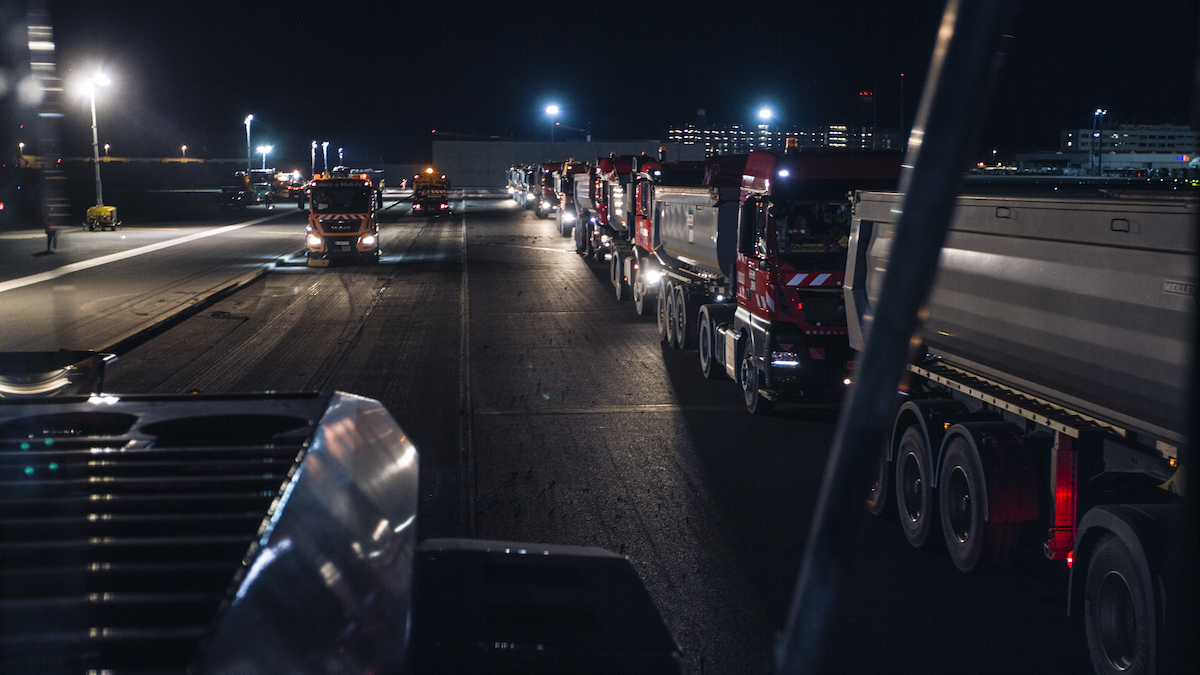
The use of efficient new construction technology at Frankfurt Airport has delivered a new runway surface within a tight timeframe
Handling up to 450 take-offs/day, Runway West is Frankfurt Airport’s busiest runway. Over 50% of the aircraft taking off from the airport uses Runway West, and a point worth noting is that this German airport is one of the busiest in Europe. In 2016, Frankfurt Airport handled nearly 61 million passengers, surpassed by Schiphol in Amsterdam and Charles de Gaulle in Paris, Europe’s third and second busiest airports respectively. Meanwhile London’s Heathrow remained Europe’s busiest airport and handled close to 76 million travellers.
Because of the sheer volume of air traffic and the forces delivered by heavily laden aircraft travelling at high speeds, the structural loads exerted on the runway are very high. The runway is subjected to enormous forces every day, and, in addition to the effects of the weather, this affects the structure of the asphalt surface and the underlying base. Runway wear and condition are closely inspected on a regular basis at Frankfurt Airport, as at all key facilities around the world, to ensure safety.
To maximise flight safety, the surface of a heavily stressed runway has to be maintained regularly. And at Frankfurt, this most recent project included the renewal of the northern section of the runway, a stretch of 1.4km in length by 31m wide. However due to the airport’s busy flight schedule, this work had to be carried out in only five days.
A key factor in the project being carried out to the tight specifications required, as well as within the strict schedule, was the use of the latest Topcon 3D technology and the SmoothRide system. The planners at the airport keep abreast of developments in construction technology and were keen to utilise the latest machine control systems so as to deliver the quality needed. Employing this sophisticated package ensured that the runway surface could be milled, paved and then compacted to high quality standards, with a homogenous mat and without undulations.
However to achieve this result, the Topcon team faced several challenges on what was a highly ambitious project and had to deliver several special requirements to meet the needs of the client. As the planning stage had already begun, Topcon got in touch with Fraport, the project owner, the airlines, the respective authorities, and the German Flight Security (DFS). Because the project had a tight schedule with only five days and six nights to complete the work, the resurfacing had to be carried out continuously and without any downtime or halts in operations.
From the start it was clear that milling of the runway could only be carried out at night due to the high volume of air traffic during the day. A further complication came from the fact that a runway is one of the areas at an airport with the highest level of security. This posed an additional logistical challenge as every single truck as well as every member of the construction team had to pass through comprehensive security checks each time they wanted to enter the construction site. All in all, a team of over 100 people worked in multiple shifts to turn this runway renewal into a success.
Axel Konrad, the Fraport project manager, explained that the project was planned well in advance. The Fraport team first approached Topcon during bauma 2016, a year before the work was planned to be carried out. Konrad said that regular meetings maintained the good communications between the Fraport personnel and the Topcon team, with both parties highly aware of the crucial roles played by expertise and skill for the project.
Konrad said, “For this renewal of the wear layer, we were looking for the highest quality and the most modern method. Thus, we chose Topcon and the SmoothRide system." And he added, "With regard to our high security requirements, this is absolutely essential to such a project.
However before the construction activities could commence, the runway stretch had to be surveyed with a high degree of precision. For this task Fraport was keen to utilise the SmoothRide system from Topcon. This package features a single scanner mounted to a vehicle and the system was able to scan the existing runway to the necessary accuracy. Karsten Dietrich, project leader, said, “The assignment was to provide a concise, accurate data model of the runway.”
He explained that this was crucial to collate the vast quantity of point cloud data required, so as to allow an accurate digital model of the working area to be generated. This precise data file could then be used to provide the basis for a program for the machine control of the milling machines.
Dietrich said that the milling task had to be carried out without using any optical instruments. He continued, “That was the only way to ensure that six milling machines were able to work simultaneously and exactly. With traditional machine control, this project would have been impossible.”
Dietrich said that this sophisticated set-up delivered the precise data required, “Only with our work process, including the RD-M1 scanner, the planning software MAGNET Office Site Resurfacing, and the RDMC machine control, a project such as this one can be completed. It took us about three hours to drive over the entire area of approximately 45,000m2 with our scanner. As a result, we had a highly precise, homogenous point cloud of the existing runway in a 20mm resolution.”
A key characteristic of the Topcon SmoothRide technology is the capability it offers for providing the milling machines with information collected during the scanning process and in the generation of the 3D model. Based on the surface of the runway and relying on the recovered data, the milling machines are able to deliver variable depth operation. This is an important factor as it means the planers only mill off as much material as is actually necessary. This ensures that an even and smooth surface can be obtained using a single pass to allow for the subsequent asphalt paving operation. For the milling operation it improves efficiency considerably by minimising the time needed for the planing operation, as well as reducing wear and tear on the milling machines themselves.
And by ensuring the surface was milled to precise standards, this helped optimise the subsequent asphalt paving operation, reducing the quantities of asphalt required and helping deliver a smoother and higher quality surface overall. Given the cost of the high-quality wearing course material in particular, this helped reduce the cost of the project overall.
Raimo Vollstädt, who is responsible for model planning and the machine set-up at Topcon, described the special situation, "This was quite different to usual road re-construction. The runway is 45m wide and was resurfaced in the middle to a width of 31m. Consequently, it was absolutely essential that the new surface could be bonded to the underlying structure without any irregularities or uneven patches.”
He explained that using scanning equipment prior to the milling operation identified issues that needed special attention and said, “During the scanning process, we observed that the current runway was rather wavy and uneven along its length. The project owner had rigorous demands concerning the longitudinal grade and transverse slope, which had to be achieved. The lane evenness and surface quality was the most important aspect for Fraport.”
Konrad recalled the first on-site inspection, "At first glance, the patch that had to be rebuilt looked like a straight lane, rather uncomplicated. However, taking a closer look, the long ground waves at the runway became visible – and they had to be evened out. For example, if an A340 prepares for take-off, the waves can generate undesirable resonances in the aircraft. As a result, the project was extremely important for safety reasons as well.”
The project team utilised the MAGNET Collage software to complete the data processing of the information that had been obtained by the scanner. This tool was able to process the point cloud data from the scanner. Afterwards, the data was transferred to the MAGNET Office Resurfacing program, which could then be used for the actual planning operation. Clearly, the efficient data transfer between scanner, software and milling machine was crucial for the operation to meet the strict parameters set by the client.
For this specific surface renewal, Topcon created several varieties. Vollstädt and Thomas Reeh, planner at Fraport, jointly completed the final draft. For this project, all data was transferred between the various devices using USB sticks. However if the Topcon construction site management system Sitelink3D is used, the data transfer can also be carried out online, directly from the planning software MAGNET to the machines.
However he said that the SmoothRide system proved to be an ideal solution and continued, “The biggest challenge, if we leave aside the immensely tight schedule, was connecting the new patch to the surrounding surface. Together with our partners, we proved that we were able to let the milling machines work exactly as desired by our customer, especially with regard to international standards for longitudinal grade and transverse slope on runways.”
After the contractor Strabag had been entrusted with the construction job and the preparation work had been completed, the milling machines were ready to get underway. The 3D-controlled machines were used to remove the entire asphalt surface, including the binder layer.
The new surface layers were then quickly paved and compacted. All of this work, which required a high volume of machine and vehicle traffic at the construction site, had to be shifted to the night hours. In this way, it was possible to optimise logistics and avoid material shipments to the site being delayed by rush-hour traffic in the mornings and evenings.
The contractor used six automatically controlled milling machines, which were able to remove exactly the right quantity of material at every point along the runway section using to the comprehensive data files provided. This allowed the contractor to make huge savings in material costs, as well as delivering time savings with regard to the surface removal. By minimising the surface removal process, the contractor was able to speed the asphalt paving and compaction operation.
During the milling operation, the survey team continuously monitored the freshly milled surface. In addition to other surveying tools, a Topcon GT total station was used. The six 3D-controlled large milling machines removed a total of 140mm asphalt surface and binder layer, which weighed a total of 16,000tonnes in all.
Once the milling machines had completed their work, the next step was to bring in sweeping machines, which cleaned the freshly milled surface intensively. Afterwards, bonding layer was added to provide join for the new asphalt layer.
A binder layer of asphalt measuring 110mm thick was paved and compacted over the surface. Finally, a 50mm asphalt layer of highway quality wearing course material was paved and compacted on top to complete the runway renewal operation. And as soon as the surface had cooled sufficiently, the new runway markings were applied, and the LED navigation lights were reinstalled.
Regarding the completion of the measures, Konrad was very satisfied, “The milled surface looked excellent. We did several resurveys at multiple points and were delighted to observe that the completed works complied exactly with all our requirements. And we already received positive feedback from pilots and airlines for this excellent job.”
Using the latest technology, the surface of one of the most important runways at the busy Frankfurt Airport was renewed successfully. This work was carried out professionally, with variable milling depth, within the set time frame, and without affecting passenger or freight transport.