Speed of erection, safety, cost-efficiency and flexibility are among the attributes of modern formwork systems. Modern formwork and scaffolding systems are attractive in particular for their speed of erection, safety, cost-efficiency and flexibility.
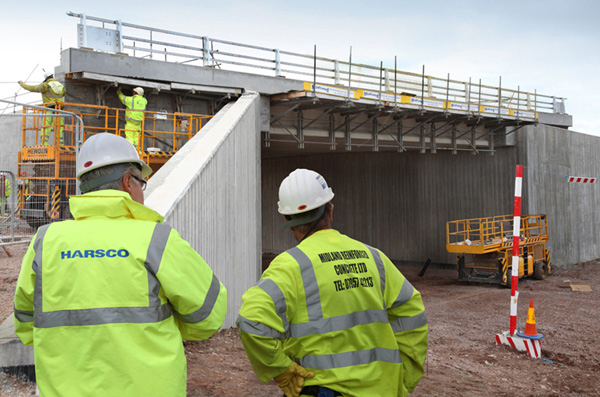
Harsco's Multiform Parapet system was designed and supplied for three bridges on the A46 project
Speed of erection, safety, cost-efficiency and flexibility are among the attributes of modern formwork systems
Modern formwork and scaffolding systems are attractive in particular for their speed of erection, safety, cost-efficiency and flexibility. This is the view of Anibrata Routh, technical head at"Our present assessment is that only around 2% of the Indian formwork and scaffolding market is covered by contemporary integrated solutions." Against a background of globalisation, companies from outside of India will increasingly have an opportunity to get a stake in this up-and-coming market, said Routh.
Jim Goldsmith, sales director at
The formwork solution for the slender, needle-like 180m high concrete suspension tower in the province of Toledo in Spain's heartland is said to be an achievement of Doka España together with Application Engineering in Sales Region 4 and the Expertise Centre for Automatic Climbing in Amstetten, Austria.
It stands on a foundation of 56 drilled piles and is inclined at 22° from the vertical, an angle at which it utilises its own deadweight to balance part of the load of the superstructure bridging the river valley. The load is carried by 76 cables linking the suspension tower to the bridge superstructure: another 76 cables stay the tower off the foreland foundation.
The tower also has to take the vertical loads imposed by the bridge to transfer them into the sub-ground and also withstand horizontal wind loads, so high compressive strength H-70 concrete was selected by contracting consortium UTE Ronda Sur Talavera.
The suspension tower, which in cross section tapers from 17m x 4m to 5.6m x 4m at the 62nd concreting section, had to be erected in concreting sections each 3m high, and to dispense with time-consuming re-rigging a craneless, speedily adaptable formwork solution was needed. Doka's solution used SKE100 automatic climbing formwork with telescopically adjustable working platforms.
"A great deal of time was saved on site because the beam formwork came pre-assembled by Doka España's ready-to-use service. The scaffolding and the formwork were ready to go within a very short time after delivery to site. Ever since completing the difficult transition at the 6th concreting section, the crew has been maintaining an impressive 36-hour cycle for forming," said Doka site foreman Jürgen Pöchacker.
The SKE100's load-bearing capacity of 10tonnes/bracket means it can carry multiple platform levels, so the various operations of placing the reinforcement and handling the formwork and casting the concrete can progress separately.
On the Talavera tower build, the lead part of the crew handles the positioning of the rebar cages (preassembled on the ground) together with the steel boxes for tensioning the stay cables in the next concreting section. At the same time another part of the crew follows up by adapting the formwork to the reduced cross section.
Formwork planning also had to allow for installation of the stay cables, because a working platform on the outside face is needed for access. On the overhanging narrow face of the tower the sides are stepped in from the 12th concreting section up, forming an inside step at this level.
Openings for the stay cables are located in this back-step zone, and access to these apertures is necessary, so Doka planned a suspended platform that can be adjusted both vertically and horizontally.
Positioning of the platform at the inside step has to be accurate to within centimetres, so the platform also extends telescopically into the back cut.
On the opposite side of the suspension tower the wall features a niche 1m wide and 300mm deep that also serves to accommodate the site elevator.
As José María Saíz Aguado, the civil engineer in charge of the project, said: "The speed with which the formwork can simply be telescoped to adapt to the cross section of the tower saves us 30 working hours by comparison with the more complicated process of re-rigging."
Abu Dhabi challenge
The Mafraq Interchange, the largest infrastructure project underway in Abu Dhabi, will allow traffic to run from north to south, connecting Abu Dhabi Airport to the Saudi Arabian border, and east to west, easing congestion from Al Ain to Abu Dhabi City.Replacing the current two-lane interchange that is now too small to cope with the increase in road traffic, the Mafraq Interchange, once completed, will consist of four lanes in each direction, two main arched flyovers (R5 and R6) and two smaller main deck bridges known as Bridge 10.
For primary contractor China Civil Engineering and Contracting, the main challenge was the rapid construction of the three bridge structures (two 980m long bridges and up to 22m high and the third 300m long). According to RMD Kwikform, the key to delivering the project on time and budget was the use of a combination of formwork and falsework equipment from RMD Kwikform Middle East.
In addition to the Rapishor, special components were designed and manufactured for the wing walls, with SuperSlim primary and GTX secondary beams used to form the support for the plywood deck structure.
With a total of 2,260m of bridge to construct, China Civil Engineering and Contracting opted to part purchase and part hire the equipment required for the job from RMD Kwikform Middle East, as the Rapidshor system could then be reused on future projects.
With 100,000m³ of Rapishor needed to complete the job, the Mafraq Interchange represented one of the most significant projects undertaken using Rapidshor in the Middle East. For the two arched flyovers R5 and R6, constructed simultaneously, approximately 50,000m³ of Rapidshor was used for each structure. The product was then re-used to construct the first span of Bridge 10, with approximately 15,000m³ of Rapidshor fully decked out, which on completion was then reused to construct the second span.
Using the Alshor Plus platform, site staff was able to instruct the crane operators and manoeuvre the beams safely so the staff could achieve the precise accuracy required for beam placement without damaging the pier heads.
Once in place, the 200m of Paraslim was erected onto the side of the beams to form the parapet part of the four-lane structure, which was then cast in concrete.
Elpidio Aspillaga, RMD Kwikform's sales manager said: "Logistically managing the sourcing and transportation of 100,000m³ of Rapishor was a complex task. However, as a business we are used to working on large scale projects of this nature, so the demands of this project were well within our experience and capabilities.
"The real challenge came with the design of two bespoke formwork and falsework solutions for the project. The first required our engineering team to design a new solution to allow the overall system to follow the wing profile of the bridge. To make this as easy to achieve as possible, a cranked Superslim soldier was created, with 440 units fabricated to a tight deadline order to complete the task.
"Because the deck edge was in parts over 22 metres off the ground and had to flow with the curvature of the bridge designed, the formation of the Superslim Soldier deck edge falsework had to take into account how it would be supported by the Rapidshor shoring, while being able to form the correct angles required to allow the deck edge to be poured.
"In order to achieve this, our engineering team had to connect regular Superslim beams and the cranked Superslim Soldiers together at non-uniform angles, while ensuring structural integrity at all stages in order for the deck edge support to withstand the concrete pressures. To make the connection a standard pin connector was used to attach the Superslim soldiers together.
"The whole approach was designed to speed up the construction process cycle time, allowing China Civil Engineering and Contracting to erect the forms at ground level in completed side units. This made for very little adjustment of the units when they were placed along the bridge edge shoring. On a long repetitive bridge such as this one, reducing cycle time was very important. By using a cantilever design, the side units could be removed early in the striking process and reassembled at the next stage of construction, speeding up the process dramatically."
PERI's parapet solution
For the realisation of parapets for bridge structures, PERI has recently added the lightweight VGK bracket to its product portfolio, and this can be installed by hand.A special feature of the system is that platform beams and the support for the formwork structure are completely separate.The work, which is to be carried out from below, is limited to the initial assembly of the platform beams.
"As a result, closed and watertight enclosures can be easily and simply realised. The solution is particularly suitable for refurbishing work as well as new bridge structures with short lengths," says PERI.
The new VGK parapet bracket supplements the VARIOKIT engineering construction kit which offers a wide variety of solutions for bridge, tunnel and civil engineering construction, and "nicely rounds off the range of parapet solutions." It is suitable for short structures and in particular for the refurbishment of the parapets for cast-in-place or composite bridges in the cantilever and wing areas, says PERI.
The first projects carried out with the new VARIOKIT VGK parapet bracket were parapet refurbishments on the Rhine Valley Motorway Bridge near Dornbirn, Austria, and the Goldbach Bridge in Überlingen, Germany. Described as lightweight, flexible and cost-effective, the brackets consist of bracket post, bracket kicker brace, platform beam, formwork support, formwork connection and spindles.
The low weight of the individual components (maximum 18kg) allows simple and fast assembly by hand. The brackets have been designed for mounting both horizontally as well as vertically and can be fixed to the underside of the cantilever and abutment walls, while the system can be flexibly adapted to suit different parapet geometries and carriageway radii.
Depending on the length of the cantilever, three different types of bracket are available. For cantilever lengths of more than 90cm, the loads can be transferred by means of a spindle which is supported diagonally against the underside of the cantilever. With bracket lengths ranging from 25-90cm, a bracket beam is horizontally tensioned against the bridge beam. For short cantilevers with a maximum length of 25cm, the vertical post of the bracket can be directly fixed to the bridge beam or abutment wall.
"To begin with, the suspension heads for the brackets are mounted on the bridge structure. The spacing of the individual brackets depends on the parapet cross section. PERI M 24 anchor sleeves are recommended as the securing means for the suspension for new bridge construction, and M 16 anchor sleeves or M 24 bonded ties (regardless of the manufacturer) for refurbishing work," says PERI.
"After fixing the bracket kicker brace, the bracket post and the spindles, the platform beams are installed together with the planking followed by the guardrail boards or enclosure."
According to PERI, after the initial assembly using an elevating work platform or scaffolding, access from below is no longer necessary: assembly of the formwork support is carried out from above. "Handling and adjustments also needs no access from below. Furthermore, the formwork construction does not require an opening in the platform itself. This is thus permanently closed which provides protection for the traffic moving under the bridge."
Harsco's A46 job
Access and formwork supplierThrough a large part of the county the route is single carriageway, but under the £220 million (US$352 million) UK
Harsco's Multiform Parapet system was designed and supplied for three of the six bridges, Saxondale North, Saxondale South and Stragglethorpe.
Tony Nicholls, managing director of Midland Reinforced Concrete, using the Parapet system for the first time, said: "The system is very safe and quick to use. We built the pre-assembled brackets into standard size units and lifted them into position with a crane, drastically reducing the need for any work at height.