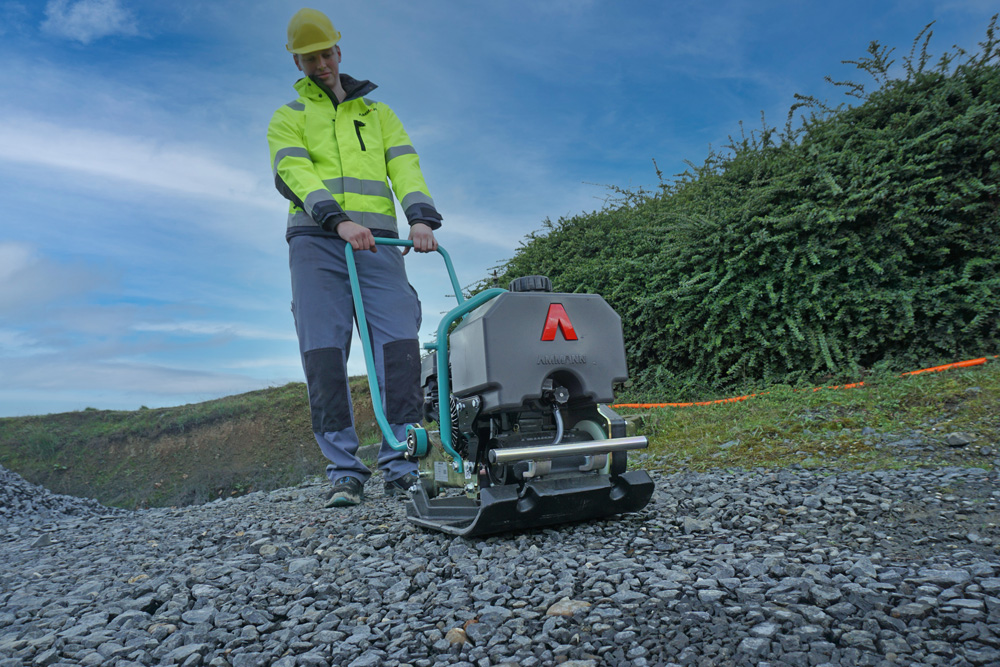
“For our customers, it’s all about compaction power,” said Bernd Holz, Executive Vice President of Machines at Ammann. “That’s what contractors care about the most.”
Ammann has an expansive range of light compaction equipment to meet virtually all jobsite needs. The product line includes Ammann APH Hydrostatic Vibratory Plate Compactors, which are known for their power.
“These are big, strong machines that handle the toughest compaction tasks,” Holz said. In some cases, they offer as much compaction force as a ride-on roller.
Holz recently discussed that compaction force and other ways Ammann APH machines separate themselves from the competition, including steering, maintenance and – one that might surprise you – lashing.
Let’s say a contractor or rental house is considering purchasing a hydrostatic plate compactor. What’s a good place to start?
Many contractors believe the most successful approach is to look at working width, total weight of the plate and – the biggest one – compaction force.
Working width gives an idea of the machine’s production and how much ground it can cover. It also indicates whether it will fit into some of the tight spaces that can be found on jobsites.
A machine’s weight provides some information regarding productivity and ability; heavier machines compact more quickly and more deeply.
But compaction force is the most important factor. It’s the power that goes into the ground, and it tells the whole story.
At Ammann, we design our machines to have an ideal balance between weight, amplitude and frequency. That combination brings deep compaction that you simply can’t get with other machines. And, I must say, it’s hard to find a more important differentiator than compaction force.
In fact, some Ammann hydrostatic machines bring significantly more compaction force than a ride-on roller. The depths reached really matter, too. You just can’t get them with a lesser machine. It’s as simple as that.
You’ve referenced lashing points on hydrostatic plates as a differentiator. Don’t competitive machines offer them as well?
Some offer them, but seemingly as an afterthought. At Ammann, we spent a lot of time and effort ensuring these APH models can be safely and quickly secured for transport.
These are heavy machines, with somewhat challenging dimensions in terms of being balanced while tied down. The lashing loops are large and able to accommodate heavy tie-down materials, and their strategic placement ensures the machines remain secure.
Lashing is very important across the globe. Tragedy could result if the machines came loose. In many countries, law enforcement is on the lookout for drivers who violate heavy equipment transportation regulations – and the fines are heavy.
Lashing is a concept a lot of contractors probably don’t think about until they are loading a machine for the first time. And then they can become frustrated with the difficulties they have securing it. They may experience those frustrations for as long as they own that piece of equipment. It can be really aggravating.
With Ammann’s lashing system, the machines can be secured in a few minutes … and away you go. And that’s really important if you’re a rental house or larger contractor who is constantly moving machines.
Can you explain the steering advantages the Ammann APH Plates have over the competition?
Ammann APH plates utilise what is called Orbitrol steering. It’s a patented process that allows the machine to make lateral and even circular movements, instead of simply moving forward or backward.
The steering is important because it makes the machine easy to control from the first time an operator uses it. Remember, these are big, heavy machines – and they need to be that way to deliver the necessary compaction.
Controlling something that powerful would be difficult without that unique steering. Precise control is even more important when working near a curb or obstacle. The accuracy of the steering is a sight to behold for something of that size.
The APH can also move very slowly, enabling the operator to focus the power on a specific spot. That’s important in some tough-to-compact locations.
Does Ammann offer any Intelligent Compaction systems?
Yes, we have ACE, which stands for Ammann Compaction Expert. It’s a proprietary system that monitors compaction progress.
For our APH machines, we have ACEforce – an advanced system that is very intuitive. The operators need only monitor an LED display, which indicates if compaction has been achieved.
This is very important for inexperienced operators because it can be more difficult for them to determine if an area is properly compacted.
ACEforce provides this information, which makes an enormous impact on the jobsite. First, it ensures that compaction has in fact been reached. Many structural problems could result if the operator moved on prematurely – or costly rework might be required.
ACEforce also prevents over compaction, which is a very common result with inexperienced operators. With the ACE system, the operator knows when it’s time to move on. This has an impact on both productivity and quality, as over compaction can harm the surface.
In the end, it’s all about efficiency … only using as much time and fuel as is needed to reach compaction.
I should note … rental houses like this system because their customers often have inexperienced operators. Therefore, the contractors who rent machines like to have them equipped with ACEforce.
Let’s talk a bit more technology. How is Ammann addressing the trend toward increased digitalisation?
Digitalisation is another area where we believe we have an advantage over competitors.
We’ve just released an updated version of ServiceLink. It’s a digital data management tool that provides light equipment customers with the information they want the most: machine location, battery status and working hours. Gone are the days of arriving at a jobsite only to discover a compactor has a dead battery.
Data transfer is automatic thanks to new hardware. This is a big step … no operator action is required. The data is on hand when the owner wants it. Access to it is only a click away, on a phone in the field or at the office.
All those features – location, battery status, hours and automatic data transfer – are essential. That’s what customers have said they care about the most.
ServiceLink will also improve reliability and extend machine life because it encourages scheduled maintenance. It provides alerts when maintenance is needed, which tends to get people to take action. That can be really important for those with larger fleets.
Some contractors have begun to talk about maintenance being a determinant in choosing one machine over another. Is that really the case?
It is. Maintenance has an enormous impact on the cost of ownership, machine uptime and even sustainability. And Ammann has made enormous strides on the maintenance front.
First, whenever possible we eliminate the need for maintenance altogether. For example, the triple-shaft exciter system on our APH machines removes the need for a V belt and the maintenance that goes with it.
When maintenance on Ammann machines is required, we’ve extended the intervals so the service work doesn’t have to be undertaken as often. That’s a convenience, of course, but it also means much lower fluid volumes are utilised during the life of the machine.
Our product development teams are committed to reducing the required fluid levels. A lower volume means a reduction in the costs to replace and dispose of the fluids. It ultimately decreases the total cost of ownership.
One good example of these maintenance efforts are APF (Forward Plate) compactors with Briggs & Stratton Vanguard engines. They have oil with five times the life of oil used in other comparable engines. That is a specific instance of extending intervals and reducing replacement/disposal costs.
Maintenance can be tracked through the Ammann Service app and MyAmmann.com. Customers can also access service and maintenance videos that provide a great deal of help. The Ammann Service app can be downloaded from the App Store.
One last point … Ammann machines have always had exceptionally convenient access for service. The operator or technician can easily reach the service points, which makes the work much faster and prevents spills, too.
There have been several references to green, or sustainable, practices. Can you summarise Ammann’s commitment on that front in terms of the APH compactors?
So many of the earlier discussion points are ultimately about creating green products – and green jobsites. I’m talking about maintenance, digitalisation, ACEforce …
When customers ask about “green” features, they’re most commonly referring to engines. There certainly is a great deal of focus on that front. Major European cities require emission-free machines in their city centres. The government mandates it, so contractors must have that equipment if they want to land those jobs.
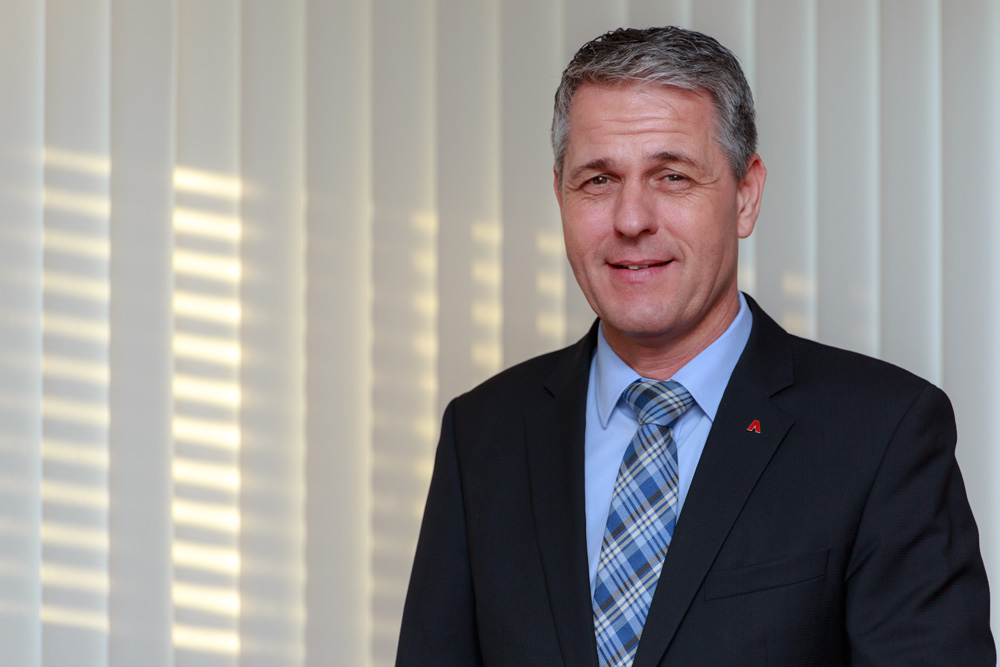
At the moment, “emission free” essentially means electric drive. More manufacturers are marketing these machines, and contractors and rental houses are looking for them.
Ammann has some offerings on that front, with additional announcements to come shortly. I can’t say any more than that at this time. I should also mention that reduced sound levels are a priority as well.
We discussed digitalisation earlier. It advances green jobsites on many fronts. For example, Ammann’s digital management tool, ServiceLink, encourages proper maintenance, which extends the life of the equipment. Stretching out the resources used to manufacture a machine has a host of sustainable implications.
Extending service intervals reduces the volume of fluids that must be used and disposed of, so there is yet another sustainable benefit.
ServiceLink also keeps managers apprised of battery charge. This prevents workers from burning fuel to drive long distances to a jobsite, only to arrive and find out the machine won’t start.
Really, when it comes down to it, any improvements in efficiency boost sustainability, too.
Sponsored content produced in association with Ammann