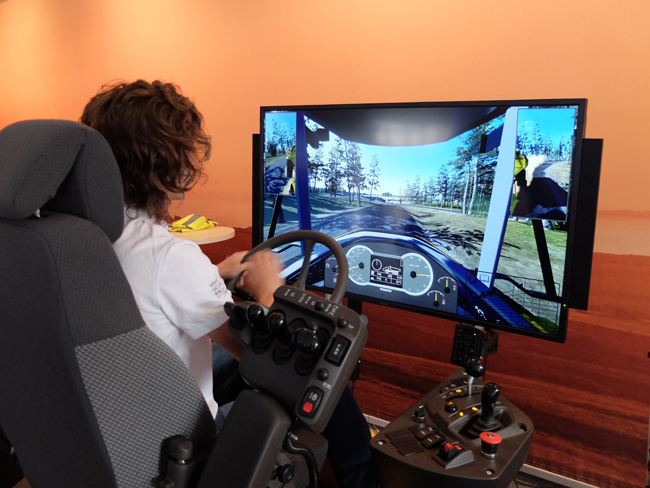
CEO Melker Jernberg said, “When it comes to performance we need to be good economically. We saw growth for 2018 in all regions.”
He continued, “When it comes to market shares we are the global market leader in ADTs,” and added that the firm is in a strong position in the global wheeled loader market, while it is also gaining market share in the segment for compaction machines as well as for wheeled excavators.
With a strong financial performance, Volvo CE is in a good position to spend on research and development. Jernberg said that the company is one of the firms in the sector investing a higher proportion of revenue in research and development to deliver future solutions.
The electric worksite is one project Volvo CE has been experimenting with in a bid to cut emissions and this aims to lower carbon emissions from an operation by as much as 95%. This will be an actual working quarry and Jernberg said, “It will be running in the Autumn. We will have one diesel hybrid loader operated by a driver.”
The site will run with just two people working at the facility, while a number of the firm’s novel autonomous electric haulers will carry materials from the working area. The autonomous haulers are still prototypes but Jernberg said he believes that autonomous machines will be introduced to certain areas of the construction equipment market, due in part to the lack of availability of operators. However, when this will happen is too early to tell. While autonomous machines are used in some sectors of the mining industry, these are large and costly items of equipment that remove the need for operators in harsh climates or dangerous working areas.
The firm is also working on a project to improve site safety, in partnership with contractor
A sophisticated detection system has been developed and Jernberg said, “We’ve tested it and it can really differentiate between what are objects and people.”
This project is intended to improve safety around machines and provides alerts to machine operators when a person is detected in the danger zone. Jernberg commented, “Together with Colas we decided solutions.”
Operator assistance technology is another area where Volvo CE believes it is amongst the leaders in the construction machinery sector. Jernberg said, “We have co-pilot assist systems for all machines.” And he added, “In the Volvo Group we have 700,000 connected machines.”
The company believes that its new Volvo Insight Reports will provide major benefits for customers. Although the company has been offering Fuel Efficiency Reports since 2016 it now has new Summary Reports and Health Reports, introduced along with the Insight Reports portfolio in April this year. The reports remove the need for customers to interpret complex data themselves and can be compiled based on an individual machine or an entire fleet.
The connected machine technology offers customers many advantages. Carl Slotte, president for sales in the EMEA region explained that firms can use the data to improve machine servicing and cut running costs, boosting efficiency as well as benefiting the bottom line. He said, “Fuel consumption costs are almost 50% of the cost of a machine over its life.”
And he continued, “With the help of Insight Reports, the management can get sight of what is happening with machines.”
According to Slotte, one customer is using the system to manage a fleet of 157 machines for example. It found that it was using 48,000litres of fuel/year. Analysis showed that the machines were delivering 65% actual utilisation, while the time the machines spent with engines idling for more than 5 minutes accounted for 2% of running time. Tackling this alone allowed for a significant cut in fuel consumption for the firm’s fleet. Addressing the time the machines spent with engines idling for shorter periods allowed for an even greater fuel saving overall.
The system has also allowed the firm to look at operator training needs. By identifying issues such as frequent engine over-speeding, the company has lowered maintenance needs for certain units. With operating and running costs accounting for around 46% of a machine’s total cost, reducing fuel consumption and maintenance needs can deliver major savings to a customer.
A user can make a video of a working site and Slotte said, “…and we can put the person into their own machine so that the operator can train at their own site. This is interactive training between the operator and the machine. After each session we get a report on wear and tear and on the fuel used.”
Teaching operators to be more economical on fuel can deliver serious cost savings.
Slotte commented that for a fleet using 48,000litres of fuel, even a 10% saving saves 4,800litres of fuel. And addressing issues such as over-speeding will also lower maintenance and repair costs. He added, “Most customers are renting them for a few months. They are really nice tools.”
The company is keen to help its customers improve factors such as fleet utilisation and cost efficiency, Fredrik Gerhardson is vice president for aftermarket and said, “Customers only make money when machines are working.”
Allowing remote access to machine data allows technicians to carry the right tools and parts when they go to work on a machine, an important point. Gerhardson said, “Around 80% of our repairs are in the field and you need to be prepared when you go out.”
Aram Mahmood is director of product support and asked, “How can we enable the dealer to identify a problem with a machine?” He said that time is crucial, “It’s time customers cannot afford.”
He said that Volvo CE is working on two specific projects to give mechanics access to the right information and support when they need it. The first is called First Time Fix and aims at identifying the root cause of an issue as early and as quickly as possible. The company is working together with SMT Netherlands as a pilot dealer on this project with the aim of rolling it out to all its largest dealers in future.
This is important too as there is a growing shortage of service technicians in the construction sector, and allowing them to utilise their time more efficiently will allow them to be more productive. According to Mahmood, the single communications platform plays a vital role.
If a machine component is behaving unusually and the issue is too complex for a dealer mechanic to solve, the technician can enter the case into the systems’ app on their phone. Photos of the component can be uploaded and the user can fill in details, which then go to the dealer site. If this issue cannot be solved at the dealer site, the case can then be escalated in the same system to a product specialist at Volvo CE.
This method also improves efficiency compared with conventional methods of fleet maintenance. And Volvo CE’s dealers will be able to access the new system on a worldwide basis. Mahmood added, “Previously, when there was no common case handling system, there was a potential for information to get lost along the way, or not even be added in the first place.”
Other innovations have been developed too. Volvo CE also introduced an updated version of its SiteSim package earlier this year with new features and benefits. A key feature is the use of drones to input 3D photos of the customer’s site into the programme. The other main improvement is that the programme can now run several different jobs at the site in the same simulation.
SiteSim calculates the optimum set-up for an entire site to give the lowest possible total cost of ownership. By inputting the type of material, distance from the loading to dumping points, and topography of the site, a Volvo consultant can recommend the ideal number and capacity of machines, as well as the optimum routes operators should drive, based on the tonnes/hour and cost/tonne. The programme can run simulations for up to a year of operation.
Although this approach is used widely in the mining industry, Volvo CE can offer comprehensive simulations for small and medium-sized sites.