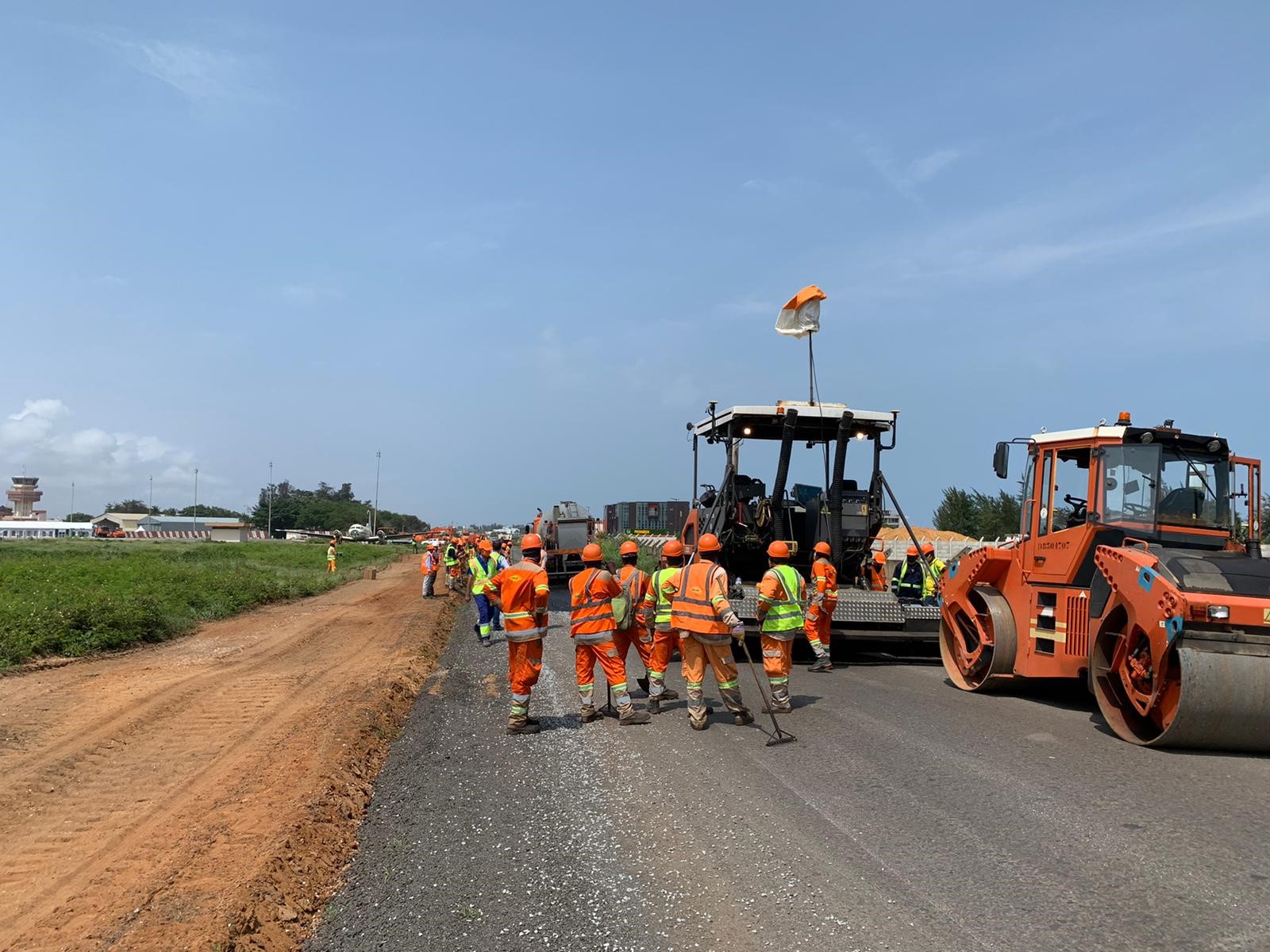
Benin, a French-speaking country of around 12 million, sits on West Africa’s Gulf of Guinea. Located in the Cadjehoun neighbourhood of Cotonou, the largest city in Benin, is Cotonou Cadjehoun Airport. This, country’s largest airport, serves as the primary entry point into Benin by air, with flights operating between Africa and Europe from a growing number of international airlines.
New airport facilities were constructed in 2011 and during the following decade, the airport has been upgraded and improved almost continuously. However, with a new objective of tripling its capacity from 500,000 passengers annually to 1.5 million passengers, major structural updates were required this time.
For tackling a project of this scale, compliance was paramount. Only when the airport was upgraded to meet international safety standards and quality would it be possible to greet more passengers from around the world.
Recognising the magnitude of the works, in 2020 the government of Benin invested just over US$16 million to bring the airport up to standard, improve its safety and rehabilitate the runway.
The project was for the client Benin Airports in partnership with ANAC, the country’s civil aviation authority (Agence Nationale de l'Aviation Civile) and ASECNA, the pan African Agency for Aerial Navigation Safety in Africa and Madagascar (L'Agence pour la Sécurité de la Navigation aérienne en Afrique et à Madagascar - an air traffic control agency based in Dakar, Senegal).
Work started in March 2020. Led by contractor Colas Afrique, the entire resurfacing and partial structural recovery of the runway covered over 2,500m. “We needed an efficient solution at the milling stage that could be applied accurately and efficiently, from a provider with a strong track record of delivering smooth, safe runways for some of the world’s busiest airports,” says Gilles Richard, director of operations at Colas Afrique.
To deliver this quality result within the timeframe required, efficiency was key so Colas brought in Topcon to provide its latest surveying and 3D guidance technology.
Before work on the runway could begin, Topcon’s RD-M1 road scanner was used to conduct an initial scan. With the ability to scan a vast distance in a short time, collecting detailed surface data without the need for prolonged runway closures, this tool played an important role for the project, explains Gael Basseville, director of business development at Topcon Positioning.
“When working on airport runways, safety is the ultimate priority. Precise planning is vital to achieving compliance and our RD-M1 is the ideal tool to deliver a highly scrutinised design from the offset,” says Basseville. “Together with our partner Smartfleet, we worked closely with Colas at this stage, offering full technical support and guidance to ensure a high-quality end result.”
Using the data collected from the RD-M1 scanner, it was then time to begin the milling process. The system is built on Topcon’s industry-leading Sonic Tracker for tight vertical thickness control, complemented by a GNSS system to deliver deliberate positional guidance. This technology a versatile solution to accurately mill and remove variable depths from the existing surface as needed. It is ideal for projects with long sections that need to be resurfaced, such as airport runways, as it optimises labour time and helps limit material usage further down the line – eliminating the need for often costly and time-consuming re-work.
“Equipped with our 3D guidance system, milling machines can calculate their exact position at all times, providing the smoothest surface for a paver to follow,” says Basseville. “In summary, the precise thickness control with compensation for differential compaction is delivered through machine control guidance in the first pass every time.”
Having a smoothly milled surface to work from as a base ensured that the new pavement on top would offer a more consistent smoothness. The technology also helped reduce the quantity of asphalt required by optimising smoothness of the base. Volvo CE paving equipment was used to lay the asphalt on the milled surface.
Use of both RD-M1 and RD-MC technologies was instrumental in facilitating efficient work at the airport and the easy-to-use nature of the technologies meant that local teams were able to carry out the work. This was extremely important to Hervé Breton, director general of Benin Airports. “When working so hard to improve a nation’s infrastructure, it’s important to use the project to boost employment and up-skill within the local region,” says Breton.
“Topcon offers progressive and modern technology, but also extensive training, which meant we were able to employ local workers to carry out the resurfacing.”