".
In addition to the requirements for the asphalt, other features of the dual-layer paving method also made it a suitable selection. This method allowed the binder and surface course to be laid in one pass, increasing productivity. And with the paving being carried out during potentially cool autumn weather, the retained heat of dual-layer paving also helped ensure effective compaction before the mat cooled. Once the go-ahead was given, the contractor had 10 days in which to mill off the 95,300m2 centre portion of the take-off and landing runway, lay the asphalt with a new profile, apply all the required markings and clean the whole surface. Flights at the airport, which is for both military and civilian use, were suspended during this period.
Four
Using dual-layer paving allowed a thin surface course of just 2.5cm instead of the more usual 4cm to be used, as the method allows effective bonding with the binder course underneath. "We based our measurements of the surface course on the requirements of the German terms and guidelines for the construction of asphalt roadways (ZTV Asphalt StB). The operators of the airport were delighted with the savings this delivered in terms of surface course material," Kanscheit explained. Minimising the costs of future maintenance operations was also the reason for another technical requirement set by the airport. The runway was to have no longitudinal joint for 10m to the right and left of the middle, "because experience has shown that the maintenance intervals are the longest then," said Kanscheit.
Kemna completed the paving with two InLine Pave trains in just three days. On the first day the teams, each consisting of two pavers and a material feeder, worked in parallel on the outside edges of the landing runway, with each laying a 7.5m-wide strip. The second day saw the binder and surface courses being laid hot-on-hot and hot-to-hot. Starting from the middle of the runway, a 15m-wide compact asphalt pavement was constructed in a single pass. On the third day, the final asphalt strip, 15m wide, was laid on the opposite side in the same procedure.
The whole job took 10 days, with the contractor laying 17,700tonnes of asphalt in just three days.
The changes in the pave widths of the screeds were achieved as Vögele equips its InLine Pave trains with extending screeds allowing widths of 3-8.5m. This enabled Kemna to lay about 5,900tonnes of asphalt on each of the three successive working days while meeting the high-quality requirements of the customer. "The hot-to-hot joint is as good as invisible", said Torben Eymer, engineer and site manager. Planner Kanscheit added, "Samples show that there are no structural irregularities in the binder at the joint. And that's exactly what's required."
An important role in the paving process was played by material transfer equipment. A Vögele PowerFeeder MT 3000-2 Offset unit was used to supply asphalt to the pavers. With a paving speed of about 4m/minute and a paving width of 7.5m, the offset material feeder delivered some 400tonnes/hour of material to the pavers, of which about 280tonnes was for the binder course and 120tonnes was for the surface course. The offset material feeder was also of benefit for laying the 3.4m shoulder. "If the mix had been delivered directly by a lorry, the existing edge of the surface up to the shoulder would certainly have sustained damage. Thanks to the pivoting conveyor, the lorries were able to drive alongside,” said site manager Eymer.