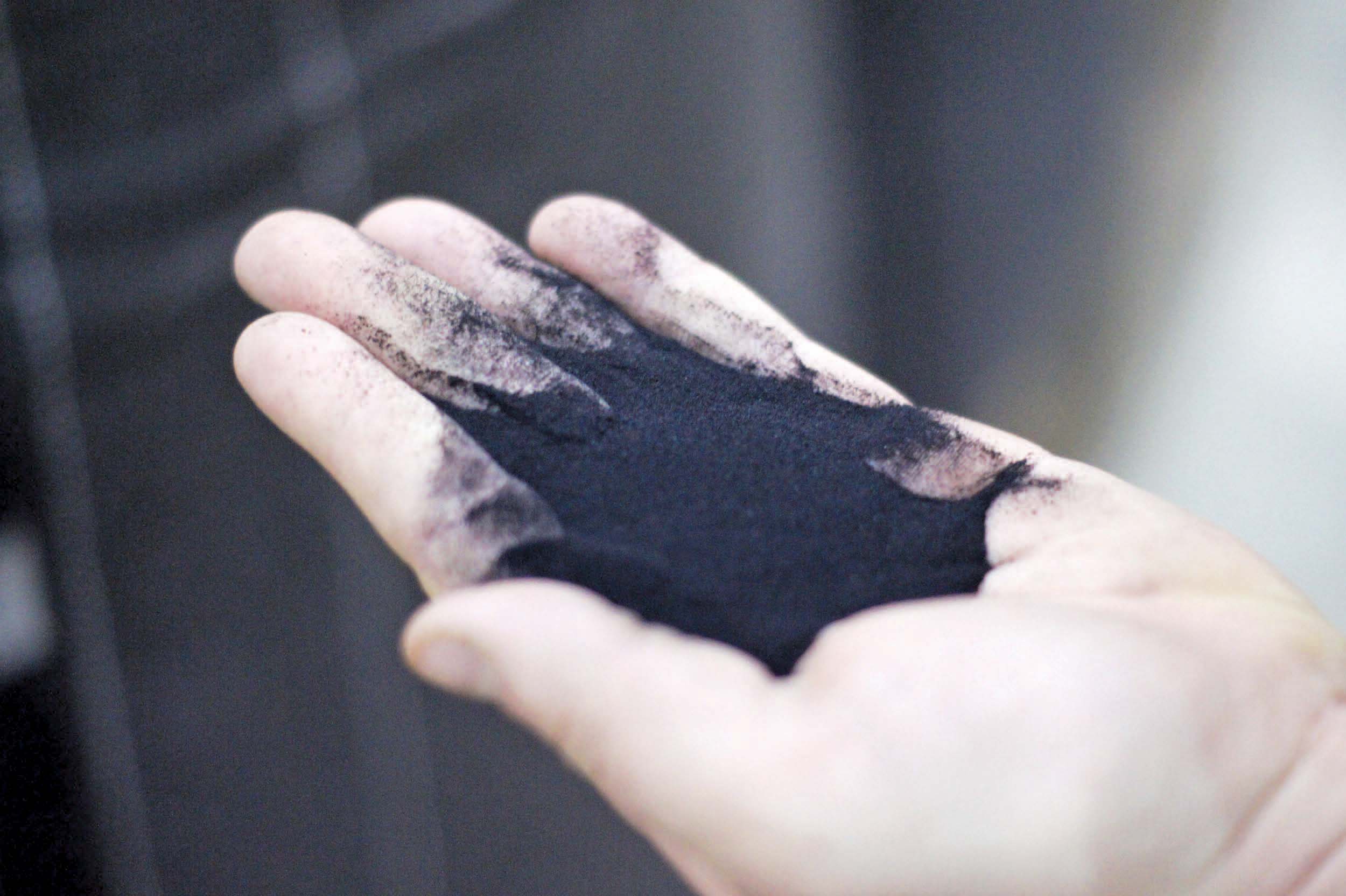
Rheopave had developed its X10 additive, a blend of reactive polymers and other elements, to work with Lehigh’s MicroDyne micronized rubber powder. It overcomes two problems currently experienced with rubber-modified asphalt, according to Lehigh’s director of coatings, asphalt and construction materials Ryan Alleman.
“The first problem is that rubber does not become part of the asphalt so it settles out. So the contractor needs to be near the plant or to fit his equipment with agitators, which is expensive,” he said. “The second issue is that base asphalts have become more robust because refiners are taking out the aromatic oils for other uses.
This means that ground tyre rubber isn’t able to modify the asphalt as well as it used to.”
Rheopave X10 works by generating active sites on the rubber particles allowing a continuous network structure to be created, suspending the rubber throughout the binder. This means it is stable in storage and transportation.
Performance benefits from using the combination of Lehigh’s MicroDyne and Rheopave X10 are longer fatigue cracking life and also enhanced elastomeric properties allowing the pavement to combat cold cracking, according to Alleman. It is also easier to handle as the mix is less tacky than one made with ground tyre rubber alone.
Though this is a new product, it is already available commercially in Florida, with over 18 companies around the US currently involved in testing it. Lehigh has also begun promoting it in Europe, Japan, Korea and Brazil. “We will initially be targeting countries that have experience of rubber-modified asphalt already,” said Alleman.
In terms of cost, this product could offer savings over conventional SBS-modified bitumen, although that will depend on the prices of SBS and how robust the base asphalt is and therefore how much additive it needs. SBS prices have historically been volatile, although they are currently low as there is no shortage in supply.
Hot mix plants looking to use the combination of Rhepave X10 and Lehigh’s MicroDyne may need to invest in modifications. “It does not require a high shear mixer like that which is needed to process SBS however it does require a terminal blender and a saw-toothed blade such as a Cowles Mixer blade,” said Alleman.
“Companies that have blenders can expect to outlay less than $5K in plant modification to process Rheopave.”