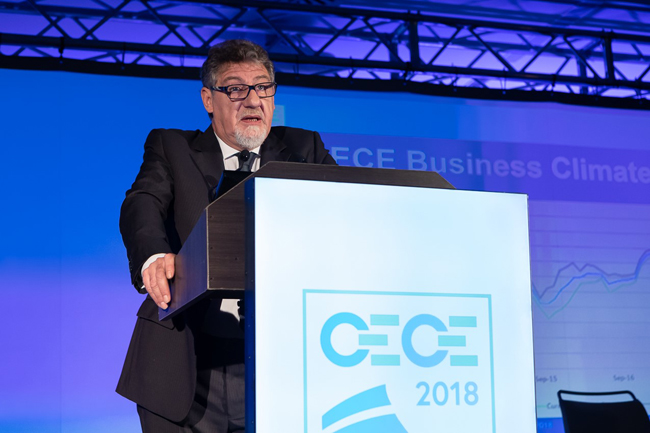
For many contractors, digitisation is key for improving on-site operational efficiency. But it may be time to take stock of progress and examine what does and doesn’t work.
That is not to say that the anchors should be thrown out to halt development. Far from it. In the past eight months, the
“This study is another step of CECE’s investment into digitising our industry,” said Enrico Prandini, CECE president. The goal remains to “facilitate the uptake of digital construction machinery in order to reap the benefits of data on productivity, safety and sustainability, our three major challenges”, he said during his opening speech to the 175 delegates to the event that was hosted by the Italian construction equipment association
“If there is one key takeaway from this project, it is the need to change business models to unlock the value of data.”
The digitisation of machinery directive is working well for regulating safety and bolstering the single internal market, and allowing for innovation of equipment, said Barbara Bonvissuto, head of the advanced engineering and manufacturing systems unit for DG Grow within the European Commission.
But there remain concerns, such as cybersecurity. This and other issues will be sitting in the in-tray of the next commission after elections in the new year. Bonvissuto reassured the delegates that the construction sector in general and the CECE in particular will continue to be regularly consulted.
Computers that dig
Digitisation is more than simply grafting the latest Internet of Things technology onto machinery and giving the operator a fancy touchscreen, said Luca Chittaro, professor of human-computer interaction at Italy’s University of Udine and who started his career looking at digitisation in the aviation sector. “How do we design the cockpit of any machine to benefit the customer in some way?"
This human-machine interface, or human-computer interface, raises serious issues for operator and owner, he warned. As a modern airplane is a computer that flies, will the coming generations of construction equipment be computers that dig?
The answer depends on the stakeholders in the construction sector, he explained. Whatever they decide, they will have to ensure the physical reliability of equipment, ease of use for the operator and that safety remains paramount – “nobody gets hurt”.
Machine designers and software developers will have to be aware of several HMI/HCI principals. One, called affordance, is whether the design and control of a feature looks like what it will do. In other words, is it obvious to an operator that if you push a certain button that that is the right button for initiating an action, whether it is stretching out an excavator’s boom or raising a bucket.
The feedback principal is whether by pushing the button an operator feels as if they have actually initiated the desired action. For example, is there a physical click or similar sound to tell the operator that, yes, that action has been initiated?
Chittaro said the world of human-machine interface is full of examples of operators pushing a button not knowing that the initiation has taken place and so he or she keep pressing that button. In the worst design cases, this has led to repeated actions being initiated to the detriment of the original intention. An excavator may take several buckets of material out of the ground instead of only one intended.
But even with good feedback from initiating an action, an operator might wish to be reassured that the action has taken place. This seeing-is-believing concept is called the situation awareness principle. Has something actually changed because of the initiated action?
For human-machine interface to be efficient, there must be some standardisation of languages for the operator to understand across many functions controlled by a computer. This can be words, icons and functionality. Consider that one type of button for initiating a task works well for many of a machine’s functions until the machine is running at a particular speed or being stretched to the limits. Vibrations, shakes and movement means an operator may have difficulty locating the switch when needed.Reading instructions may also be difficult. This was the case in the aviation industry when planes were flying in turbulence.
Also – and more important than previously thought – digitisation should make the job more interesting for an operator. This raises the issue of just how much automation should a machine have and to what degree should an operator have to over-ride that automation. In this respect, the operator will be key to digitisation, he said. It might be that some number of tasks should be left to an operator at which they are particularly good.
These last points highlight “the three ironies of digitisation”, he said. The first is that you digitise to reduce human error, only to increase computer error. Secondly, you may digitise to relieve an operator of difficult tasks, only to make his work harder because of increased use of monitoring many more details.
A third irony is that digitisation may make an operator computer literate but reduce his skills to manually take over a machine when automation fails. To this end digitisation may “take [an operator’s] eyes and mind off the road”, said Chittaro.
AI versus operator
During a panel debate on human-machine interface, speakers noted that there can be a struggle between artificial intelligence experts and operators. The AI people see the advantage of having full automation of a machine. Meanwhile, operators wished to retain some sort of “physical feeling” of control over the machine and for the machine’s performance.
An operator is happy feeling the machine, said Frederico Pagliacci, development vice-president of drilling and foundation equipment manufacturer
Getting right this balance between operator and automation will ensure the most efficient use of the machine, said Xavier du Boys, chief executive of French equipment rental company Groupe Kiloutou. It must be remembered in the rush to automate machines, that there are still millions of operators in Europe between 45-55 years old who grew up with feeling their machine’s performance intuitively. Training to handle more automation should reflect these people’s skill levels and desirability to move toward more automation. To this end, there needs to be a lot more cooperation between software developers and machine owners and operators.
Robert Laux, senior vice-president for operations at
A lot of cooperation between software designers, machine manufacturers and the machine owners and operators is already being done, noted du Boy. However, this so-called “participatory design” has perhaps relied too much on an operator’s input being collected from too formal an interview. There should be more on-site discussion where everyone has their heads around a machine and sees for themselves what the issues are for an operator.
Chitarro agreed, saying that designers should perhaps have a little more humility when it comes to taking into account an operator’s concerns.
Also, noted Chitarro, with all the data that is even now being collected on a machine’s performance, the issue of safety is rarely talked about in relation to operator performance. For operators, it can be a case of who is watching me and what data is being collected about how well the machine is being operated safely. This is where there needs to be some transparency about data sharing to make the operator feel comfortable that nobody is looking over his or her shoulder in an aggressive way.
It was good to see, said both Pagliacci and Laux, that contractors appear to be increasingly interested in, and ready to commit to, more high-level training for their operators. At the end of the day, digitisation and automation should be about not replacing an operator but making their lives easier, said Prandini. It is best the digitisation comes first to large, simple repetitive procedures and jobs.
Buyer beware
The global value of auctions and online sales of new and used heavy equipment and attachments is steadily rising. But there can be issues for contractors that go down this route. Know your purchaser and do your homework on the product, said the two speakers in a panel discussion about digitisation of sales.
The warning should be heeded to most rigidly by small- to medium-sized contractors who think they are getting a real bargain, said Felipe Urrutia, director of strategic accounts for Europe within Canada-based global auction house
While brand loyalty may be breaking down, brand awareness is getting more important in this age of internet sales, be they at on-site auctions or from websites. Purchasers should ask about servicing histories, trustworthy inspection reports and any guarantees being offered. Ritchie Bros, he said, offers all this, so online buyers can be reassured that the auctioneer is backing up its product.
Michele Vitulano, managing director of Italian attachment manufacturer
This is where buying from a trusted OEM reduces risk and increases value for money. Sadly, otherwise, safety is compromised. Don’t forget, said Vitulano, the contractor will be responsible in the event of a tragic accident.
Level playing field?
China’s Belt and Road Initiative may be one of the largest global infrastructure strategies ever set out but it is also one of the most threatening to European manufacturers and contractors.
The tactic is to replace western technology with that of China, said Jost Wuebbeke, an analyst with Sinolytics, a Berlin-based consultancy that provides research, analysis and advice to international firms and investors about China’s strategic development.
It is part of moving china from being a global factory to a global industrial superpower by 2049, the centenary of the communist takeover of China’s government, he said. The construction sector will not be immune from this strategy.
Belt and Road is focused on investing and physically developing - if not outright ownership of - ports and road networks from China to South East Asia and from China across northern Asia to the edge of Europe. The object is make it easier to get Chinese products to these markets and these markets to sell into China.
Financing port and road development is through low-cost loans to governments, many of which likely won’t be able to repay the debt. In the long term this may be of little consequence to China given that it will control the trade routes.
Wuebbeke said an analysis of these construction contracts – as much as can be done given transparency is not very high – is that 90% are carried out entirely by Chinese contractors and their extended Chinese supply chains. There has been, and will continue to be, little business going the way of European contractors, at least outside Europe, he said.
Within Europe, China will likely secure few major contracts because it fails to adhere to EU procurement legislation, such as for the use of local contractors. For a recent major road deal with Montenegro – not an EU member – China was able to stipulate that local subcontractors, should they be used, must have 70% of their equipment purchased from Chinese manufacturers. This would not be acceptable under EU procurement rules, said Wuebbeke.
At the moment, he said, Chinese equipment manufacturers are as competitive as they are with European companies because they are highly subsidised. This includes Chinese makers YMCG, ZoomLion, Sany, Shantui and Sumec. In some cases, net losses are wiped out by subsidies, said Wuebbeke.
This situation is sometimes “crazy”, said Philippe Citroën, director general of UNIFE, the EU association of rail manufacturers. On the one hand, it is getting harder for EU manufacturers to sell into China because of restrictive ownership rules. On the other hand, EU taxpayers are paying for Chinese contractors using only Chinese construction equipment to build infrastructure in Europe.
During a panel debate, Citroën cited the example of the controversy over the recent deal by Croatia to award construction of the Peljesac Bridge to China Road and Bridge Corporation. CRBC undercut EU infrastructure consortia by a massive 30%.
Citroën said it is usually very hard to prove that subsidisation goes on. Meanwhile, Howard Dale, chairman of Liugong Europe, said there can also be misunderstanding about what constitutes a subsidy – something which, he noted, his parent company does not get.
It is not unusual for a major manufacturer to get government grants and money to move an entire plant out of an area which has been transformed over the years from an industrial belt into a green belt due to urban sprawl. This, he said, goes on in many countries and is not particular to China.