Bauma opens today
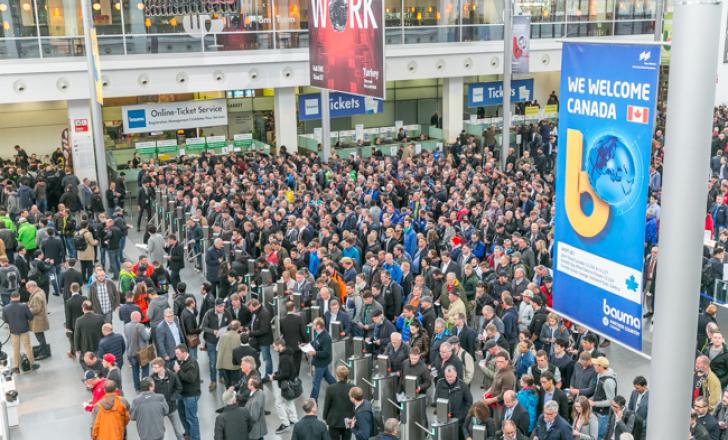
Caterpillar highlights prototype batteries for off-highway equipment
Leveraging expertise across the construction, quarrying and mining equipment giant’s global network of technical centres in the US, UK, China and India, the programme focuses initially on battery solutions for equipment used predominantly in industrial applications.
The battery range, currently in prototype form, uses lithium-ion technology and features a modular design to optimise performance and packaging.
They have also been engineered with sustainability in mind throughout their lifecycle, with the potential to reuse and recycle the units at the end of their life.
The development programme also encompasses inverters, motors, electronic controls, digital services, and other critical technologies to deliver the performance, reliability, durability, maintainability, and long-term value needed for equipment buyers working in harsh operating environments.
“Caterpillar has demonstrated a long-standing commitment to sustainability through improvements in our operations and by helping our customers achieve their climate-related goals,” said Steve Ferguson, senior vice president Caterpillar Industrial Power Systems.
“Our battery programme is our latest step in combining a wide-ranging inventory of innovations with extensive knowledge of the off-highway industry to offer solutions for a range of power needs, application types, duty cycles and operating environments.”
Caterpillar has committed that 100% of its new products through 2030 will be more sustainable than the previous generation, which is reflected in the company’s line-up of industrial-power solutions and integrated services finely tuned for owners of third-party equipment powered by Cat engines.
“Improved sustainability is a journey, not a destination, and one size doesn’t fit all in determining the appropriate power solution for equipment owners,” continued Ferguson.
“Our offerings can help customers and end users start improving the sustainability of their operations today through high-efficiency engines, fuels and digital solutions now available for the jobsite, by extending value and reducing waste over the lifecycle of equipment they already own, and by powering the next generation of equipment with innovations precisely configured for the jobsite.”
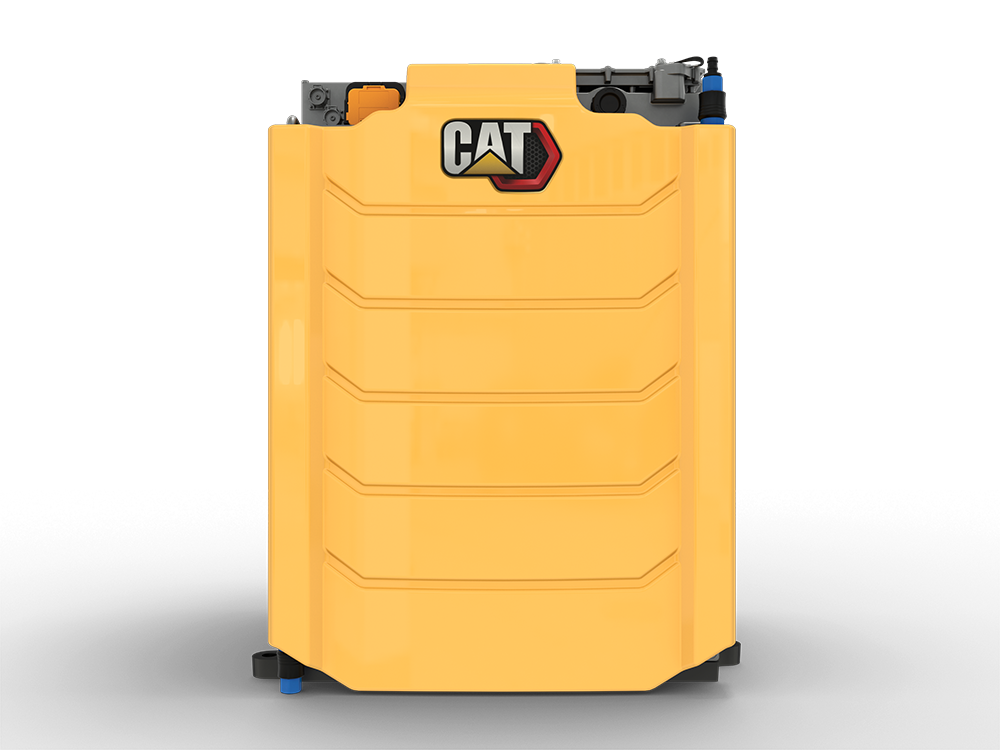
Liebherr’s new MDC3 smart camera for Sandvik roadheaders
Sandvik’s Mechanical Cutting Division located in Zeltweg, Austria, is among global market leaders in roadheaders and its powerful machines are often used for cavity construction on tunnel projects.
The cutting process in underground mining produces strong vibrations and huge quantities of dust. According to Uwe Restner, product manager for roadheaders and digitalisation at Sandvik: “The enormous forces at play in underground mining pose great challenges on the components in our machines. We, therefore, subject the components to intensive tests before we use them in our machines, and Liebherr’s MDC3 convinced us in particular due to its high quality and robustness.”
Sandvik has extensively tested the suitability of the MDC3 digital smart camera for underground mining. It has been put through demanding vibration tests and performed convincingly well under heavy shock loads without any failure or impairment.
Sandvik says that it wants its machines to be compatible with tele-remote operation in the future. This requires a high-resolution camera and, above all, reliable 360° viewing, even under heavy vibrations.
Due to the blind angle, failure of the camera would require immediate interruption of the tele-remote operation for safety reasons, and thus result in downtimes.
“The most decisive factors in the choice of the camera, besides its robustness, were its reliability and latency. The MDC3 has proven to reliably deliver images to our displays, with minimal delays,” added Restner. “This will be key to future tele-remote operations.”
In Bern, Switzerland, Marti Tunnel is using a Sandvik MT520 roadheader to dig new caverns for a railway station project. The machine has an operating weight of 115tonnes and a power output of 537kW. The MT520 is equipped with a unique telescopic arm, which enables cavity construction to a height of 7.1 metres and a width of 10.3 metres.
Six Liebherr cameras are installed on the MT520 for comfortable 360° viewing in the operator's cab: two in the front with a view of the telescopic boom, two on the sides and two more for rear-view monitoring. With its integrated high-performance imager, the MDC3 shows all the necessary information right on the display, even in very dark environments with an illuminance of 1 millilux.
One innovative solution devised by Sandvik illustrates the harsh environment during cutting: Dirt deposits from water and dust normally crystallise to form an opaque layer on the camera that clouds viewing. Sandvik’s underground specialist has therefore installed an air nozzle in front of the Liebherr camera to prevent the layer from building up.
Despite the challenging operating conditions, Sandvik says its high-quality machines are designed to stay operational for 20 years.
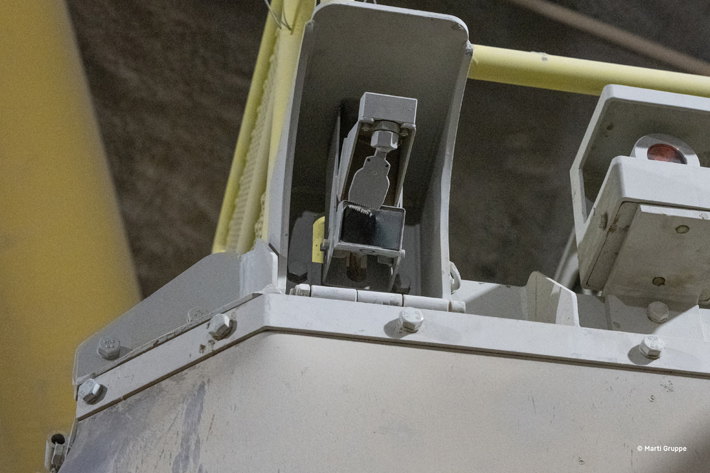
Malaysian 2023 infrastructure budget set
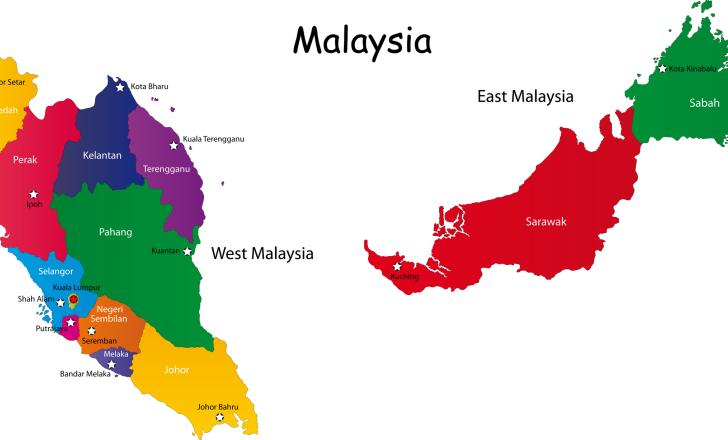
Liebherr wins innovation award at bauma 2022
The machine is powered by an internal combustion engine modified to run on hydrogen. This clean burning concept produces mostly water vapour from the tailpipe, ensuring low emissions. The CO2 emission profile of the machine from manufacturing to decommissioning are estimated to be around 70% lower than for a conventional machines.
The special H966 power unit was developed at the firm’s Liebherr Machines engine facility in Switzerland and is based on conventional technology adapted for the purpose. The port fuel injection (PFI) and direct injection (DI) systems are said to ensure efficient combustion. Series production of the Liebherr hydrogen-fuelled engines is scheduled to commence in 2025. The H966 engine features six cylinder and a four cylinder H964 unit is also in development. The machine has a 50tonne operating weight.
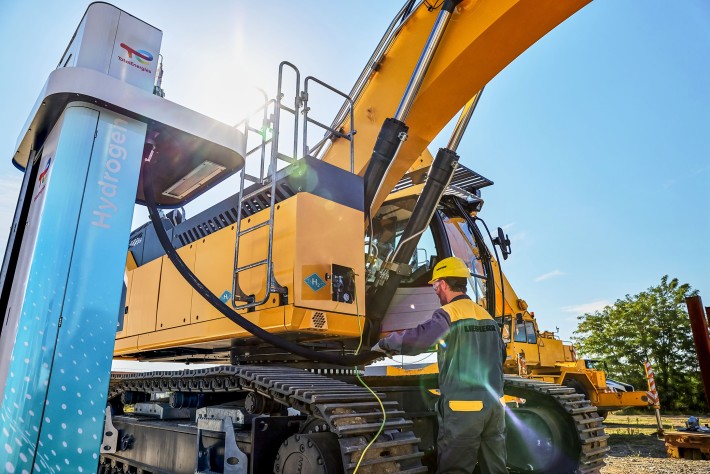
Hamm offers high performance soil compaction
Operating weights range from 11-25tonnes while engine power outputs range from 85-160kW. However, new ECO modes ensure more efficient operation and allow the machines to operate in partial load mode unless more output is required, saving fuel.
The cabs are larger and more comfortable, with even lower vibration levels for the operator than on the earlier models. A wide array of options is available including an automatic engine stop system and a dozer blade, while CR variants with reinforced drums for use on rocky ground will be available in due course.
All the new soil compactors can be fitted with the latest machine control systems from the leading suppliers, to suit customer preference.
Efficient recycling system for asphalt plants
The firm recognises also that using up to 100% RAP in the feed is dependent on the availability of quality material as well as effective logistics with regard to its retrieval and storage. For applications where lower quantities of RAP are to be used in the feed, Ammann also offers the RAH50 and RAH60 dryers, which have maximum usage of 50% and 60% RAP, respectively. In addition, the firm offers the RAC system, which can handle up to 40% RAP in the feed.
All Ammann recycling systems are able to produce high-quality mix with 100% virgin aggregate if so desired.
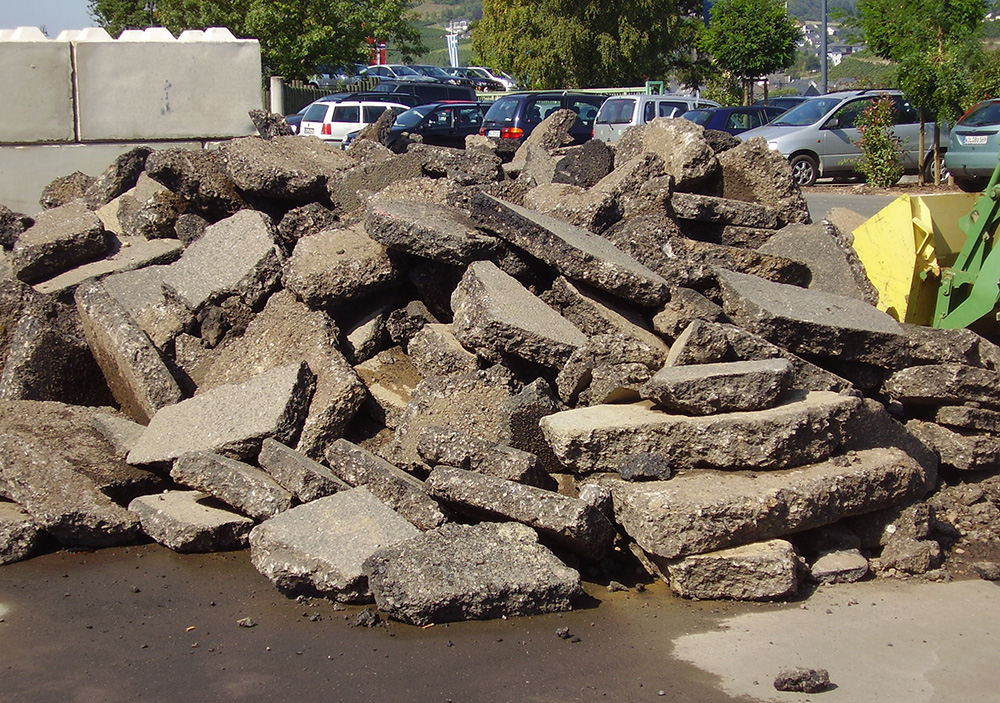
SBM’s Remax 600 crusher on show
As well as the standard version, it comes in a ‘summer’ edition with roofs and shade, and a ‘winter’ edition with full insulation cladding. Austria-based SBM is also adding a less expensive version to the range, which it hopes will sell in certain export markets.
The plants also come with a new, high-pressure cleaning system developed in-house by SBM.
Also being introduced is the Remax 600 crusher/screener, the idea for which was decided over the course of an afternoon and which has been developed in a year – around one-third of the time normally taken for equipment of this type. “We’re a family-run company and can make decisions straight away,” explained Jürgen Reischenböck from SBM’s marketing department.
The machine has what SBM describes as a very large capacity at the back of the unit, a 600tonnes/hour maximum capacity and has three deck screens, giving three finished products.
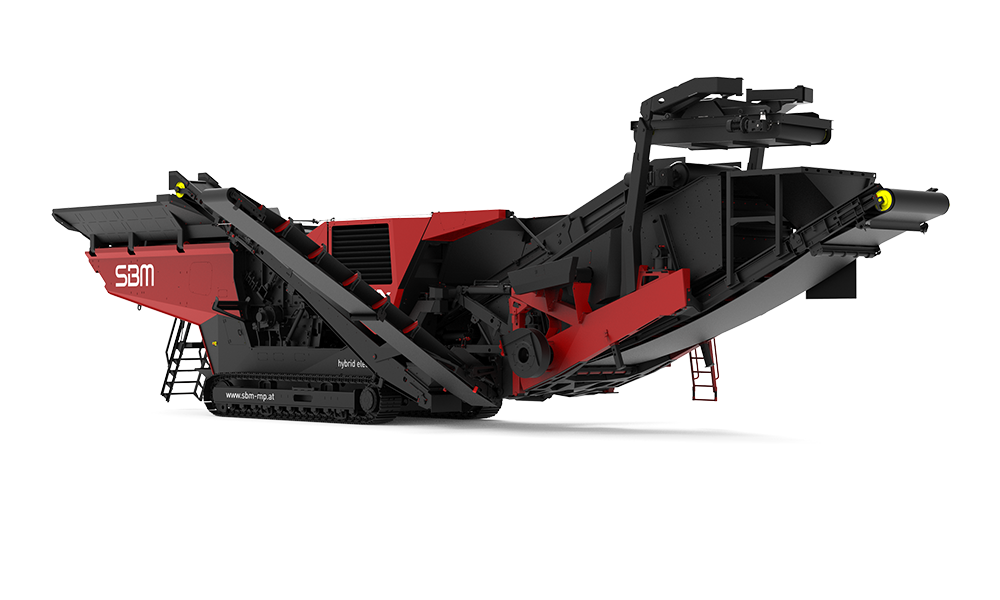
Kubota makes RT loader range electric
The RT105T-2 is based on the RT100-2, with an engine delivering 18.6kW compared with the 15kW of the earlier variant as well as a telescopic arm allowing a maximum height at hinge pin of 2820mm as against 2170mm. The company believes it will be an asset for customers requiring more reach, while still able to work in narrow jobsites like the RT100-2.
The RT210-2e and RT220-2e, meanwhile, are Kubota’s first electric articulated wheel loaders. Based on the diesel-powered RT210-2 and RT220-2, the Kubota engine is replaced by an electric system consisting of two electric motors – one to propel the machine and one working the hydraulics – plus a battery pack.
Kubota believes the RT210-2e will be of particular interest because of its lifting height, while the RT220-2e’s lifting capacity is aimed at construction and rental companies. The electric motors provide power on sites where quiet operation is at a premium, as well as having no CO2 emissions.
“The new RT105T-2 opens up the telescopic loaders segment for us and will be followed soon by another machine,” Kubota Europe product manager, Mathieu Bourson, said.
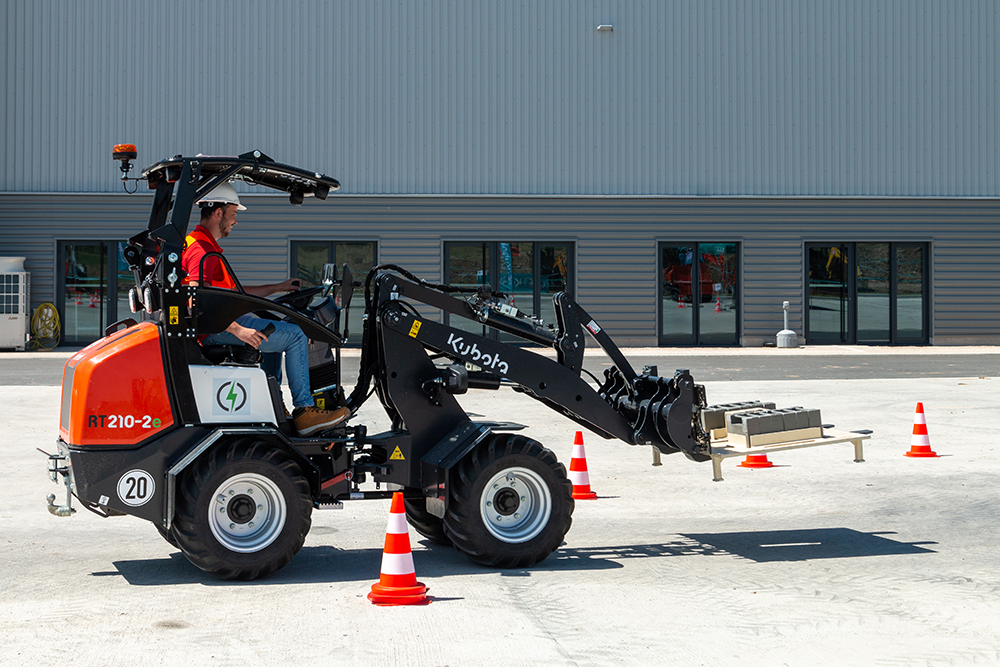
Meet the future with Wacker Neuson
The companies are presenting their solutions in three categories, called Meet Green, Meet Connectivity and Meet Innovation. Under "Meet Green", the brands will be presenting their zero-emission range, which will be expanded at Bauma to include a number of machines and services - such as special financing solutions.
The E-products are found in the "Meet Connectivity" area that highlights how construction machinery and equipment are increasingly digital to optimise efficiency and transparency.
Meanwhile, Wacker Neuson is showcasing its DNA in the "Meet Innovation" area where is it highlighting product development over the years and what is already on the drawing boards for future announcements.
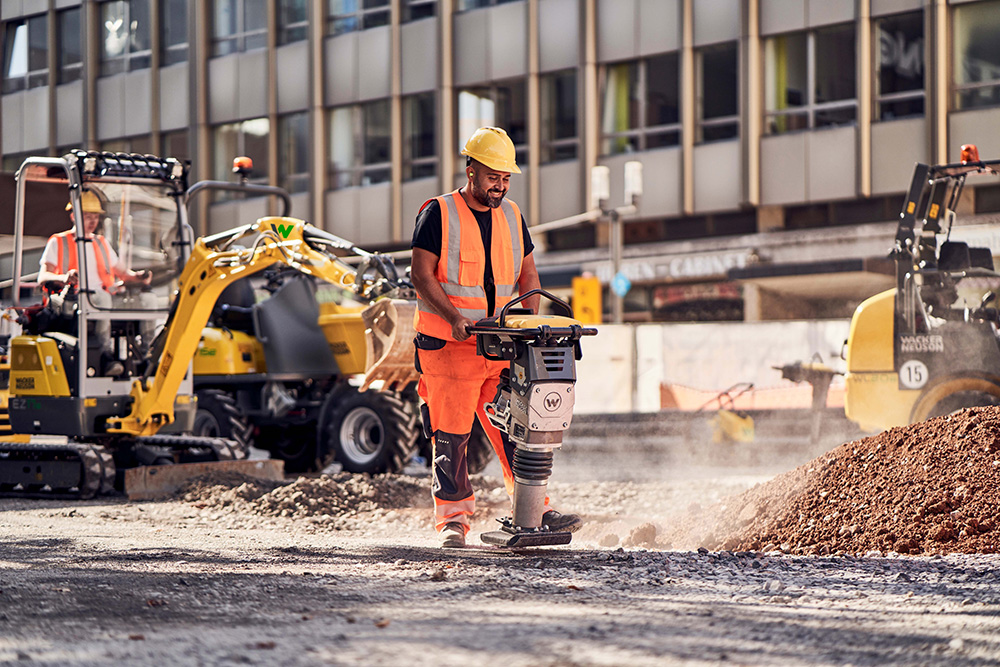
Peri bridges it with the incremental VARIOKIT VIL
The optimised shuttering and striking mechanism of the slab formwork via Roller Dropheads releases the formwork more quickly for time-critical work in the construction sequence and thus ensures accelerated workflows. Thanks to the cross-swivel head, the slab props of the mobile VIL Slab Formwork solution can also be folded up easily and do not have to be moved by hand. During the moving process, Roller Dropheads automatically bring the formwork back into concreting position.
Importantly, the incremental launching system offers another feature when used as external formwork. The distance between the cured concrete and the formwork is produced directly by means of a mechanism and thus, in the case of steep web walls, does not have to be moved in a horizontal direction as part of an additional work step.
Another advantage is that the clamping points of the trough formwork can be used for anchoring, thus reducing the number of lost components.
The clamping holes of the wall formwork can be used for anchoring the wall supports. The well-thought-out anchoring procedure reduces costs. Time-consuming scaffold tube bracing is no longer required. The flexible VARIOKIT formwork units can be individually adapted to suit the supporting construction and bridge geometry.
Based on the VARIOKIT Engineering Construction Kit, rentable project solutions can be created in order to accelerate and rationalise work operations.
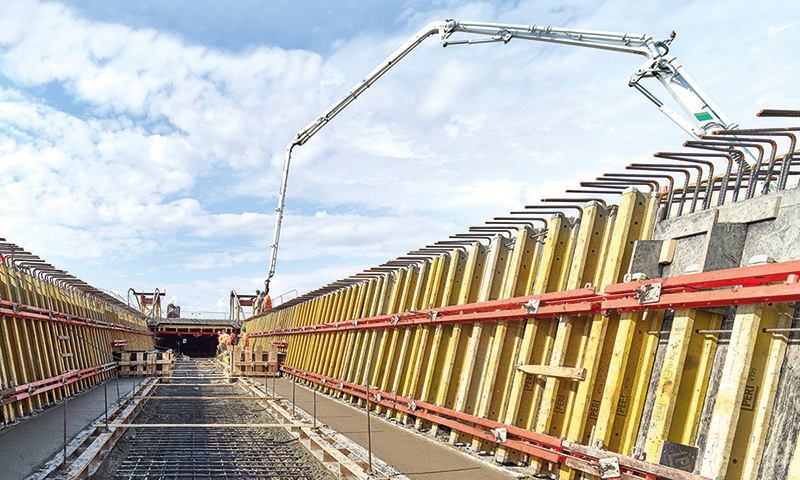
Electric power system from Liebherr
The electric power system can deliver up to 120kW for electric machines operating in urban areas or on sites where emissions need to be reduced. This fairly compact unit is the first in a range of electric power systems from Liebherr, with larger power packs being made available for use with bigger equipment in the future.
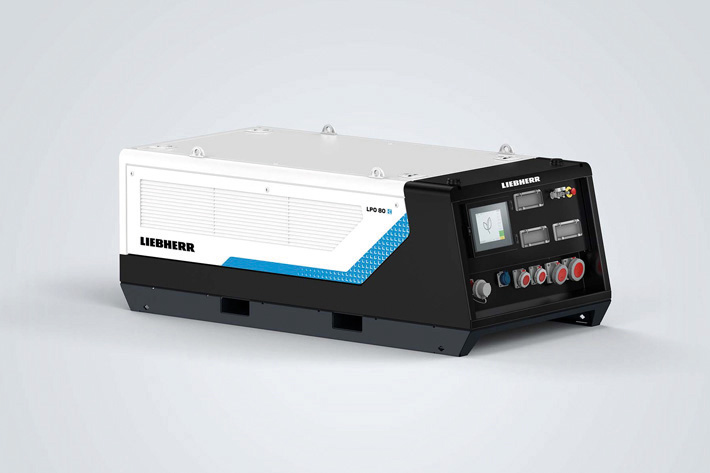
Efficient electric driveline from Volvo Penta
The technology has been trilled as a proof of concept in a modified terminal tractor and will be available for a wider range of industrial installations.
“We take a system supplier approach which means that we can create a flexible, bespoke electric driveline solution for a specific vehicle and application,” explained Morgan Blomgren, director Strategy & Business Development. “We are very experienced in a variety of different segments, so by using that knowledge and combining it with the Volvo Group’s proven electromobility experience, we can build the best modular platform for our customer’s applications. With that as a base, we can optimise the design and adapt the complete electric driveline system for a specific vehicle, considering the exact application, usage, climate and environment it will operate in.”
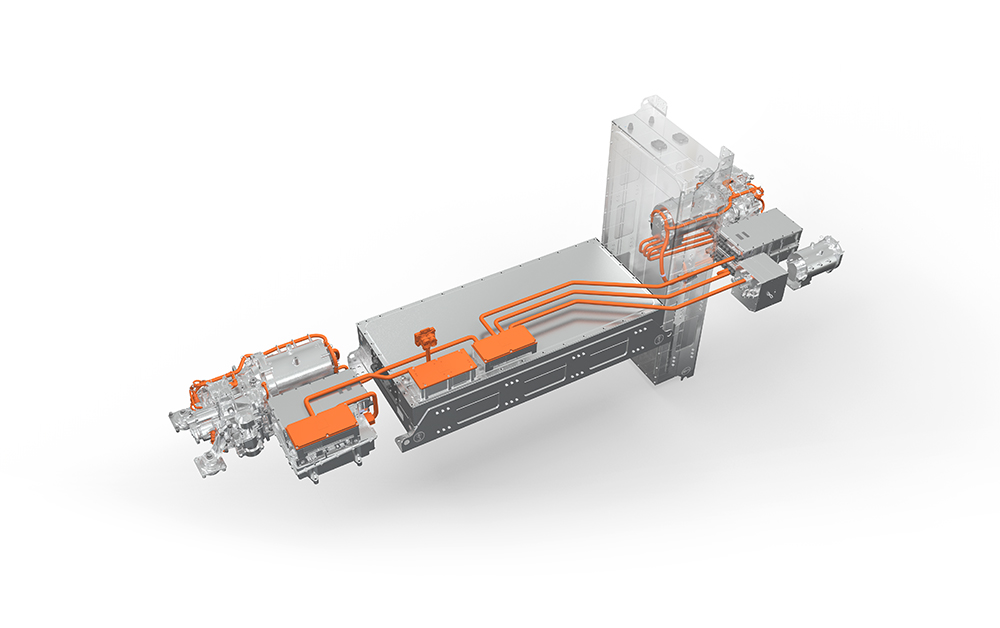
Innovative electric paver from Dynapac
Depending on the type of job, application, and intensity of the work cycle, the SD1800W e offers up to four hours of rugged performance with one single charge. Charging is done with a provided CE-compliant Type 2 plug for 400V, 6-32A, 1.4-22kW AC.
Charging can be achieved using a wall box or a charging station. The SD1800W e is also chargeable using a Type 2 AC or CCS2 DC. Depending on the battery's condition (temperature, battery cycles) charging takes around three hours to go from 5% to 80% @ 400V 22kW (AC) and 40 minutes to go from 5% to 80% @ 80kW (DC). And while charging while working is not possible, a user can pre-heat the screed with the charger (with Type 2 AC or CCS2 DC) while waiting for the material to arrive, preserving the battery level.
The SD1800W e is similar in its build & performance to the diesel powered variant. The electric model delivers a paving capacity of up-to 350tonnes/hour and can pave widths up to 4.1m with the screed extended.
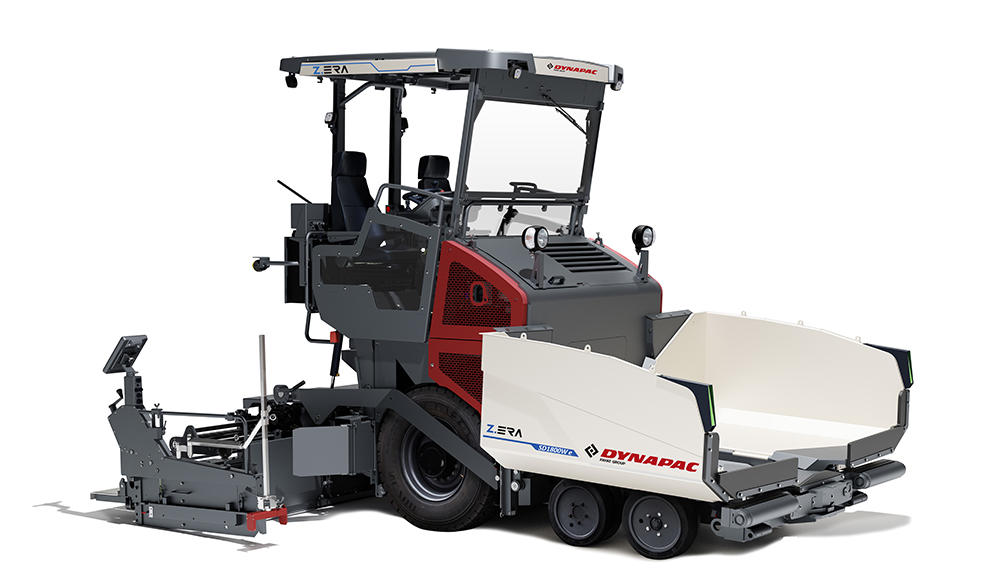
Mini paver options from Vögele
The four compact models share many features and the tracked MINI 500 is available with diesel power or as an e variant, with battery electric drive. Similarly, the MINI 502 wheeled model is offered with a choice of diesel power or as the battery electric e variant. The machines are suitable for use in small-scale construction projects that include constructing cycle and pedestrian paths, paving between railroad tracks as well as repair work in small inner-city sites.
The standard screed working width is 0.8m and it can be enlarged up to 1.35m hydraulically. The minimum paving width can be reduced down to 0.25m, while the width can be built up to a maximum of 1.8m using bolt-on extensions.
Compact transport dimensions of 2,670 x 870 x 1,585 mm and low weights of between 1tonne and 1.5tonnes are said to allow for easy transport. A narrow turning radius is a feature of both the wheeled or tracked variants.
The new Vögele MINI series has been developed in partnership CM, an Italian company that will also build the machines for Vögele.
BOMAP: Smart Compaction Control.
We have developed BOMAP for maximum benefit with the simplest operation. The app works on regular Android smartphones and tablets without the need for special hardware. BOMAP is immediately ready for use on all earthwork and asphalt construction sites worldwide, increasing efficiency and ensuring the best results. Including comprehensive documentation from A to Z. BOMAP impresses with many useful functions that are easy and intuitive to use. No training is required. BOMAP is perfectly compatible with BOMAG JOBLINK. Together they make a perfect team for the seamless digital construction site, and guarantee maximum efficiency.
Norway transport budget boost
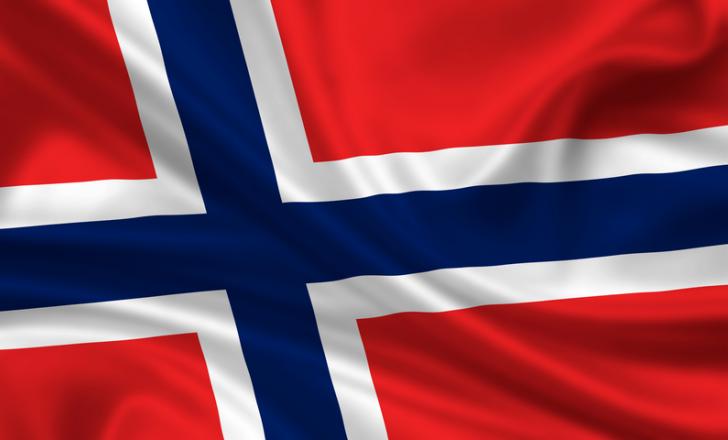
Rebuilding Australia’s flood-damaged roads in NSW
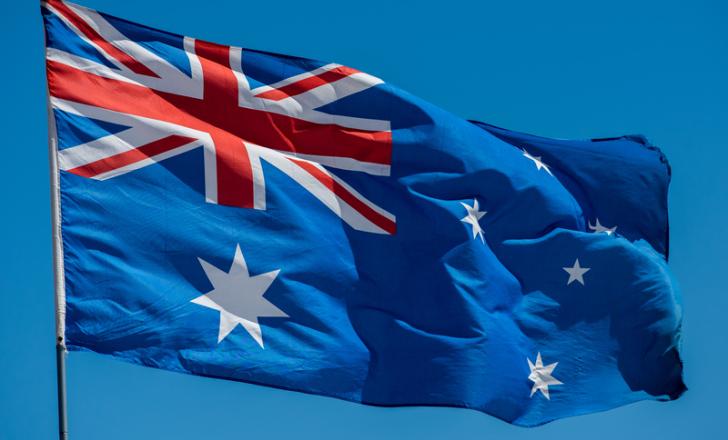