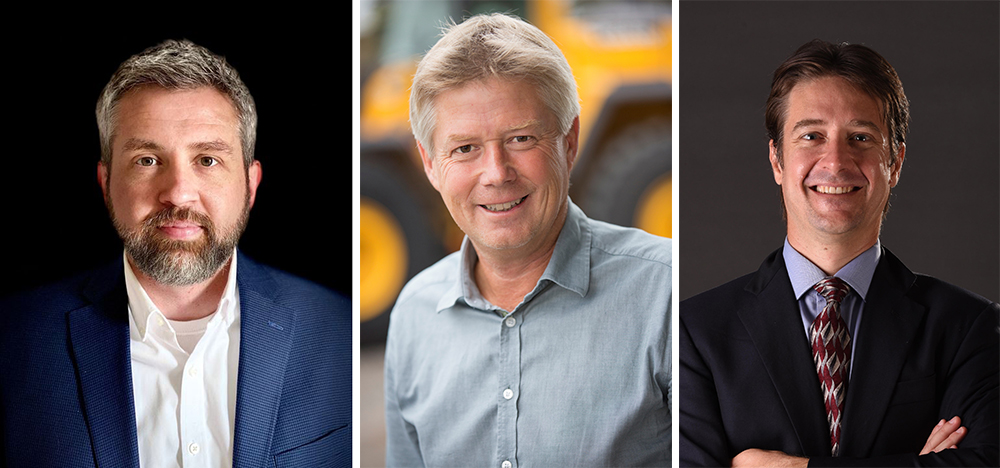
World Highways and Aggregates Business spoke with a trio of experts from leading construction and quarrying equipment and linked technology sector manufacturers to hear their takes on helping to address customers’ current and future sustainability needs.
Jeremy Harsin
Jeremy is responsible for segment strategy development & execution, digital connectivity leadership for construction, global OEM collaborations, and planning for the future. He describes himself as: “A dedicated off-highway professional who has been at Cummins 14 years, holding various positions in the Off-Highway business." His Cummins career path started in new product service engineering for Tier4 Interim followed by leading the customer care function for Tier4 Final.
Henrik Amann
Henrik is based at Eskilstuna in Sweden. He describes his role as: “Driving Volvo CE’s powertrain development regarding transmission, axles and electromobility.” In the last 25 years he has held different positions with the Volvo CE Technology and research and development departments. Previously he worked with a deeper focus on engines as the group’s director for Engines & Auxiliaries.
Dietmar Grimm
Dietmar is responsible for driving Trimble’s approach to strategic management and Key One Trimble initiatives. Dietmar says that this role “includes commercialising sustainability and carbon through the efficiency and productivity gains delivered by Trimble products across natural resources, construction, transportation and logistics, and related sectors.” Prior to Trimble, Dietmar worked at The Nature Conservancy organisation, responsible for creating distinct, country-specific conservation strategies and regional systems change approaches around the world.
Q: The classic definition of sustainability is: “Sustainability is about fulfilling the needs of current generations without compromising the needs of future generations.” Do you agree?
Jeremy: Most people probably would but it’s about how you get there. You’ve got to protect that future but also account for current needs. There is a cost to being green. There are technology limitations existing today. Those have to be balanced as we think this through. There are practical things we could easily do today. There’s a ton of opportunity just with fleet turn. A lot of equipment has been around for years but stuff released in the last decade or so is a lot more efficient and friendly from an environmental perspective.
Things like HVO [hydrotreated vegetable oil] fuels, for example, could easily be used today, where available. Definitely some scalability challenges there. Something I’ve been pushing for a while is idle management. There’s a lot of untapped potential there. We did a random test on a wheeled loader using a makeshift stop-start system. In its normal operation there was 30 to 45% idle time. In terms of wasted fuel and unnecessary emissions, 15 to 20% or so fuel economy was gained just by turning that on. Cummins’ role is about converting energy into power and having that solutions portfolio to suit customers, applications and use cases where different things make sense.
We want to make sure we’ve got that portfolio available at the right time to help customers. If some are ready today, that’s great. Others are thinking through what they need and looking for a thought partner. We position ourselves in that way about sustainability.
Henrik: Our main purpose is building the world we want to live in. It’s a great purpose – “Building the future for future generations in the right way”. It makes people think work is not just about a salary. It’s about doing something for the future.
Dietmar: I completely agree. We base our entire sustainability initiatives around that statement at Trimble. We see it as indistinct from Trimble as a company. It’s about driving the productivity and efficiency gains we want to see in society. As a technology company, we have this opportunity to focus on the immediate things we can do - driving productivity efficiency today and finding innovations for the future. We see it as transforming the way the world works towards a sustainable future. When you look at how society has evolved over the last few hundred years, in terms of our economy, it’s through technological innovation that we’ve been able to break free.
A couple of hundred years ago, when we had about a billion people, we thought we were going to run out of resources. We just passed eight billion people on the planet and technology has driven that. What we want to drive, through productivity and efficiency gains, is better business with improved productivity and profitability to create a strong, growing economy providing resources for a successful society with high wellbeing, improved wealth, health and education. That means using resources more efficiently so we can improve biodiversity and ecosystem outcomes too.
Q: Returning to Cummins, how does it see its role in achieving a more sustainable future for our industry?
Jeremy: Looking at that well-to-wheel emissions view, how do we make sure we’re thinking through that whole chain and offering products that our OEMs [original equipment manufacturers] and customers need? I think advanced diesel is still in the mix. There’s a long way to go there, a lot of opportunity. We’ll talk about some of the springboards we have into different fuel types for combustion engines.
We’ve talked battery, we’ve talked fuel source. We genuinely believe it’s not going to be one solution. We have to prepare for different solutions and help customers think about the right one for them. Sometimes it’s going to be cost driven, or infrastructure driven or environmentally driven based on how and where you’re operating and what you need. We try to be a good thought partner and are constantly looking at our product portfolio, and thinking how it’s going to apply to the markets we serve.
Henrik: We have had this environmental aspect as a core value for 50 years. Now we are signed up to the Science-based Target initiative (SBTi) to make sure we plan for and meet future needs.
Q: We must address the resources question. How much are your companies investing in sustainable solutions?
Jeremy: I don’t have a dollar amount. My generic answer would be ‘a lot’. We are investing in advanced diesel solutions. We expect more legislative hurdles in the next few years, depending on which market you’re talking about. We continue to invest in our diesel product line. You’ve probably seen things in the media around our field-agnostic strategy? We’re thinking about how to be greener in an affordable way. One of the big challenges is scalability. How do you find scale on some of those components when the market is only ready to adopt in niches in a lot of cases? We think fuel agnostic is a good solution. If nothing else, it’s a bridge product - and may even be a longer term one - being able to take a lot of those base components from a combustion engine running on diesel - and you also need to think about after-treatment.

When you go from a diesel to a natural gas or to a hydrogen combustion version of that, what you’re changing is the top end of the engine – its cylinder head, its field system parts. At the same time, you’ve got a decent amount of scale on a lot of those base components. While it doesn’t make it equivalent to diesel from a cost perspective, it helps because you’re sharing some of that scale. Since 2017, we’ve invested in acquisitions for different technologies. We acquired a battery company, then a company specialising in electric driveline. We’ve also invested in a hydrogen company for fuel cells, electrolysers. Recently, we have a joint venture with a company called NPROXX that produces hydrogen storage tanks.
We’re placing those investments for the long-term future. The good part is most of this stuff is complementary. You share components, and you think hydrogen engines versus fuel cells – it doesn’t matter what you put it in. Getting that hydrogen made, and to where it needs to be and stored – that’s something that can transfer independently if it’s an engine or a fuel cell. You could tell a similar story for a lot of those components. How do you invest? How do you find something that scales across technologies, across markets? Cummins has a decent paper trail for what it’s been doing in that space.
Q: Is Trimble able to match what Cummins is doing?
Dietmar: Absolutely. When you look at Trimble as a whole, and at our history, we’d say our entire company is invested in sustainability. Our technologies have always been about driving productivity and efficiency gains. Often, people hadn’t recognised that as being about sustainability because they say, “Hey, we just want to reduce fuel use”. But that is a core part of sustainability. A lot of our thinking about sustainable investments is reinforcing our product portfolio and how we view technology here. Our vision going forward is what we call our connect-and-scale approach. There’s no one solution or idea per se. Everyone needs to be all in on this.
Market forces will drive this. We want to make sure everyone’s driving carbon emissions down. Through our connect-and-scale approach we bring people together. We’re trying to connect the entire construction industry – to drive those productivity and efficiency gains down from an individual workflow on a construction site to how the whole thing works. When you look at construction overall, the first step is design, working with architects to make sure you’re designing with lower embodied carbon and lower long-term operational carbon. The second piece is optimising site management so you’re reducing site emissions and the amount of rework and waste onsite. You compare design to as-built, and make sure it’s going according to plan to avoid fixing it later.
Lastly, you have operators who ultimately own the asset. They manage that asset by pushing designers to make sure we’re designing for lower embodied carbon and lower operational carbon but they can also manage that asset longer term. So, you’re repairing it, thinking about replacement rates because the longer you use that asset, the lower long-term overall carbon emissions you have. We’ve been working with companies like Ecovia in Italy. They’re using a Wirtgen cold recycling system. When considering replacing something they say, “Hey, let’s reuse the material”.
They’re reusing asphalt as they’re replacing the road as part of the core materials in there. Our companies have been driving sustainability for a long time. Cummins has done a great job of improving power production with lower fuel use. That’s what we do at Trimble, too. It’s in our DNA. We need to work together more effectively, collaboratively as an industry.
Q: What is the response when involving other community members in this conversation? Is working together happening in practice?
Dietmar. I think so. We’re discovering that sectors want to talk about this, that we’re working together to understand solutions, driving policies towards a sustainable future. A big part of it, especially when it comes to carbon emissions as a sustainability component, is we have to get much better at measuring and sharing that information. Once you measure something you can manage it, and we can start to reduce it together.
That’s where the shift has been recently – measurability, sharing that information, looking at these things in terms of insets or accounting offsets. That’s the way you start to optimise for reducing the total amount of emissions. We are starting to work together. Is there a lot more to do? Absolutely.
Q: Henrik, you talk about getting better at sharing information. That’s about trust, isn’t it?
Henrik: It is about trust but it’s also about developing things with customers and partners. That’s what we’re doing now. We need to work together and look into how customers want to run this transformation because they are very eager for new equipment supporting future CO2-free targets.
Q: From Volvo’s perspective, how much is your company investing in sustainable solutions?
Henrik: I don’t want to go into figures but we are focusing on this now. We have committed to different targets, including the SBTi. For example, we have said that 35% of equipment in 2030 should be electric.
Q: You’ve mentioned diesel and electric. Is there anything not obvious being developed by any of your companies currently?
Jeremy: It depends on what ‘obvious’ is. We are again diesel heavy. That’s going to be the problem so we’ve got to continue to push battery. Everybody believes battery-electric will find its place. Where that line gets drawn on any given type of equipment is probably the biggest point. There are many things to consider. How much energy do you need on board to get the job done? It’s very different from past conversations, when you’re thinking value-power product.
In other markets we’re talking natural gas and different fuels but from an off-highway perspective, it’s diesel, battery-electric and then hydrogen, either in combustion-engine form or in fuel-cell form. There are also hybrid installations. We participate in a lot of those as a component supplier. There may be something more niche or specialised we’re unaware of but those are the ones dominating conversations.
Q: Equipment manufacturers have an increasing range of powertrain options available. How should equipment buyers best approach these options when making specification choices and how should buyers evaluate what will best impact future sustainability and optimal fleet utilisation?
Dietmar: I might defer to my colleagues to get their sense of how people choose specific powertrain options. We look at this as what can you do today versus what does the future look like in terms of real-time optimisation? We’re agnostic on what the powertrain options are. We want to ensure we’re driving those to be most productive and efficient in the relevant timeframe. So, irrespective of what it is - diesel, hydrogen or electric - you want to use the least amount of that resource moving forward. It’s an economic choice for each organisation and that part of the economic choice is reducing ultimate fuel use and probably not putting all your eggs in one basket.
No-one is saying, “Go battery-electric for everything”. What we’re seeing, across the spectrum, is it can be very site-specific. Certain locations work really well for battery and electric because power supply is nearby, the grid is nearby. Other places are more remote and so it’s looking at different ways to power that resource. There isn’t a clear winner yet in the short run.
Henrik: I agree but it depends on a lot of things like where in the world you are and on what type of machines you are running. For example, an excavator can be grid-connected. That’s not perhaps the thing for articulated haulers running long distance. Perhaps it depends on what you are doing with them, what segment you are in. Perhaps they already have a good electricity supply. If it’s a local construction it might be trickier. It depends on circumstances to decide the right solution for customers and different machine types.
Jeremy: Your original question asked how buyers should foresee or make a selection. I would say thoughtfully and carefully. Diesel as a fuel, as a power source, has been convenient for a long time. It’s spoiled us, probably, when you think how complicated some of the other things are. With the specced engine, based on repeat power demands - it’s pretty easy to package the fuel onboard to do a specific job. When you look at alternative technologies, you’ve got to be more thoughtful about what you need. There are a lot of trade-offs coming with that. Obviously, there are cost trade-offs, operational trade-offs, serviceability trade-offs, environmental trade-offs to consider. From an OEM perspective, a lot of the conversations are, “Okay, you’ve got an excavator, or a wheeled loader - how much run time do you need?”
Generically, the first answer is, “A full shift.” That can mean many things. Is it a full eight-hour shift, 10 hours or is it only four? That’s going to drive, from a battery perspective, a whole lot more power on board. Batteries are big and add weight. You have to consider the cost of charge times and everything else. From a hydrogen perspective, independent of which solution, the rundown comes down to how much can you package on board? Undoubtedly, the packaging is more difficult than it would be for diesel.
From an OE perspective, there’s a balance between cost and what you need. Do you need eight-hours’ worth of fuel or can you run for four hours and do a top-up over lunchtime? It forces you to think what you need versus what you’re accustomed to because it’s so different from what we’ve all experienced for the last 100 years or so.
Q: There are still huge challenges. How optimistic are you that solutions will be found?
Jeremy: Optimistic. The timing of the solutions for any given use case is where the conversation is. A lot of site-centric applications today are big enough to drive some financial sense into investing in charging infrastructure locally. A lot of those areas are probably going to adopt first and adopt faster. Where it’s more of a nomadic-type job, that’s obviously going to lag. It’s positive in that sense. From our perspective, many solutions are going to come from the hydrogen space.
We’re trying to build out solutions that work today and tomorrow. In a lot of places, we definitely think fuel cell is going to be the long-term answer. It may not be right just now. We’re curious and interested in hydrogen as a fuel because from an OEM perspective, people want to invest in a zero-emission or a low-emission solution but there is little volume to back it in the near term. It’s difficult to justify full-on electrifying a machine if I’m not sure it’s going to turn into a decent amount of volume pretty quickly.
From an OE perspective, you’ve got to package hydrogen but you can pull out a diesel engine, drop in the same engine platform, power the hydrogen, package the fuel, and it lets you ease into that. All the electrolyser and hydrogen generation stuff that we talked about - those storage tanks I mentioned before - all that stuff transfers from combustion engines into the fuel-cell space. We’ve got opportunity and optimism about how those products are going to ease us into this. Maybe ‘ease’ isn’t the right word but we can work our way into this in a rational, phased approach in a lot of applications.
Henrik: We are very optimistic. Technical solutions are improving all the time so we are going in the right direction for the environment. Different solutions will be good for different markets and different machines.
Dietmar: I’m extremely optimistic for a couple of reasons. One is because all of us have been driving sustainability for a long time because it was already incentivised within our economic system. We didn’t call it that but we’ve been driving fuel-use reduction since the beginning. The incentives are there. The current system was very tied to the idea of burning money. It was expensive and we wanted to reduce that. That’s how the system works. Now we’re integrating and optimising carbon emissions as another metric alongside costs to improve efficiencies.
We want to reduce carbon emissions. We’re better at thinking about how we account for that, how we put that into company financials. Trimble has also joined the SBTi which means we have a plan towards net-zero emissions, or Paris Accord goals by 2050, reducing our emissions and thinking about offsetting for the remainder of emissions in that period. Our companies take this seriously. Thousands of companies have now joined the SBTi. Incentives towards reducing carbon emissions are now tied into our economic system. We believe in our companies because we’re all technology innovators. Years ago, we thought we were going to run out of resources but the technological and the green revolution has proved all of that wrong. I am a big believer in technology.
We’re starting to quantify. We’re providing the data. A big thing for us is connecting the physical and digital worlds, getting the data available. If you put the data in people’s hands, they’re going to optimise it within our economic system. Hopefully, we can ramp up and scale faster. That’s the key thing. Long-term, I’m super optimistic. Are we going to have some challenges in the midterm? Maybe. Our goal is to help drive that.
Q: Apart from driveline choice and equipment type, there are other factors affecting contractors’ ability to deliver a more sustainable onsite performance. Can you suggest practical early steps operators can take to lock into those benefits. It’s about adoption, isn’t it?
Dietmar. Definitely. I encourage everyone to get the data. The data are going to help you make choices. What’s the biggest way you can reduce your emissions? Start accounting for the carbon within whatever you’re doing. There may be choices you haven’t thought about. The biggest opportunity might be around changing your cement mix. Cement’s one of the biggest global emitters. There are cost-effective technology innovations right now - just by changing from Portland clinker cement to new methods with different mixes can dramatically reduce your emissions onsite. That could be more important than other things you might think about.
It’s thinking about those things and then working with that full ecosystem: you want architects, contractors, and owner operators to think about this together because incentives need to be aligned throughout the system. If you think about it individually, you may not optimise for that long-term carbon reduction. Think about quantifying the information, sharing thought leadership. That’s a big thing. We’re producing thought-leadership material to get that information to our customers and partners. Part of our website, civilconstruction.trimble.com/sustainability, shares that information. The goal is to get it out there so we can partner in driving a sustainable future.
Q: There’s that word, ‘sharing’. Any thoughts?
Jeremy: Some of the operational stuff – fuel burn etc., has been out of sight, out of mind. Data availability and having that in front of people will highlight things people weren’t thinking about before.
Returning to an earlier idea, how do you bring older equipment back into the fold? Things like idle management. How do you convince people of the value of that? Considering the last three or four emission changes, you’re talking 5-8% fuel economy benefits in one, another 5% in the next, another 3% in the one after and more coming down the line.
If a fleet report shows me how much fuel I burn, it’s an easy step to say, “Okay, I can monetise the value of upgrades”. Similarly, with idle management, if you take that example where the operator was idle 30% of the time, the fuel burn is the obvious one. Carry it a step further, most maintenance happens on a schedule so if you are not idling 30% of your time, your 500-hour-old drain interval will last longer.
You’re also not racking up machine hours. It won’t show up as all that idle time and that affects your end-to-life or resale value. Seeing this data will help you monetise that. You can make good environmental improvements which can also be really good for your bottom line.
Henrik: As Trimble says, how do we optimise the work site and run machines optimally? That’s one thing we can do now. Driver education is something we have been doing for a long time. You can save a lot of fuel by educating the driver how to drive the machine efficiently. We have also started building machines with fossil-free steel for selected customers. It’s another way to protect the environment.
Q: To what extent can autonomous operation benefit the industry, not least because of the challenge of finding skilled operators? Are all machine and driveline types equally suited to autonomous operation?
Henrik: I don't think all applications are equally well-suited, but some are more suitable than others, absolutely. Different types of automation will absolutely support the operator. We offer solutions that are assisting the driver, such as the train memory and cruise control, which are rather low-level automation. On the higher end of automation, we have a system, called the TARA. It’s a complete autonomous haulage system designed for use in confined areas such as quarries and mines, consisting of a fleet of small fully automated electric haulers.
So different solutions are more or less suitable for automation, and the value of autonomous operation also depends on the different applications. 5G opens more opportunities or course. With 5G, it’s possible to tele-operate a machine from hundreds of kilometers away. This can add benefits for example in forestry, where operations often are carried out in remote locations, or in mining, making it safer by removing humans from potentially hazardous environments. So these are solutions for operators that we're also looking into.
Dietmar: Trimble’s very focused on this. There are major aspects of sustainability that we believe are important. One is safety. From a safety perspective, a lot of onsite injuries happen getting in and out of vehicles. It’s inevitable. These are big machines that are hard to get in and out of. Removing that, you’ll end up having less injury. But from a pure carbon standpoint, we think there’s tremendous opportunity. We did a study this year to prove how productivity and efficiency gains drive sustainability.
We compared an experienced operator to an inexperienced operator to an auto-steering compactor. We found a 15 to 30% efficiency improvement over those operators. That means a 15 to 30% carbon emission reduction, largely because using auto-steering you can reduce overlap. Using the compactor multiple times over a site, it gets more complicated for an operator to do that as effectively as an auto-steering and autonomous solution. We see tremendous opportunity through autonomy to drive sustainability.
Jeremy: Today, we are participating in diesel-powered autonomous applications. The question is, is one powertrain-type better suited than another? Probably. As portions of these machines start to electrify, it probably gives you more finite control over some operations. Obviously, automation and connectivity go hand in hand, at least from our perspective. The further removed a person is from the cab, the more interest we have in making sure that the asset is healthy.
Thinking operationally, construction-wise, some of the assist-type functionality was mentioned. Traditionally, if I needed to dig a two-foot-deep trench, I’ll bring in my excavator. I’ll take a couple of scoops of dirt out, get out of the cab, probably leave it running, measure it and say, ‘Nope, I’m 18 inches’. I get back in, and repeat that before I get it right. With solutions that Trimble and others are bringing in, you don’t have to get out, which means you are not wasting operator time. You don’t need a skilled operator. You can get those jobs done a lot quicker. I think it will take a combination of the different product types that our companies will bring to the market.
Q: Let’s consider new factors coming into play in the sustainability toolkit, for example, green hydrogen. How do you view this opportunity and how can buyers best deploy a more intelligent approach to the selection and operation of equipment fleets?
Dietmar: It’s still unclear exactly how that is going to play out on specific locations, specific sites. The biggest transition we’ll see is how all this energy is produced because there are different kinds of hydrogen, depending on how you define green hydrogen. Because of that uncertainty and the need to make careful choices depending on the job, the workflow and the site location, we’re thinking about how you optimise for any of those solutions.
We see it everywhere, customers getting smarter about understanding their carbon footprint and how they’re going to reduce it because the people they are building for are demanding it. Whether it’s federal agencies or whatever, they want people to report their carbon emissions and how they can reduce them, compared to other contractors. Things used to be quantified in terms of price but now carbon is part of that equation so that people can provide competitive bids for new projects.
A big trend coming, already adopted by other industries, is around carbon offsets and insets in the sector. How do we work as a whole construction site to think about a net-zero asset, whether that’s a building or a piece of infrastructure? You have to think from design-to-site operations to the long-term operation to be able to do that, to quantify it all and ask, ‘Is it net zero?’
You’ve quantified the carbon reductions you’re producing through the supply chain as an inset. Then you need to think about buying offsets down the road. Getting more sophisticated regarding how we think about carbon insets and offsets is an important part of the economic equation going forward, especially as more companies join the SBTi, and as we see more federal agencies worldwide making us think about a net-zero future.
Q: Jeremy, do you agree? A more sophisticated industry is required?
Jeremy: The green hydrogen economy, obviously, is something we’re interested in. It’s going to be a critical part of the future solution, especially in our markets. Some things are going to be more suited for hydrogen than some of the other alternatives. We’re uniquely positioned for that to take off in the future with some of our investments. So, hydrogen generation for electrolysis - we have invested in companies that have that capability. Fuel cells, combustion engines, how are you going to consume that? We’re very well positioned, very much interested in that taking off. Thinking about how that plays out in the field, it’s going to be the timing and how quickly some of these things come along.
Henrik: Hydrogen is interesting for the future. The problem is storing electricity. We have wind and solar but difficulty storing it. Hydrogen can also be used directly in combustions, as Cummins discussed earlier. That is a great opportunity and we can use fuel cells to get electricity. We can also think about having power containers in those places where you don’t have electricity but where you could use hydrogen to produce electricity. If you already have electrical machines onsite, that’s an opportunity. Green hydrogen is also an opportunity, for example, to produce fossil-free steel. Hydrogen can be used in different ways to be CO2-free in the future.
Q: Have you any final thoughts to share?
Henrik: We share a common view on how to make a better world and have a lifetime opportunity to do something good for future generations.
Jeremy: We have been talking about what we call our Destination Zero Point. We are marching towards a common goal but we shouldn’t get too fixated on the 2050 picture. Those incremental improvements probably stack up to a lot more than if we all waited for some lightbulb moment. It’s going to take time and probably play out a bit slower than we would like but it’s going in the right direction.
Dietmar: I agree 100%. Our companies are pushing for change and many of our customers and partners have been driving sustainability without realising it. We can take that position of strength and lead the world towards a more sustainable future.
With today’s technology, we can reduce emissions further. There may be new technologies we are uncertain about so let’s think carefully how we drive that portfolio towards an innovative future.