Slovakia’s D1 highway project underway

Mostostal Warszawa picked for S19 segment
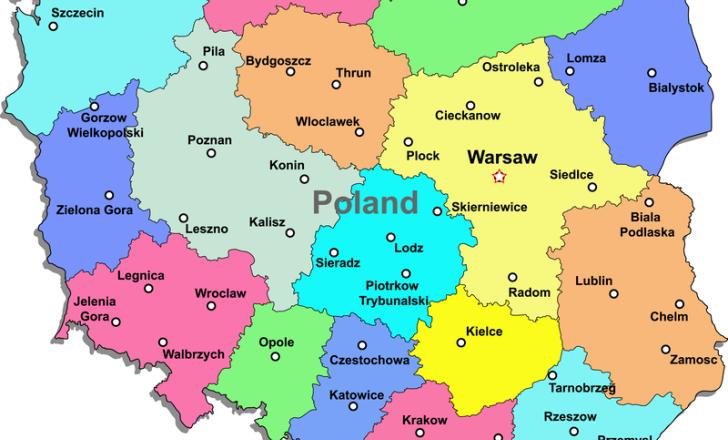
Astec celebrates its half century
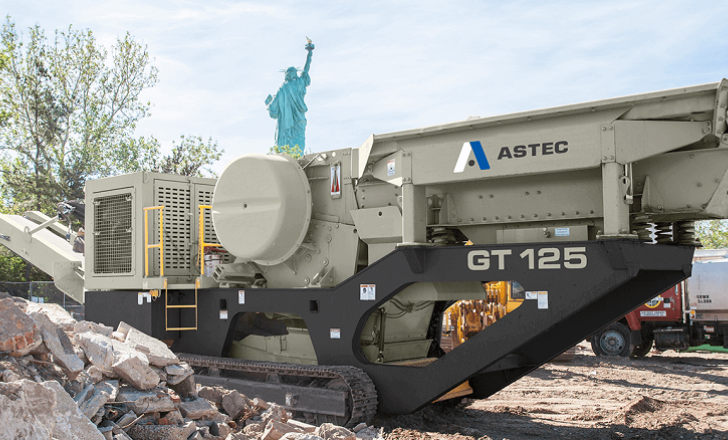
Concrete plant efficiency from Elba
The CBT 60 SL Elba is designed as a skip plant and can produce up to 60m³/hour of concrete. It is equipped with the proven CEM 1000 S Elba single-shaft mixer and an integrated linear bin for storing up to four aggregate components. Alternatively, it is possible to use the containerised linear bin CEL 25, where between two and eight aggregate components can be stored. The storage volume can range from 50-100m³.
The CBT 105-150 TB Elba is designed as a conveyor belt plant and meets customer needs for general construction sites and mixing tasks. It is said to be versatile and can be used for a wide range of duties. The plant has pre-installed assemblies that allow faster commissioning when it arrives onsite.
The plants are equipped with a proven Ammann Elba twin-shaft mixer. Feeding is via an inclined conveyor belt, and the aggregates are stored in the containerised linear bin with up to eight aggregate components and a volume of up to 100m³. A simple concrete slab is sufficient for the installation of the plant. In addition, a linear bin with up to 12 aggregate components and a volume of 210m³ can be used if the units are to be located semi-permanently.
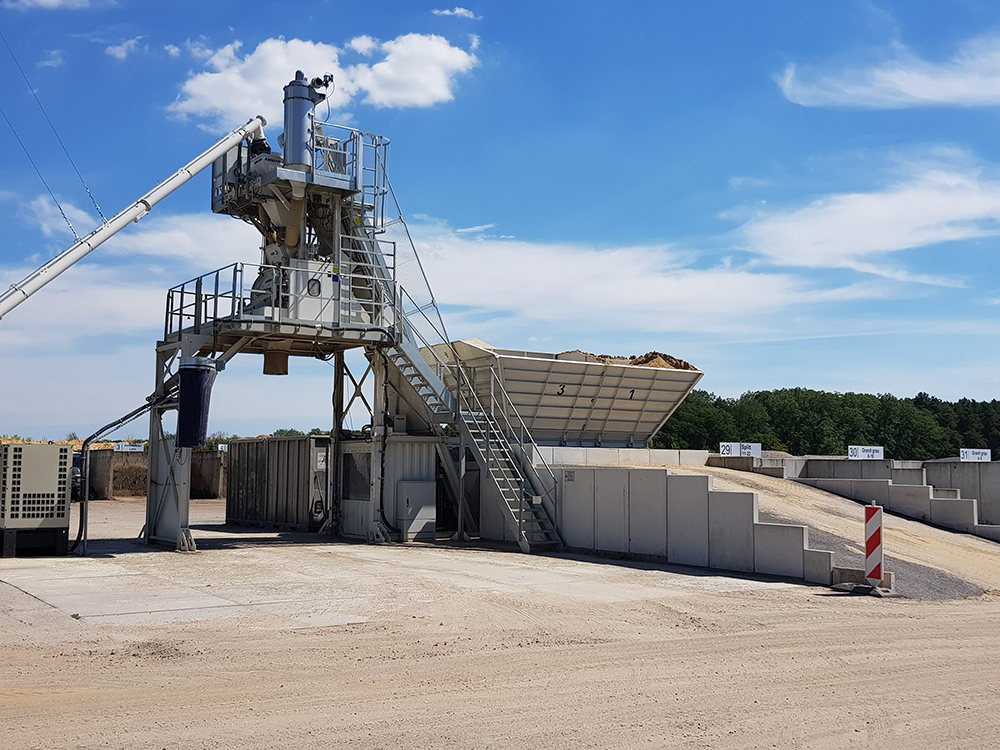
Slovakia tenders for Visnove IT systems
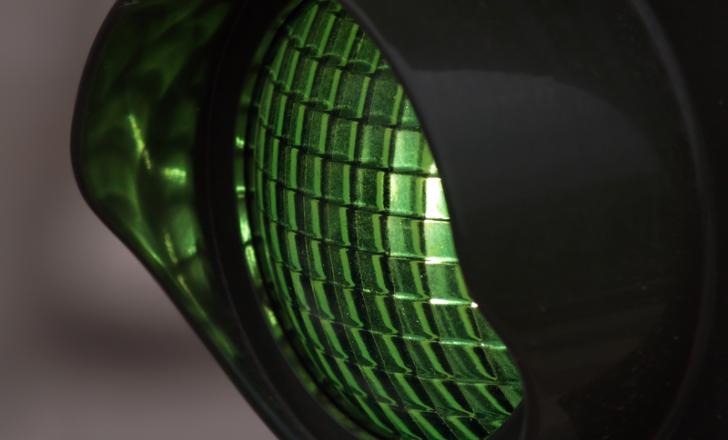
New generator power systems

Bolivian road development programme
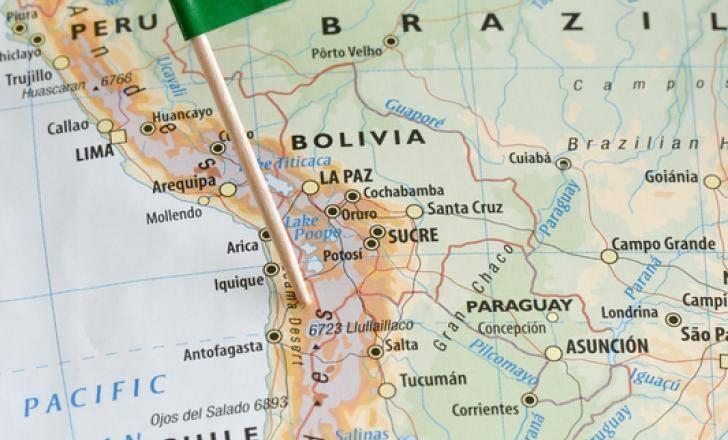
Nigerian road upgrade deals signed
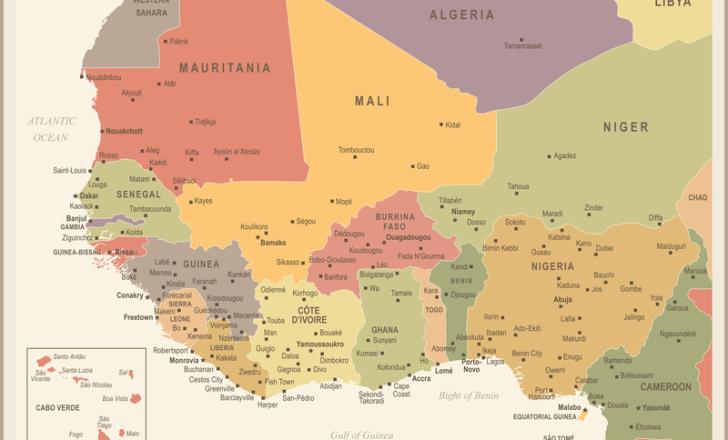
Topcon option for Cat machines

Milestone for RAP use in asphalt plants
One of the key features of the Marini Evo Dryer is the increased length of its dryer drum, allowing the plant to change the position of the RAP Introduction after the dryer flame and in turn providing plant operators with added versatility. As a result the aggregate heat exchange area stays constant, ensuring an efficient drying process.
In addition, to ensure the correct position of the flame inside the dryer drum a special long burner with internal protection is now available. This design means that the RAP introduction area is positioned after the flame, allowing a mixing area at the end of the cylinder, between the aggregates and the RAP. The design includes purpose-built mixing blades that reduce the stickiness of the RAP into the dryer drum.
The RAP can then be heated gradually, without being over-stressed by the high temperatures in the flame area. This allows the residual bitumen to be recuperated efficiently, without the risk of burning or drawbacks found with some conventional dryers such as high emissions and odour.
The Marini EvoDryer comes complete with another novel development, the new EvoDryer cylinder, which can be used to treat the fumes produced by the mixing tower in the discharge area of the mixer. A dedicated fan system sucks the diffused emissions produced by the mixer discharge. It also allows the management of the complete system and to convey emissions to the dryer discharge area behind the burner. A deflector inside the cylinder optimises the airflow emissions inside the drum, which are then flame-treated to burn off organic particles, reducing emissions and odours.
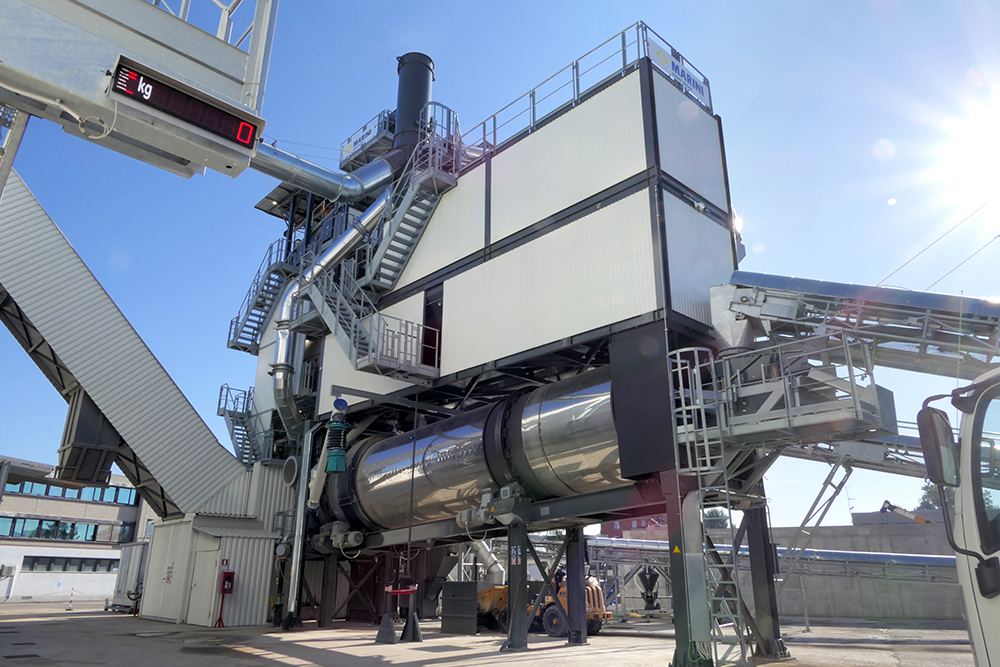
Hanging out with Pilosio’s Dynamo trailer
The standard version is 2.3m wide and 6.3m long, suitable for scaffolding pitches up to a maximum of 2.2m wide and up to 6.25m long. However, a Dynamo trailer is built according to the dimensions requested and can be customised according to the needs of the construction site and customer.
The trailer is also equipped with parking brakes on all wheels and can be towed by any vehicle on the site, even a forklift or van.
A variable counterweight is placed as needed under the chassis to set the weight of the scaffolding overhang.
Work areas can also be created below the road surface with any type of multidirectional scaffolding and pitch and, above all, with whatever geometry is needed to reach the extreme points on bridges, viaducts, and tunnels and generally any work to be served.
There is also a Dynamo Plus hydraulic model, only on request, that uses hydraulics for stabilsation expansion transverse displacement and alignment among other things.
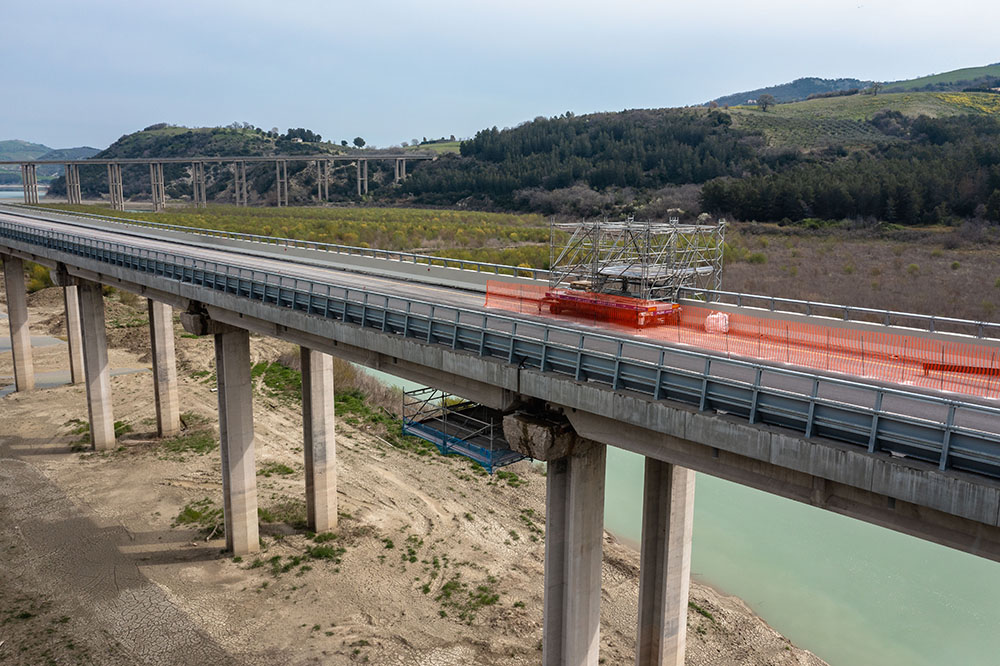
Works for Vietnam’s North-South Expressway approved
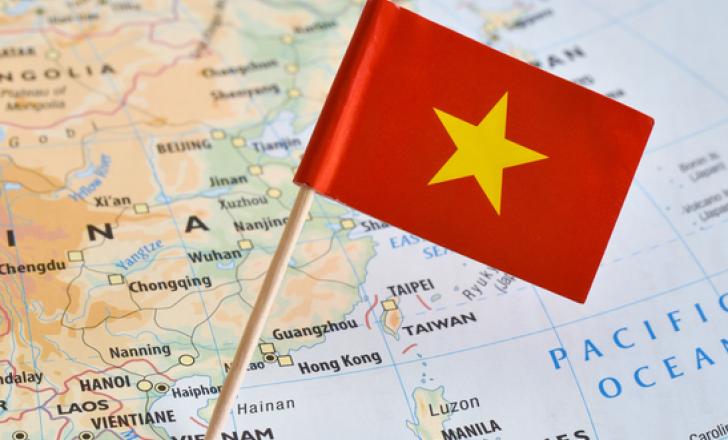
Productive pivot steer asphalt compactor
The touchscreen allows full control over functions. Touchscreen operation meets the need for digitalisation, though the rollers can also be operated using the rotary pushbutton on the control lever.
The operator can configure default settings and operate and control all functions using the touchscreen. A driver can set individual user profiles and switch to default settings. There is also a pre-set profile for the truck driver when loading the machine for transport.
High visibility allows the drivers to watch the drum surface and see if the spraying system is working correctly.
The BW 154 and BW 174 tandem rollers are available in several variants and with a wide range of equipment. They offer working widths of 1.5m or 1.68m and operating weights of 7.1tonnes and 9.8tonnes. Three compaction systems are offered: Asphalt Manager 2, vibration or the split drum oscillation TanGO4. The Asphalt Manager system has been simplified and regulates amplitude as well as compaction direction. This allows it to achieve optimum compaction quality with minimal passes.
The Asphalt Manager system allows the operator to concentrate on the rolling pattern and other machines working alongside, as well as being suited to compacting low-temperature asphalt.
Bomag offers optional extras including a second monitor at the rear of the cab for reversing, four additional mirrors on the cabin and rear frame, up to 16 LED lights, a chip spreader and a measuring technology interface for data transmission to the BOMAP app.
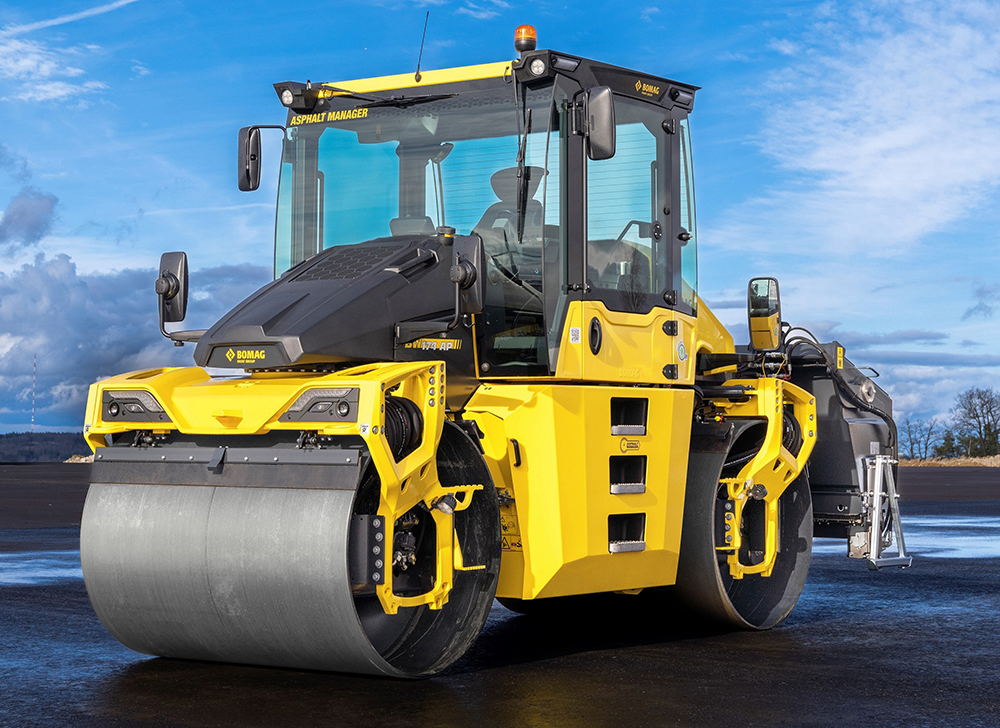
Profit boost for Rolls-Royce Power Systems
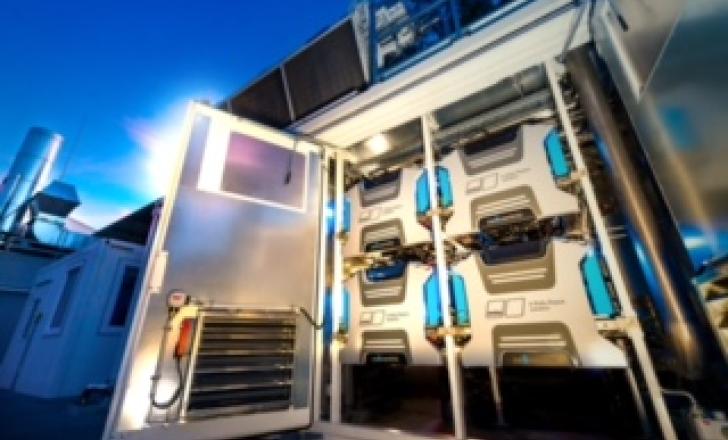
Bulgarian highway works to be carried out
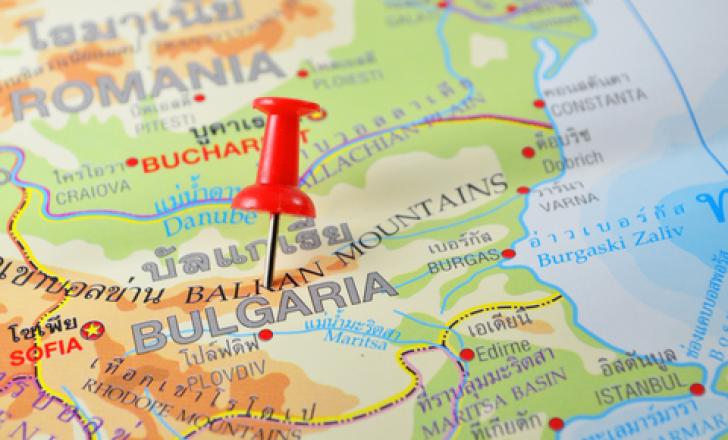
Flexibility with Mobiscreen MSS 802(i) EVO
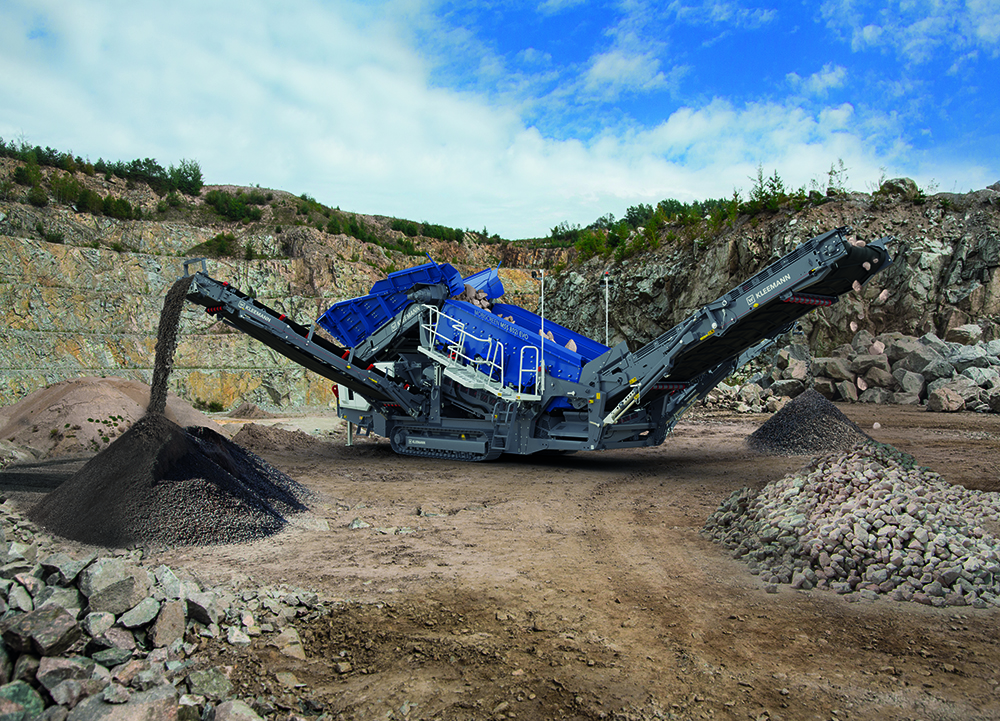
Efficient recycling system for asphalt plants
The firm recognises also that using up to 100% RAP in the feed is dependent on the availability of quality material as well as effective logistics with regard to its retrieval and storage. For applications where lower quantities of RAP are to be used in the feed, Ammann also offers the RAH50 and RAH60 dryers, which have maximum usage of 50% and 60% RAP, respectively. In addition, the firm offers the RAC system, which can handle up to 40% RAP in the feed.
All Ammann recycling systems are able to produce high-quality mix with 100% virgin aggregate if so desired.
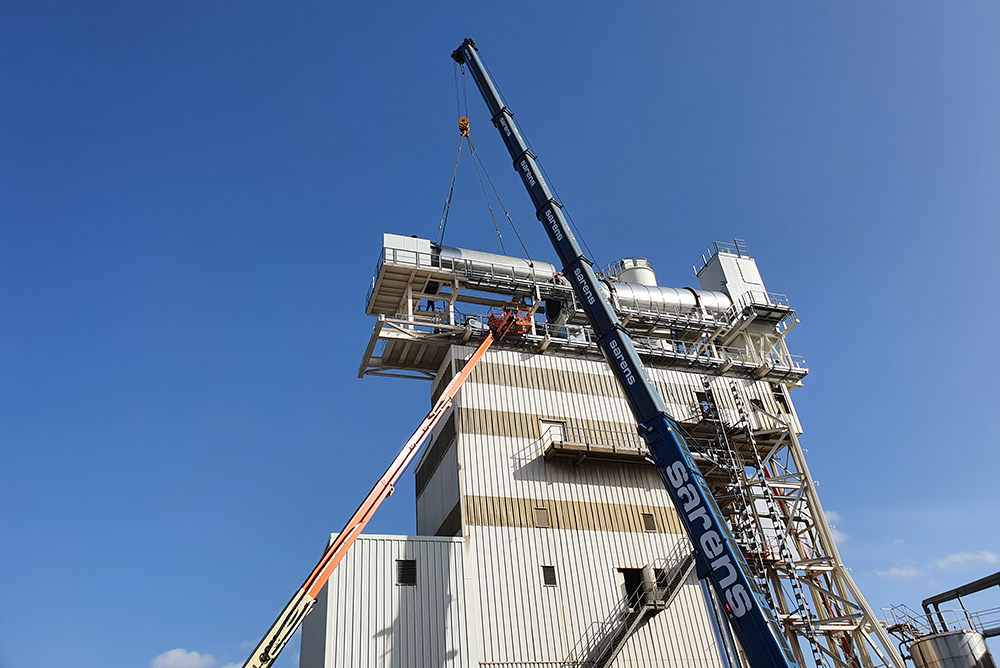
The environmental case for geosynthetics
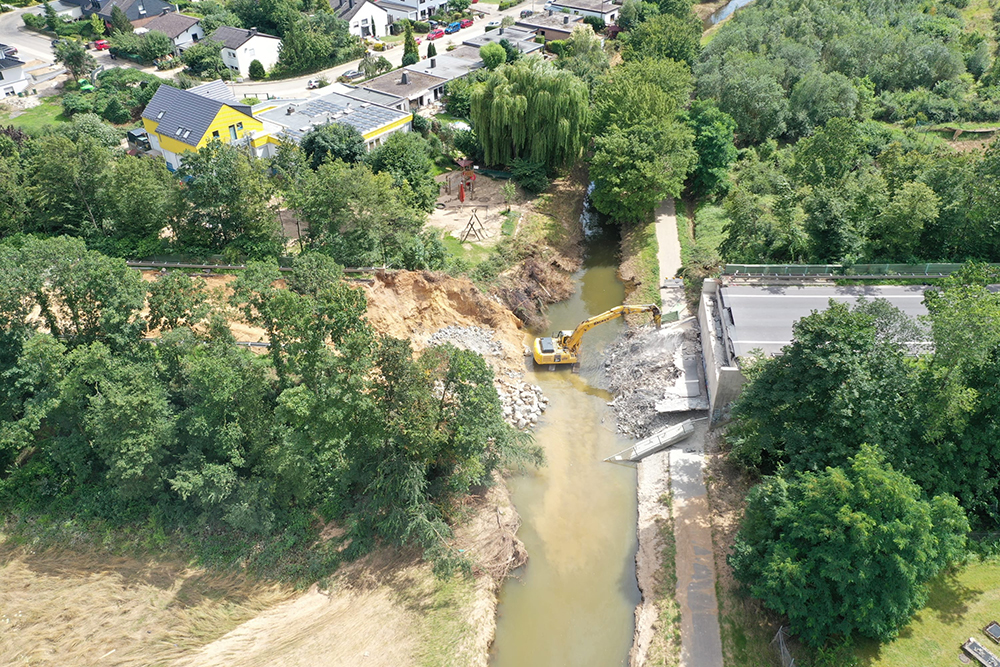