A series of formwork developments are helping with challenging bridge construction projects around the world - Mike Woof writes
In the Polish city of Krakow, a cost-effective cable stayed bridge is being constructed using a balanced cantilever technique. The current expansion of the Krakow metropolitan railway network (KST) requires the building of a crossing of the Krakow-Plaszow railway junction. Ensuring that daily rail operations remained unaffected during the construction of the 252m long crossing w
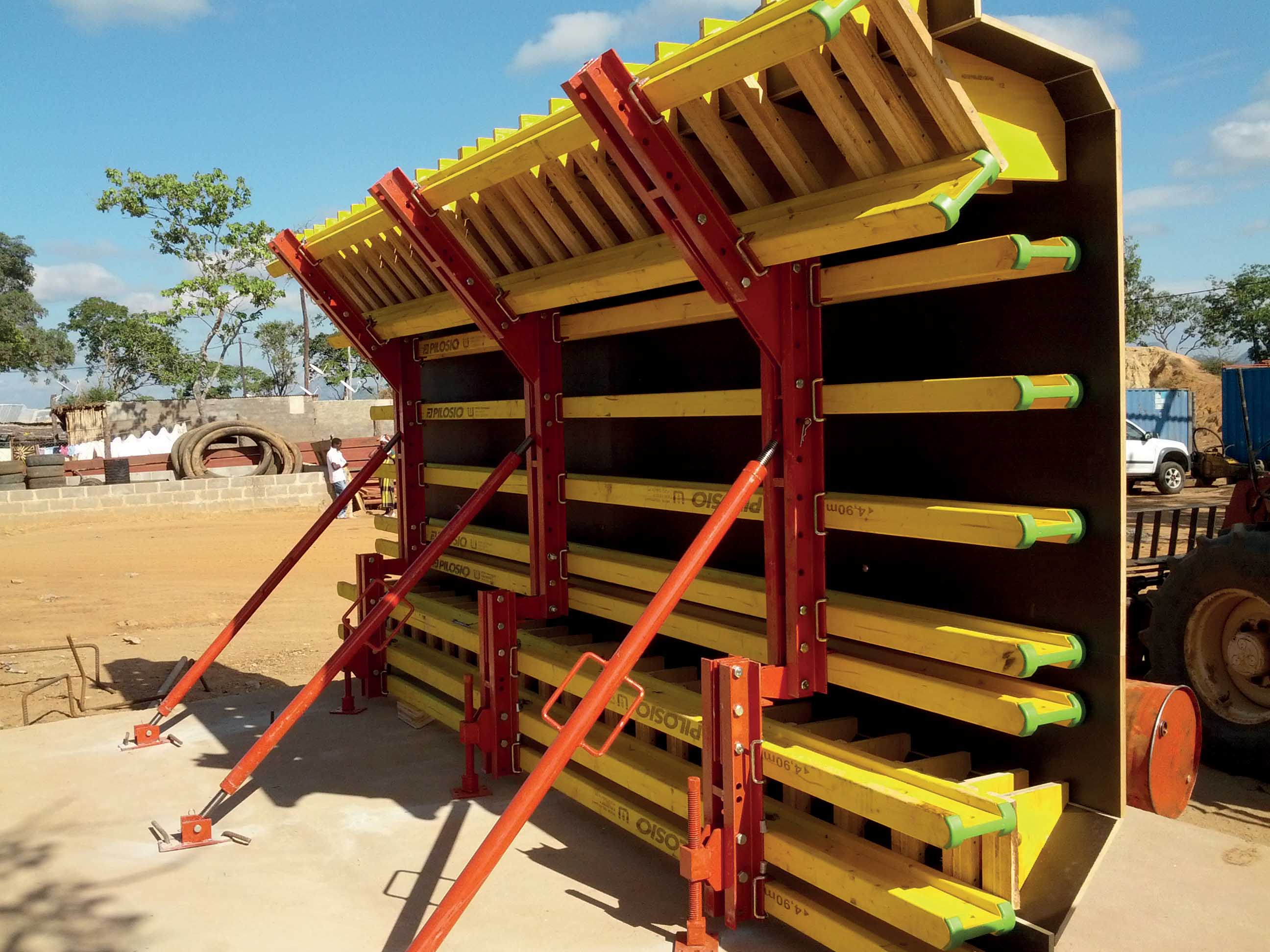
The Pilosio MAXIMIX system is used to carry the main bridge girders
A series of formwork developments are helping with challenging bridge construction projects around the world - Mike Woof writes
In the Polish city of Kraków, a cost-effective cable-stayed bridge is being constructed using a balanced cantilever technique. The current expansion of the Kraków metropolitan railway network (KST) requires the building of a crossing of the Kraków-Plaszów railway junction. Ensuring that daily rail operations remained unaffected during the construction of the 252m long crossing was crucial, however.
This led the contractor to decide in favour of the cantilevered construction method to deliver the extradosed bridge with its hollow box cross-section. In addition, the compatibility with the298 PERI UP modular scaffolding provided safe working platforms and access means to all working areas.
Using a customised solution devised by PERI engineers, the construction team has provided 5.7m long concrete sections using 4 VARIOKIT cantilevered construction carriages. The versatility of the system has aided with the complicated pre-tensioning sequences. As a result, these have been carried out in the longitudinal and transverse directions of the viaduct.
A further challenge came from the tendons, as well as the anchorage points of the stay cables outside of the box girders. In addition, carrying out construction work during daily train operations along with the allocated downtimes complicated the completion of the cantilever above the tracks.
After closing the gap of the bridge span, the PERI VBC balanced cantilevered carriage automatically returns to its starting position, although cable stays are positioned along the structural axis. As a result, dismantling the equipment is said to be efficient and safe.
PERI Poland took on the project planning and static calculations of the comprehensive solutions for the superstructure on PERI UP falsework as well as the cantilevered construction. The systems and processes were well matched and allowed on-time completion. Cooperation between the contractor, planners and PERI engineers allowed the shape of the reinforcing ribs along the bridge superstructure to be optimised during the planning phase, cutting construction time. The biggest challenge for the formwork planning proved to be dealing with the asymmetric shape of the superstructure cross-section, as well as its varying width along the structural axis.
Fast implementation has been achieved due to the availability of extensive technical documentation. Detailed preparation work was carried out using sophisticated 3D formwork planning tools, further easing the process. This detailed visualisation has achieved cost-effective and efficient on-site forming operations.
7163 Pilosio meanwhile is developing its presence in Africa and in Southern Africa in particular. The firm has been active with projects in Mozambique as well as South Africa.
Pilosio is working closely on a major infrastructure project in the South African city of Durban, the Mount Edgecombe Interchange junction, which includes two of the longest bridges in the country. This project is being handled by CMC Africa Austral, part of CMC, with which Pilosio has worked on other construction jobs. As the Durban project is proving successful, CMC again opted to work with Pilosio for a job in Mozambique. The Italian formwork specialist is supplying provisional solutions for the construction of a viaduct to connect the cities of Marrupa and Litunde.
The viaduct project forms part of a larger development programme for transport links and infrastructure in the country. This involves the construction of a section of road consisting of a viaduct with seven spans going through the savannah, which will improve accessibility to the city of Lichinga.
The client opted to use Pilosio’s MAXIMIX system for the casting of the decks and for two different shoring systems. Meanwhile, Piliosio’s SIMPLEX towers and MP heavy-duty towers were selected for the portals, optimising the construction site's requirements.
The MAXIMIX formwork system using wooden beams was selected by the client to construct the T-type girders, which are 2.4m tall and built using self-compacting concrete. These girders are crucial to the project, as they carry the road deck itself. The MAXIMIX system allows the construction of large-sized panels and geometrical shapes of any type and with high capacity and limited weight. This versatility is important for the bridge project. The MAXIMIX is highly suitable for large-scale infrastructure work, where large surface modules can be assembled on-site, maximising productivity on-site. In particular, the system can be designed to deal with very high fresh cement pressures. Meanwhile, by varying the distance between the PL20 wooden beams and steel beams, the scale of the module can be adapted to the needs of the project. In this application, it is easier to reach the construction site and handle a system with wooden beams rather than with other systems in steel.
For the support system the SIMPLEX tables with an average height of 5.8m were selected, providing a capacity of 200kN/tower. Among the Pilosio shoring systems, this is said to be highly suitable for applications where the soil is fairly even. SIMPLEX provides a rapid table system for in-situ casting of concrete slabs. The firm said that this is well-suited for high structures as well as major loads, when constructing key infrastructure (as well as large buildings). The table handling device is also said to be easy to use as it requires only two operators and allows setting up and stripping work to be done simply and quickly.
The heavy-duty towers, made with the MP multidirectional system, were used for this job to support the heavy girder. This has been specifically designed for making underpasses that allow the passage of existing roads and waterways. In this project the height of the towers is 4.8m. Each vertical element of the high-capacity MP HD Towers consists of four MP uprights connected to one another by a lower and upper frame: each column providing a capacity of 200kN, equivalent to 800kN/tower.
Work is progressing well on the project and, when complete, the structure will provide an important new traffic link that will help develop trade and transportation in this area of Mozambique.
Specialist sub-contractors China Civil Engineering and Construction Corporation (CCECC) and Structcon have been using a wide range of319 RMD Kwikform formwork and shoring solutions on the extensive construction works, required for the $1 billion Sharjah Ring Road in the United Arab Emirates (UAE).
Working for Al Rajhi Construction, CCECC and Structcon have been tasked with the construction of five new bridges, 1,030m long in total, which forms part of the National Paints roundabout development. RMD Kwikform have designed the solutions and provided the equipment for the construction of the decks, abutments and piers for each of the five elevated bridge structures, which reached up to a height of 19m.
The new National Paints roundabout is part of Sharjah’s wider investment in road infrastructure, catering for the commercial and population growth within the region. With a local base in Sharjah, RMD Kwikform engineers were able to support the entire project, providing technical designs and site assistance during each construction phase.
In order to support the height, curvature and size of the bridge decks, which ranged from 12.6 to 27m wide, RMD Kwikform supplied its 80kN modular Rapidshor shoring, Superslim Soldiers and GTX Beams. With the project being constructed over existing main roads that needed to remain open, one of the main challenges was to create a gantry system that would safely span these vital transport links.
The gantry system also had to be strong enough to support the construction of the elevated bridge deck above, including the additional formwork required to cast the deck cells in-situ. It was here that the engineering team at RMD Kwikform had to come up with a flexible and cost-effective solution to cater for the loading, the connection of the formwork and the camber of the deck sections above.
To achieve this, a solution incorporating six different product components was designed. Alform beams were used on top of the Gantry beam with a B clamp, combined with suitable timber packing used to create the right angle for the bridge deck. Above the clamp and packing section, a Kwikstage socket base was mounted and used to support a Rapidshor U head. This, in turn, allowed for steel Superslim Soldiers to be supported as primary soffit beams, before GTX secondary timber beams were then mounted above.
Commenting on this challenge and the wider project, Chris Jardine, UAE general manager from RMD Kwikform, said, “When we looked at the gantry section, we realised that it was going to be quite complicated to achieve in the available budget. The key to keeping costs down was to ensure we had no special items that would need to be fabricated; we had to provide a solution that would support the 12 standard 10m long standard gantry beams successfully. By achieving this, we ensured the customer had no additional gantry beam fabrication costs.
“In order to meet the curvature and weight challenges of the structure above the gantry, we needed to come up with a flexible yet robust support solution that ensured the safety of the site team, and the traffic flow underneath the bridge. By modelling this in our local Sharjah office, we were able to use standard components from our fleet to construct what was a simple and cost-effective solution.
“Similarly, when it came to supporting the main bridge deck construction, next to the existing carriageways, we were able to work with the site team to model the Rapidshor solution required for the varying curves of the structures.”
With the height of the elevated bridge decks reaching up to 19m tall, RMD Kwikform engineers had to calculate the complex forces involved in the design of the Rapidshor birdcage-style shoring solution. This included taking into account the impact that high winds would have on the equipment and overall solution.
This process started at ground level, with a plan developed to support simpler erection with the casting of concrete pads, which allowed for the secure mounting of the base plate for the Rapidshor legs. The erection team was then able to construct the Rapidshor towers, using bracing to link them together.
Finer refinements were then made possible by using the adjustable top jack and U Heads at the top of the Rapidshor shoring, allowing the solution to accommodate the sloping gradient of the bridge deck, from 455mm on one side to 96mm on the next. As the 19m high towers were braced together, the site team cast the cells in-situ using RMD Kwikform shoring to create the voids within the deck sections, providing the most cost-effective bridge design.
Chris Jardine said, “This was a very complex project carried out in a very busy location; it was important that we got the site support right. So not to impact the tight programme time, we trained the erection teams and also ensured our equipment was delivered efficiently, in order to maintain the highest levels of safety. Our design team provided cost-effective, reliable and practical solutions for the varying depth of bridge decks, with curved shape and gantry systems. The project itself really took advantage of the flexibility of our Rapidshor system, and the skills of the erection teams made a noticeable difference to the completion of the concrete works.”
In the Polish city of Kraków, a cost-effective cable-stayed bridge is being constructed using a balanced cantilever technique. The current expansion of the Kraków metropolitan railway network (KST) requires the building of a crossing of the Kraków-Plaszów railway junction. Ensuring that daily rail operations remained unaffected during the construction of the 252m long crossing was crucial, however.
This led the contractor to decide in favour of the cantilevered construction method to deliver the extradosed bridge with its hollow box cross-section. In addition, the compatibility with the
Using a customised solution devised by PERI engineers, the construction team has provided 5.7m long concrete sections using 4 VARIOKIT cantilevered construction carriages. The versatility of the system has aided with the complicated pre-tensioning sequences. As a result, these have been carried out in the longitudinal and transverse directions of the viaduct.
A further challenge came from the tendons, as well as the anchorage points of the stay cables outside of the box girders. In addition, carrying out construction work during daily train operations along with the allocated downtimes complicated the completion of the cantilever above the tracks.
After closing the gap of the bridge span, the PERI VBC balanced cantilevered carriage automatically returns to its starting position, although cable stays are positioned along the structural axis. As a result, dismantling the equipment is said to be efficient and safe.
PERI Poland took on the project planning and static calculations of the comprehensive solutions for the superstructure on PERI UP falsework as well as the cantilevered construction. The systems and processes were well matched and allowed on-time completion. Cooperation between the contractor, planners and PERI engineers allowed the shape of the reinforcing ribs along the bridge superstructure to be optimised during the planning phase, cutting construction time. The biggest challenge for the formwork planning proved to be dealing with the asymmetric shape of the superstructure cross-section, as well as its varying width along the structural axis.
Fast implementation has been achieved due to the availability of extensive technical documentation. Detailed preparation work was carried out using sophisticated 3D formwork planning tools, further easing the process. This detailed visualisation has achieved cost-effective and efficient on-site forming operations.
Pilosio is working closely on a major infrastructure project in the South African city of Durban, the Mount Edgecombe Interchange junction, which includes two of the longest bridges in the country. This project is being handled by CMC Africa Austral, part of CMC, with which Pilosio has worked on other construction jobs. As the Durban project is proving successful, CMC again opted to work with Pilosio for a job in Mozambique. The Italian formwork specialist is supplying provisional solutions for the construction of a viaduct to connect the cities of Marrupa and Litunde.
The viaduct project forms part of a larger development programme for transport links and infrastructure in the country. This involves the construction of a section of road consisting of a viaduct with seven spans going through the savannah, which will improve accessibility to the city of Lichinga.
The client opted to use Pilosio’s MAXIMIX system for the casting of the decks and for two different shoring systems. Meanwhile, Piliosio’s SIMPLEX towers and MP heavy-duty towers were selected for the portals, optimising the construction site's requirements.
The MAXIMIX formwork system using wooden beams was selected by the client to construct the T-type girders, which are 2.4m tall and built using self-compacting concrete. These girders are crucial to the project, as they carry the road deck itself. The MAXIMIX system allows the construction of large-sized panels and geometrical shapes of any type and with high capacity and limited weight. This versatility is important for the bridge project. The MAXIMIX is highly suitable for large-scale infrastructure work, where large surface modules can be assembled on-site, maximising productivity on-site. In particular, the system can be designed to deal with very high fresh cement pressures. Meanwhile, by varying the distance between the PL20 wooden beams and steel beams, the scale of the module can be adapted to the needs of the project. In this application, it is easier to reach the construction site and handle a system with wooden beams rather than with other systems in steel.
For the support system the SIMPLEX tables with an average height of 5.8m were selected, providing a capacity of 200kN/tower. Among the Pilosio shoring systems, this is said to be highly suitable for applications where the soil is fairly even. SIMPLEX provides a rapid table system for in-situ casting of concrete slabs. The firm said that this is well-suited for high structures as well as major loads, when constructing key infrastructure (as well as large buildings). The table handling device is also said to be easy to use as it requires only two operators and allows setting up and stripping work to be done simply and quickly.
The heavy-duty towers, made with the MP multidirectional system, were used for this job to support the heavy girder. This has been specifically designed for making underpasses that allow the passage of existing roads and waterways. In this project the height of the towers is 4.8m. Each vertical element of the high-capacity MP HD Towers consists of four MP uprights connected to one another by a lower and upper frame: each column providing a capacity of 200kN, equivalent to 800kN/tower.
Work is progressing well on the project and, when complete, the structure will provide an important new traffic link that will help develop trade and transportation in this area of Mozambique.
Specialist sub-contractors China Civil Engineering and Construction Corporation (CCECC) and Structcon have been using a wide range of
Working for Al Rajhi Construction, CCECC and Structcon have been tasked with the construction of five new bridges, 1,030m long in total, which forms part of the National Paints roundabout development. RMD Kwikform have designed the solutions and provided the equipment for the construction of the decks, abutments and piers for each of the five elevated bridge structures, which reached up to a height of 19m.
The new National Paints roundabout is part of Sharjah’s wider investment in road infrastructure, catering for the commercial and population growth within the region. With a local base in Sharjah, RMD Kwikform engineers were able to support the entire project, providing technical designs and site assistance during each construction phase.
In order to support the height, curvature and size of the bridge decks, which ranged from 12.6 to 27m wide, RMD Kwikform supplied its 80kN modular Rapidshor shoring, Superslim Soldiers and GTX Beams. With the project being constructed over existing main roads that needed to remain open, one of the main challenges was to create a gantry system that would safely span these vital transport links.
The gantry system also had to be strong enough to support the construction of the elevated bridge deck above, including the additional formwork required to cast the deck cells in-situ. It was here that the engineering team at RMD Kwikform had to come up with a flexible and cost-effective solution to cater for the loading, the connection of the formwork and the camber of the deck sections above.
To achieve this, a solution incorporating six different product components was designed. Alform beams were used on top of the Gantry beam with a B clamp, combined with suitable timber packing used to create the right angle for the bridge deck. Above the clamp and packing section, a Kwikstage socket base was mounted and used to support a Rapidshor U head. This, in turn, allowed for steel Superslim Soldiers to be supported as primary soffit beams, before GTX secondary timber beams were then mounted above.
Commenting on this challenge and the wider project, Chris Jardine, UAE general manager from RMD Kwikform, said, “When we looked at the gantry section, we realised that it was going to be quite complicated to achieve in the available budget. The key to keeping costs down was to ensure we had no special items that would need to be fabricated; we had to provide a solution that would support the 12 standard 10m long standard gantry beams successfully. By achieving this, we ensured the customer had no additional gantry beam fabrication costs.
“In order to meet the curvature and weight challenges of the structure above the gantry, we needed to come up with a flexible yet robust support solution that ensured the safety of the site team, and the traffic flow underneath the bridge. By modelling this in our local Sharjah office, we were able to use standard components from our fleet to construct what was a simple and cost-effective solution.
“Similarly, when it came to supporting the main bridge deck construction, next to the existing carriageways, we were able to work with the site team to model the Rapidshor solution required for the varying curves of the structures.”
With the height of the elevated bridge decks reaching up to 19m tall, RMD Kwikform engineers had to calculate the complex forces involved in the design of the Rapidshor birdcage-style shoring solution. This included taking into account the impact that high winds would have on the equipment and overall solution.
This process started at ground level, with a plan developed to support simpler erection with the casting of concrete pads, which allowed for the secure mounting of the base plate for the Rapidshor legs. The erection team was then able to construct the Rapidshor towers, using bracing to link them together.
Finer refinements were then made possible by using the adjustable top jack and U Heads at the top of the Rapidshor shoring, allowing the solution to accommodate the sloping gradient of the bridge deck, from 455mm on one side to 96mm on the next. As the 19m high towers were braced together, the site team cast the cells in-situ using RMD Kwikform shoring to create the voids within the deck sections, providing the most cost-effective bridge design.
Chris Jardine said, “This was a very complex project carried out in a very busy location; it was important that we got the site support right. So not to impact the tight programme time, we trained the erection teams and also ensured our equipment was delivered efficiently, in order to maintain the highest levels of safety. Our design team provided cost-effective, reliable and practical solutions for the varying depth of bridge decks, with curved shape and gantry systems. The project itself really took advantage of the flexibility of our Rapidshor system, and the skills of the erection teams made a noticeable difference to the completion of the concrete works.”