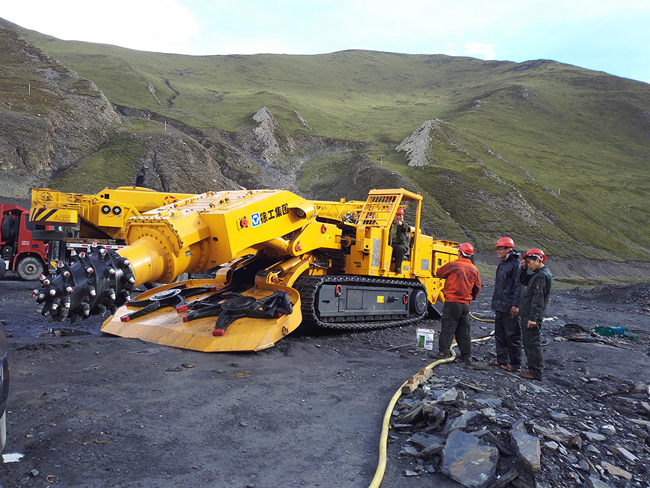
The project to build the right-hand bore for the Micang Mountain tunnel on the Sichuan-Shaanxi Expressway has taken 54 months to complete.
The tunnel was needed as the Micang Mountain has been a barrier to direct transportation at the junction of Hanzhong and Bazhong. This has blocked the major transport route between Sichuan and Shaanxi, preventing traffic flows across the region. Now that the 13.8km long Micang Mountain Tunnel is complete, there is a direct route that will cut journey times substantially.
Now that the project is complete, this is the third longest road tunnel in the world, and the longest in China. The tunnel on the Sichuan-Shaanxi Expressway will slash the travel time for travelling around the Micang Mountain from four hours to just 30 minutes now that drivers can go directly underneath.
The rare brittle rock mass in the high geostress area that the Micang Mountain Tunnel traverses has a high risk of rock bursts, landslides, fractures, cracks and even cave-ins. To maximise safety, this required real-time monitoring of the rock conditions throughout the construction operation. In addition, toxic gases released during tunnel excavation operations required workers to wear safety gear, adding to discomfort for personnel.
In order to overcome these difficulties and speed the construction work, mechanised cutting was selected as the main tunnelling method at the start of the project. XCMG’s Railway Equipment Division sent its two triple boom drilling jumbos to the project contractor: First Project Department under China Railway Engineering Group to assist in the tunneling operation. XCMG also supplied the mechanised cutting equipment that carried out the majority of the tunnel driving work. Both the drill jumbo and the roadheader machines performed reliably, despite the tough conditions, helping to ensure that the work was completed successfully.