Several of the major equipment manufacturers now offer sophisticated telematics packages fitted as standard to their machines. Caterpillar and Komatsu were amongst the leaders in this field, allowing a high level of access to a machine's systems and sub-systems for performance monitoring, maintenance management and geofencing purposes for example. To the customer this offers the chance to address fleet running costs and utilisation, reduce the risk of theft and increase overall efficiency. Customers can eve
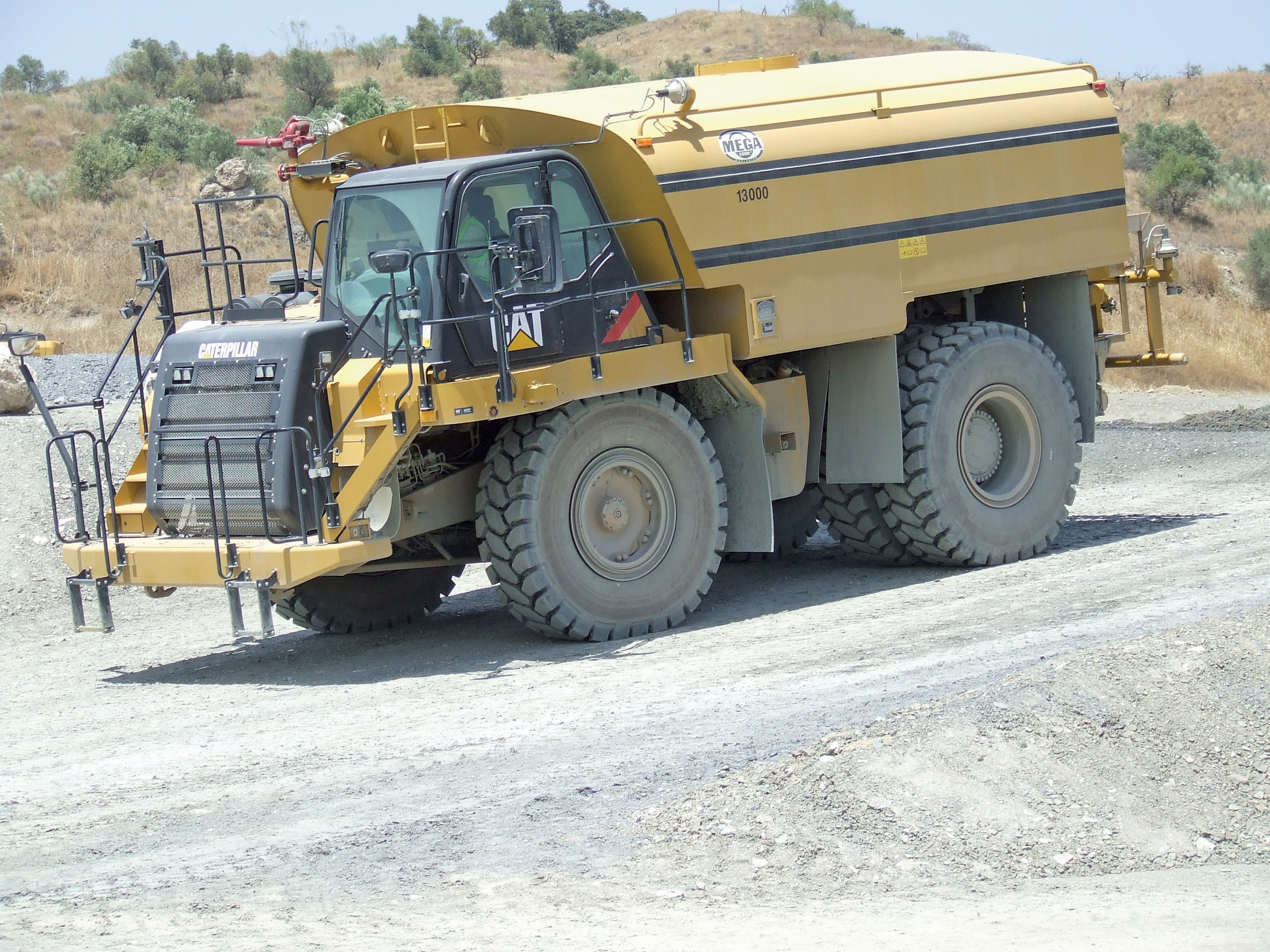
Caterpillar’s latest machines all come with the Product Link telematics package as standard
Sophisticated telematics systems offer major savings for fleet owners – Mike Woof reports
Several of the major equipment manufacturers now offer sophisticated telematics packages fitted as standard to their machines.Caterpillar recently unveiled its new additions to the Product Link telematics system, which will offer customers a range of benefits. Herwig Peschl is Caterpillar’s marketing manager for the EAME region and he said, “Product Link allows us to better track our equipment. All core construction and paving machines are shipped as Product Link ready.”
Isidora Arosemana is Caterpillar’s EAME Equipment Management Solutions Manager and he explained how the advances offered by Product Link have allowed Caterpillar to offer a new machine fleet package for customers. “It is a global marketing initiative and it goes across industries. There are five options, from basic to full.”
These range from providing access to valuable machine data, right up to full fleet management via the Caterpillar dealers, which allows for fixed operating costs for maintenance and repairs. Arosemana explained that this uses telematics to monitor and manage pieces of equipment, with plans in hand also for further development as the next generation technologies come to market and provide a deeper level of diagnostic capabilities. He said, “We can do some of these things now but some information we cannot get yet. But it’ll mean you won’t need a service technician on-site. You can use it to monitor an entire rental fleet and we’re working on a growing Cat-connected population.”
Hyundai Heavy Industries says that its web-based monitoring system HI-MATE can reduce running costs for fleet owners and maintenance departments. This web-based system monitors a machine and supplies additional data such as location and performance data. The HI MATE package offers detailed machine utilisation history including fuel consumption and usage, as well as GPS-based location and geo-fencing capabilities that ensure better theft protection. The HI MATE system allows the exact position of the machine to be determined to within a few metres. As soon as the machine leaves a specified area, HI MATE will automatically produce a warning message using either a GSM connection or email that allows the owner to contact the police if necessary.
The system communicates through the ORBCOMM satellite without extra charges for data transfer. Every day data on operating hours, engine hours, fuel consumption and the amount of fuel remaining in the tank is transmitted to a control centre at Hyundai. HHI operators and service technicians can access the data on a central website. The only requirement is that the HI MATE-equipped excavator or wheeled loader must be registered at Hyundai Heavy Industries. A particularly important point, especially for rental fleets, is the exact provision of maintenance dates. Actual working hours, engine and idling hours are monitored in conjunction with hydraulic attachments, so managers can use data to plan machine maintenance schedules more accurately. The HI MATE package is now standard on all Hyundai Heavy Industries construction machines weighing 14tonnes or more.
Meanwhile Komatsu’s KOMTRAX system has been recently updated as well, adding additional capabilities and combined with the firm’s extensive warehouse facilities, this allows the company strong customer back-up in key territories. According to
According to a representative from Komatsu Europe, “It’s easier for distributors to order the kits. They get a better price on it because we can reduce costs. Using KOMTRAX we can track machine hours so we know when a maintenance kit will be needed and we can plan our purchases.”
This also holds true for parts needed for repairs and the representative said, “Everything is packed so that the customer can make the repair the next day.”
Komatsu’s main rivals from Europe, Japan, Korea and the US are using similar systems to supply components and minimise delays for customers, while some of the larger Chinese firms are also adopting this technology. The cost savings for the supply chains in optimising components supply means that stock holdings can be optimised with high demand parts being easily identified. The lower cost of the component supply operation can be reduced for the customer as well, further encouraging companies to buy genuine parts rather than risking purchasing items from other sources.
An independent dual-mode telematic package is now available from ORBCOMM. The firm is offering its global satellite and cellular connectivity combined with a robust web-based analytics platform and state-of-the-art hardware designed for the heavy equipment market. This sophisticated system is targeted at OEMs, machine dealers, rental companies and fleet owners. Customers can receive data on engine hours, RPM activity, fuel level, and asset location anywhere in the world. In addition, this solution can read and analyse engine CANbus data for preventive maintenance. It also offers geo-fencing capabilities, sending alerts for unauthorised use outside of pre-designated work sites. The web portal is said to integrate seamlessly with OEM and dealer back-office platforms, allowing customers to gain visibility over their fleet, while increasing asset utilisation, productivity and service. The package uses ORBCOMM’s global dual-mode communications service and allows customers to connect to assets even in remote locations. Customers can optimise connectivity through ORBCOMM’s range of satellite and cellular services. The package works with ORBCOMM’s OG1 and next generation OG2 satellites and 3G cellular for global coverage. A key portion of the hardware is Quake’s Q4000 and QPRO dual-mode asset tracking and monitoring devices, which suit use with the system for construction machines.
But one of the major stumbling blocks with regard to telematics technologies at present lies within the machines themselves. Different manufacturers have developed their own system architectures individually so compatibility is an issue at present. This means that a customer with a mixed fleet of machines cannot use the one system to monitor performance and handle maintenance management for all the equipment. The manufacturers are working on solving the problem by offering a greater degree of compatibility but for the moment at least, it means only basic functions can be checked on one machine using telematics technology from another company. This will change though and in the future machines from one manufacturer may well be able to hook into the telematics system of another firm, so that an owner will be able to monitor a mixed fleet through one system.