AECOM delivers climate change guidance
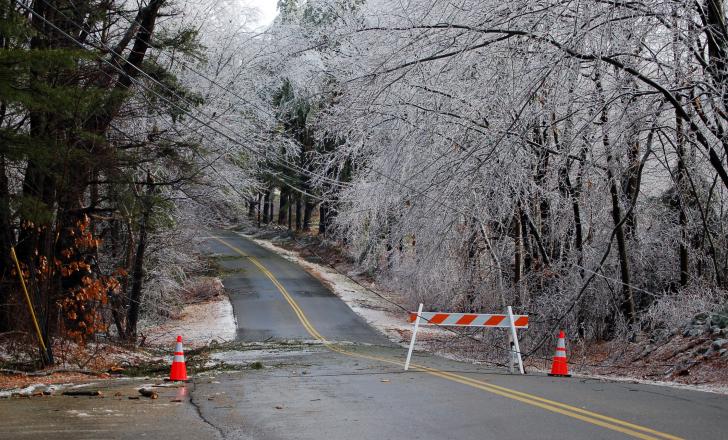
Zepp conversion for Liebherrs
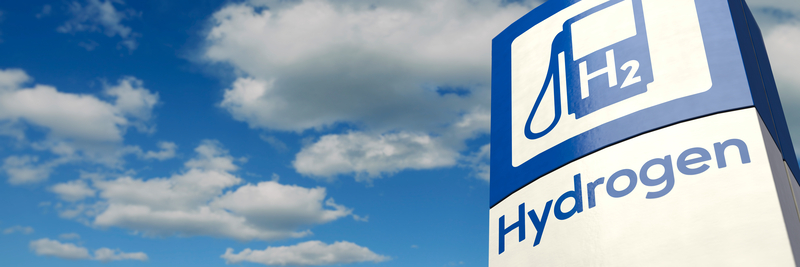
Emissions approach enables FPT to make F34 and F36 engines compact, powerful
At that time, FPT recognised SCR was the better emissions solution, although pursuing it would be expensive. “Developing engine emissions is not cheap,” said Braden Cammauf, brand vice president of North America for the company.
FPT stuck with SCR and now holds a number of patents on the technology. The company’s engines require only 7% EGR. “What happens with full EGR?” Cammauf asked. “You have a huge radiator.”
The F34 and the F36 Tier 4 Final/Stage V engines do not have that large radiator, and therefore are more much compact and light, Cammauf said.
The F34 powerpack stands out for low operating costs and extremely easy maintenance in a compact layout, the company said. This solution with mounted ATS allows for layout optimisation and plug-and-play installation. The Tier 4 Final compliant ATS, without DPF, minimizes engine downtime and operating costs with a 600-hour service interval.
Engine displacement of the F34 is 3.4 litres. Maximum power is 55 kW and torque is 318 Nm.
Cammauf describes FPT as the “biggest engine company no one has ever heard of.” In the past the engines were branded by other OEMs. The company is now branding them as FPT – an acronym for Fiat Powertrain Technologies.
Nearly 20 years after committing to SCR, FPT faces another decision: which engine power source to pursue? They are exploring hybrid, battery, biodiesel, methane, hydrogen fuel cells, combustible hydrogen, e-axles and e-transmissions.
Once again, FPT will not necessarily take the convenient, or even cheapest, path.
“We’re keeping our options open,” Cammauf said. “We have multiple viable answers and we’re going to invest in every one.”
Booth S83941
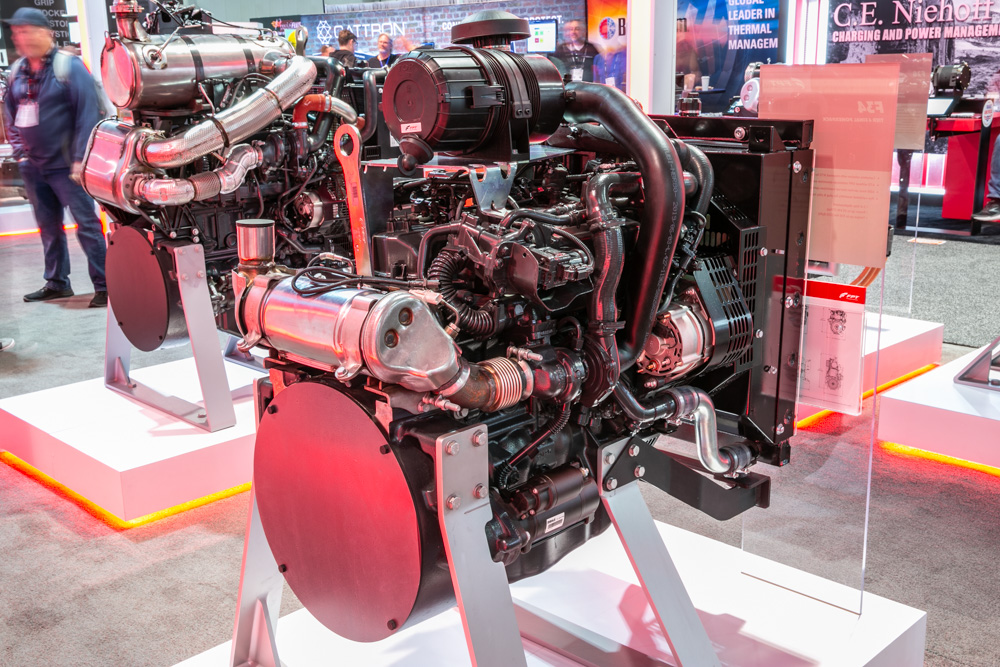
A new tunnel for Vietnam
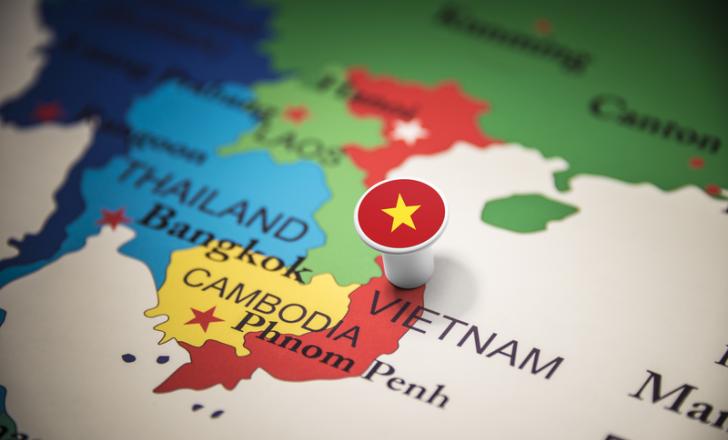
Push up profits with SBM’s JAWMAX 400 hybrid-electric crusher
The JAWMAX 400 is described by its designer as a “solid middle-class track-mounted mobile jaw crusher - easy to transport while offering great performance and output at the same time.” Ideal for the recycling market, the JAWMAX 400 dry jaw crusher features one of the most advanced hybrid diesel-electric drive concepts on the market. A combination of fuel-efficient onboard diesel and performance-tuned generator powers the plant’s materials processing.
The unit is part of the SBM mobile plant range which comprises 12 track-mounted JAWMAX jaw crushers and REMAX impact crushers, capable of 250–800tonnes/hour production.
All of the units in the range share the same innovative drive concept, with fewer hydraulics ensuring fewer failures, lower maintenance and parts inventory costs, and higher availability, says SBM.
Overall savings from running the plants can be 40-75%. Electrified, automated, and money-saving, the JAWMAX 400 is the perfect crushing machine says SBM. “Easy to handle and easy to operate, the crusher can make you more profit,” says Helmut Haider, head of sales for SBM Mineral Processing.
New SmartROC T25 R surface drill rig from Epiroc
The SmartROC T25 R is a radio-remote rig built on a new platform and offers features including an exceptional coverage area, excellent terrain ability and application versatility. These are backed up by a smart Rig Control System (RCS) and future-proof digital functions that are designed to improve efficiency and help to reduce the rig’s climate impact through fuel savings.
The machine will be launched initially on the Scandinavian market later this year, with a full global rollout in 2024.
Global product manager Marcus Leu said the rig offers greater stability and balance to increase safety. “These rigs operate on unprepared ground, and we have lowered the centre of gravity,” he added. “The SmartROC T25 R has new features including the ability to drill sideways which enables applications such as small tunnels and vertical shafts.
“The machine offers a coverage area of 45m2 which is three times greater than the 15m2 that we currently have.”
Another new feature is being able to choose between rubber and steel tracks on the machine.
Epiroc is also rolling out an upgraded version of the advanced SmartROC T40 tophammer rig for quarrying and construction. It is claimed to consume less diesel than any other diesel-hydraulic rig in its class and offers superior performance even under the toughest drilling conditions.
The manufacturer says the rig’s fuel efficiency reduces environmental impact and costs. It also comes with smart features and options that boost productivity, including enhanced automation which helps to increase both drilling consistency and output.
In addition Epiroc is introducing the new DTH 5 hammer, which it says represents a significant upgrade that gives more drilled meters per shift and the versatility needed to tackle any type of rock and task. The design offers 12 configurations and a 5% higher penetration rate compared to its predecessor and lasts approximately 10% longer. For the operator this translates into more productive and profitable workdays with fewer time-consuming and heavy changes of tools.
Booth 31348
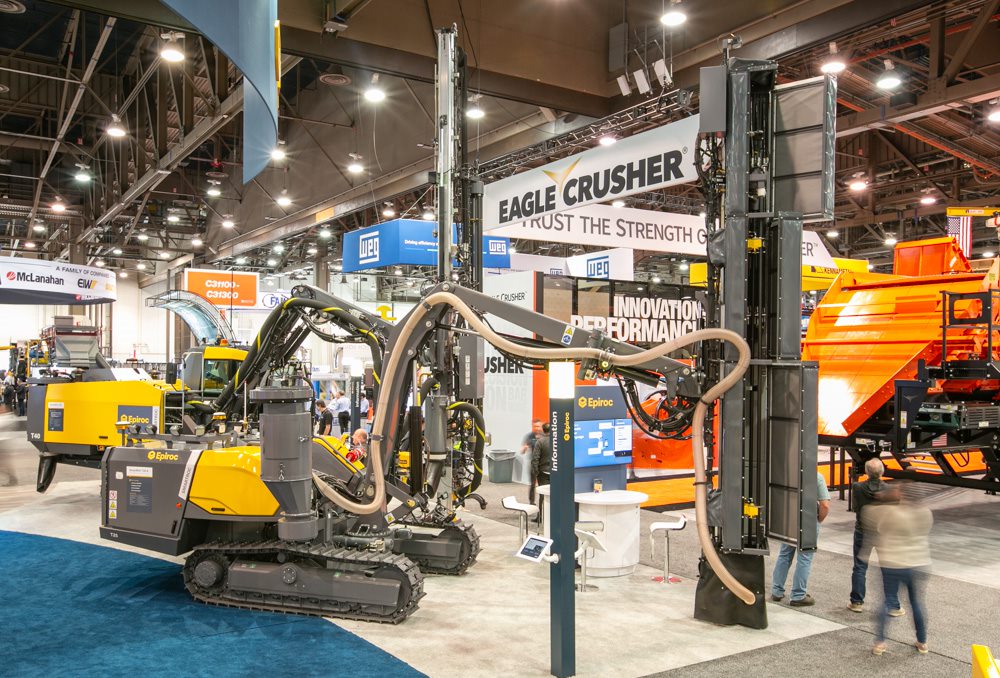
Svevia to renovate Sweden's Smögen Bridge
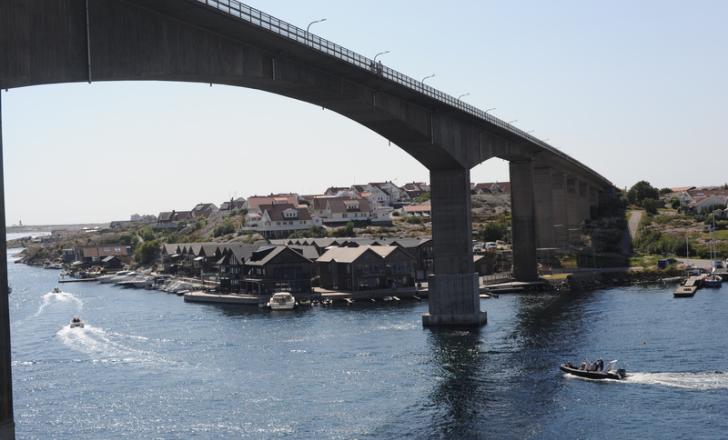
Green road solutions from Wirtgen
New digital solutions from the Wirtgen Group combine with smart technology and green systems to deliver sustainable road building methods for future needs...
Read more on our CONEXPO-CON/AGG 2023 Daily News website
Green road solutions from Wirtgen
New digital solutions from the Wirtgen Group combine with smart technology and green systems to deliver sustainable road building methods for future needs...
Cengiz wins Corridor VC contract in Bosnia

Bechtel-Enka win North Macedonia deal
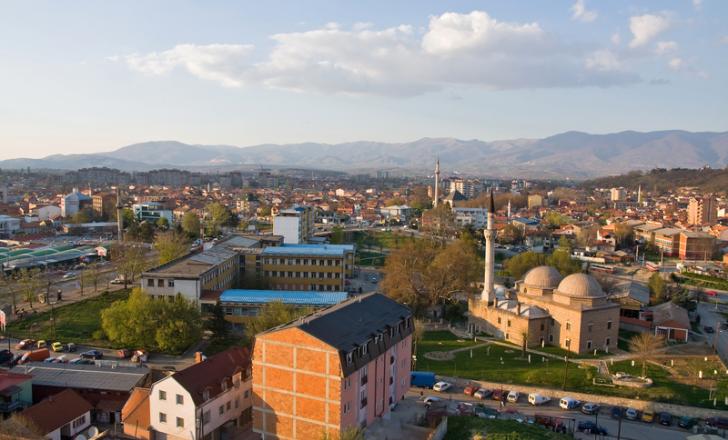
New Benninghoven plant in Norway
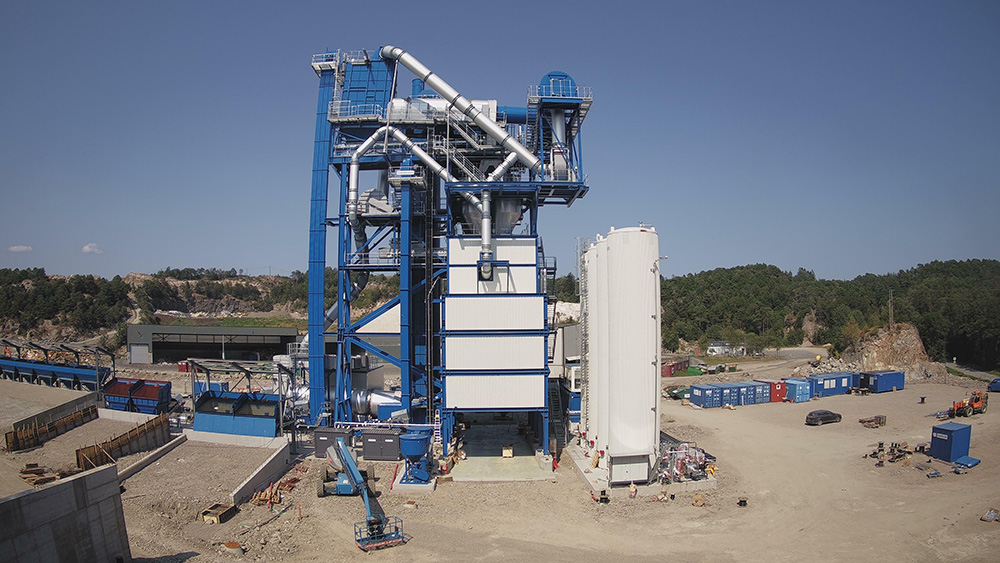
Italy's Messina Strait bridge

Ammann’s new road construction machines deliver versatility and productivity across an array of applications
A range of new road construction technologies are available from Ammann, as these videos show. Ammann’s ARS 30 Single Drum Roller features versatility and reliability – combined with low maintenance needs. The ARX 10.1 Tandem Roller can work in tight and tricky sites where space is limited, compacting next to walls and in confined spaces with ease. Ammann’s plate compactors are able to finish work faster due to optimum performance. The new ARR 1575 trench compactor delivers productivity and manoeuvrability. And ... mobility and high-quality output are key features of the new Ammann ACM Prime Asphalt-Mixing Plant.
Compact, versatile and productive, that’s Ammann’s ARS30 soil compactor
Here's our latest video on Ammann’s compact yet productive, ARS30 single drum roller. A tight turning circle ensures manoeuvrability while the machine offers high compaction forces for its size plus maximum stability for working on uneven sites. A number of key components are designed to last the life of the machine, while maintenance is eased due to good access for servicing.
Product Information Link
Keestrack eyes big sustainability-minded growth
Keestrack is targeting 30% growth a year over the next five years in its North American business. The Belgian sustainability-minded crushing and screening plant manufacturer had a strong presence at CONEXPO/CON-AGG 2023, showcasing its diesel-hydraulic, diesel-electric hybrid, and zero (no onboard engine) plant range. Displayed solutions included the B7H jaw crusher, a heavy-duty machine for mining and quarrying customers, the R3h mobile impact crusher, the H4 cone crusher, the R5e hybrid impact crusher, and the W4 dust suppression cannon. Keestrack’s first electric plant solution was launched in 2006, and the company has established an impressive reputation as a sustainability pioneer. Management sees mineral materials processing decarbonisation as one of its core goals.
Martin Engineering rolls out Canoe Liner conveyor belt impact absorber
The new product is installed inside conveyor belt transfer point skirtboards to absorb impact and abrasion, and to create a dam to shield the sealing system from the weight of the of the material load, prolonging the life of the seal.
Seth Mercer, marketing manager at Martin Engineering, said the main markets for the product are in aggregates and mining. “It is geared strongly towards aggregates – dealing with large diameter materials that are heavy and abrasive,” Mercer added.
“We have 19 business units worldwide. Cement is a huge business for us and any raw material extraction. We are seeing a lot of potential growth for our products in Africa. We have an office in South Africa and are expanding in the region.”
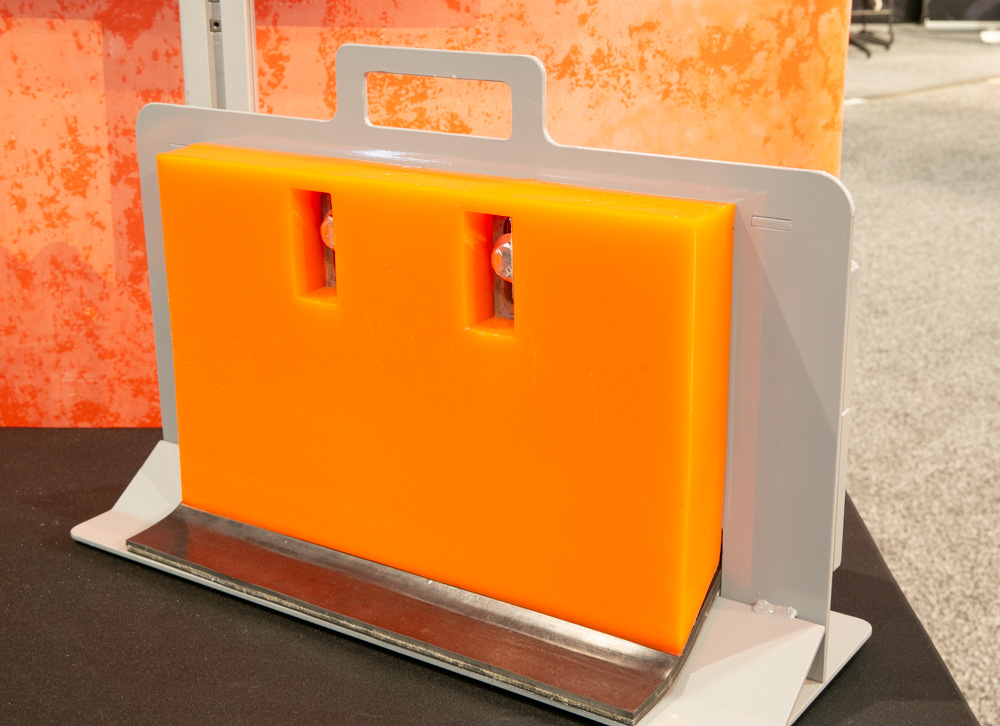
New Trimble autosteer function increases soil compaction efficiency
The report has been produced for Trimble by Michael Granruth and he said that the technology has highlighted a number of benefits. “A lot of products are focused on productivity. We created a study to manage the overlap in horizontal steering. Typically, there’s around 30% more overlap with manual steering.”
He continued, “What we saw was a 26% saving in fuel, in addition to production savings. If you’re doing the same work in less time, you’re achieving better efficiency.”
He said that for the tests, two operators were selected at random to compare the manual steering with the autosteer function and to gather the relevant data. However, Trimble says that since the study has been released, it has had feedback from customers that the estimate of 30% more overlap using manual steering is conservative and that it can actually reach 50% in many instances.
For the contractor, the package helps ensure an inexperienced operator can achieve the same working quality as someone with many operating hours. In addition, the system can help reduce running costs by lowering fuel consumption and issues such as tyre wear or general service needs for equipment. Trimble says that the system can even allow its clients to meet sustainability targets. Granruth said, “Technology like this autosteering solution is something contractors can use on existing fleets and achieve sustainability gains.”
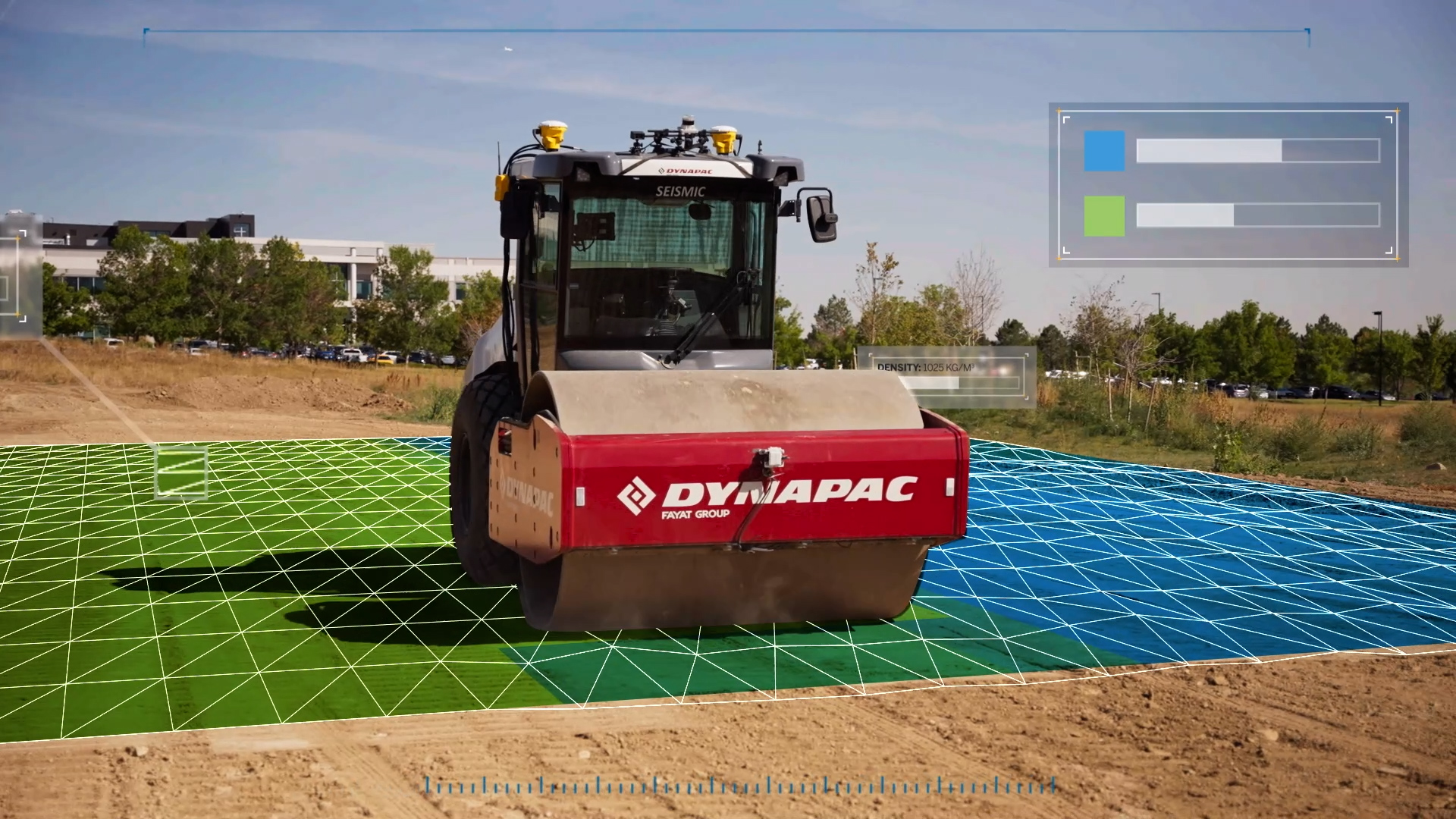