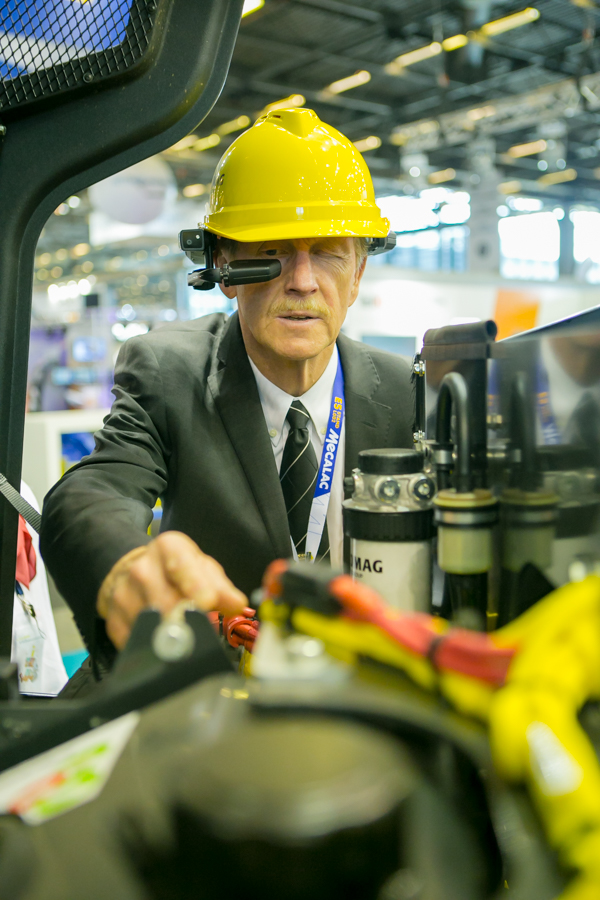
The focus here is not digitisation for its own sake. Rather, it is an attempt to reduce downtime by linking a maintenance operator on site, wearing a construction hard hat with a built-in camera and a “heads up” mini-screen in view, remotely guided by a Bomag expert back at the company’s headquarters.
Problems on site can be talked through, whether the machine is 1km or 1,000km away. Bomag experts can be linked to the exact location on the machine where the problem needs to be analysed.
The operator talk directly to the Bomag expert through the connected helmet and the hat-mounted cameras then allow the head office engineers to see what the problem is in real time.
They are in full visual and oral communication as if both are standing there together on site.
The expert can also draw indicators onto the “heads up” screen to “physically” point to the areas that need to be examined by the on-site operator out in the field.
The system is still in development but is currently being field tested.
The digital service concept also includes the BOMAG service app for iOS or Android.
With technical data, operating and maintenance instructions, spare parts lists and videos with quick guides, the user has everything to hand – including addresses of BOMAG dealers nearby.