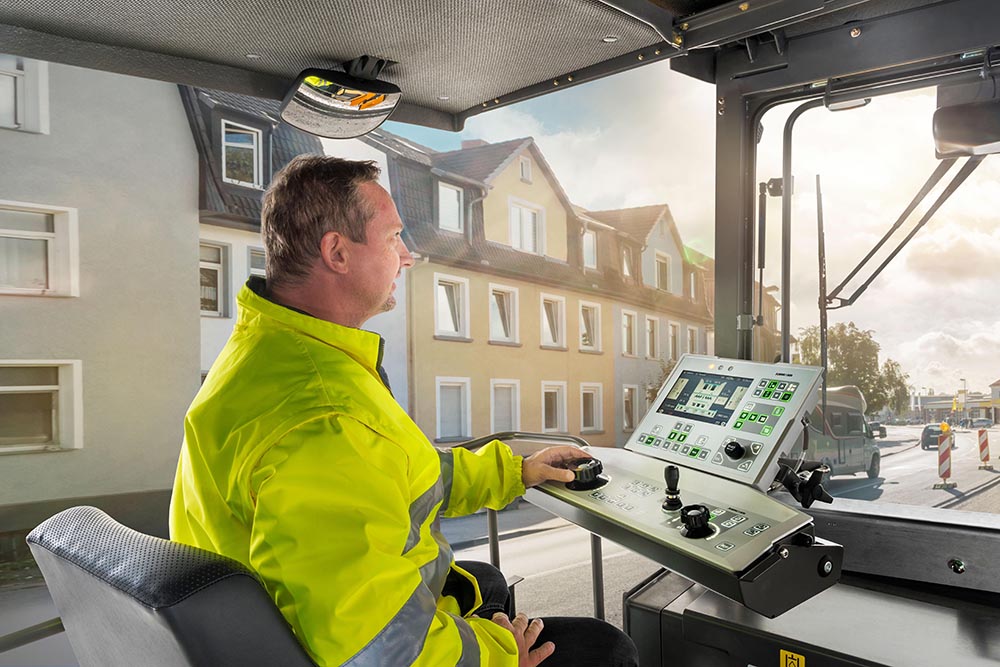
“ABG is a strong brand that we’re proud to welcome to Ammann,” said Hans-Christian Schneider, CEO of Ammann Group. “We will continue to build on ABG’s exceptional product line and reputation and provide complete roadbuilding solutions for the industry.”
The transaction includes the transfer of Volvo CE’s paving businesses in Linyi (China) and Bangalore (India) as well as Volvo CE´s ABG facility in Hameln (Germany). ABG pavers and screeds will continue to be produced at the facility in Hameln. Ammann production facilities in Mehsana, India and Suzhou, China, will also be a source in the near future.
Ammann will leverage its industry knowledge and customer relationships to guide the development of the pavers, with ABG in Hameln (Germany) becoming the Center of Excellence for paving operations within the Group.
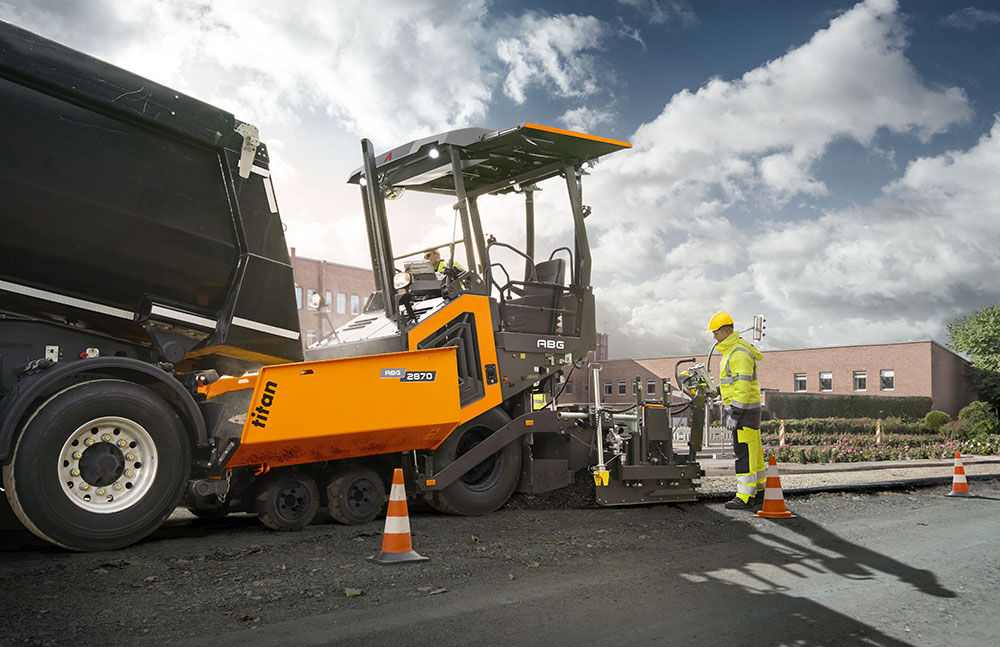
Initially established as a construction equipment repair shop in 1945, ABG in Hameln has evolved into one of the most recognized paving brands globally. Demonstrating its ongoing innovation, ABG recently introduced a new electric paver at INTERMAT 2024 in Paris.
Ammann will retain the respected ABG name. “The ABG brand is synonymous with quality in the industry and aligns perfectly with Ammann’s history in asphalt compaction,” said Bernd Holz, Executive Vice President Division Roads at Ammann.
--
Smoother Mats, Hundreds of Hours of “Found” Production
The Benefits that Drive the New Ammann ABG Paver Line
Ammann has strengthened its roadbuilding product offerings with the purchase of the ABG paver line from Volvo CE, effective 1 June. What does the acquisition mean to Ammann customers? What value will the newly branded Ammann ABG Pavers bring to the marketplace?
Bernd Holz, Executive Vice President of Ammann’s new Roads Division, provided some answers.
Have you already implemented any changes in the paver line?
The pre-fabrication and the assembly-line for pavers is state-of-the art and designed to the newest lean-manufacturing design. The previous owner, Volvo, made many investments. Ammann will continue with the current design and make some fine-tuning where needed. There is no need at the moment for tremendous changes.
Why did Ammann acquire the ABG Paver line?
It gives us a chance to bolster our roadbuilding products with what we most certainly consider the leading paver brand. Ammann offers plants, pavers and compactors that provide exceptional value during every phase of the asphalt paving process.
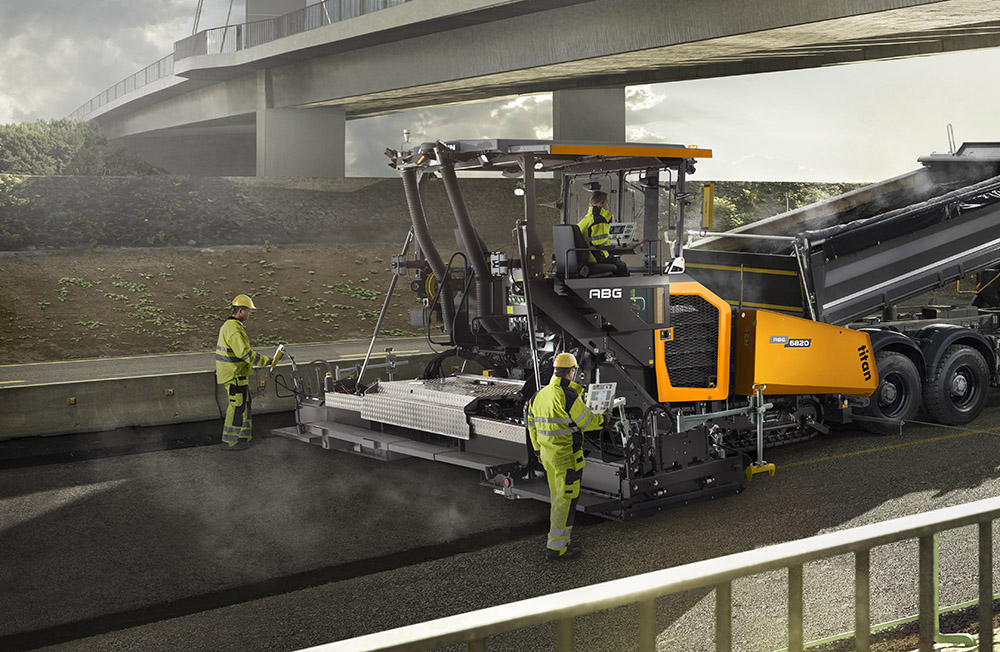
Why did Ammann target ABG pavers?
ABG is a strong, well-established brand with a long history. It started as a construction equipment shop in 1945, and evolved into the global brand it is today. By the way, we see strong similarities to Ammann, which started as a one-man shop more than 150 years ago.
The paving product line is comprehensive. The basic paving widths vary from 1.5 metres to 13 metres. That was important; we wanted to make sure we could meet the needs of virtually all customers.
So we have pavers that are wheeled and tracked, and big and small – and everything in between.
What would I notice about the pavers if I visited a jobsite?
You would likely notice machines are quieter and the mats they produce are smoother. Ammann ABG pavers operate at lower volumes – only 105 decibels. Operators tell us less noise on the jobsite makes a big difference. The screed was designed to be quieter, but at the same time able to achieve much more pre-compaction. In fact, double tamper screeds achieve up to 98% compaction. Communication is easier, which improves safety. There is a health factor as well.
You’ll also notice the jobsites are very quiet before the shift starts thanks to the e+ screed heating system.
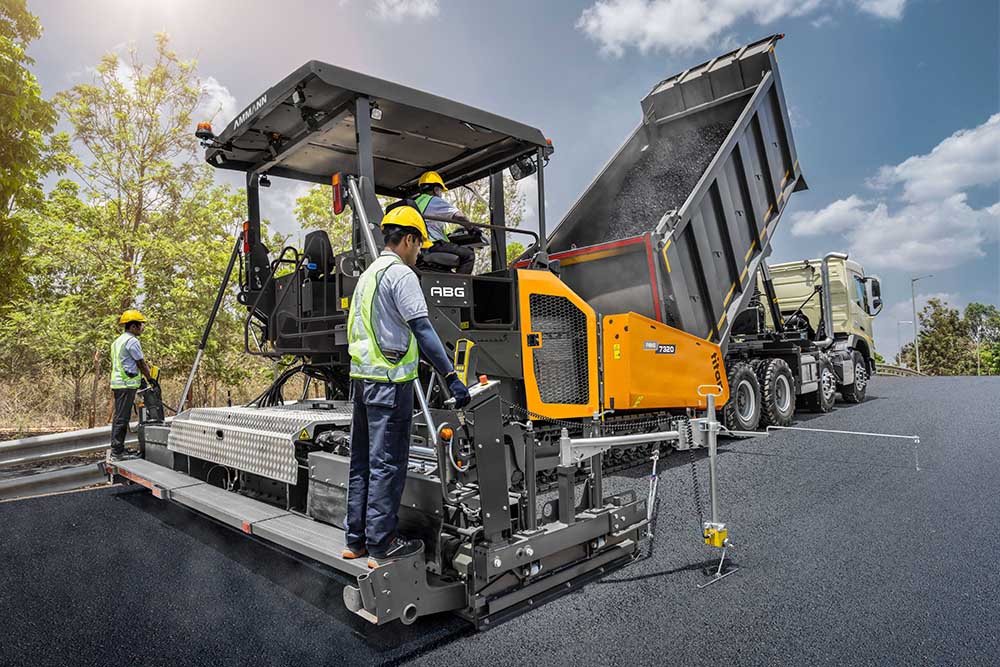
Can you explain the screed heating system?
The e+ screed heating system does not require a running engine to generate electric power. Instead, the paver can be charged directly from the grid – usually from a power pack brought to the jobsite. That means the screed can be heated during mandated quiet times. The crew start working the minute work is allowed.
It takes about 30 minutes to heat a screed, thanks to two heating bares per screed plate and a direct heating bar in the tamper bar. Multiply that 30 minutes of “found” work time across hundreds of days a year, and the production gains are enormous.
I should point out that the e+ screed heating system also lowers CO2 emissions, which fits into Ammann’s goal of making roadbuilding greener every day.

What makes the mats so smooth?
Much of it can be attributed to the ABG screeds. They have consistently set the bar in the industry. In fact, ABG provided the first hydraulically adjustable, high-compaction screed on the global market.
There are now many Ammann ABG screed choices ... fixed or Variomatic, single or double tamper. The double-tamper technology delivers a 5% to 7% higher degree of compaction than some competitive products and can achieve up to 98% Marshall density.
Fixed screeds are suitable for various materials, including asphalt, roller-compacted concrete, graded mineral mixes and railway ballast. Variomatic screeds are adaptable to different project types, from cold mixes to hot mixes and special profiles. The fact that these screeds are built for specific materials makes them even more effective.
There are also features such as optional hydraulically controlled endgates and a unique advanced quick-coupling system for easy extensions, only available on ABG screeds.
Beyond the screeds, how do Ammann ABG Pavers differentiate themselves?
One way is with Electronic Paver Management, known as EPM3, which is renowned for its operator-friendly controls. It has features that make a real difference – including an intuitive display that guides operators through individual functions. It is especially helpful when working at night. Adjustments can be made quickly, too.
All Ammann ABG Pavers are recognised for their advanced technology, ease of operation, reliability and quality. They are designed to minimise fuel consumption, reduce emissions – and operate quietly, as discussed earlier.
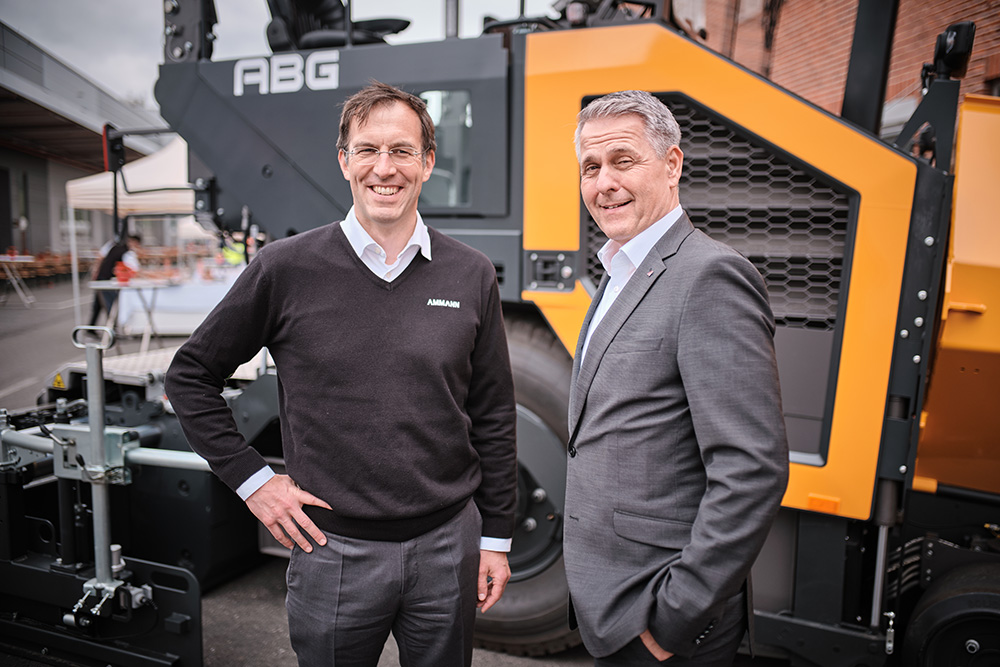
What kind of paver innovations can we expect in the future?
A recently introduced electric-drive paver reduces CO2 emissions on the jobsite by about 70%. It’s an important step toward the zero emissions paving initiatives we are seeing across the world.
Ammann has unveiled its sustainability action plan, “A Green Path Forward.” We are very committed to being a part of that – including but not limited to e-drive machines.
As for what’s coming up ... We will continue to invest in product development. We made this acquisition to add even more value to the line of pavers. We want to make what is already great even better. That is our commitment.
Content produced in association with Ammann