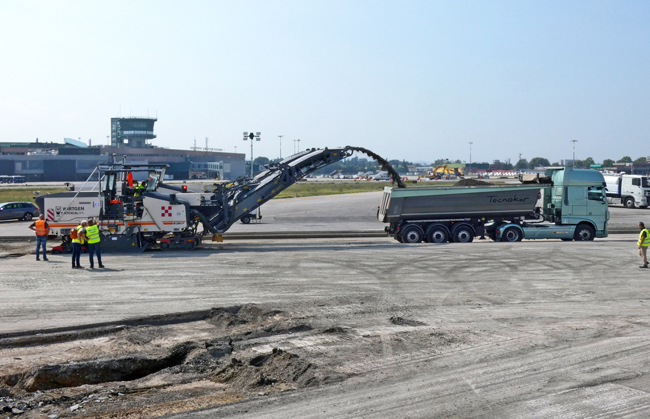
Airport runways face special challenges with regard to the loads they carry on a daily basis, particularly when aircraft are landing. A modern jet aircraft will typically land at speeds of around 240-260km/h, with a laden 747 weighing as much as 265tonnes at the end of a long flight.
The stresses these large aircraft place on runway surfaces are enormous and not just with the massive impact forces exerted during landing. As soon as an aeroplane is safely on a runway the pilot will often brake hard, exerting huge shear stresses on the runway surface.
Meanwhile, the loads exerted on the undercarriage of a large aircraft during landing are also massive. Clearly, the smoother the runway is, the lesser the shocks to the undercarriage system and the safer each landing will be.
To deliver the safety standards required means that runway surfaces have to be paved to exacting requirements so as to ensure that both smoothness and skid resistance values are within the tightest tolerances. The runway structure itself has to be sound, as even minor subsidence cannot be tolerated. To this end, many runways are built with a thick concrete base overlaid with asphalt layers, a design that combines structural strength with a smooth running surface and high skid resistance.
Meanwhile, the high-quality asphalt itself has to be able to maintain its mechanical performance across a wide range of ambient temperatures and also able to endure spillages of fuel and hydraulic oil, as well as periodic blasts of heat from jet engines.
At Bologna Airport in Italy, heavy wear and tear on the runway meant that improvements to the surface were becoming necessary. The airport authorities had monitored the condition of the surface since its extension in 2004 and were keen to keep working efficiency and safety at a maximum, opting to resurface key stretches of the runway.
The airport has a single main runway, 12/30, which features an asphalt surface and measures 2,800m in length by 45m wide. To carry out the necessary work, the runway was shut from 00:01am on the 14th September 2018 to 06:00am on the 18th September 2018. During this tight timeframe, the construction crew was able to carry out the maintenance works on the runway as well as for the taxiway.
The dates for this work were fixed well ahead of time and took into account an array of factors including those for technical, operational and weather issues, so as to allow the work to be carried out efficiently. All flights to and from Bologna airport had to be cancelled during this period. The airlines using the airport had all been informed well in advance, giving them the opportunity to plan ahead also. Some flights were cancelled while others were moved to neighbouring airports.
Lead contractor Costruzioni Generali Infrastrutture (CGI) won the job to mill, repave and compact the 66,000m2 area of runway, facing the tough challenge of making sure the new surface met the demanding smoothness requirements of the airport authorities. The job was all the more demanding as the work had to be completed within this 102-hour timeslot from the 14th September to the 18th September.
With the project involving the coordination of 25 companies, 500 personnel and 450 separate items of machinery or vehicles, CGI required a technology that would make the process run as smoothly as possible. The lead contractor opted for the latest technology from Topcon Positioning, using its SmoothRide system to optimise operations. Employing this system allowed the builders to ensure the ambitious project was completed with optimum efficiency and precision.
Manuel Ferrara from CGI explained: “Due to the time constraints, we needed stringent logistic organisation of all personnel in order to minimise inefficiencies and make sure we didn’t lose even one minute. It was necessary to foresee every single aspect of the construction site, with dozens of tasks needing to be completed simultaneously. Production was planned to the minute.”
Magnet Resurfacing software was also used to analyse the recovered data embedded in the 3D model, as well as for redesigning the surface and finalising the plans.
Collecting a huge dataset meant that every problem or undulation in the existing surface could be captured precisely in the model. Conventional surveying technology only collects data at certain points, so imperfections in a surface between the points would not be captured. Worse still, this would result in surface undulations for example being replicated in the new surface. While conventional survey systems may well highlight smoothness at specific points, they will be unable to detect longitudinal undulations occurring over a distance of several metres.
However, the more accurate dataset recovered by the scanning process allows the removal and resurfacing operations to deliver a smooth surface. Using this method provides a more accurate control of the milling process, removing exactly the correct quantity of material to ensure longitudinal smoothness. Leaving a more precise (and smoother) milled surface then allows for a more efficient paving operation, as the contractor no longer has to make up for any deficiencies by controlling the quantities of asphalt to compensate for any existing undulations in the surface. With asphalt costs being high, the more accurate control of the milling operation also cuts material costs considerably.
“The processing of the scanned surfaces was carried out very quickly,” said Cristiano Volz, product sales manager for construction at Topcon Positioning. “It was possible to make a real-time comparison between the state of the track and the project plans, identifying where any improvements to the design solutions were necessary and correcting any errors.”
Once the original runway surface had been removed completely, the same profile set by the first milling passes were followed precisely when it came to laying down the new asphalt layers using
Integrated efficiency
Throughout the resurfacing contract, it was essential that the equipment fleet was able to work quickly so as to stay within the tight time schedule. Meanwhile, the machine also had to deliver optimum accuracy, which was assisted by the integration of design, machine control and operations arising from the use of sophisticated technology. The precision of the initial milling operation provided an accurate reference for the subsequent milling and paving machines to follow. There was no need for 3D correction systems to be installed as the equipment was already working to grade.
Ferrara commented, “Topcon’s integrated system provided us with a considerable advantage in terms of precision of intervention, coordination of the machinery used and optimisation of the project. The challenges were tackled with the help of technology from the start of, and throughout the project, which enabled interaction between what was planned and the actual machines used to execute this plan. It also allowed for an open and constructive dialogue and extensive collaboration between all parties involved.”
The use of six pavers working in echelon also allowed for paving to be carried out in record time. As the pavers worked alongside each other, the joints were paved hot to hot, ensuring a better bond. This vastly reduces the risk of a joint problems over time, a point worth noting as joint failure due to the ingress of moisture and subsequent freeze/thaw issues provide the primary cause for asphalt surface replacement.
The pavers were also fed using material transfer vehicles, providing a more homogenous mix and with reduced material or heat segregation, issues that might otherwise cause subsequent surface problems also.
Ferrara added that the integrated SmoothRide satellite technology helped to ensure that the work could be carried out in the tight time schedule, despite the number of machines and personnel working on the job. He said that while the company has used more conventional technology in the past for large runway jobs, the benefits of this newer system allowed the work to be carried out more quickly and to higher precision than previously.
Transport hub
Bologna Airport is situated around 6km to the north-west of the city. Located in Italy’s Emilia-Romagna region, the airport is named after the famous Italian engineer and inventor, Guglielmo Marconi, who was born in Bologna and is best known for his pioneering work in developing radio transmissions.
The airport is handling more passengers than ever before, which further boosted the need for the runway redevelopment work. In 2018 the airport handled a record 8,506,658 passengers, an increase of 3.8% from the previous record of 8,198,156 who passed through the facility in 2017, itself a 3.1% jump from the 7,680,992 using the facility in 2016. Aircraft movements have similarly increased, rising 11.5% to 69,697 in 2016.
The airport is located close to the factories that build the famous Italian performance car brands, Ferrari and Maserati, as well as the motorcycle firm Ducati. The airport plays an important role in the operations for all three factories.
In addition, the airport is also in the vicinity of the Caterpillar road machinery factory at Minerbio as well as the Marini asphalt plant factory at Ravenna.