Work is progressing on a £320 million (e385 million) project to upgrade a busy 18km stretch of the main A80 Glasgow-Stirling road in Scotland to motorway standard. The project, between the villages of Stepps and Haggs, is part of a massive infrastructure investment in Scotland's transport network, and construction work includes almost 8km of new dual-lane motorway and hard shoulders between
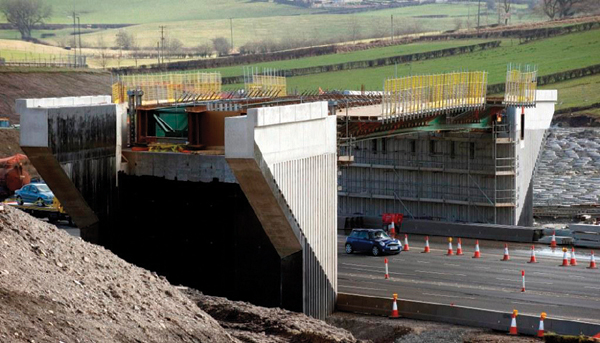
Harsco Infrastructure is playing a vital role providing specialist systems for the A80 upgrade in Scotland
Work is progressing on a £320 million (e385 million) project to upgrade a busy 18km stretch of the main A80 Glasgow-Stirling road in Scotland to motorway standard.
The project, between the villages of Stepps and Haggs, is part of a massive infrastructure investment in Scotland's transport network, and construction work includes almost 8km of new dual-lane motorway and hard shoulders between; 2.7km of the existing A80 road upgraded to three-lane motorway; and almost 7.3km of the existing A80 upgraded to dual-lane motorway with hard shoulders and climbing lanes.
Work on the project has required extensive demolition and reconstruction on existing structures along the route, including the widening of existing bridges and construction of new ones. This is complicated because as a vital arterial route across Scotland's most densely populated region, the road must remain in use throughout the construction period.
1483 Harsco Infrastructure is playing a vital role providing specialist access, formwork and falsework systems.
Concrete and civil engineering specialist2805 T Mac Construction is carrying out all the on-line work, constructing new bridges and extensions to existing bridges on the main route, some 16 structures.
T-Mac was awarded the subcontract via a traditional competitive tender process and part of its winning bid was a methodology developed in partnership with Harsco Infrastructure, to minimise disruption on the A80 by closing off the hard shoulder and slow lane.
The work requires a varied approach to access and formwork. This not only entails considerable health and safety risk, but also imposes significant logistical and design problems. The safety challenges have been met by using Harsco Infrastructure's equipment to create an enclosed working area to isolate the workforce from the traffic, which presents challenges as space within the route is limited.
"We are utilising a variety of systems from our portfolio to offer workable and time saving solutions" says David Hancock, sales manager for Harsco Infrastructure.
CUPLOK and MkII Soldier Falsework components are used to create a safe hydrodemolition deck under each bridge which serves as a working platform, as well as access for steel-fixing operatives before the introduction of falsework for the new in situ concrete.
"Essentially, the work involves hydrodemolition to break out existing concrete to expose the steel reinforcement before erecting formwork, stitching in the new rebar and casting the bridge extensions," explains T-Mac managing director Mike Traynor.
The newly-widened carriageways, the existing bridge cantilevers and RC bridge beams are partially demolished and new ones cast. The bridge cantilevers are then extended at either side of the decks and new parapets formed. The central sections of the carriageway are also being strengthened by casting new in situ concrete beams and in situ soffits.
"We planned this project for months in conjunction with the main contractor and sub-contractor to ensure the correct solutions for each individual structure. This included the use of our MULTIFORM parapet brackets, for on-line as well as off-line bridge structures," said Hancock.
T-Mac also used the TOPEC soffit panel system supported by modular aluminium GASS legs for the soffit stages on the existing structures reinstatement, due to extremely restricted work space on these structures.
"TOPEC allows the contractor to fit large soffit areas of completed falsework by simply lifting the aluminium panels into place because they are lightweight. Traditional falsework solutions would have required prolonged work in a confined space for both erecting and striking the system," said Hancock.
The original plan was to complete all the extension work on the southern (westbound) carriageway, then switch to the northern (eastbound) side and then travel back to Haggs, carrying out bridge strengthening work along the central reserve. However, the need to adapt to unforeseen circumstances has resulted in a flexible working regime and the methodology has altered slightly.
"This project has demanded the highest possible level of planning, engineering, design and logistics. In January 2010 we had the worst winter weather for several years, with record low temperatures and heavy snow but although the project suffered delays, the contractors have managed to adapt to the conditions and the final completion date has not been affected. The meticulous planning has paid off," Hancock added.
The project, between the villages of Stepps and Haggs, is part of a massive infrastructure investment in Scotland's transport network, and construction work includes almost 8km of new dual-lane motorway and hard shoulders between; 2.7km of the existing A80 road upgraded to three-lane motorway; and almost 7.3km of the existing A80 upgraded to dual-lane motorway with hard shoulders and climbing lanes.
Work on the project has required extensive demolition and reconstruction on existing structures along the route, including the widening of existing bridges and construction of new ones. This is complicated because as a vital arterial route across Scotland's most densely populated region, the road must remain in use throughout the construction period.
Concrete and civil engineering specialist
T-Mac was awarded the subcontract via a traditional competitive tender process and part of its winning bid was a methodology developed in partnership with Harsco Infrastructure, to minimise disruption on the A80 by closing off the hard shoulder and slow lane.
The work requires a varied approach to access and formwork. This not only entails considerable health and safety risk, but also imposes significant logistical and design problems. The safety challenges have been met by using Harsco Infrastructure's equipment to create an enclosed working area to isolate the workforce from the traffic, which presents challenges as space within the route is limited.
"We are utilising a variety of systems from our portfolio to offer workable and time saving solutions" says David Hancock, sales manager for Harsco Infrastructure.
CUPLOK and MkII Soldier Falsework components are used to create a safe hydrodemolition deck under each bridge which serves as a working platform, as well as access for steel-fixing operatives before the introduction of falsework for the new in situ concrete.
"Essentially, the work involves hydrodemolition to break out existing concrete to expose the steel reinforcement before erecting formwork, stitching in the new rebar and casting the bridge extensions," explains T-Mac managing director Mike Traynor.
The newly-widened carriageways, the existing bridge cantilevers and RC bridge beams are partially demolished and new ones cast. The bridge cantilevers are then extended at either side of the decks and new parapets formed. The central sections of the carriageway are also being strengthened by casting new in situ concrete beams and in situ soffits.
"We planned this project for months in conjunction with the main contractor and sub-contractor to ensure the correct solutions for each individual structure. This included the use of our MULTIFORM parapet brackets, for on-line as well as off-line bridge structures," said Hancock.
T-Mac also used the TOPEC soffit panel system supported by modular aluminium GASS legs for the soffit stages on the existing structures reinstatement, due to extremely restricted work space on these structures.
"TOPEC allows the contractor to fit large soffit areas of completed falsework by simply lifting the aluminium panels into place because they are lightweight. Traditional falsework solutions would have required prolonged work in a confined space for both erecting and striking the system," said Hancock.
The original plan was to complete all the extension work on the southern (westbound) carriageway, then switch to the northern (eastbound) side and then travel back to Haggs, carrying out bridge strengthening work along the central reserve. However, the need to adapt to unforeseen circumstances has resulted in a flexible working regime and the methodology has altered slightly.
"This project has demanded the highest possible level of planning, engineering, design and logistics. In January 2010 we had the worst winter weather for several years, with record low temperatures and heavy snow but although the project suffered delays, the contractors have managed to adapt to the conditions and the final completion date has not been affected. The meticulous planning has paid off," Hancock added.