Major infrastructure projects worldwide are relying on innovative formwork solutions for speed and safety as Patrick Smith reports. The 970m long cable-stayed Golden Ears Bridge crossing the Fraser River in Vancouver, Canada, is the core element of a six-lane, highway project near the Canadian west coast.
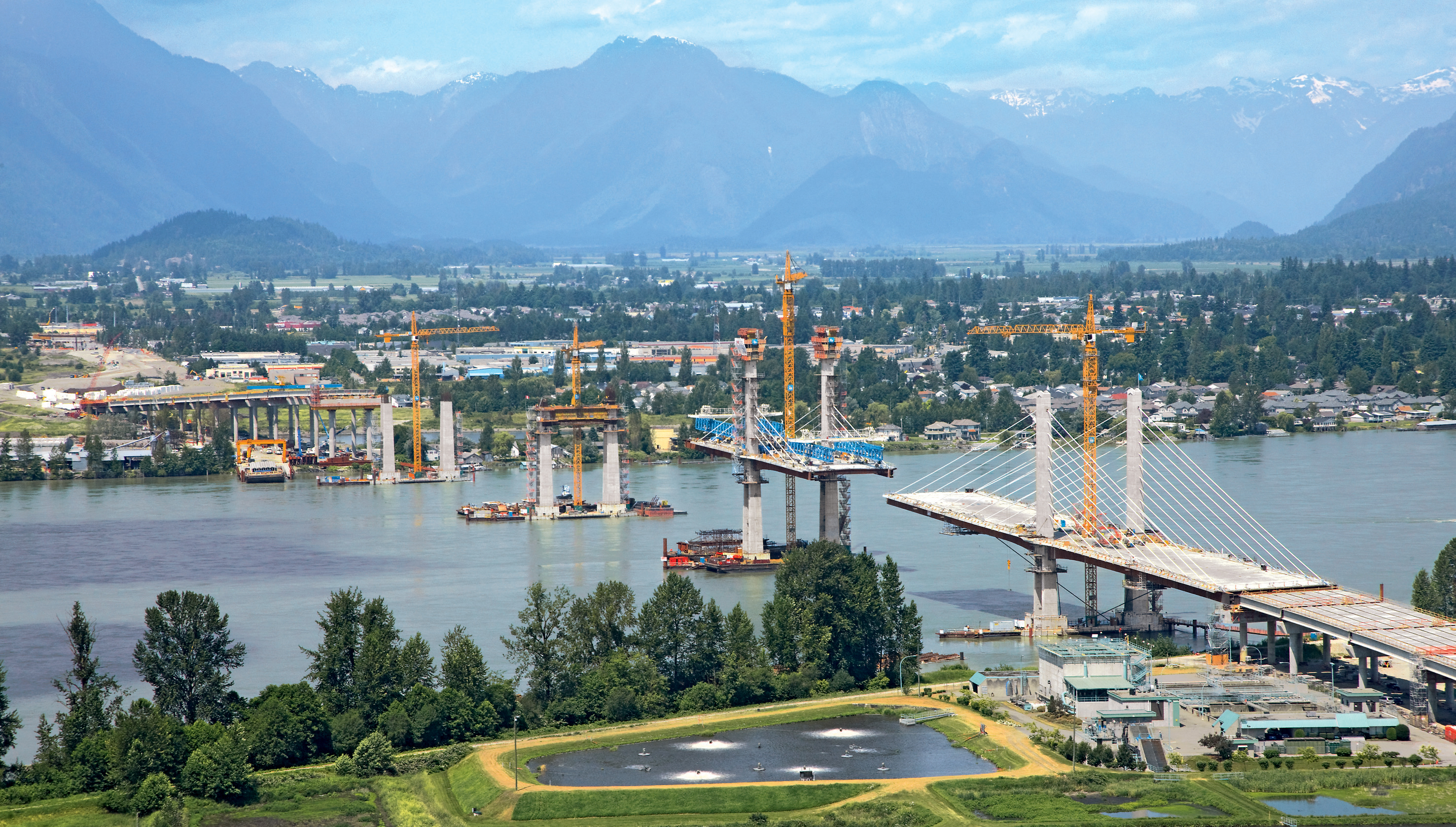
The almost 1km long cable-stayed bridge over the Fraser River constructed with a formwork and scaffold solution from PERI. (Photo: PERI)
The 970m long cable-stayed Golden Ears Bridge crossing the Fraser River in Vancouver, Canada, is the core element of a six-lane, highway project near the Canadian west coast.
The approximate 13km long Golden Ears Crossing infrastructure project, with an investment of e600 million (US$775 million), is one of the largest public-private partnership (PPP) projects in Canada, which Bilfinger Berger has planned, financed and built (2874 CH2M Hill is also part of Golden Crossing Constructors Joint Venture).
Set to open in mid-2009, it will relieve conditions on the main road into the city centre, reduce travelling times and be in use for the 2010 Winter Olympic Games in Vancouver.
The bridge, designed as a so-called extradosed bridge, is a cross between a girder bridge and a cable-stayed bridge. The inclined cables function like a prestressing, and are installed outside the superstructure, positioned at an extremely flat angle.
In spite of the large spans the four bridge pylons, each at intervals of 242m, grew steadily up to heights of 86m with the help of298 PERI ACS self-climbing technology. Pylons of this height are much lower than a traditional cable-stayed bridge.
The PERI formwork and scaffolding solution for the four H-shaped pylons is based on the modular-designed ACS (Automatic Climbing System) self-climbing technology and VARIO girder wall formwork.
As a result, the continuously-changing pylon cross-sections (tapering on all sides) could be cost-effectively and safely constructed using 4m concreting cycle heights and without requiring any crane support.
In addition, the pylon legs underneath the carriageway deck are constructed as double piers in a longitudinal direction, and as individual piers in the form of a composite construction with prefabricated steel cores for the upper half.
The cross-sections change from a dispersed trapezoidal form (5.26m by 1.4m and opening dimensions of 5m at the base) to a single cross-section with external dimensions of 2.46m by 5m at the top of the pylon.
For anchoring the ACS units to the pylon's slanted edges, the PERI ACS system with its pivotable climbing shoe provided a flexible system component. Through this, the ACS platforms can be fixed in position up to 15° from the vertical axis.
PERI formwork planning for the double piers took into consideration that the 5m opening would be reduced to around 4m. Offset ACS brackets ensure that the platforms of the four different working levels could still be securely interlocked.
Formwork elements for the 1.4m wide, inclined front ends are mounted on climbing platforms which are positioned on the longitudinal sides (the complete construction is suspended on rollers which ensures a simple and easy moving process). This means that climbing brackets are not required on the front ends and only two climbing units are needed per individual pier. Material requirements are reduced and every climbing operation can be accelerated.
In order to ensure efficient construction progress, PERI engineers included two separate ACS/VARIO sets of formwork, one set for the top and bottom halves of the pylon, thus avoiding any time-consuming adjustment work having to be carried out on the climbing platforms and formwork.
Climbing has taken place each Monday: initially, the pylon legs with around 4m concreting cycle heights in eight climbing stages up to the level of the carriageway. After the cross member had been concreted, 11 additional climbing cycles using the second set of climbing formwork were required for the top half of the pylon.
PERI's Canadian engineers also designed efficient solutions for the approach bridges and elevations which are part of the overall project.
For this, the broad PERI product range could optimally fulfil the requirements. With standardised modular construction systems, the best-suited formwork and scaffold solution has been able to be developed for each construction task with the contractor realising time and cost advantages.
PERI systems brackets from the VARIOKIT engineering construction kit transferred concreting and live loads during construction of the carriageway slab (which included in situ concreting) into the T-beams, delivered and installed as partly prefabricated sections. For the composite between the prefabricated longitudinal beams above the cross-members, PERI VARIOKIT also provided the optimal solution.
Soft ground and the constant risk of earthquakes made elaborate and costly foundation work necessary, with bored piles for the four pylons up to 95m deep.
In areas where ground load-bearing capabilities were limited the carriageway of the access roads and ramps rests on lightweight EPS rigid foam plastic (the geofoam construction method), which minimises additional loads arising from the required fill and absorbs any vibrations and shocks that may occur.
The name Golden Ear, taken from nearby mountains, is derived from eyries (eagles' nests found in the mountains). For this reason, stylised steel eagles will be placed on the top of the bridge pylons.
203 Doka Portugal developed various alternative formwork and shoring solutions for the main contractor Somague Engenharia and formwork subcontractor Vilaplano Construções: the final solution enabled the construction works to proceed swiftly despite all technical, economical and time constraints.
The 675m long bridge has twin 18.2m wide box sections, six spans of various lengths and an average height of 25m. The double piers each have an elongated 8-shape measuring 2.5m x 11m: for the top 3m of the piers, they merge to create a solid flush pier head. Above this is located the hammerhead, the first section of bridge deck from which the main contractor initiated construction of the bridge deck using the balanced-cantilever method.
Owing to the special shape of the piers and the variations which had to be executed, the chosen solution was to use custom elements of Doka Top 50 large-area formwork. Designed for concreting steps of 4.9m, the formwork was assembled with shaped timber sections to form the final geometry of the piers.
All vertical elements within the piers had a special rippled finish to the surface. Due to the variations between elements, the solution was to utilise hardwood slats to form this finish on the surface of the elements. The rippled effect was an important part of the final appearance of the bridge piers, and due to their simple manner of fitting, the Top 50 elements ensured a flush joint between the casting sections.
"Due to its capabilities and easy adaptability to the Top 50 formwork, the Doka MF 240 climbing system was selected," says Doka.
Its 2.4m wide platform provides enough space to compensate for the variation in shapes, leaving plenty of room for steel reinforcement assembly and cleaning operations, as it can easily be rolled back 75cm from the concrete. Between the double piers, a platform with telescopic shaft beams was used.
The same formwork system was used for the pier heads, and (with minor alterations) for the linking zone on the sides of the piers. For the soffit, special steel beams anchored to the sides of the piers were used to create a support system.
The hammerhead, the first section of the bridge deck, presented the most complicated formwork and shoring task. The hammerhead has a length of 12.5m, is 18.2m wide and has an overall height of 7m. Because the piers below have a much smaller area in plan and are located slanted some 15° away from a right angle to the longitudinal line of the bridge deck, this led to a cantilever of varying size all round the piers, which had to be supported. The fresh concrete weights were very high, and not equally distributed. Due to ground conditions, Doka Portugal had to design a suspended solution. The variation in size and inclination in the longitudinal and transversal section created an added complication, necessitating minor adaptations from pier to pier.
For shoring the hammerhead, Doka selected Doka Supporting Construction Frames of 4.5m, 6m and 8m in length to create a series of cantilever brackets around the pier.
The Supporting Construction Frames have been extensively used for this purpose and are a safe means of supporting the hammerhead without resorting to the traditional method of shoring. They created a base platform for the formwork, and also provided access for personnel working in this area of the works. The frames were anchored to the piers by two Doka pigtail anchors at 45° and by a horizontal anchor, for easy and safe assembly of the entire system.
Doka large-area Top 50 was also used for the hammerhead formwork, as this system enables the contractor to execute the complex shapes required and deal with all the adaptations necessitated by the changes between piers. Doka d2 shoring towers were erected on the inverted Supporting Construction Frames, to support the bridge deck on the inside of the box section and for the works on the cantilever slabs.
It has also brought about a huge boost to319 RMD Kwikform Middle East's business in the region.
Tony Madden, regional manager for RMD Kwikform in Abu Dhabi, said: "This is the first of the civil infrastructure projects to be started on Yas Island to give people access to the Formula One track, though there is a lot more to come. We have enjoyed a very good working relationship with the contractor,2808 Taisei Abu Dhabi, and have been able to keep up with the schedule for what is a very demanding contract.
"Basically our involvement with the new freeway has acted as a springboard, the base from which we have grown the business here in Abu Dhabi. Our operation in Abu Dhabi is becoming more impressive by the month."
RMD Kwikform is partnering with the Taisei on the vast project that involves the erection of seven box cell bridges as well as three extensive culverts. With rapid completion being imperative for the essential transportation scheme, and with major waterways having to be temporarily diverted to facilitate the erection process, RMD Kwikform has had to provide intelligently designed formwork systems together with a number of specially fabricated steel shutters to keep the contract on programme.
Five of the seven bridges, including the 250m long, parallel BC7 and BC8, are being erected using Rapidshor, along with GTX beams. This falsework structure and the accompanying RMD Kwikform Rapidshor stair-towers for safe personnel access are all being supported off the infill where the river/canal bed has been temporarily raised.
Tony Madden explains: "The external webs to the bridge box cells are being built up first (forming a slab and side walls) with the Rapidshor and GTX beams being used to cast the deck element. Then the side walls and central walls are assembled using Superslim Soldiers plus GTX beams. Finally for the top slab to the boxes we have supplied Kwikstage, again with GTX beams."
The RMD Kwikform formwork has to continue to carry the dead loads of the reinforced concrete, plus all the construction equipment and manpower, until the mix has gained sufficient strength, for the specialist sub-contractor, VSL to carry out the post-tensioned pre-stressing of all the cables that run within ducts in the box walls.
The decks to both BC7 and BC8 are being built with a 1:40 super-elevation to respect the curve of the road line, meaning that the box cells vary in depth up to a maximum of 4.5m.
Each of the two bridges will carry six lanes of traffic in opposite directions, while a further structure between them supports the two tracks of Abu Dhabi's new rapid transit system.
Prior to the start of deck construction, RMD Kwikform supplied Alform and Superslim Soldiers to cast the vertical walls of the bridge piers. These rise some 9m between ground level and the pier-heads where the bridge bearing plates are inserted. They also display bull-nosed vertical edges with a 900mm radius for which RMD Kwikform's designers and special fabrication unit produced bespoke steel shutters are being reused along the contract.
Such are the demands of the timetable, however, that the Taisei Corporation has purchased 60,000m³ of Rapidshor for the contract. The formwork specialist also provided some initial training for the contractor's operatives, as well as continuing site supervision.
The last two bridges for the freeway are additionally making use of RMD Kwikform's Paraslim system to enable the in situ concrete element to the composite decks to be cast up to 1m in cantilever beyond the line of the precast concrete beams that span between each abutment and the pier-head. The hanging soffit support system can be built up in modules of 6m and then craned into position without relying on staging rising from ground level.
Although the first deliveries to Taisei on the site only began in December 2007, the majority of the bridges are scheduled to be completed by this month. The longer, BC7 and BC8 bridges are expected to be structurally complete by May.
The approximate 13km long Golden Ears Crossing infrastructure project, with an investment of e600 million (US$775 million), is one of the largest public-private partnership (PPP) projects in Canada, which Bilfinger Berger has planned, financed and built (
Set to open in mid-2009, it will relieve conditions on the main road into the city centre, reduce travelling times and be in use for the 2010 Winter Olympic Games in Vancouver.
The bridge, designed as a so-called extradosed bridge, is a cross between a girder bridge and a cable-stayed bridge. The inclined cables function like a prestressing, and are installed outside the superstructure, positioned at an extremely flat angle.
In spite of the large spans the four bridge pylons, each at intervals of 242m, grew steadily up to heights of 86m with the help of
The PERI formwork and scaffolding solution for the four H-shaped pylons is based on the modular-designed ACS (Automatic Climbing System) self-climbing technology and VARIO girder wall formwork.
As a result, the continuously-changing pylon cross-sections (tapering on all sides) could be cost-effectively and safely constructed using 4m concreting cycle heights and without requiring any crane support.
In addition, the pylon legs underneath the carriageway deck are constructed as double piers in a longitudinal direction, and as individual piers in the form of a composite construction with prefabricated steel cores for the upper half.
The cross-sections change from a dispersed trapezoidal form (5.26m by 1.4m and opening dimensions of 5m at the base) to a single cross-section with external dimensions of 2.46m by 5m at the top of the pylon.
For anchoring the ACS units to the pylon's slanted edges, the PERI ACS system with its pivotable climbing shoe provided a flexible system component. Through this, the ACS platforms can be fixed in position up to 15° from the vertical axis.
PERI formwork planning for the double piers took into consideration that the 5m opening would be reduced to around 4m. Offset ACS brackets ensure that the platforms of the four different working levels could still be securely interlocked.
Formwork elements for the 1.4m wide, inclined front ends are mounted on climbing platforms which are positioned on the longitudinal sides (the complete construction is suspended on rollers which ensures a simple and easy moving process). This means that climbing brackets are not required on the front ends and only two climbing units are needed per individual pier. Material requirements are reduced and every climbing operation can be accelerated.
In order to ensure efficient construction progress, PERI engineers included two separate ACS/VARIO sets of formwork, one set for the top and bottom halves of the pylon, thus avoiding any time-consuming adjustment work having to be carried out on the climbing platforms and formwork.
Climbing has taken place each Monday: initially, the pylon legs with around 4m concreting cycle heights in eight climbing stages up to the level of the carriageway. After the cross member had been concreted, 11 additional climbing cycles using the second set of climbing formwork were required for the top half of the pylon.
PERI's Canadian engineers also designed efficient solutions for the approach bridges and elevations which are part of the overall project.
For this, the broad PERI product range could optimally fulfil the requirements. With standardised modular construction systems, the best-suited formwork and scaffold solution has been able to be developed for each construction task with the contractor realising time and cost advantages.
PERI systems brackets from the VARIOKIT engineering construction kit transferred concreting and live loads during construction of the carriageway slab (which included in situ concreting) into the T-beams, delivered and installed as partly prefabricated sections. For the composite between the prefabricated longitudinal beams above the cross-members, PERI VARIOKIT also provided the optimal solution.
Soft ground and the constant risk of earthquakes made elaborate and costly foundation work necessary, with bored piles for the four pylons up to 95m deep.
In areas where ground load-bearing capabilities were limited the carriageway of the access roads and ramps rests on lightweight EPS rigid foam plastic (the geofoam construction method), which minimises additional loads arising from the required fill and absorbs any vibrations and shocks that may occur.
The name Golden Ear, taken from nearby mountains, is derived from eyries (eagles' nests found in the mountains). For this reason, stylised steel eagles will be placed on the top of the bridge pylons.
Doka's Portuguese solution
The centrepieces of the new A17 motorway between Marinha Grande and Mira in Portugal are the bridge and viaduct over the Mondego River.The 675m long bridge has twin 18.2m wide box sections, six spans of various lengths and an average height of 25m. The double piers each have an elongated 8-shape measuring 2.5m x 11m: for the top 3m of the piers, they merge to create a solid flush pier head. Above this is located the hammerhead, the first section of bridge deck from which the main contractor initiated construction of the bridge deck using the balanced-cantilever method.
Owing to the special shape of the piers and the variations which had to be executed, the chosen solution was to use custom elements of Doka Top 50 large-area formwork. Designed for concreting steps of 4.9m, the formwork was assembled with shaped timber sections to form the final geometry of the piers.
All vertical elements within the piers had a special rippled finish to the surface. Due to the variations between elements, the solution was to utilise hardwood slats to form this finish on the surface of the elements. The rippled effect was an important part of the final appearance of the bridge piers, and due to their simple manner of fitting, the Top 50 elements ensured a flush joint between the casting sections.
"Due to its capabilities and easy adaptability to the Top 50 formwork, the Doka MF 240 climbing system was selected," says Doka.
Its 2.4m wide platform provides enough space to compensate for the variation in shapes, leaving plenty of room for steel reinforcement assembly and cleaning operations, as it can easily be rolled back 75cm from the concrete. Between the double piers, a platform with telescopic shaft beams was used.
The same formwork system was used for the pier heads, and (with minor alterations) for the linking zone on the sides of the piers. For the soffit, special steel beams anchored to the sides of the piers were used to create a support system.
The hammerhead, the first section of the bridge deck, presented the most complicated formwork and shoring task. The hammerhead has a length of 12.5m, is 18.2m wide and has an overall height of 7m. Because the piers below have a much smaller area in plan and are located slanted some 15° away from a right angle to the longitudinal line of the bridge deck, this led to a cantilever of varying size all round the piers, which had to be supported. The fresh concrete weights were very high, and not equally distributed. Due to ground conditions, Doka Portugal had to design a suspended solution. The variation in size and inclination in the longitudinal and transversal section created an added complication, necessitating minor adaptations from pier to pier.
For shoring the hammerhead, Doka selected Doka Supporting Construction Frames of 4.5m, 6m and 8m in length to create a series of cantilever brackets around the pier.
The Supporting Construction Frames have been extensively used for this purpose and are a safe means of supporting the hammerhead without resorting to the traditional method of shoring. They created a base platform for the formwork, and also provided access for personnel working in this area of the works. The frames were anchored to the piers by two Doka pigtail anchors at 45° and by a horizontal anchor, for easy and safe assembly of the entire system.
Doka large-area Top 50 was also used for the hammerhead formwork, as this system enables the contractor to execute the complex shapes required and deal with all the adaptations necessitated by the changes between piers. Doka d2 shoring towers were erected on the inverted Supporting Construction Frames, to support the bridge deck on the inside of the box section and for the works on the cantilever slabs.
Yas Island: boxing clever
Constructing the ten structures along the route of the Shaham to Saadiyat Island Freeway is helping to create an essential link from mainland Abu Dhabi to the site of the planned new Formula One Grand Prix circuit in the Emirates (see also Onsite this issue).It has also brought about a huge boost to
Tony Madden, regional manager for RMD Kwikform in Abu Dhabi, said: "This is the first of the civil infrastructure projects to be started on Yas Island to give people access to the Formula One track, though there is a lot more to come. We have enjoyed a very good working relationship with the contractor,
"Basically our involvement with the new freeway has acted as a springboard, the base from which we have grown the business here in Abu Dhabi. Our operation in Abu Dhabi is becoming more impressive by the month."
RMD Kwikform is partnering with the Taisei on the vast project that involves the erection of seven box cell bridges as well as three extensive culverts. With rapid completion being imperative for the essential transportation scheme, and with major waterways having to be temporarily diverted to facilitate the erection process, RMD Kwikform has had to provide intelligently designed formwork systems together with a number of specially fabricated steel shutters to keep the contract on programme.
Five of the seven bridges, including the 250m long, parallel BC7 and BC8, are being erected using Rapidshor, along with GTX beams. This falsework structure and the accompanying RMD Kwikform Rapidshor stair-towers for safe personnel access are all being supported off the infill where the river/canal bed has been temporarily raised.
Tony Madden explains: "The external webs to the bridge box cells are being built up first (forming a slab and side walls) with the Rapidshor and GTX beams being used to cast the deck element. Then the side walls and central walls are assembled using Superslim Soldiers plus GTX beams. Finally for the top slab to the boxes we have supplied Kwikstage, again with GTX beams."
The RMD Kwikform formwork has to continue to carry the dead loads of the reinforced concrete, plus all the construction equipment and manpower, until the mix has gained sufficient strength, for the specialist sub-contractor, VSL to carry out the post-tensioned pre-stressing of all the cables that run within ducts in the box walls.
The decks to both BC7 and BC8 are being built with a 1:40 super-elevation to respect the curve of the road line, meaning that the box cells vary in depth up to a maximum of 4.5m.
Each of the two bridges will carry six lanes of traffic in opposite directions, while a further structure between them supports the two tracks of Abu Dhabi's new rapid transit system.
Prior to the start of deck construction, RMD Kwikform supplied Alform and Superslim Soldiers to cast the vertical walls of the bridge piers. These rise some 9m between ground level and the pier-heads where the bridge bearing plates are inserted. They also display bull-nosed vertical edges with a 900mm radius for which RMD Kwikform's designers and special fabrication unit produced bespoke steel shutters are being reused along the contract.
Such are the demands of the timetable, however, that the Taisei Corporation has purchased 60,000m³ of Rapidshor for the contract. The formwork specialist also provided some initial training for the contractor's operatives, as well as continuing site supervision.
The last two bridges for the freeway are additionally making use of RMD Kwikform's Paraslim system to enable the in situ concrete element to the composite decks to be cast up to 1m in cantilever beyond the line of the precast concrete beams that span between each abutment and the pier-head. The hanging soffit support system can be built up in modules of 6m and then craned into position without relying on staging rising from ground level.
Although the first deliveries to Taisei on the site only began in December 2007, the majority of the bridges are scheduled to be completed by this month. The longer, BC7 and BC8 bridges are expected to be structurally complete by May.