Atkins wins Cork N40 Ten T work
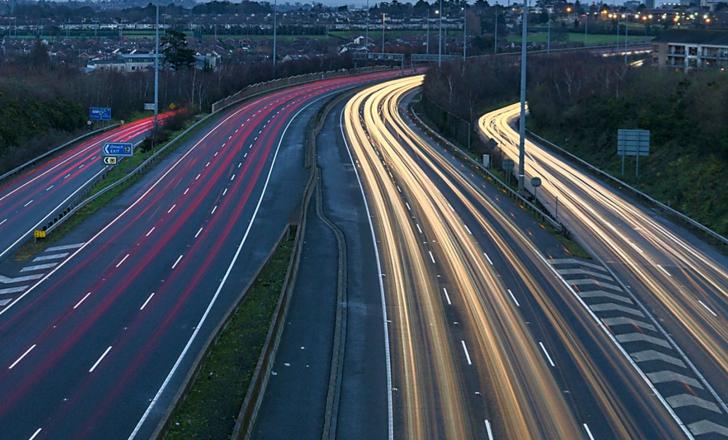
Efficient crushing from Kleemann
The machine features an all-electric drive concept with the option of an external power supply, offering low energy consumption/tonne of final product. The optional large double-deck secondary screening unit allows the production of two classified final grain sizes. The MR 130(i) PRO is highly versatile and can be used in a wide application range in natural stone and recycling. With its heavy rotor and powerful electric 250kW drive, the crushing unit is said to deliver a high and stable throughput. A continuous crusher load is guaranteed by the Continuous Feed System (CFS).
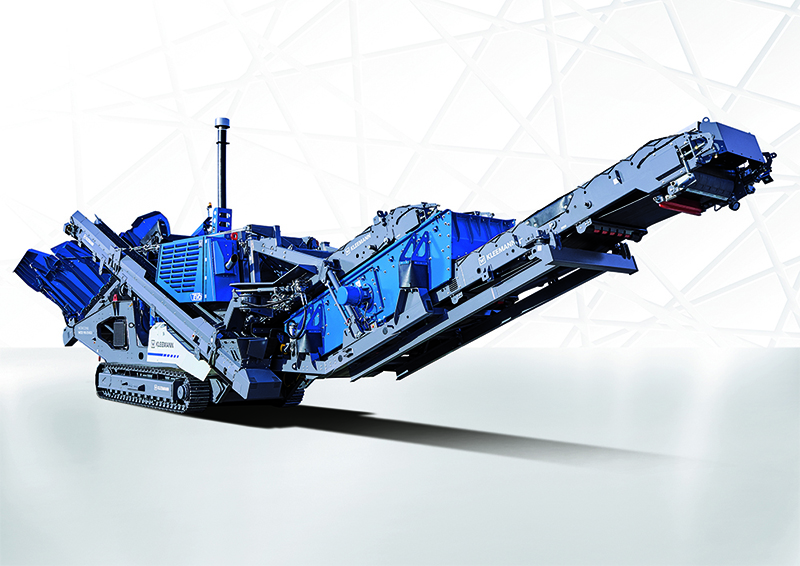
US road safety is a concern
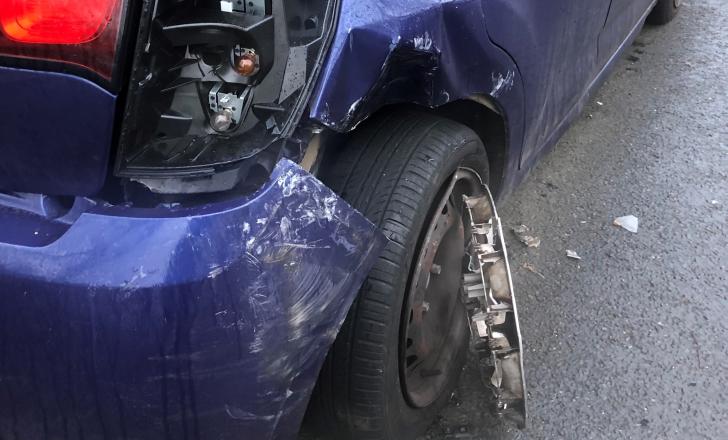
Colombian dual carriageway contract signed
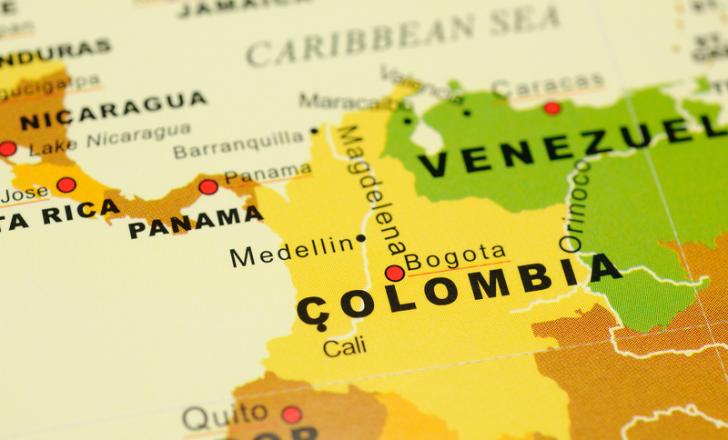
Clean engine power from Volvo Penta for Metso Outotec
According to Volvo Penta, output is high and maintenance needs are low as its Stage V-compliant engines are optimised to meet customer needs in terms of productivity, uptime and TCO. Passive regeneration of the aftertreatment system has been maximised, for example, eliminating unplanned stops during operation, while fuel consumption has been reduced by up to 5% over the Stage IV models.
The D16 offers an output of up to 585kW as well as a 10% reduction in fuel consumption over the earlier generation unit. By incorporating water-cooled charged air, its dual-stage turbo delivers high performance right across the operational range, enabling maximum torque to be produced at both low and high engine speeds.
On top of its low fuel consumption, the D16’s reliable Exhaust Aftertreatment System (EATS) has been designed to use selective catalytic reduction technology only, removing the need for exhaust gas recirculation (EGR) and a diesel particulate filter (DPF).
By incorporating water-cooled charged air, the D16’s dual stage turbo system delivers high performance across the operational range, providing high torque at both low and high engine speeds. This allows the engine to be used in multiple applications, without compromising between performance and torque.
In addition to leveraging an array of proven technologies and expertise from across the Volvo Group, the firm is working on innovative driveline solutions.
“In the short-term, the focus is still very much on internal combustion engines and we will continue our development work in this area to stay competitive,” explained Morgan Blomgren, director Strategy & Business Development. “Our engines are already able to run on HVO and biodiesel, and to further support our transformation journey to zero-emission solutions, we are also looking into powering them with CNG, biogas and hydrogen, as well as the use of hybridisation – all of which are likely transitioning solutions for those markets that cannot yet support fully electric solutions.”
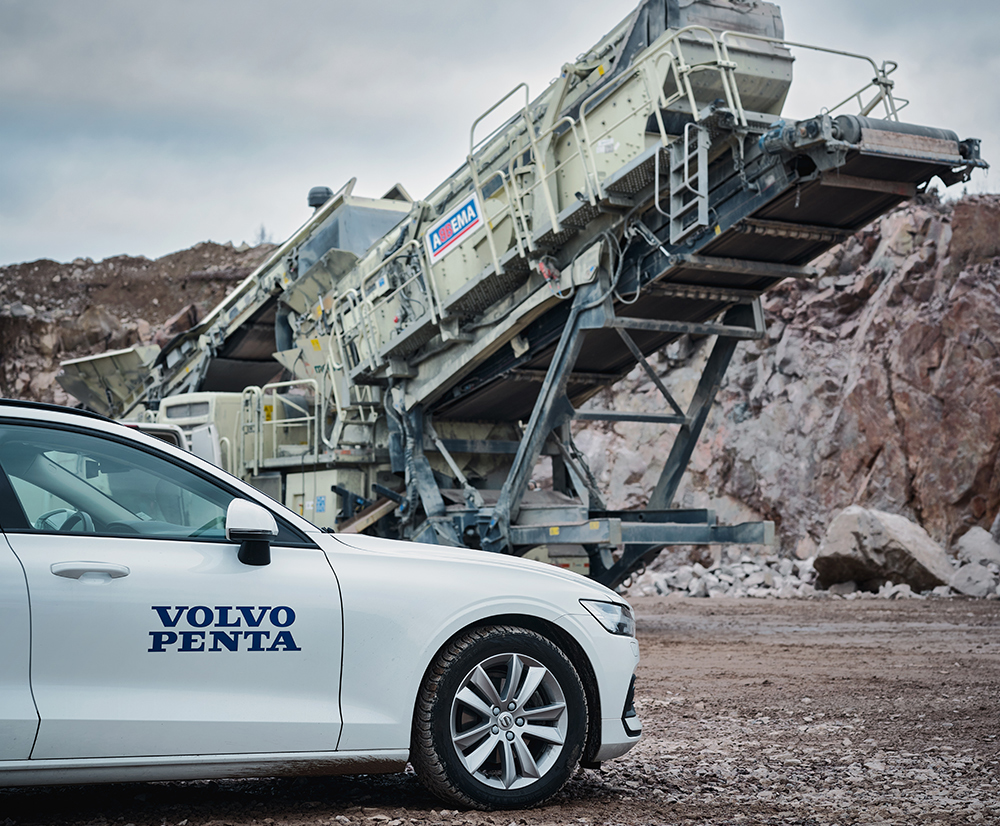
Generate real-world ROI with reality modeling!
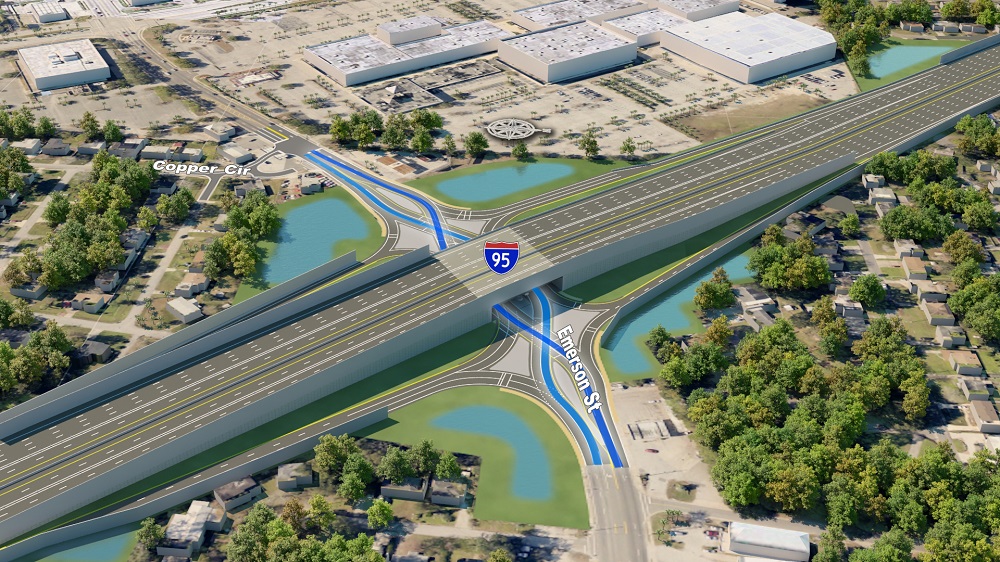
Digital Construction Works develops new fully-integrated highway design and construction workflow tool
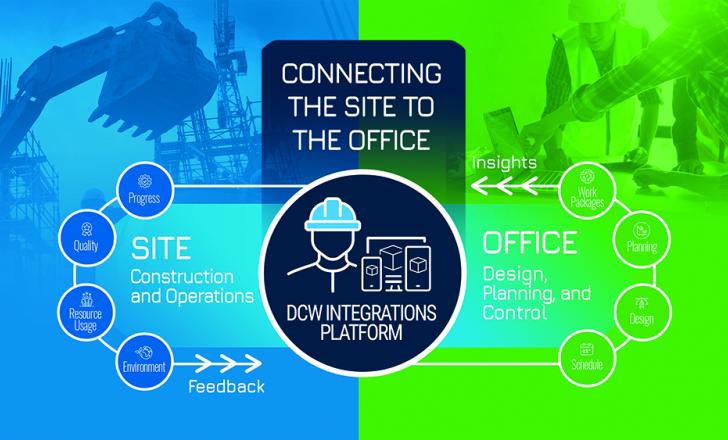
El Salvador’s new road projects
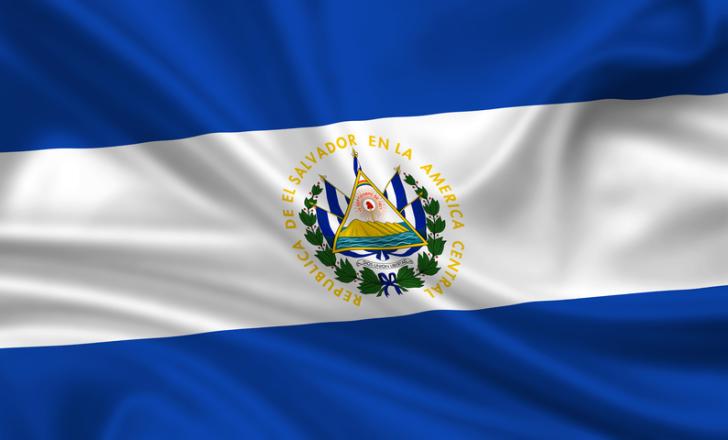
Revamped US-Mexico border crossing
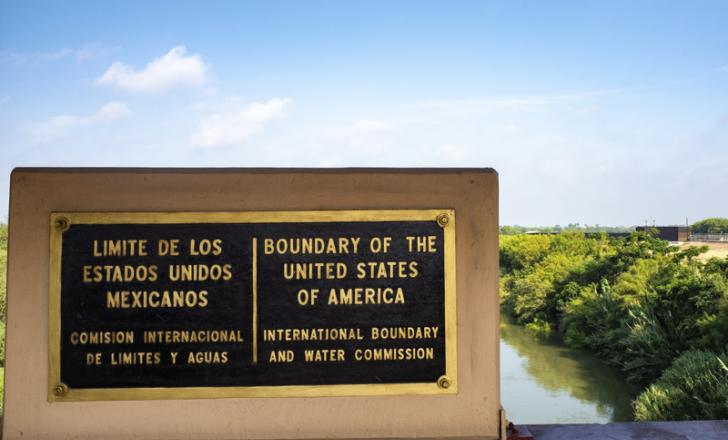
Ahmedabad airport roll-out for Dynapac
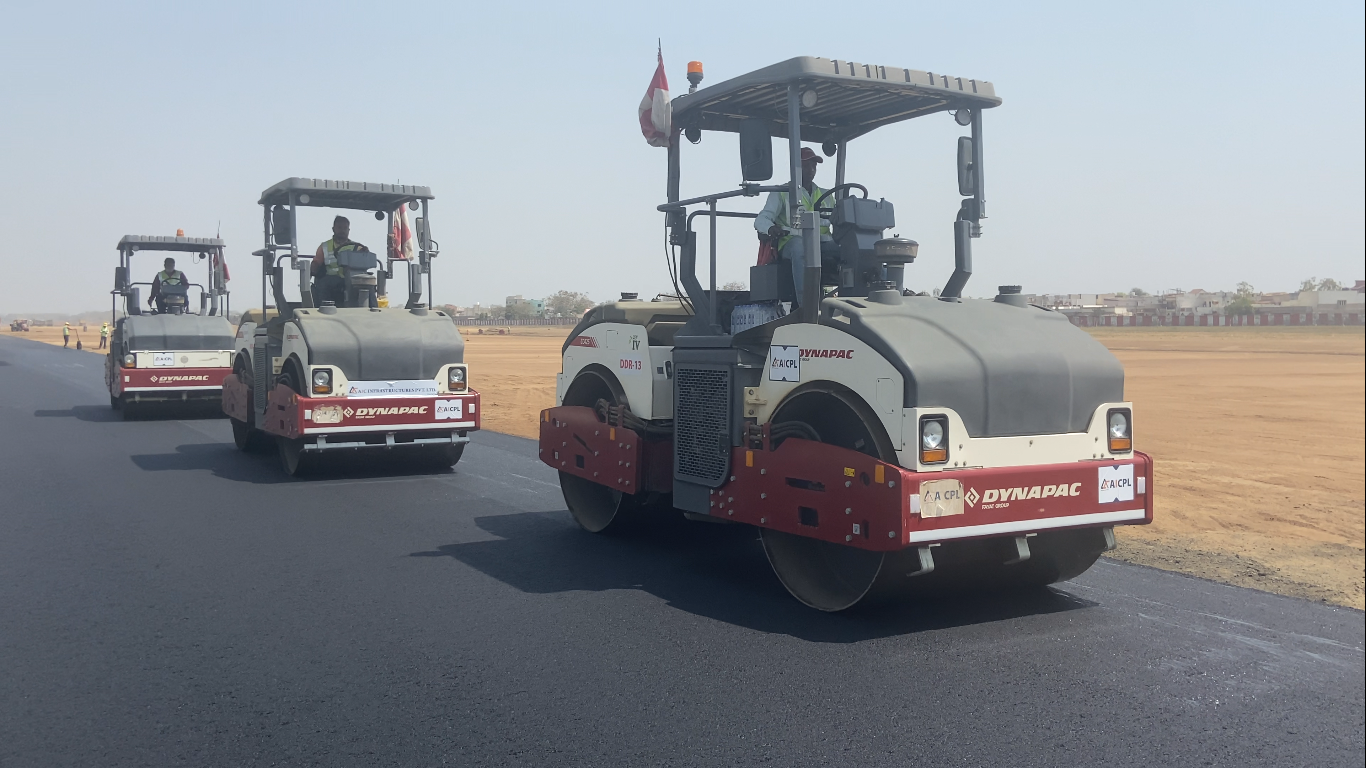
Efficient concrete batching plants from Liebherr
The Betomix and Mobilmix mixing plant series use prefabricated modules and replace several earlier models. Increased weighing accuracy allows up to 7.5kg of cement to be saved for each 1m3 of concrete produced, reducing operating costs.
Various modules can be combined with other modules, while the units are prewired and assembled at Liebherr. These modules are within the 3m width restrictions and can be delivered as complete units to the construction site, reducing transport costs while they can be quickly assembled and commissioned.
Liebherr offers its own twin-shaft or ring-pan mixers and different units can be specified as required. The units can provide rates of 100-210m³ of compacted fresh concrete/hour while optional accessories can be integrated. Different storage facilities for the aggregates can be incorporated, such as a tower silo or the optional winter cladding.
A new high-pressure mixer cleaning system, LiClean, combines with the creep speed cleaning mode, to ensure optimum cleaning. In addition, an optional automatic cleaning system is available for the truck mixer feeding hopper.
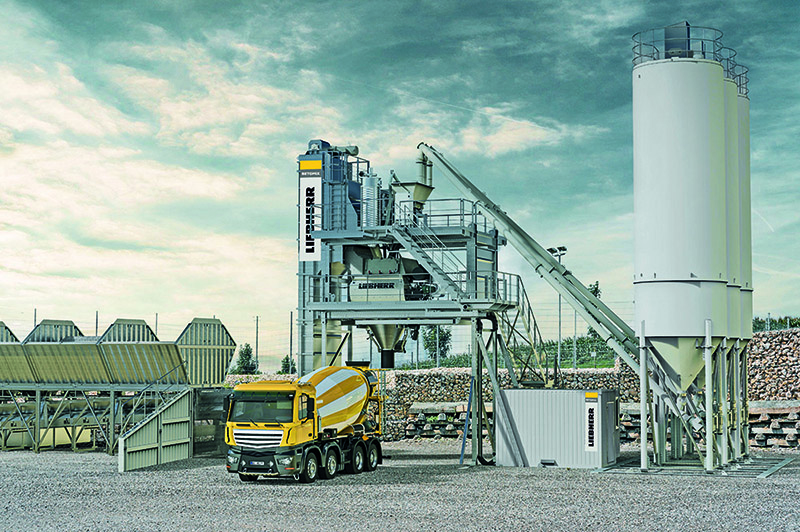
New road project for Gabon
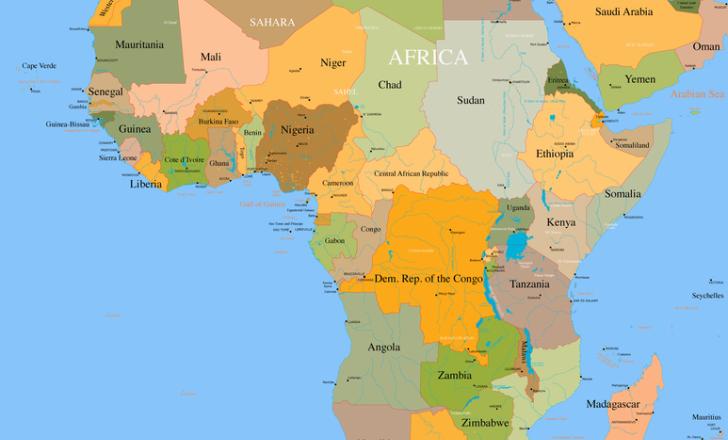
The power of the future with Kohler
Kohler already offers some electric power options and will be expanding this segment with new electric motors coming soon and additional battery technology in the future. The company says that its engines for Europe and the US can run on alternative HVO fuels, while the company is working on solutions that will allow the use of hydrogen as fuel in its internal combustion engines.
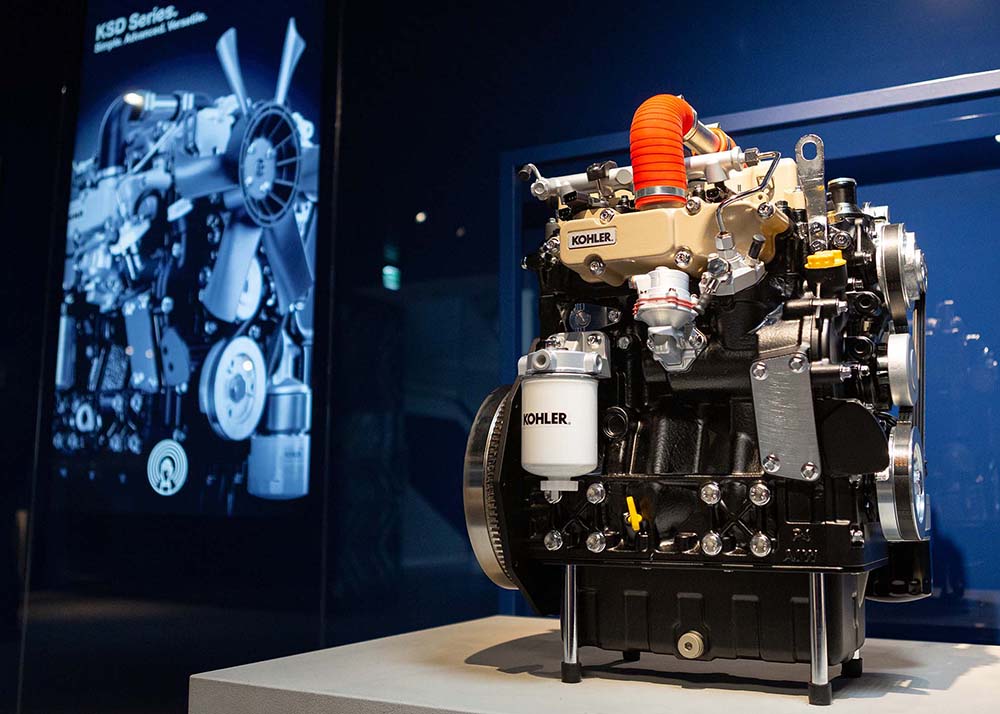
New German bridge - cost increase
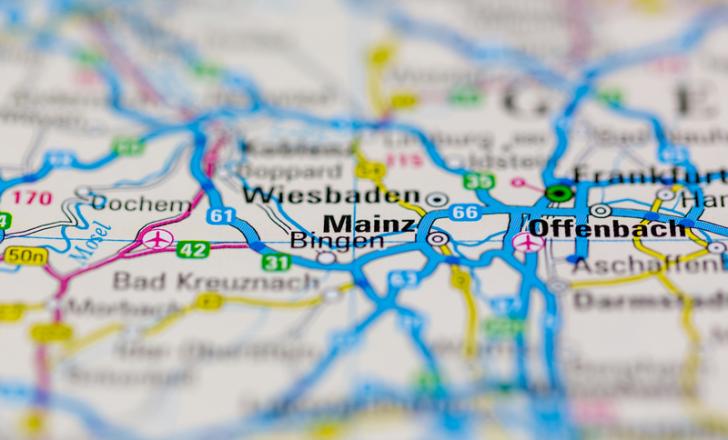
New roads for Vietnam

Benninghoven | The fuels of the future are carbon neutral
Power Curbers ramps up Florida projects
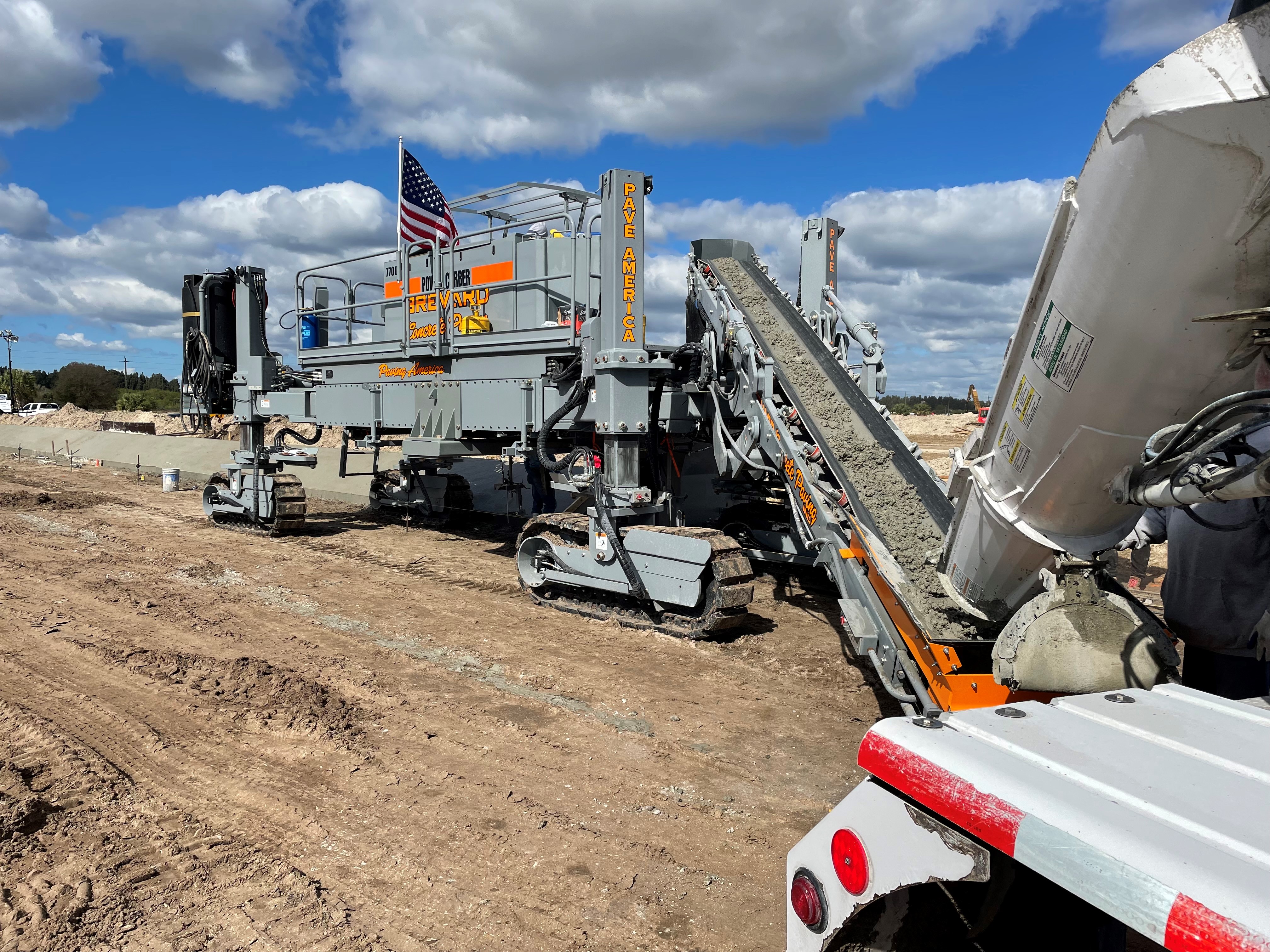
Foiled by foliage
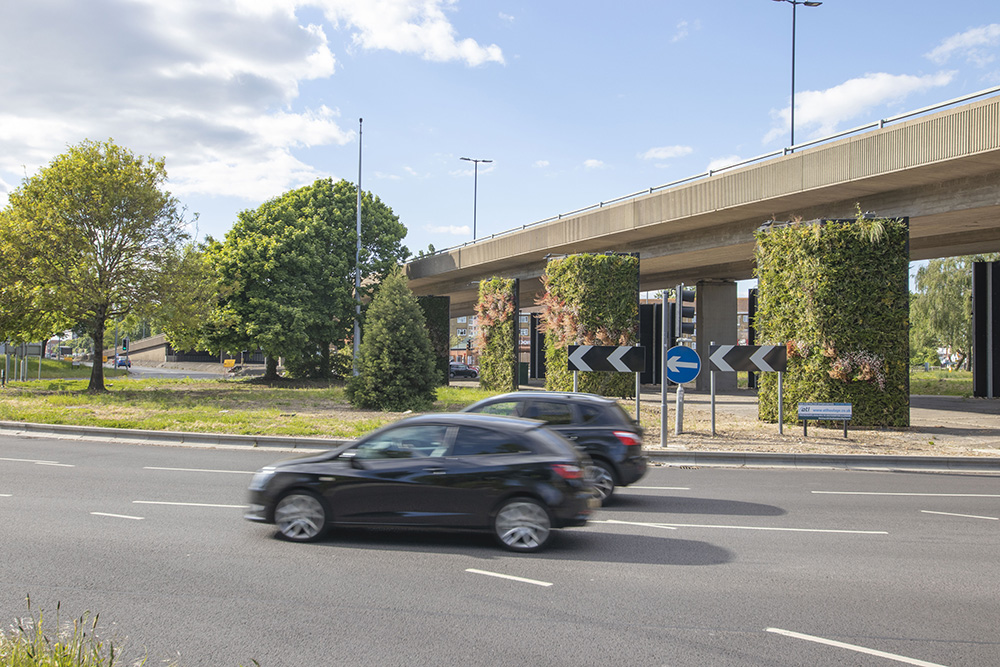
Electric compact asphalt rollers from Hamm
There are 24 models in the conventional CompactLine at present, with weights ranging from 1.6tonnes up to 4.8tonnes as well as drum widths from 800-1,380mm and an array of specifications and features. Hamm has offered emissions-free electric variants of the most popular units however.
The new electric models feature Li-ion batteries with 23kWh capacity, allowing operation for a full working day without the need to recharge. Included in the electric range is a model featuring both oscillation and vibration, the first such model available on the market. This last unit will be of particular benefit for working in urban areas as it is quiet in operation while the oscillation system means it does not transmit vibration to the surrounding area.
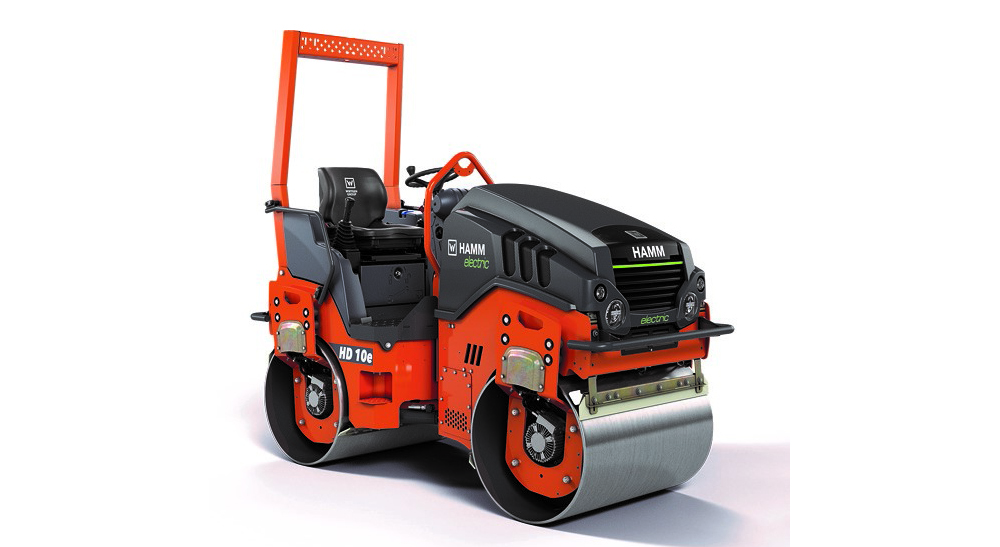
Tajikistan infrastructure projects
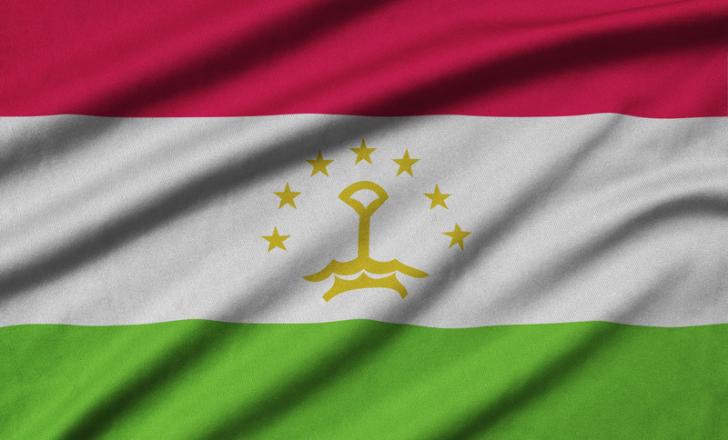