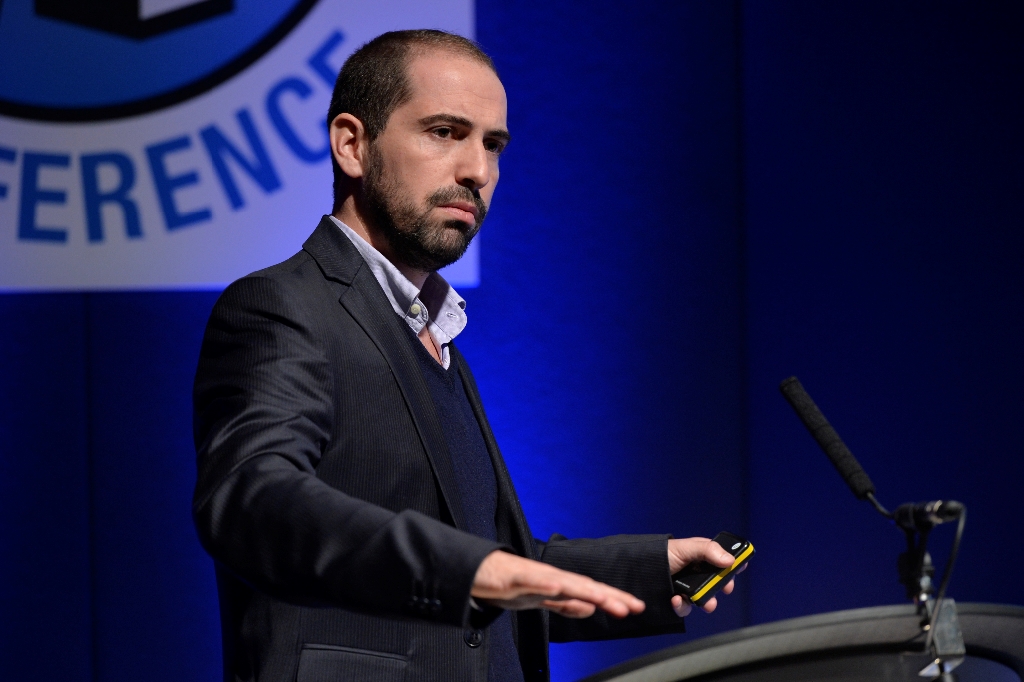
A new way to introduce end-of-life tyre rubber into asphalt mixes could be the key to diverting more tyres away from landfill, according to Dr Davide Lo Presti, principal research fellow at the Nottingham Transportation Engineering Centre (NTEC) at the University of Nottingham.
The new technology involves pre-treating crumbed rubber so that the crumbs are swollen before they are added to the asphalt mix. The treatment reduces challenges with workability and compaction and means that more rubber can be used and there is no need to buy new plant or update existing equipment.
“The good news is that we can use a very good amount of rubber,” said Lo Presti. “In some projects, there are claims that it accounts for 4% of the mix which is massive. With the wet process or the traditional dry process, we were looking at 0.5 to 0.6%.”
Some regions already use a significant amount of end-of-life tyre rubber. “The big markets are in the US, the West Coast in particular, China, India, Spain and Portugal and some Eastern European countries,” said Dr Richard Taylor, global product technology manager at
There are several ways of combining end-of-life tyre rubber with asphalt including the dry method, the wet method, terminal blends and hybrid terminal blends. Until now the methods that deliver the most performance improvements also require the most upfront investment to modify plant and equipment.
The dry process sees crumbs of rubber added to the mixing plant as a substitute for a very small proportion of the aggregate, with no modifications to plant required. With this method there is limited interaction between the rubber and bitumen. The downside is that the crumbs soak up bitumen from the mix, reducing workability, making it difficult to compact and sometimes leading to ravelling of the road surface.
The wet process requires the crumbed rubber to be mixed with the hot bitumen and the mixture then held at a temperature of around 190°C for 45 minutes so that the rubber can truly blend with the bitumen. This requires a specialist blending unit. The rubber modified bitumen is then added to the aggregate in the mixing plant in the normal way.
Specialist suppliers, such as Shell Bitumen, are working on ways to make rubberised asphalt easier to work with. “The latest developments in crumb rubber technology attempt to address some of the issues surrounding its manufacture and installation, in particular technologies which improve storage stability and reduce viscosity resulting in lower storage and handling temperatures,” said Taylor. “In Shell we have filed patents for lower viscosity, stable crumb rubber modified bitumen as well as developing technologies which address odour concerns which arise from time to time when using crumb rubber in bitumen.”
One of the pre-swollen products Lo Presti has been working with is RAR (reacted and activated rubber), such as RAR X from SHRP Corporation which is made from fine crumb rubber, plain bitumen and an activated mineral binder stabiliser. It can be added to any kind of hot mix asphalt, replacing part of the bitumen and can be added directly to the mixer and yields the same kinds of performance improvement as the wet process.
Lo Presti is about to embark on a research programme for the Swiss Government where he will work in collaboration with another research organisation, a tyre recycling company, asphalt producers and equipment manufacturers to look at different types of wearing course that contain rubber. The pre-swollen crumb rubber will be one of the technologies tested.
Lo Presti, who has long been an advocate for the reuse of end-of-life tyre rubber, said he believes that political intervention is the only way to increase the use of waste rubber. The asphalt industry already has an accepted technology which produces similar performance improvements – polymer modified bitumen (PMB) – so without incentives it makes no sense for them to invest in change.
“Unless there are policies that say we need to reuse as much as possible, and this is recognised with economic incentives, it’s not going to happen,” said Lo Presti.
The next challenge for markets where rubber has been widely used in pavements could be how the asphalt behaves when recycled. “There are some concerns that RAP containing crumb rubber - or for that matter polymers - could lead to difficulties in mobilising the bitumen in future recycling of the RAP,” said Taylor. “The higher viscosities may lead to material which is less readily miscible in bitumen than unmodified bitumen and there are also some concerns regarding using RAP containing CR through a mix plant in terms of emissions.”
However, the way we analyse and use RAP will become more sophisticated in the future, suggests Taylor: “Currently, RAP is largely considered to be a mixture of aggregate and bitumen but as new materials containing a much wider range of additives start to arise during road recycling, the view of RAP will evolve to make the best use of the additives present in the RAP”.