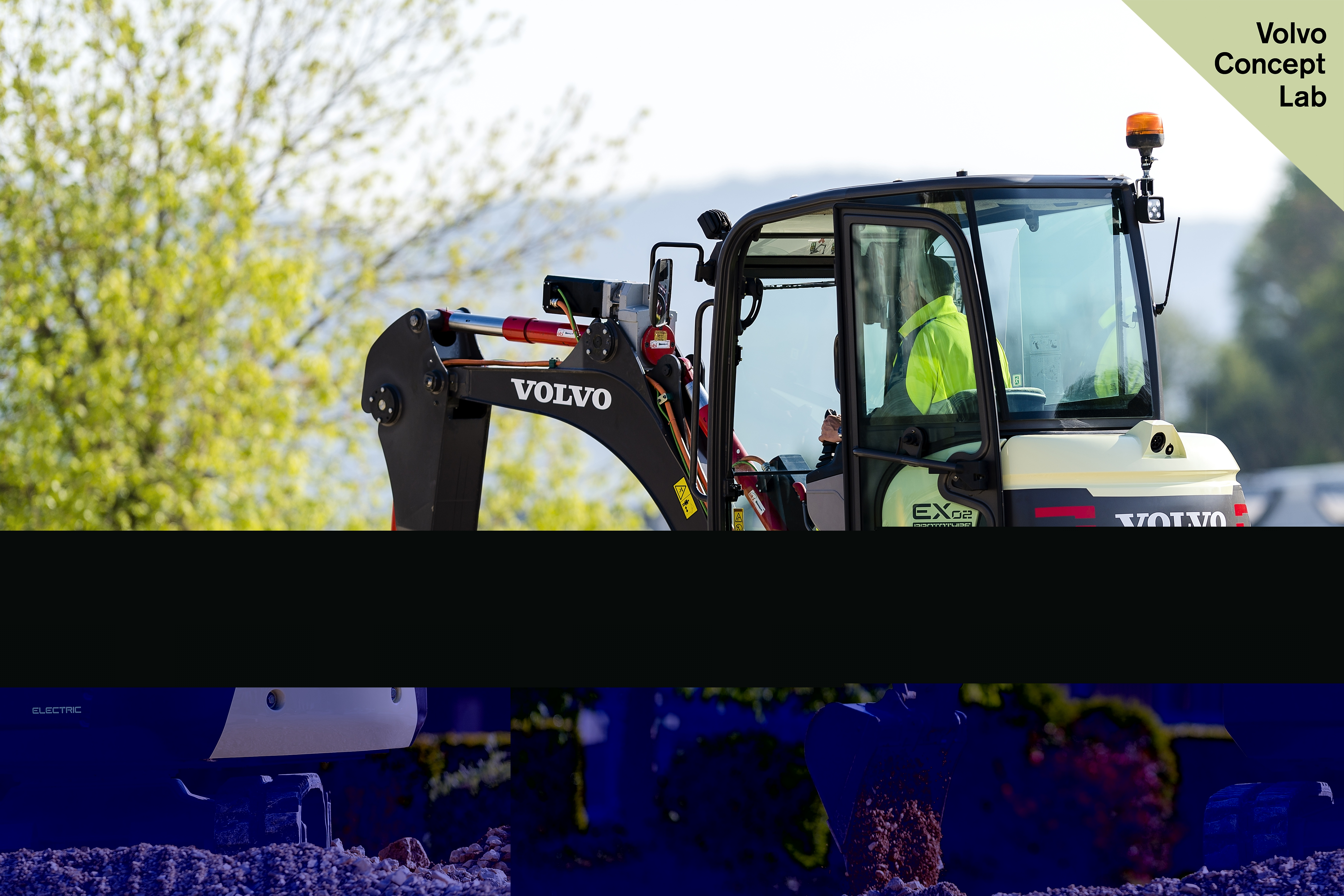
The driver of the charter bus stood outside the hotel in Trier, Germany, and waved at a passing local city bus. “I know the driver,” he told one of the assembled journalists waiting for the group’s ride to the nearby
His comments were a reminder of similar concerns being voiced by contractors and quarry owners about not getting enough skilled and willing-to-learn drivers.
The journalists were headed to Konz, about 10km along the lush Mosel River valley in western Germany, for a factory tour and the launch of two compact wheeled excavators. The EWR170E and EW220E were to be unveiled simultaneously with a larger crawler excavator, the ECR355, via video-link with Volvo CE’s manufacturing site in Korea.
Just under 1,000 people work at the Konz R&D and manufacturing site for the compact wheeled loaders L20-L50, wheeled excavators EW140-EW210 and EWR150 and crawler excavators EC160-EC250.
Add to this the EWR170E and EW220E. Meanwhile, the weather gods looked down favourably as some fireworks erupted and a huge white veil was drawn away to reveal the machines.
Volvo CE is sailing on the crest of an extremely good financial wave for the construction manufacturing sector in general. Half-year results saw sales grow 36% in the second quarter. Order intake rose 54%. Deliveries were up 49%. Europe is doing particularly well and company profitability is up.
Previously, global construction equipment manufacturers were seeing sales rise and fall on a 7-10-year cycle. No more, says Carl Slotte, Volvo CE’s Finnish-born president for sales in Europe, Middle East and Africa. Slotte, who has 22 years with Volvo CE, says these cycles happen with much shorter frequency.
The financial seas may look calm, but he believes the sector is in the middle of a perfect technological storm: automation such as driverless machinery, electro-mobility including fully electric vehicles and connectivity of all machinery such that they ‘talk’ to each other. In this respect, manufacturers are racing and struggling to come up with “total site solutions”.
The launch of the two compactor excavators is a response to a growing need for machines better suited to tighter working conditions in urban environments, coupled with a rising emphasis on sustainable construction methods, says Slotte.
In May, Volvo CE unveiled its EX2 prototype compact fully electric excavator during its Volvo Group Innovation Summit in London. The company claims that this “world’s first” and “concept” machine ticks the box for zero emissions. It is also claimed to be 10 times more efficient with 10 times lower noise levels and reduced total cost of ownership compared to its conventional counterparts.
Testing of the prototype will continue for now, he says. “We cannot tell when it will be available, if it will be available.”
Slotte also cautions about overblown sales expectations. Slotte also cautions about sales explanations, saying that demand for fully electric machines will only grow once legislation becomes tougher on sustainability adding that the time is not yet right.
From a quarry owner’s point of view, the issue is about improving site efficiency as much as environmental concerns. This, says Slotte, is where the real battle lies in the medium term for fully electric vehicles. They will work in conjunction with hybrid and fossil-fuel powered machines.
“Quarrying is now the most exciting aspect of the construction equipment manufacturing sector because it will be the proving ground for leading-edge technologies and the connected worksite,” he says. “Gone are the days of ‘bigger the load the better’. It’s now ‘small loads but more efficiency’.”
Slotte points out that no company, including Volvo CE, can create the connected worksite on its own. Development of tomorrow’s quarry requires what he says is the “transparent digital data world”. Information must be collected, analysed and shared transparently among trusting partners.
Good relations with end-users and dealers are central to development of the connected worksite because it is they who hold data on machine operations. An intense collaboration with many stakeholders will be needed, including machine end-users, software developers, supply chain partners and governments. Getting there requires a continuation of small steps.
Volvo CE’s EX2 is a case in point for this collaboration. It stemmed from the company’s earlier ELEXC research project starting in 2012, which was partly financed by the French government as well as various funding bodies in France. The company collaborated with six companies which all contributed towards the €7 million project.
One example of a small step is Volvo CE’s LX1 prototype, an electric hybrid wheeled loader. It is being field-tested in California by Volvo CE’s customer Waste Management – the largest environmental services and recycling company in North America. The machine can deliver up to a 50% improvement in fuel efficiency, as well as significant reductions in emissions and noise pollution compared to its conventional counterparts.
The LX1 is a ‘series hybrid’ that incorporates a driveline consisting of electric drive motors mounted at the wheels, electric driven hydraulics, an energy storage system, a significantly smaller diesel engine and new machine architecture, including a new design of the lifting unit. Volvo CE says that this combination allows the LX1 improved fuel efficiency. It has 98% new parts and can do the work of a wheeled loader that’s one size larger.
Volvo CE’s most visionary project by far is the HX2 autonomous (driverless) battery-electric load carrier. It was launched at
HX2 shares technologies and components from the entire Volvo Group, such as electric motors, batteries and power electronics and a new drivetrain. There is also a vision system that allows the machine to detect nearby obstacles and people.
Importantly, HX2 is part of an electric site research project that aims to reduce carbon emissions by up to 95% and total cost of ownership by up to 25%. Volvo CE teamed up with its customer
The project aims to electrify a transport stage in a quarry, from excavation to primary crushing and transport to secondary crushing. As well as a small fleet of HX2 machines, other prototypes will include an electric hybrid wheeled loader and a grid-connected excavator. Skanska will incorporate the demonstration machines into its operations and test the electric site concept at a quarry in western Sweden for 10 weeks at the end of 2018.
Volvo CE is coordinating the project and developing the machines and systems. The Swedish Energy Agency – a government agency for national energy policy issues – is part funding the project. It should be up and running within a year, says Slotte. But it remains a research project with no plans as yet for commercialisation, according to Volvo CE.
Regarding autonomous vehicles, Slotte says the object is not to make humans redundant in a quarry operation but allow them to do more productive work with an eye towards boosting efficiency. An autonomous vehicle, such as the HX2, if it ever makes it to market, will not necessarily replace a driver. Far from it, he insists.
A quarry operator will still need the brains behind the wheel, but not necessarily still sitting behind the wheel, or joystick in some cases. A driver in a future quarry will be a very different animal than today. He or she will be in a central control building or tower overseeing the operation of perhaps several autonomous vehicles.
Data capture and management, master planning of vehicle movements and coordinated planned maintenance. In short, business acumen will be a core competency of tomorrow’s drivers; they will be steering the business and not simply a vehicle, electric or otherwise. “They will not be physically part of the work flow but managing the work flow”.
This in turn should solve what the bus driver in Trier was pointing out - a shortage of drivers because nobody wants a vehicle-driving job.