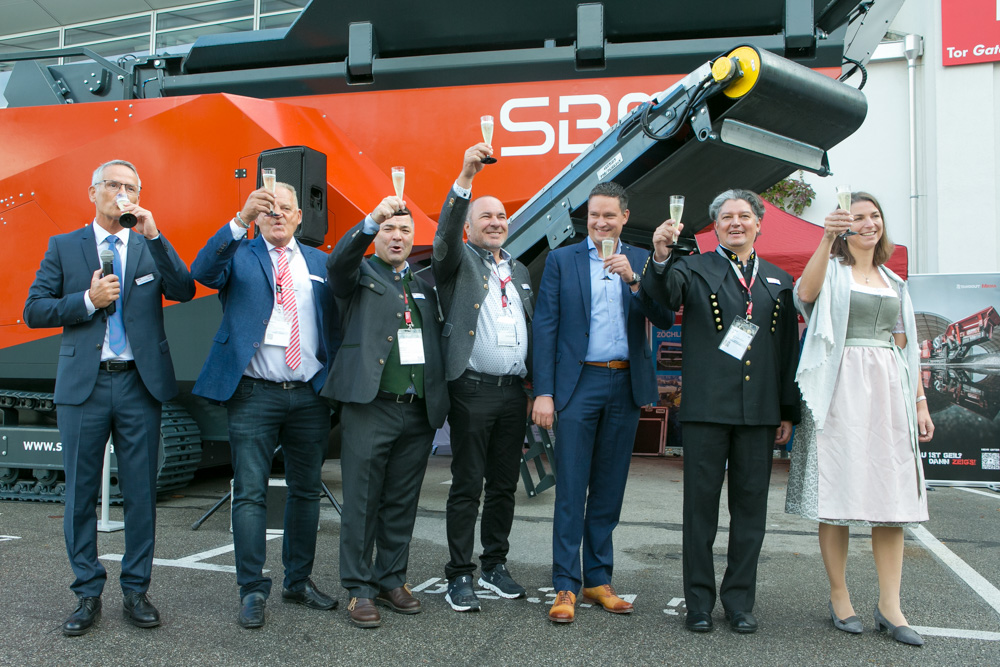
The technology is currently being developed by the company and researchers at Montanuniversität Leoben, Austria’s university for mining and metallurgy.
The REMAX 600 features a cutting-edge sensor system, video technology, powerful communication and IT networks. It will offer a set of technological innovations, such as an automatic gap adjustment facility.
It can offer up to five fractions in one cycle. With a feed capacity of 600t/h, the new machine can accommodate material feed sizes up to 900mm and a maximum total weight of 75 tonnes depending on the equipment.
Triple wind sifting and an ultra-efficient overbelt magnetic separator with longitudinal discharge as an option (a novel feature in highly mobile impact crushers) are said by SBM to ensure high purity of final products, even in recycling applications.
SBM stresses that the industry-first introduction of an 'autonomous crusher' will help users and operators with all decisions, permanently support efficient operation, assure optimum product quality at all times, as well as make an important contribution to save energy and costs during crushing.
The autonomous crushing R&D project has been running for two years and features interdisciplinary teams from the Montanuniversität Leoben chair of mineral processing and SBM research departments.
The project aims to make the decisive step from today’s already extensively monitored and optimised crushing operations to autonomous fully automated production by means of ‘intelligent self-learning’ mobile crushers.
The machine independently assesses feed material and final products via sensors and camera systems, registers better-than-before-the-load conditions of crusher and conveyor equipment, and optimises all separation processes down to overbelt magnetic separators and wind sifters.
The SBM control system, Crush Control, validates all operating conditions and material properties in real-time and sends the values to SBM’s headquarters via the cloud. A ‘digital twin’ compiled there matches the real machine data with thousands of stored reference data coming from 1:1 quality testing, laboratory tests and computer simulations (including rock properties, grain-size distribution curves, particle shapes, etc).
The optimisation potentials determined from this are sent back to the machine control system in real time. This allows immediate and permanent adaptation of all process steps on site without any stoppages, says SBM.
By means of an interactive menu control, SBM says even inexperienced operators can precisely adjust the production process – depending on whether maximum output, minimum fuel consumption (eco mode) or quantity-optimised production of certain valuable grain sizes are required.
The newly integrated tool monitoring system in the REMAX 600 is another benefit, one which counteracts shortfalls in quality due to wear during production and provides key support for preventive maintenance.
Large-scale test runs will take place in the coming year to make sure everything works as it should in practice.