Major new tunnel construction projects will, on completion, help secure more reliable journey times for hundreds of thousands of people across the world. Meanwhile, as Guy Woodford reports, leading ITS solution companies have been providing vital equipment for major road tunnels The Martina Tunnel Boring Machine (TBM), a 4,500tonne Herrenknecht Earth Pressure Balance Shield said to have a world record diameter of 15.55m, has required just under a year to build the first of two tunnel tubes for the 2.5km lon
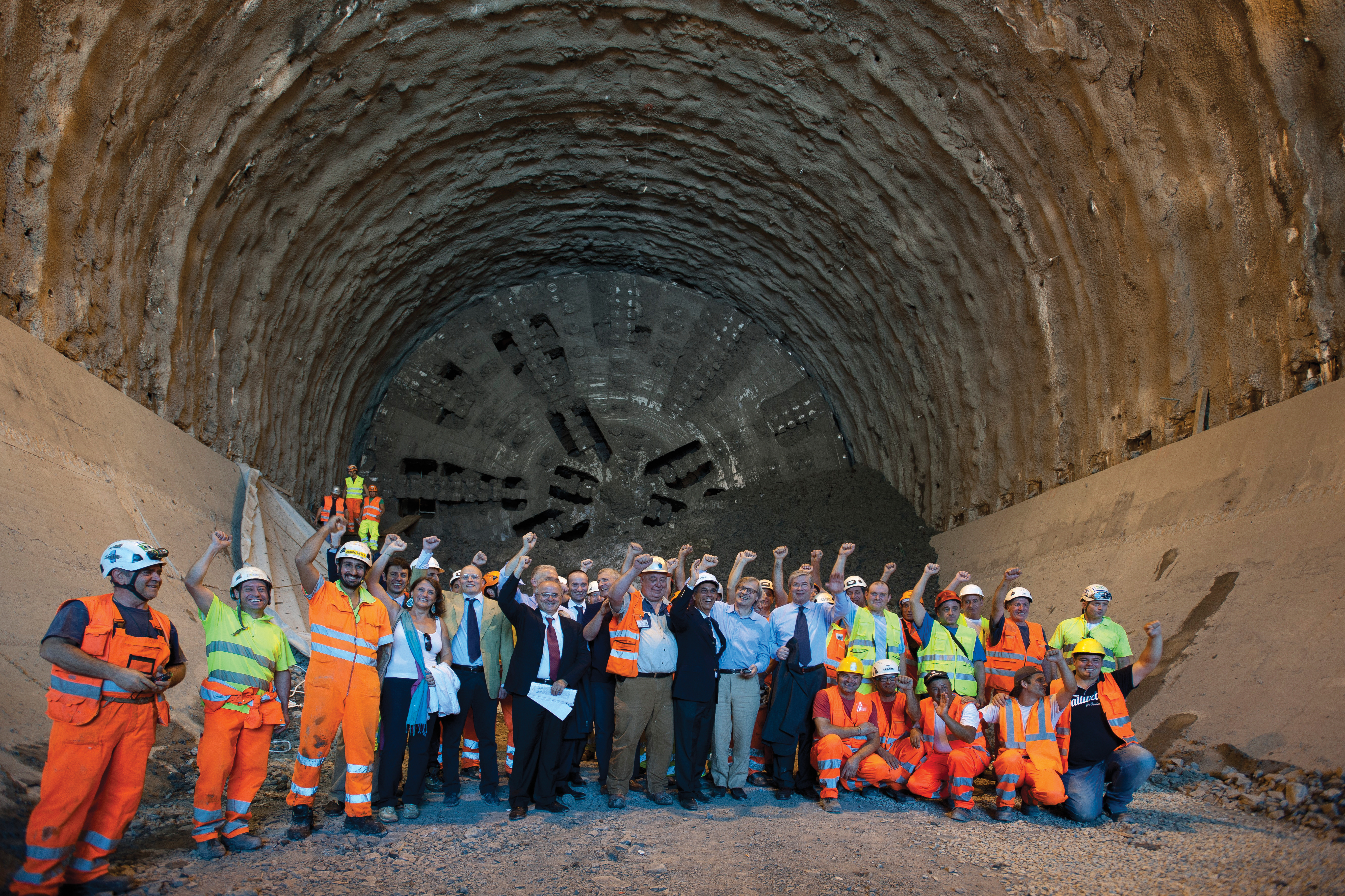
Workers celebrate the completed installation of the first of two two-lane tubes in the Sparvo Tunnel, part of ongoing route extension works on Italy’s A1 motorway
Major new tunnel construction projects will, on completion, help secure more reliable journey times for hundreds of thousands of people across the world. Meanwhile, as Guy Woodford reports, leading ITS solution companies have been providing vital equipment for major road tunnels
The Martina Tunnel Boring Machine (TBM), a 4,500tonneThe excavation task during the tunnel works has been, according to Herrenknecht, regarded as the most demanding part of the overall project, not only on account of its sheer size but also because of the prevailing geological conditions: the tunnel route comprised mainly clay, claystone, sandstone and limestone. There is also partial prevalence of firedamp. In order to achieve the requisite safety and speed during construction, Italian client
After recently installing the first tunnel tube, a Toto spokesperson told media: “A top advance rate of 22metres per day has confirmed the superiority of mechanised tunnelling when compared to conventional technology."
The first tube installation process is said to have involved the removal of 4,215m³ of soil – a major challenge for site management. Over the next few months, the Martina TBM will be turned around for the second tube which is spaced 20m away.
"This machine was intended to set new standards, including with regard to its features for particularly gaseous soil,” said Herrenknecht project manager Alexander Ell.
In partnership with Toto and with support from local authorities as well as the Universities of Bologna and Turin, Herrenknecht developed a complex safety system for the Sparvo Tunnel project. This included the use of explosion-protected equipment, a fully-enclosed conveyor belt, a permanent fresh air supply to all areas, and the permanent monitoring of housing tightness and gas concentration. “The concentration of methane at the tunnel face was so high that fresh air had to be transported to the excavation chamber over longer periods of time", said Ell, who added with satisfaction: “So far, our new system has worked just the way we have anticipated."
The A1 extended alternative route between Bologna and Florence is due to be completed before the end of 2013.
Remaining in Italy, in August this year works were completed to reinforce the Varzo Tunnel on the Italian border with Switzerland. Ceprini Costruzioni (CC), an Italian contractor specialising in railway maintenance and construction, was contracted to perform the three-phase project, with the final phase requiring all traffic to be halted to allow for the installation of two-hinged steel ribs every 1.75m, anchored to ties with a C-shaped fastening element (totalling 44 elements), and the laying of a 10x10cm, 6mm diameter wire mesh covering up to 18cm of fibre-reinforced shotcrete.
One of the major challenges of the third phase was to cut around 20cm deep and 40cm wide into the crown of the tunnel in order to create the inserts for the steel ribs. A solution to the problem was said to be offered by
While evaluating solutions, a hydraulic breaker for the application was immediately discarded by CC due to the length of time associated with its use and the lack of optimum precision, with the possible introduction of dangerous vibrations into the crown near the deteriorated area.
CC decided to order and utilise a pair of Komatsu PC 138 US excavators and two Simex TF 800/V rotary cutters. The cutters were equipped with drums measuring a width of 400mm and diameter of 1100mm, and fitted with 144 Betek VC 33 bits with a 22mm bit holder.
Both cutters were said to have proven highly productive and reliable and were operated without interruption for 164 hours each. Their claimed excellent performance contributed to the success and on-time completion of the job. Summing up the project Franco Ceprini, founder and president of CC, said: “The equipment supplied by Simex played a critical role because it allowed us to install five steel ribs a day. The rotary cutters were even used horizontally by changing the direction of the bracket in order to allow cutting for positioning of the ties for the tunnel walls."
In South East Asia,
AMG's international sales & marketing director Sara Bullock said the firm’s CCTV surveillance solution for the tunnel complex had been engineered to give maximum resilience and performance.
“The solution operates within a dual redundant configuration with video insertion points providing analogue video, data and Ethernet capability,” explained Bullock. “The AMG’s 3700 series solution has a proven record in tunnel implementations, such as the new Hindhead Tunnel in the UK. The solution operates with two single mode fibres in ring configuration. The benefit of this system is that operations are robust and resilient and no signals are lost in case of a failure or a fibre breakage.”
Bullock said that all signals from AMG are routed to the Central Intelligent Transport System Centre (ITSC) Control Room, as well as to the control room in the facility building on-site. She added: “Guthrie conducted vigorous factory testing and we understand they were delighted with the resilience the solution offered. They were also impressed with the extended MTBF (Mean Time Between Failure) longevity results, and the resilience to the environmental influences."
The Woodsville Tunnel is part of a US$105.05 million upgrade of the Woodsville Interchange that began in 2008. It consists of three new road tunnels linking Upper Serangoon Road to Bendemeer Road, Serangoon Road to Upper Serangoon Road, and MacPherson Road to Bendemeer Road. The new tunnels are expected to decongest the affected roads and cut down commuter travel times. AMG says motorists using the Woodsville Tunnel can expect smoother traffic flow and times savings, particularly during peak hours, due to the improved traffic flow. The company gives as an example of a motorist travelling from Upper Serangoon Road to Bendemeer Road who will have their travel time cut from 10 minutes to 4 minutes by using the new Woodsville Tunnel during peak hours.
Elsewhere in South East Asia,
Hsuehshan tunnel is South East Asia's second longest road tunnel and comprises three independent tunnels (one pilot tunnel, one Westbound tunnel, and one Eastbound tunnel) stretching 12.9kms through Hsuehshan Mountain, the second highest mountain in East Asia. Moxa says emergencies occurring inside tunnels of this length can be disastrous, especially a fire-related incident. To minimise casualties during an emergency, a traffic control system consisting of two entry gates and two exit gates has been deployed to lower the appropriate gates in the event of an emergency to effectively divert traffic and prevent vehicle entry into dangerous areas.
Moxa's NPort 5230 device servers connect RS-232/422/485 serial devices for remote control/monitoring, while the EDS-508A-SS-SC Ethernet switches feature Turbo Ring and Turbo Chain technologies for recovery times of less than 20 minutes at 250-switch load.
In the United States, Austria-based
The IDS 2.0 non-invasive detection system will be linked to 14 fixed roadway cameras for incident direction for two-way traffic in the vehicular tunnel, and up to six infrared intrusion detection cameras in the ventilation tunnel, said by Kapsch to enable tunnel operators to provide cost-effective continuous 24/7 surveillance and monitoring.
“Incident detection in tunnels and on the open road is critical to maintaining traffic flow and keeping drivers safe,” said Chris Murray, president and chief executive officer of Kapsch TrafficCom IVHS.
Kapsch says its IDS 2.0 processes the video stream from existing cameras for automatic incident detection, traffic data gathering, and movement detection. Using video analysis, the system also provides automatic camera calibration, wrong direction detection, slow and stopped vehicle information, and lost cargo and pedestrian on road notification. It also alerts tunnel operators to smoke, as well as movement in non-traffic areas. Further capabilities of the IDS 2.0 include the provision of traffic jam information, vehicle speed measurement, vehicle classification (two classes) and vehicle counting, vehicle distance measurement and statistical data. Intrusion detection in the ventilation tunnel identifies both people and large animals.
First introduced for what
Sandvik iSURE software consists of four modules: Tunnel, Report, Analysis and Bolting. Bolting is available for the Sandvik DTi series jumbos only.
In contrast other similar software, Sandvik says its iSURE software uses what is perceived to be the most critical point of the round: the end where the blasting initiates, as the basis for the whole planning process. The drill plan is thus implemented to fit with the blasting plane, meaning that the hole bottom spacing and the burdens are adjusted accordingly, and the used charge defined and the cracking zone examined.
The iSURE features a tool for preparing and managing the blasting plan. Based on information filled in, explosives used in different parts of the pattern; their relative strength, degree of charge and fracture zone; the total consumption of explosives per round; and the charge per delay detonating at a specific time can be illustrated. This is said to make plan modifications easy, while also offering enhanced smooth blasting and vibration control efficiency – a major benefit due to increased tunnelling in urban areas and city centres.
The iSURE 6.5.0’s pull-out analysis is said to combine information on two sequential rounds, accurately showing the pull out of the round under investigation. The results of the analysis are then traced back to the drilling pattern, meaning that the plan can be modified accordingly if needed. This is said by Sandvik to allow for significant reductions in excavation costs while, at the same time, increasing productivity.
New MWD (measuring-while-drilling) items such as air flow, and feed pressure and rotation speed settings, are said to be another feature of the iSURE 6.5.0. Its supply of 19 different MWD parameters are said to be more than any other similar software on the market.
No video provider was found to handle the given URL. See the documentation for more information.