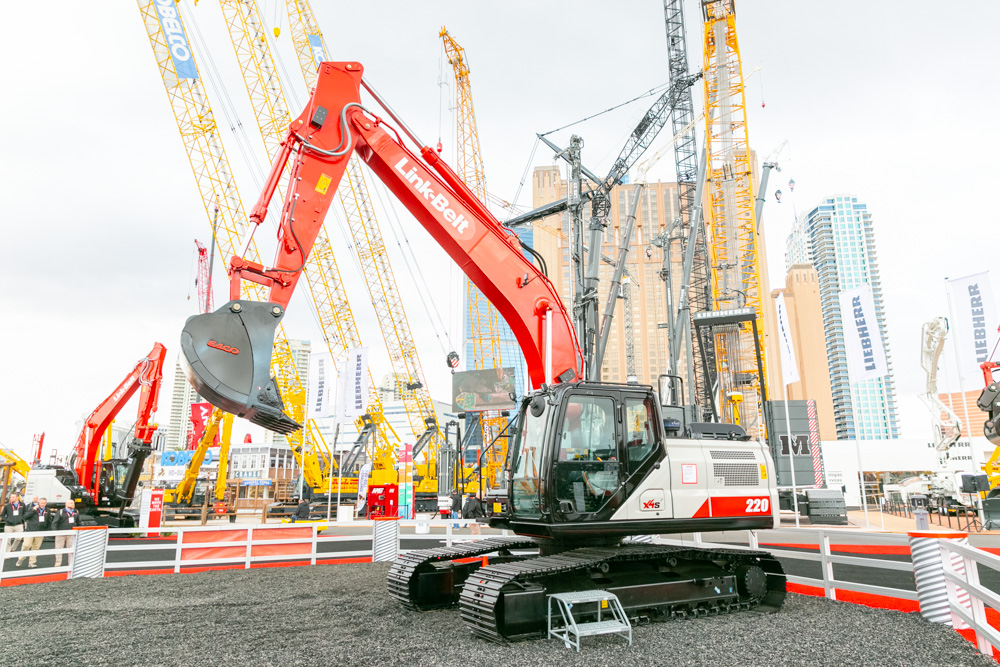
“With sustainability, we have targeted emissions reductions of 30% by 2030 – when compared to 2010,” said Adam Woods, general manager of innovation and product portfolio strategy at the company.
The reduction is just one step in Link-Belt’s commitment to utilising carbon neutral machines by 2050. “We are preparing for a world that will have no diesel engines” in 2050, Woods said.
The company is exploring a variety of fuel options, including hydrogen and conversion of waste materials. Electric machine models are already in Link-Belt’s product line-up.
The biggest challenge with alternative fuels might be ensuring consistent supplies, Woods said. “Everything is focused on the implementation of the goal, and not necessarily the support of it,” he said.
Autonomous machine operation is another process underway in the industry – and at Link-Belt.
A Link-Belt 220 X4S at the show demonstrated the company’s Precision Grade grade control system, technology that was developed with Trimble. Precision Grade accuracy is now +/- 2 cm, Woods said.
“That’s all leading up to machines that are fully autonomous,” said Chris Wise, marketing director at the company.
Woods certainly sees the need. “Autonomy fills a labour gap, improves efficiency and there is no learning curve,” he said.
Autonomous operation might be the long-term goal, but some nice gains are being realised along the way – just like with sustainability. “Precision Grade can take a new operator and make them somewhat proficient in a day,” Woods said. “It used to be months.”
An already proficient operator can become an expert with the help of Precision Grade, he said.
Booth F9241