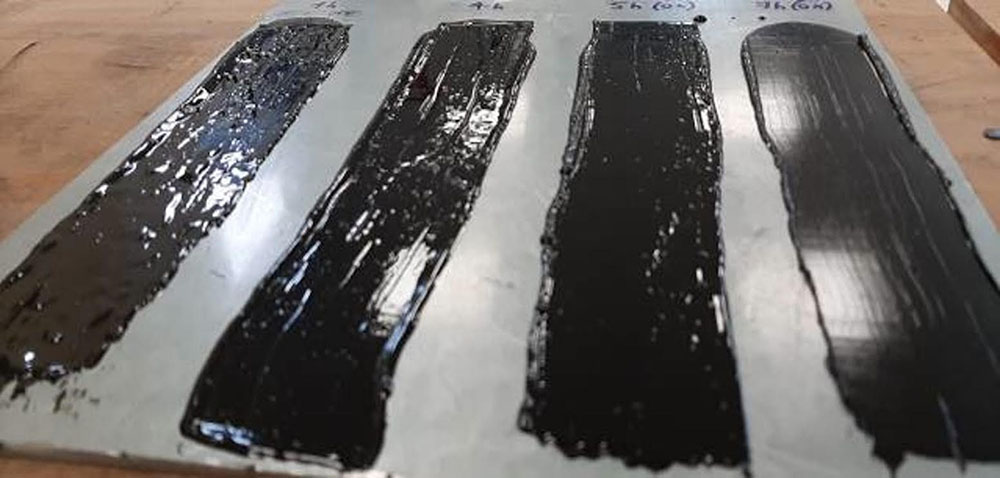
Italian bitumen plant specialist Menestrina has invented a new process which turns crumb rubber from waste tyres into a binder that can be used to replace some of the bitumen in an asphalt mix.
The Oxyboost process is based on air blowing technology which passes a stream of air through bitumen causing a chemical reaction which is part oxidisation and part dehydrogenation. Menestrina has been supplying air blowing plants for roofing industry bitumen for many decades and, in the last 20 years, for the road industry to create multigrade bitumen. Oxyboost, which has a patent pending, adds temperature and pressure into the process in a closed loop reactor.
There are many possible applications for the technology, according to Menestrina CEO Massimo Menestrina. Breaking down waste tyre rubber is one the first applications that the company is investigating using Oxyboost, working in partnership with bitumen laboratory MOPI.
“The Oxyboost process breaks the bonds of the molecules that form the rubber in the same way as when pyrolysis happens, but at a much lower temperature,” said Menestrina. Initial trials have worked at around 300°C but it may be possible to lower that to 250°C for industrial production, said Menestrina.
This way of using recycled rubber in roads is energy efficient, expanding the ways recycled tyre rubber can be used in asphalt. Traditional approaches see crumb rubber added straight to the mixer - the ‘dry process or blended earlier with the bitumen at high temperatures - the ‘wet process’. Menestrina’s process is different: it changes the rubber into a different material by end-of-life rubber into oil-extended bitumen whose final hardness can be adjusted up or down.
Menestrina and MOPI have been working on the new process for around three years. Initial phases saw the creation and testing of a laboratory scale unit. Now Menestrina has created an industrial unit which has undergone some initial tests and will now be upgraded for the next round of testing.
Another benefit of the Oxyboost process, said Menestrina, is that it reduces the smell of sulphur which is sometimes present in rubber-modified bitumen. The sulphur is mostly transformed into sulphates which have no smell.
Menestrina is aiming to have a commercial unit ready to market in one to two years. The company’s vision is that one of these plants could be placed at every asphalt manufacturing facility, using waste rubber to create a binder, reducing the use of virgin bitumen.