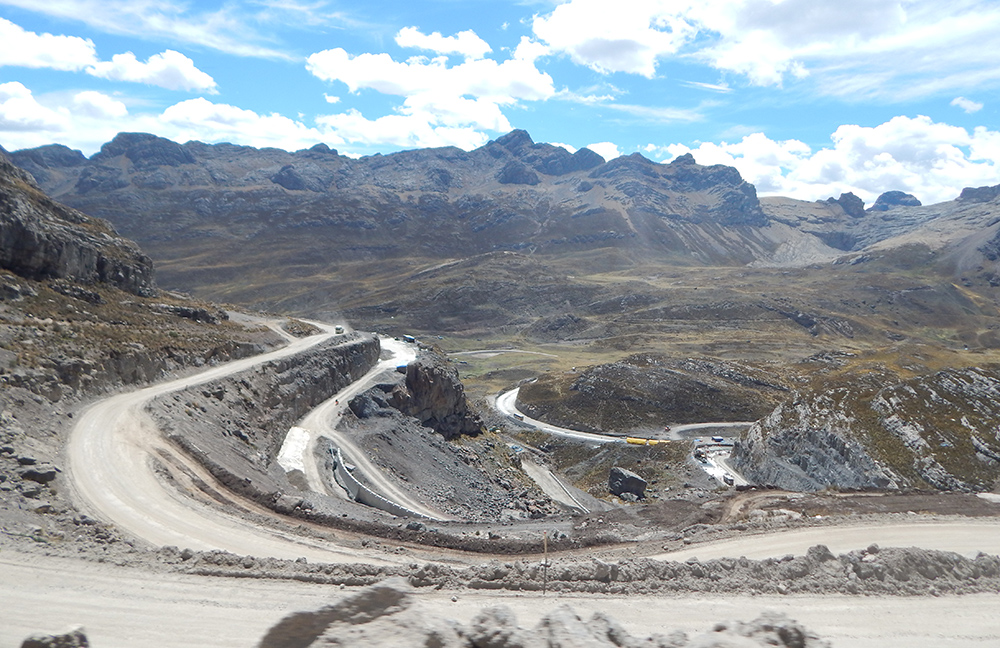
A major highway project in Peru is being carried out in a mountainous area of the country, presenting enormous technical challenges for the builders. However, the use of modern equipment is helping the construction team deliver the project efficiently.
The new Oyón-Ambo Highway is a landmark project for the country as this is the first large-scale road project in Perú to be built in concrete. The project presented a number of geographical challenges and the project team opted to use concrete to build the road, as this better suited the application than asphalt. The work has faced very difficult climatic conditions and high altitudes as well as a number of other technical challenges.
When it is complete, the Oyón-Ambo Highway will provide an alternative route to Peru’s existing Central Highway. The new route will help to reduce the time and cost of transporting goods, delivering a major economic benefit. When finished, it will benefit around 140,000 residents in the centre of the country as well as providing better access.
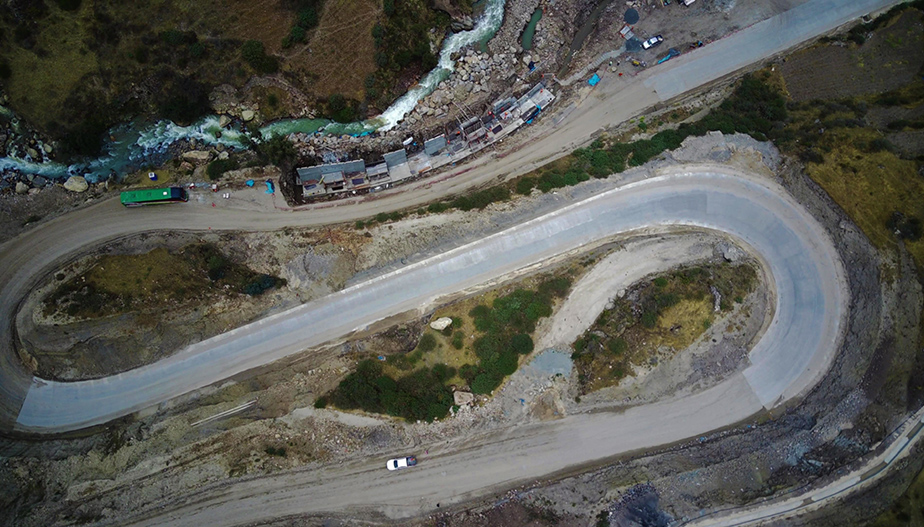
This road corridor measures nearly 150km and has been divided into three sections for its construction. The new route will improve traffic conditions and strengthen road integration in central Peru by connecting the coast with the highlands and the central jungle.
The start of the highway is located 250km from Peru’s capital, Lima. It runs from the province of Oyón at km 135 of the national road, an area that features a very rugged geography. This has made the construction project particularly challenging. In addition, widening the existing road link has required an earthmoving job of some 2 million m3, with blasting being carried out in some of the rocky areas. Working at altitude has presented a major challenge to the builders. Even the lowest point of the road, Oyón, is at a not insignificant 3,589m. Meanwhile, the other end of the road, Abra, is at an altitude of some 4,780m.
The high altitude of the road was one of the key reasons that the builders chose to construct the link using concrete. Previous asphalt road surfaces have fared poorly over time, with cracking caused by the freeze thaw process being a common problem. The use of concrete was preferred as this rigid pavement would cope better with the tough winter climate.
Road to the mountain
The 149.9km Oyón-Ambo road improvement project was divided into three sections for the work. Section 1 runs from Oyón - Desvío Cerro de Pasco/Oyón Branch and is 48.9km long, starting at km 134+98 and ending at km 181+00. Section 2 runs from the Cerro de Pasco - Chacayan Bypass/Chinche Bypass and is 49.02km long, starting at km 181+00 and ending at km 230+02. Meanwhile, Section 3 runs from the Chacayan - Ambo Bypass/Cochachinche Bypass and is 51.9km long, starting at km 230+02 and ending at km 281+92.

By December 2021, 27km of the 48.9km of Section 1 had been paved, some 55.2%. The paving work had to be halted due to the rainy season until April 2022. Similarly, by December 2021, some 19.43km of the 49.02km of Section 2 had been paved, around 39.6%. This work also had to wait until mid-April before the paving work could recommence, again due to the rainy season. Meanwhile, bidding is still being carried out for the 51.9km Section 3.
According to engineer Oscar Valdivia, special projects manager of UNICON Peru, “The project is being executed in the most difficult geographical conditions in the world.”
Valdivia said that the lowest part of the route is located in Oyón where the route begins and is at an altitude of 3,589m. He said that the road then rises until reaching Abra, the highest part of the project, some 4,780m above sea level. The altitude presents challenges, with temperatures during the day ranging between 13°C and 14°C and providing a working window that allows the concrete paving to be carried out to the required specification. However, Valdivia added, “During the night, temperatures can drop to -10.5°C with a heavy snowfall."
The logistics of the project have presented further challenges, with additives having to be transported 253km from Peru’s capital, Lima. Meanwhile, the cement used in the paving work is being transported 210km from the Andean cement factory belonging to the UNACEM group, located in the city of Tarma in Junín Department.
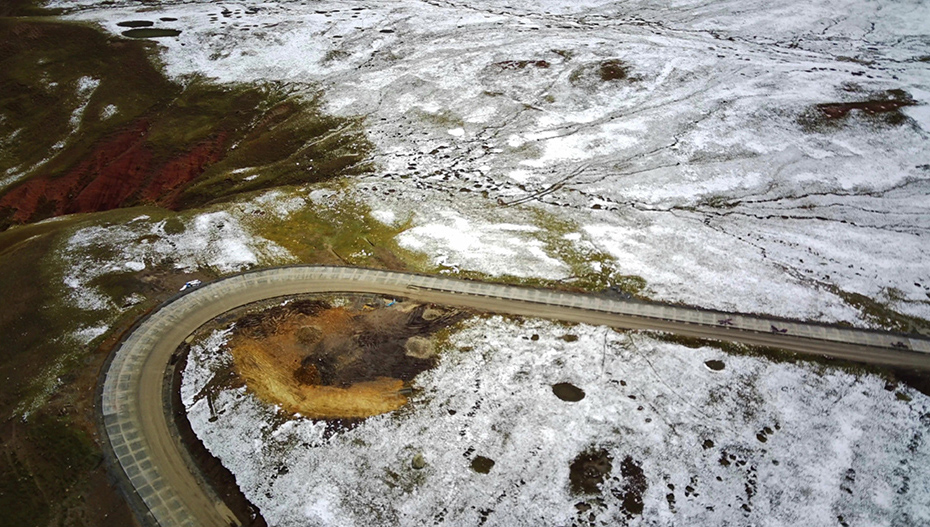
The high altitudes have provided difficulties for the construction crews, with working practices tailored to ensure safety for site personnel. Many Peruvian workers are used to working at altitudes and are familiar with the methods required. However, the high altitudes have also provided demands for the construction equipment. Machines operating at high altitudes often run hot, as there is less air for cooling. Many engines also lose power at altitude, typically over 2,500m, due to having less oxygen available to ensure efficient combustion. All the equipment used for the work has been used with care so as to prevent overheating, with performance also matched to the capacity limits of the high altitude.
Rigid pavement
The concrete for the Oyón-Ambo project was specified with a Modulus of 45kg/cm² and a minimum cement content of 300kg/m³,
50mm slump. The concrete has been transported in dump trucks and has been laid using conventional slipform paving equipment. However, concrete with 75mm of slump has had to be transported to the site using mixer trucks. This material has been used for manually placed pavements, being placed with a vibratory screed.
Valdivia explained, “The technical specification of the project not only required the evaluation of the concrete, but also demanded the verification of the strength of the concrete in the finished pavement through diamond cores and had to reach a resistance of 350kg/cm². This made the requirement more demanding.”
A number of considerations had to be taken into account to meet the project specifications in the mix design and to counteract the climatic conditions of the project area.
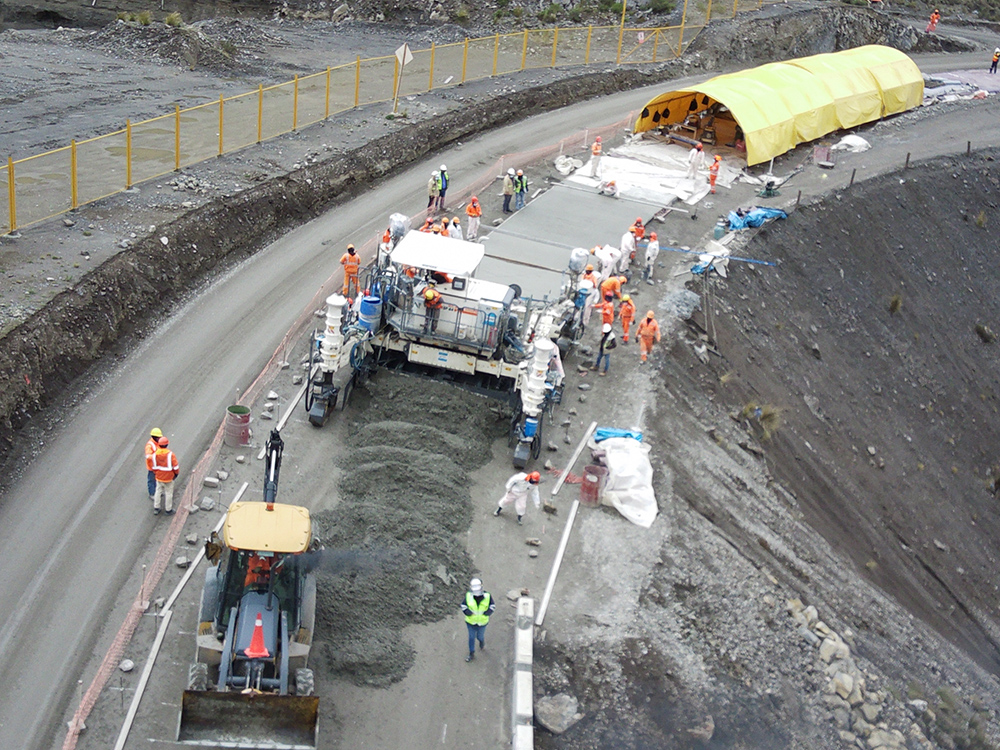
The Shilstone method is a recommended practice for laying rigid pavements with a slipform paver, which allows the mix to be optimised using coarseness factor, mortar factor, and aggregate particle distribution.
Using the Shilstone method delivered a mix with better workability, reduced segregation potential and a final concrete strength higher than specified. "This method allowed us to have a mixture with better permeability, less thermal shrinkage and a reduction in the shrinkage,” according to Valdivia.
An air additive has been incorporated, which generates micro-bubbles that are uniformly distributed in the concrete mass. This is used to break the capillarity of the concrete and improve waterproofing. The use of the additive was important to address potential issues from the freeze/thaw effect. This admixture improved workability at the time of placement, avoiding segregation in transport.
A plasticising admixture has been employed that offers a high controlled setting range and also allows rapid development of initial strength. In addition, this provides fluidity for longer times, compatible with the use of air-entraining admixtures. The use of water heaters has also helped the concrete construction process, providing temperatures at least 13°C in the material.
Technical difficulties
The design of Section 1 was a task that UNICON was in charge of and the firm was able to evaluate the chosen parameters for the rigid pavement utilising the Shilstone method. "The methodology has allowed us to improve the proportions of the aggregates, and in this case we have considered an intermediate material, which is stone or gravel," commented Valdivia.
Delivering the project has required extensive widening works along the existing alignment to help improve the road for drivers. The use of blasting has been required in the rocky areas, while there has also been a need for backfilling as well as the construction of structural retaining walls.
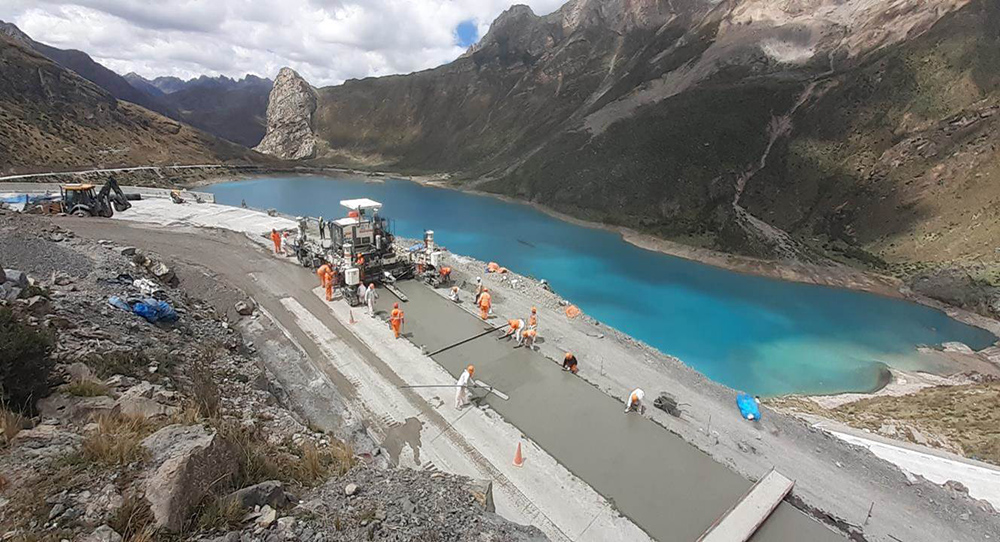
Although the alignment does not require the construction of bridges and tunnels, it has required large number of culverts to be constructed.
Removal of the 2million m3 of material is including blasting in the rocky mountain areas to allow the existing road to be widened.
The geography along the alignment has also demanded the construction of large structural retaining walls throughout the entire project. This has been a particular issue for the section closest to Abra.
Four pavers have been used so far, three in Section 1 and one in Section 2. All of the slipform pavers employed have been Wirtgen SP-64 models, equipped with DBI and TBI units.
In Section 1 there are two ready-mix concrete manufacturing plants in operation. One of the units is an ODISA model capable of producing 100m³/h and featuring a 9m³ REXCON mixer. The other concrete plant is a ROSS unit capable of producing 60m³/h and featuring a 3m³ SICOMA mixer.
Varying terrain
Peru is a country with extremes of terrain. Its mountains form part of the Andes range, with the highest mountain being Huascarán, with its peak at 6,768m above sea level. The country has borders with Chile in the south, as well as Bolivia, Brazil to the east and Colombia and Ecuador to the north. In the west Peru has large plains while there are rainforests in the east. With mountain ranges and rainforest areas, Peru’s climate varies considerably. Rainfall is frequent in summer in the mountain region, which presents challenges for construction operations.

Although it is a democracy, the country has a tangled political history and a number of prominent leaders have been accused of corruption, with one former president still serving a lengthy prison sentence.
The country’s economy has been growing and inflation has been low while the inhabitants have an above average lifespan according to the World Health Organisation. But a significant percentage of its population have remained poor, despite attempts to improve the lives of its people by various governments. Mining of gold, copper and zinc have been key industries for Peru and the country's main trading partners include the US and China, as well as its neighbours Brazil and Chile.