CIFA launches new K42E electric concrete pump
The K42E is equipped with a 30amp hour cell battery pack that powers two Rexroth electric motors. The first drives the hydraulic pump to move the boom and open the outriggers, while the second drives the pumping unit, in a closed circuit and at maximum capacity of 160m³/hour at 80bar.
The charging process is quick and easy, says the company, with the integrated battery charger compatible with the 220V system. The boom extends up to 42m and consists of five sections, with the last two made from carbon fibre.
“If the job requires higher performance than the batteries can provide, the new Energya pump can be connected directly to an electrical outlet on site,” explains Davide Cipolla, CIFA’s CEO. “The system will then cut out the batteries and power the electric motors directly from the power source. A 40m power cable is included.”
This, he adds, means that the pump continues to operate with the truck’s diesel engine switched off, thus eliminating emissions and noise. If there is no electrical supply on site, an emergency system allows end-users to connect the K42E to the truck’s power take-offs and use the engine to complete the work, then close the boom and outriggers.
“The aim is to eliminate CO2 and noise emissions throughout the supply chain, from transport to laying of the concrete, by expanding the possibilities of using high-performance vehicles in areas where noise pollution and CO2 emissions are prohibited,” adds Cipolla. “The special feature of the Energya K42E pump is that the battery allows it to always operate in full electric mode.”
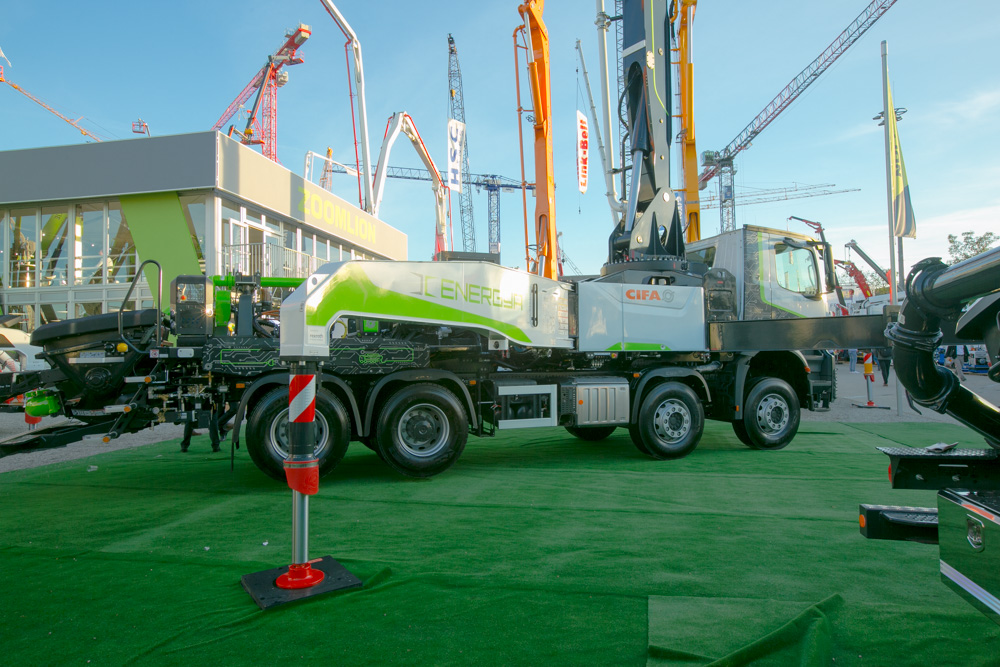