Skanska wins major A46 upgrade in England
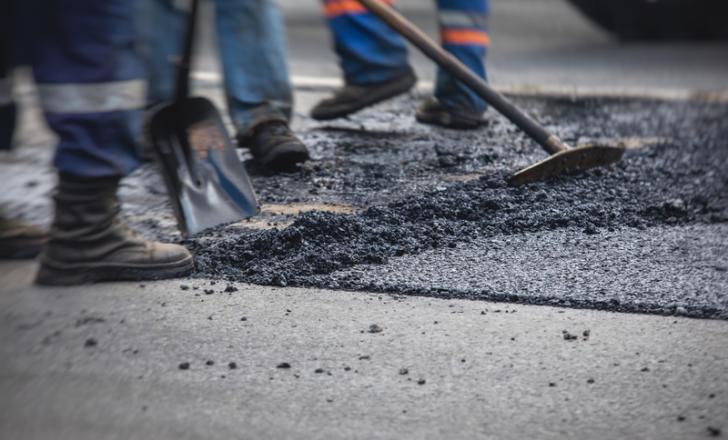
Indian airport revamp sets record

Capital Beltway widening to go ahead
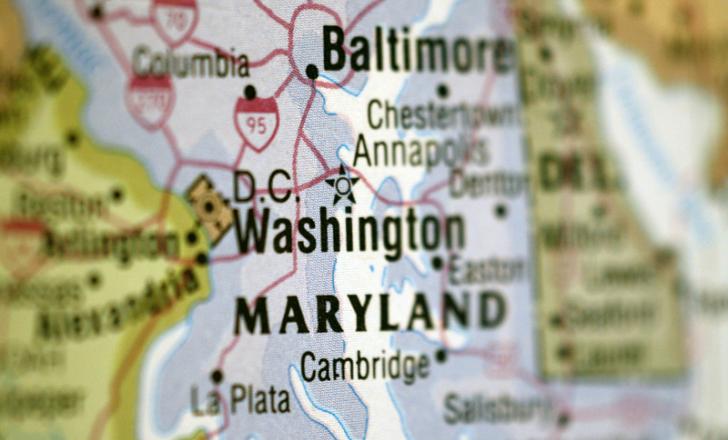
Rubble Master highlights big innovative hybrid plant operating savings
The Austrian company has been powering its mobile processing plants with electricity for decades. Using this expertise, Rubble Master says it is continuously setting standards in the energy efficiency and cost-effectiveness of its machines. That is why with the tagline Meet the future, Rubble Master says it is displaying technology that "is still a dream of the future for others".
With the claimed revolutionary new development of the showcased RM H50X hybrid screen and the RM J110X jaw crusher, customers are said to be saving even more fuel costs. In addition, the RM XSMART software solution and other new digital innovations demonstrate how operators and machines can network intelligently to get even higher output. As a result, mobile RM crushers and screens can be combined in a versatile, flexible and efficient way.
Even at a time before steadily rising fuel prices, the electrification of Rubble Master machines was said by the company to be a "key economic as well as ecological argument".
As part of the RM NEXT philosophy, the RM Group says it is consistently supporting electrification and offers all its crushers and screens as hybrid versions as a matter of principle. These machines can also be operated fully electrically. A special focus is on combining machines to form crushing and screening trains so they can be operated together. This means, for example, that the crusher can also power the screen. That is how customers can save time and money because they only need to refuel and service one engine.
Rubble Master hybrid machines are said by the manufacturer to consume up to 25% less fuel than diesel-direct systems. If a crusher equipped with a hybrid drive system also powers an electric screen - a standard set-up with RM - even greater savings are said to be achievable. With this technology, the savings are said to be much higher than with conventional diesel-hydraulic systems. Another advantage, in addition to lower operating costs, is that the machines can be used in emissions-sensitive areas.
Digital solutions and networked machines increase efficiency in addition to electrification, and Rubble Master is focusing intensively on digitalisation to give customers a full overview of their machines while operating even more efficiently. Using the RM XSMART app, machine operators can network with their machines either using an app on their mobile devices or by using the browser app. Fleet management, condition monitoring, end-to-end reporting, and troubleshooting support make everyday life much easier and, at the same time, increase productivity. Rubble Master, however, says it goes one step further by networking the machines with each other. In a networked crushing and screening train, the machines can communicate with each other to adjust their output to optimise the utilisation of the upstream and downstream units or react to an event such as one of the machines in the train switching off. This means that machines are not overloaded, nor do they run idle. Rubble Master says autonomous crushing and screening is the next logical step the group will be presenting soon.
New road works planned for Kazakhstan
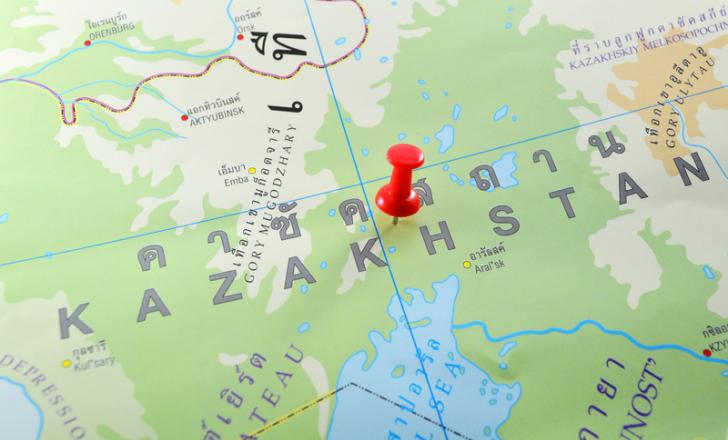
Volvo CE increases hybrid range with new gentle giant
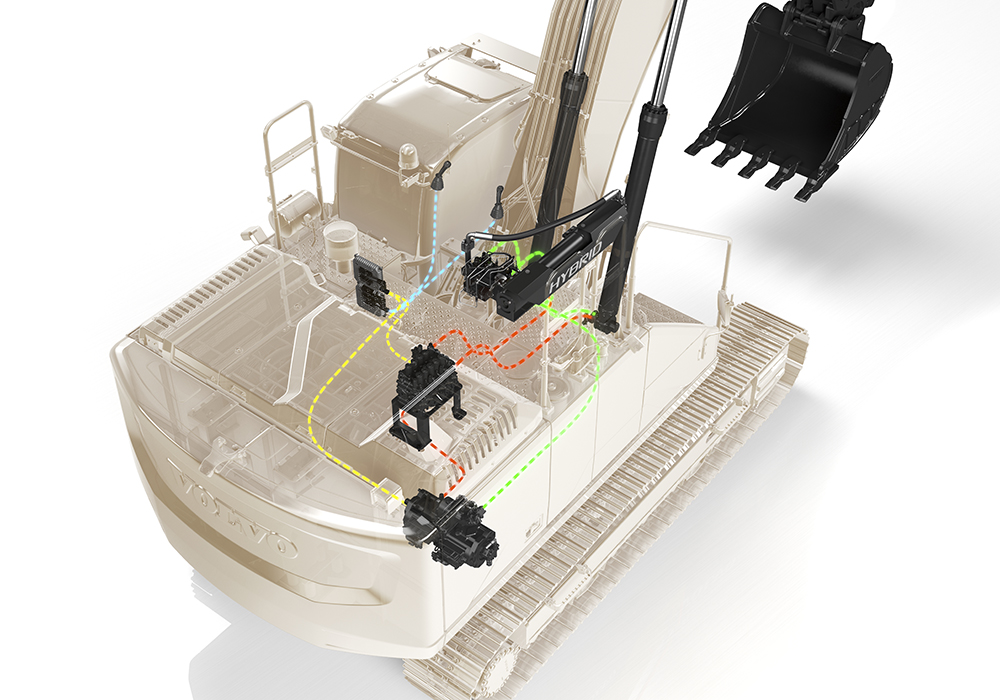
Difficult terrain in Ostend
Soil stabilisation with the BOMAG RS 300 tractor-towed stabilizer.
In the Belgian city of Ostend, soil stabilisation with lime was required for 4,000 square metres of future industrial space. The Verhelst Aannemingen company was commissioned to carry out the work. The Ostend-based family business used the BOMAG RS 300 tractor-towed stabilizer for the first time.
Shhhh, keeping roads quiet
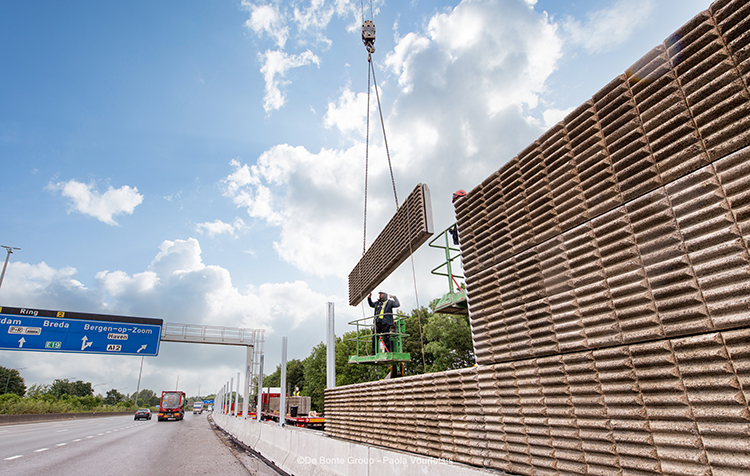
Plant retrofit reducing odours
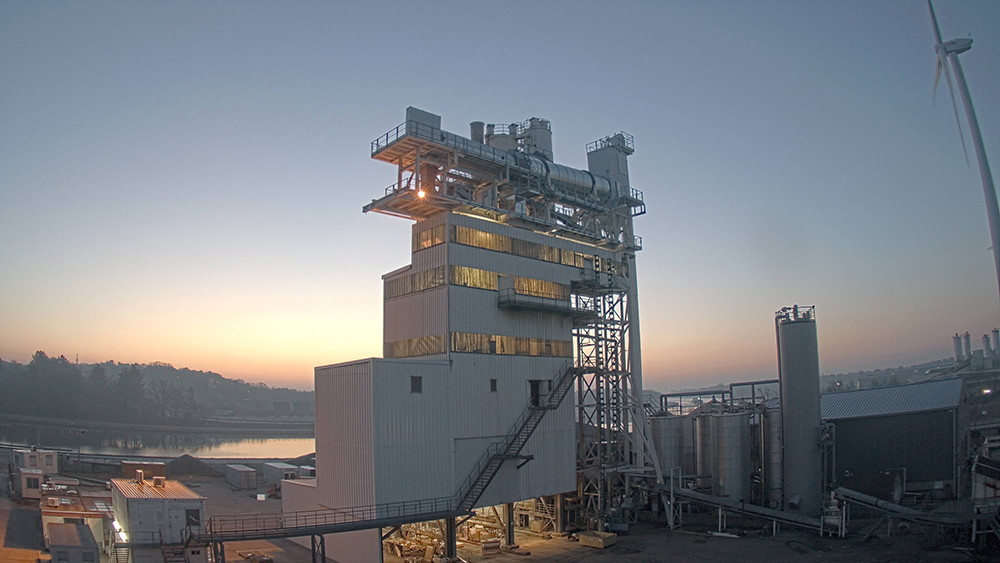
Optimised soil compaction system
This intelligent technology allows the roller to determine the optimum frequency for any compacted material automatically. An onboard machine control unit and next-generation compaction meter work together to allow the SEISMIC system to sense dynamic characteristics of the ground and calculate the optimum frequency for compaction. The process uses advanced data flow from the SEISMIC Compaction Meter to the onboard machine control unit, which regulates the hydraulics. SEISMIC technology automatically detects the resonant frequency of the soil. This system automatically applies the correct compaction forces exactly where required and can hydraulically change the drum frequency, every 0.2 seconds for maximum performance. As the drum no longer randomly hits the soil, it achieves precision and efficiency while saving time and fuel.
The system increases job-site productivity while reducing the number of passes required and eliminates the risk of over- or under-compaction. Fuel consumption can be reduced by up to 55%, while productivity can be boosted by up to 40%. Due to lower frequencies, noise levels are also reduced while operating at lower frequencies also helps to reduce maintenance needs for the machine.
The SEISMIC feature is now available for Dynapac soil compactors ranging from the 7tonne CA1500 to the 21tonne CA6500 model.
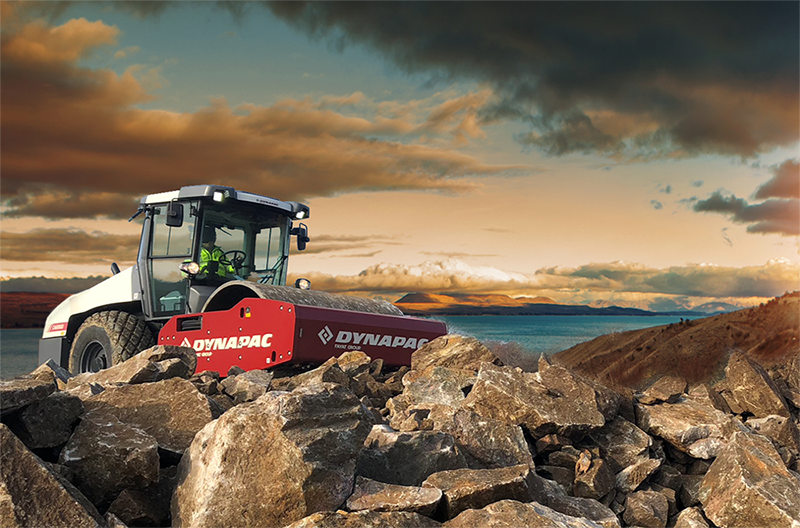
Hannes Norrgren appointed Volvo Penta Industrial president
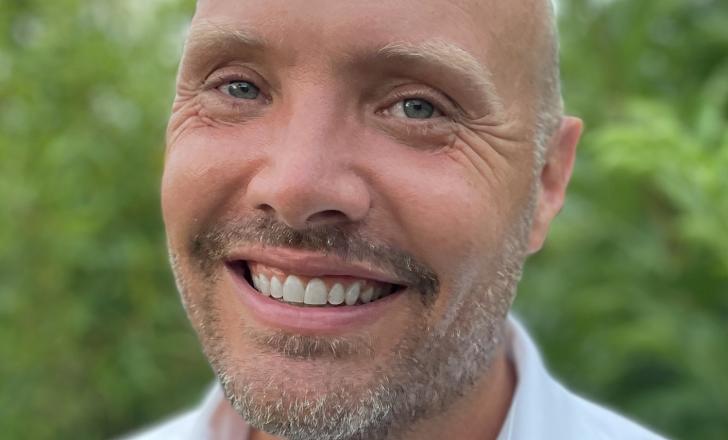
North Carolina road widening contract for Ferrovial
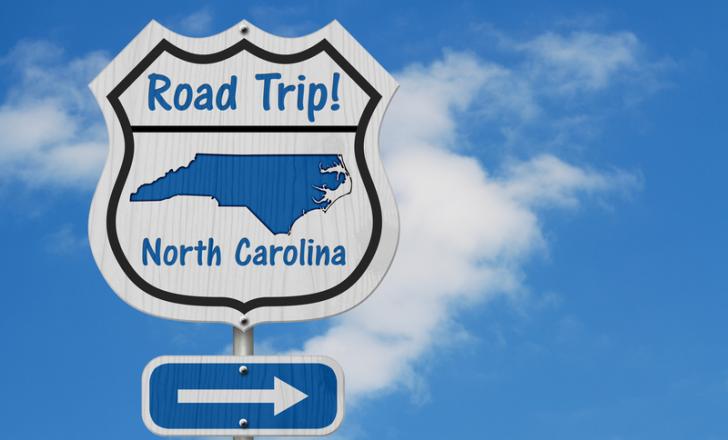
Recycling the Italian way: FAE, Simex, CAMS
FAE says that its dedicated soil stabiliser is now well-accepted and can work to depths down to 500mm. Because the unit is towed by large tractors, it is suitable for smaller and more compact sites where self-powered stabilisers would be difficult to use.
As the units are towed by large tractors, the company also distributes the machines through a number of tractor dealers, according to Giorgio Carera, chief executive of FAE in North America. “That’s the kind of distribution we use.”
Vision Zero for the Balkans: IRF road safety conference
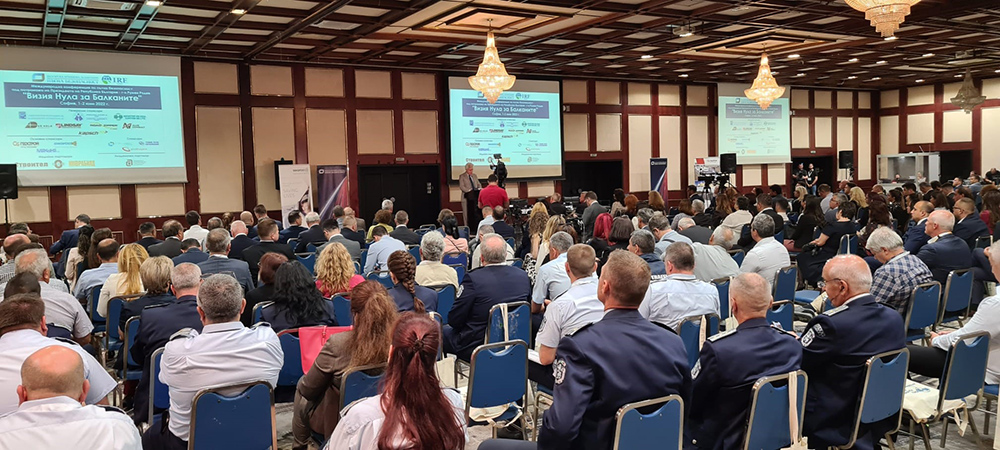
Concrete paving success with Power Curbers
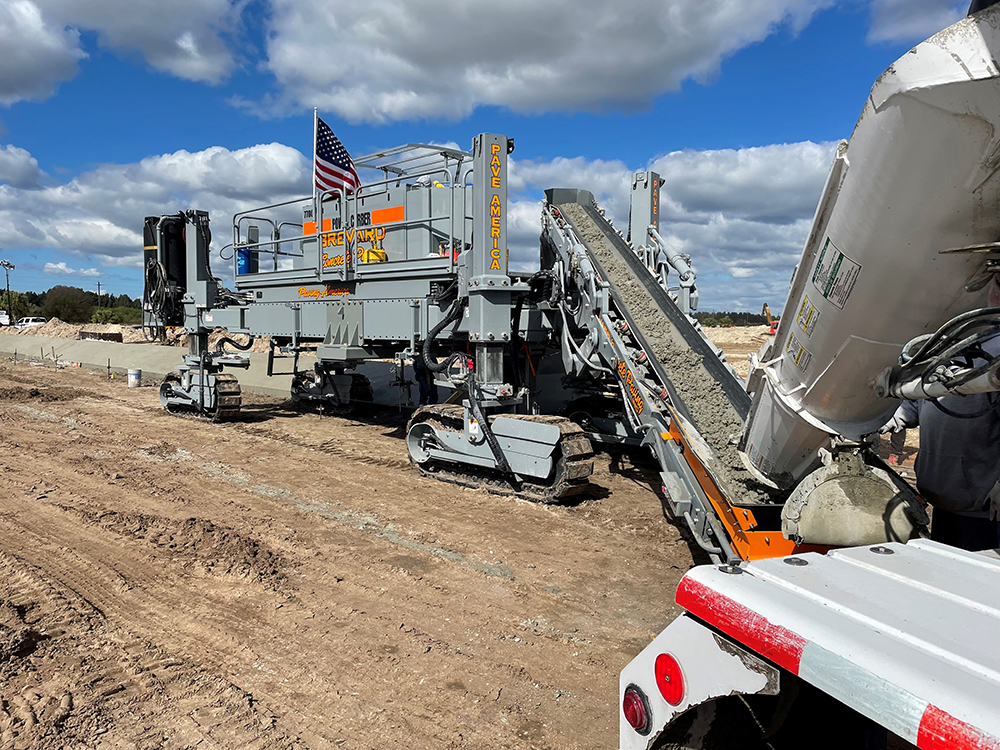
Efficient continuous asphalt production
The TSX models have been developed to meet the need for an increase in recycling of materials such as bitumen and aggregates, as well as the reduction in the quantities of CO2 emissions linked to production and transport logistics of these raw materials. The TSX technology also benefits from a new process called DUOTHERM. This combines thermal exchanges between RAP and slightly overheated aggregates and thermal exchanges between RAP and moderate-temperature gases that have already exchanged with aggregates beforehand. Using this technology helps to reduce emissions into the atmosphere, below statutory regulations.
The TSX technology ensures a high-quality mix as it features a single dryer drum composed of three distinct zones, associated with a twin-shaft mixer as a standard. The first is the combustion zone, where the burner’s flame expends and generates hot gases to heat-up and dry materials. In the second zone, hot gases from the first zone exchange heat with the aggregates, drying. This zone also acts as a thermal screen to avoid any flame radiation in the third zone. The third zone meanwhile is where the RAP is introduced by the recycling ring but the material is protected from a direct flame by the second zone. Drying of the RAP occurs in the third zone due to the DUOTHERM process.
During this operation, RAP binder migrates homogeneously onto the aggregates. At the drum outlet, this homogeneous mix is conveyed to the twin-shaft mixer where it is mixed with imported binder and potential rejuvenator. Meanwhile, the long mixing time ensures full binder remobilisation.
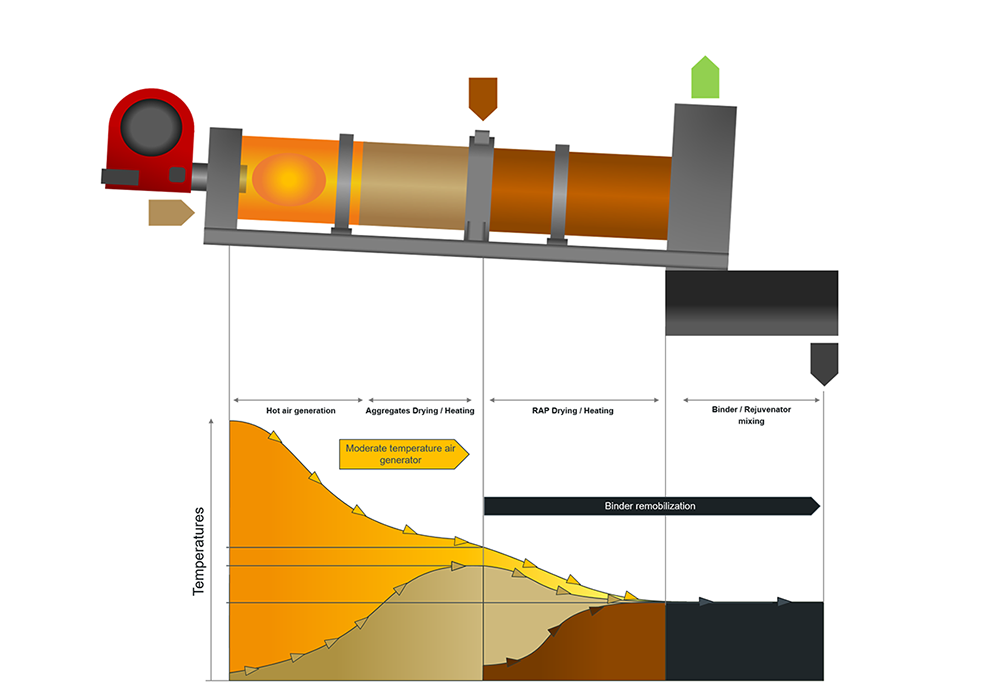
Malaysia boosting transport infrastructure
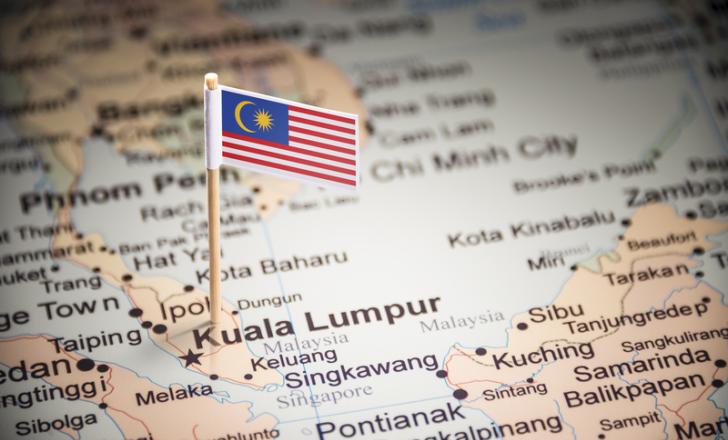
Florida and one.network in lane closure pilot

Peru’s Oyón -Ambo Highway presents challenges
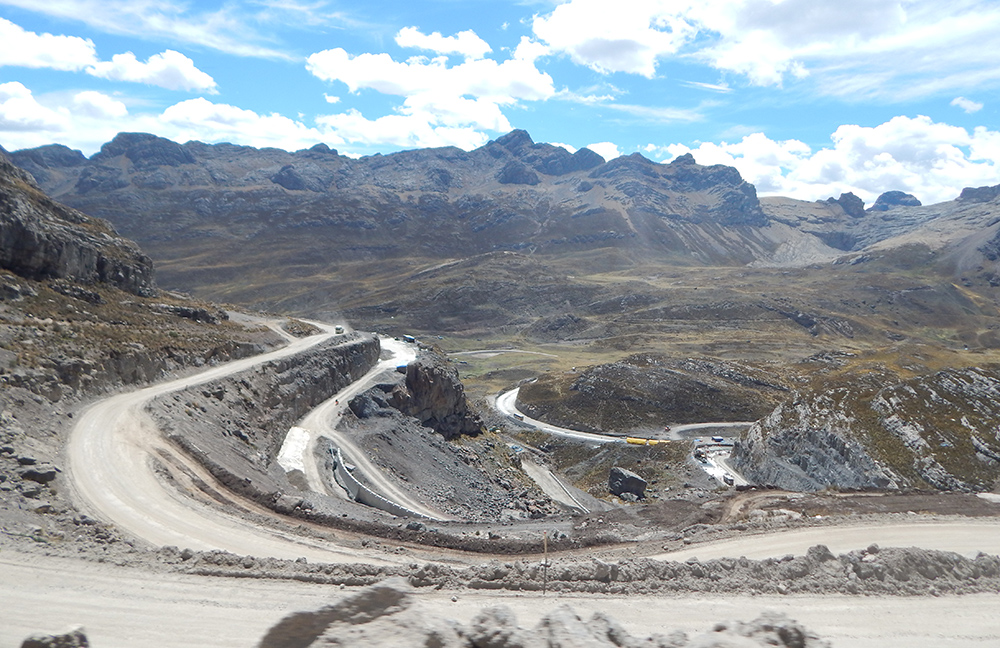
Powerful demolition machine from Kobelco
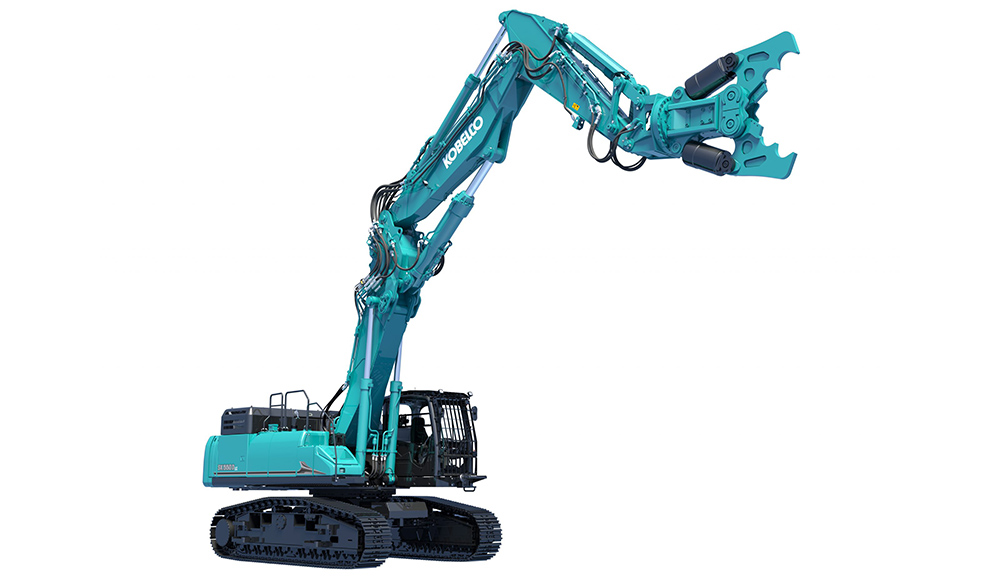