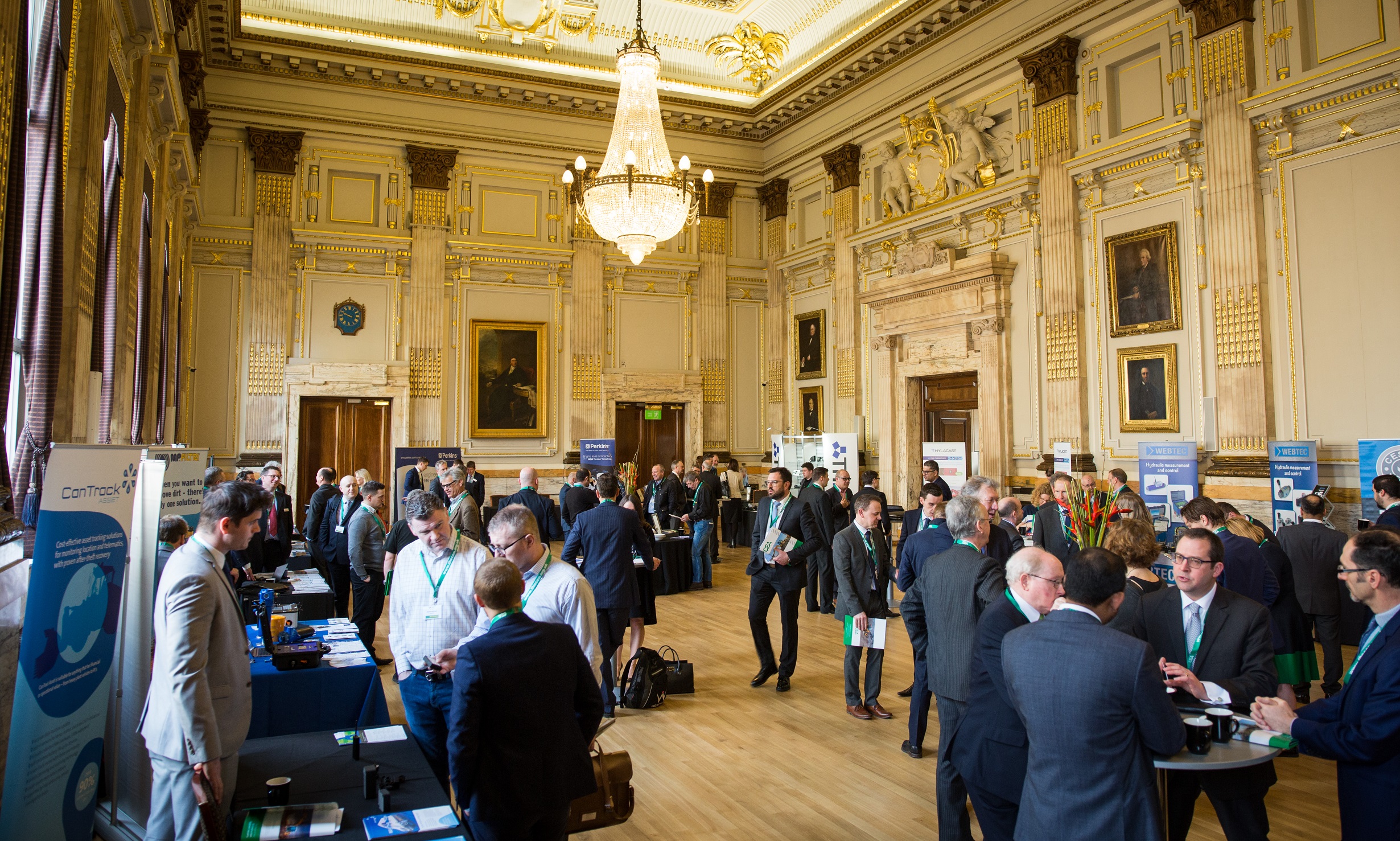
Construction machine manufacturers are going to have to find new solutions if targets on emissions controls are going to be met. This is a clear viewpoint for the industry. But as the speakers at the recent CEA conference in London showed, there are differing opinions on how that will be achieved and what technical solutions will come to the fore.
Duncan Riding, business development manager at
However Riding said that comparing the numbers of cars and construction machines is important. There are around 47 times more cars in use around the world than construction machines. With this is mind it is clear that reducing emissions from cars is of higher priority than for the construction machinery sector. That said, construction machine builders have already made inroads into cutting emissions, offering new models.
He said, “If I’m burning fossil fuels, perfect combustion results in CO2 and water from the tailpipe. Too high a temperature means we get NOx and imperfect combustion means we get hydrocarbons.” Riding said that as no engine offers perfect performance, emissions do have to be addressed. “Local air quality is a big deal and we need tools as we are worried about it.”
But he continued, “The final question comes down to fuels of the future.”
Riding explained that while electric vehicles offer many advantages in terms of emissions, the numbers still do not add up with regard to range and recharging. For example, he said that the fuel capacity of a diesel tractor allows it to operate for a full 8-10-hour working shift, without need for refuelling. But even with a good battery back, an electric tractor will typically only work for two hours before needing recharging. And he added that to provide enough cells for a 56kW motor to operate for a full 10-hour shift would cost around £33,500. Meanwhile fast charging of such a machine in two minutes, equivalent to the time needed to refuel the diesel equivalent, would require a power supply of 10MW. Given that construction or agricultural machines often operate in remote locations, supplying fast charging networks would be impractical.
Riding said that he does believe electric power will be of value, “I’m saying all electric will work in passenger cars.” And he added that some off-highway machines, such as access equipment or forklifts are already using electric power. And he thinks that the percentage of electric access machines or forklifts will continue to grow. For these machines, electric power allows them to be used inside buildings and for forklifts, and he added, “Customers are also used to having to swap between machines while charging.” While up-front purchase costs can be higher for this approach, the low running costs of an electric machine will offer a benefit over the longer term.
There are other power options too and Riding said, “Most engine manufacturers have looked at alternative fuels. LPG is very quiet in diesels and we’ve all done that.”
But for construction or agricultural machines he commented, “Off-highway will still be predominantly diesel-powered in the future. We can use any type of liquid fuel in our engines and algae -based diesel fuels are very interesting.”
He continued, “The construction industry needs a structured and consolidated view on what fuels to aim for.”
With regard to emissions he said, “Local air quality we can manage with the new machines we’re producing today.”
A rather different perspective was given by Jenny Elfsberg, director of emerging technologies at
She said that the firm’s prototype HX02 all-electric, autonomous hauler was tested at a quarry operation as part of a research project run in partnership with Skanska and two universities. The quarry site also used a hybrid wheeled loader, which is able to run in all-electric mode for around 30 minutes. However the machine generally operates in hybrid mode, which is said to make it around 30% more fuel-efficient than a comparable machine.
The 15tonne capacity autonomous hauler from Volvo CE in particular offers the benefits of electromobility and connectivity. However, more simple technologies may offer greater efficiencies and Elfsberg said, “We did studies before and they showed that there is waste on the site. If we look at how operators are using machines, there is room for greater efficiency. We are in need of optimising processes.”
She pointed out that the process to release energy from diesel fuel into working power for a machine is inherently inefficient and commented, “If we make internal combustion engines more efficient we can use them for many more years to come. It is not obvious we should go to electric drives because we do need the power density.” However she added, “Electricity has a future. You can use that energy between machines.”
While autonomous machines may come in the future, these may also be for certain categories only and operators will still be needed for many years to come.
Operator training
Meanwhile, other discussions focussed on the use of virtual reality in operator training, with Dale Hawkins and Mark Kennedy of UK Plant Operators making key comments. Kennedy said that there is a desperate need for machine operators in construction as many are coming up to retirement age. He said, “There are more operators leaving the industry than coming in. The average age of a dozer operator in the UK is 54 years old. We need to be able to train young operators, but operators are not being trained quickly enough to meet demand.”
According to Kennedy, using virtual reality system can help address this shortcoming and help to encourage younger people used to gaming systems to enter the construction sector. He said, “Everything is on the simulator programs and works as on a real machine.”
Virtual reality offers major advantages for training too and he said, “If you’ve got a group of trainees it can be difficult to work in the field with machines. Virtual reality means you can give the initial training in a classroom environment.”
He continued, “We have started to use these for inductions,” explaining that this allows the trainer to assess the aptitude and skill level of a trainee for a particular job. He added, “We can also take in non-operators and show them how difficult it is to operate a machine.”
Kennedy said that while there are still limitations with the virtual reality systems, the technology gives a valuable start to the overall training process. “For hazard perception, we can get the trainee to highlight those areas.”
The systems are becoming more advanced however. Hawkins said, “Our simulator is one of the very few in the country to incorporate a live GPS system.”
He said that this feature was added to meet a specific need, “Machine control is taking the industry by storm,” adding that this allows sites to do away with the need for personnel to place stakes or act as banksmen onsite. And he said that using simulators allows operators to get training on sophisticated machine control tools before they get on site.