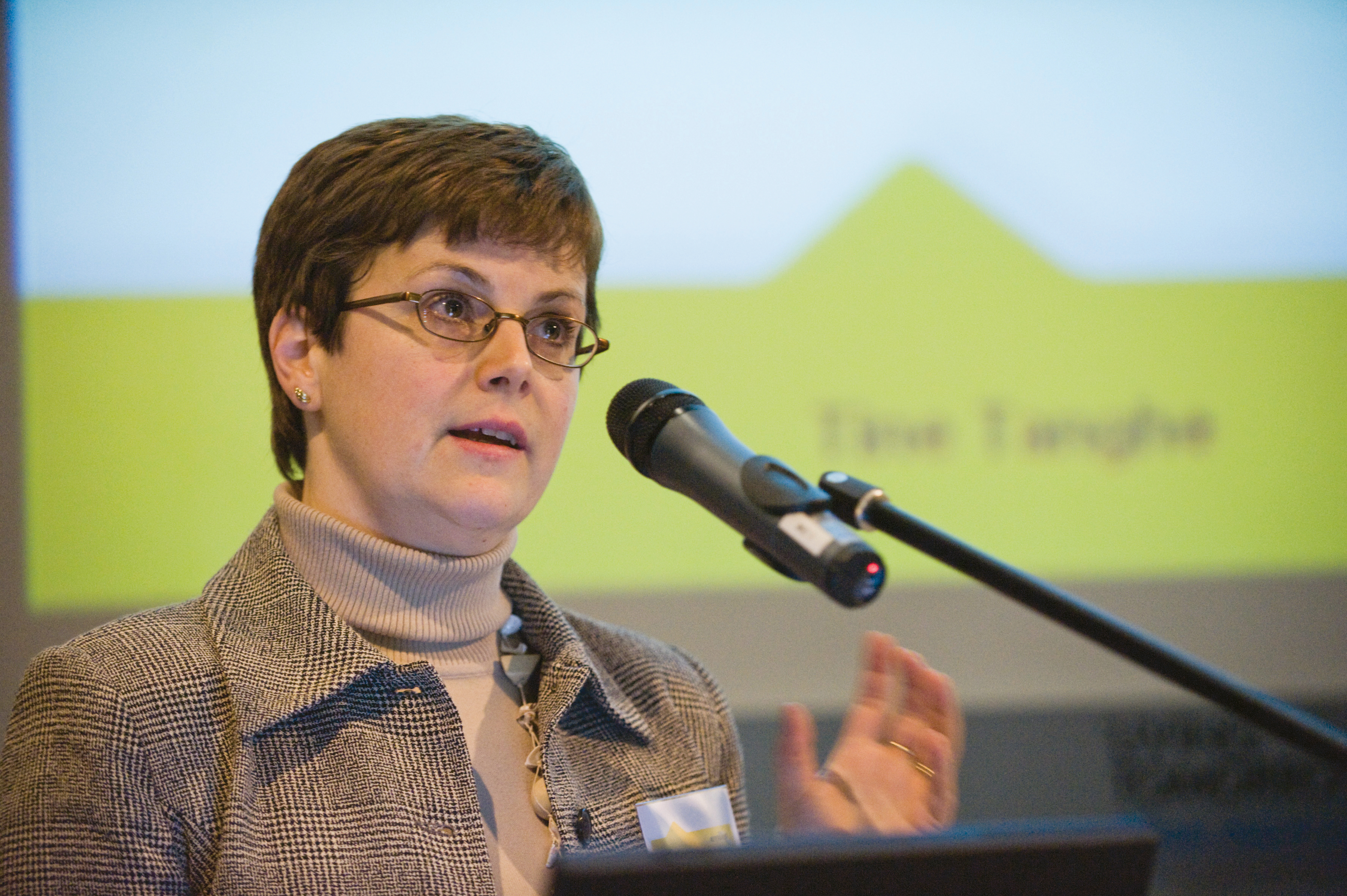
From chip fat to banana bags, the race is on to find new bitumen additives which will solve two problems with one solution: replace diminishing petrochemical-based products and make use from waste rather than landfilling it - Kristina Smith reports
It is not just the desire to preserve our environment which is driving the industry’s search for products which don’t eat up raw materials. The hunger of emerging economies – particularly China – mean that resources can be hard to come by, so it makes sense for suppliers to investigate ‘greener’ alternatives such as recycled or renewable oils and waste streams.It was this lack of raw materials which drove specialist chemicals company
“Three or four years ago, we could not find any raw materials for production,” said the director of one company who oversees the firm’s R&D activities. “China has a huge need for raw materials and they buy everything available on the market.”
The company – which has a strong trackrecord in research and innovation – joined forces with universities, laboratories and asphalt suppliers to test used oils, tyre rubber and plastics. Armed with the results, the company is preparing to launch a ‘green line’ which incorporates waste or recycled materials. Its research into waste oils was extensive.
“We studied hundreds of oils from which we found four which could be used,” said the director. Having invested much time and resource, the company will not reveal what these four oils are.
However, in a paper prepared for the Eurasphalt & Eurobitume 2012 conference in Istanbul in June, the company gave an indication of how much virgin oil can be replaced by used lube oil in various additives. The company is not alone in its quest. A review of the papers published at the congress, where the theme was ‘Asphalt, the sustainable road to success’ reveals that many companies and institutions are carrying out research in similar fields.
Grow your own binder
Renewable, and possibly recycled, vegetable oil could prove useful as a rejuvenator for recycled asphalt or as an asphalt additive in the future. What we need to know now is: which types are most effective; how much should be used; and what are the long-term implications when it comes to performance and recyclability? Helen Bailey ofBailey and Zoorob had earlier investigated modifying virgin bitumens with used vegetable oil.
The trial saw a control mix using 70/100 pen bitumen and a 40/60 pen bitumen blended with used vegetable oil to create a 70/100 pen equivalent binder, named Vegetex 85. Tests on the live trial materials showed that the Vegetex material ages significantly less (20%) than the control mix composed of a standard bitumen. “This is a positive result and will enhance the long term performance and durability of the asphalt composites,” said Bailey and Zoorob. A visual assessment of the site made six months after laying revealed no early signs of deterioration and, according to local reports, the section of road remains in good condition now.
Nynas has been looking at three possible types of rejuvenator – hydrocarbon oil, vegetable oil and tall oil which is a distillate from pine trees – and comparing their performance against softer virgin bituminous binder which is the standard rejuvenating agent for recycled asphalt. The first phase, already complete, involved tests on the binder at three stages, equivalent to fresh, during mixing and when on the road; the second phase will look at asphalt mixes.
The results of the binder tests were interesting, according to Tanghe. The first surprise was that some additives affected recovered binder differently to fresh binder. With vegetable oil, the difference was marked, with hydrocarbon oil there was some variation. But perhaps most relevant, according to Tanghe, was the observed decline in the performance of some of the oils as the binder got older. Besides the fresh binder, only the hydrocarbon oil retained its rejuvenating effect after the binder was subject to ageing, with the vegetable oil’s rejuvenating properties declining the most.
“It seems that the vegetable oil does not have all the right components to repair the bitumen,” said Tanghe. “If you look at bitumen, it’s made up of different fractions, which in literature are often described as a simple model of a solid phase of asphaltenes and an oily phase of maltenes. By adding fresh bitumen or hydrocarbon oil, you can repair the best of its original composition. Vegetable oil does not have the correct molecules to repair bitumen to as close as what it was originally.”
Nynas now plans to follow up the binder tests with some field trials using the hydrocarbon oils. For the time being, Nynas has not decided whether tall oils and vegetable oils will be further investigated, with the option for later field trials, says Tanghe.
Nynas is also in contact with customers who have rejuvenated recycled asphalt using virgin binders, the Nynas Nypave RX range, with a view to taking samples to work out how this traditional rejuvenation method has performed in the long term.
Of course, there are many types of vegetable oil, and not all of them lead to the same results when added to a binder. This fact was highlighted by research into using vegetal products by the Petrobas Research Centre in Rio de Janeiro.
Among the products they investigated were palm oil, castor oil, dark cotton oil and used frying oil derived from a number of oils. The researchers found that vegetable oil enhances the thermal susceptibility of asphalt.
Notably they found variation between the different types with castor oil the best performer and used frying oil the worst; they suggested this was due to loss of properties during cooking.
With so many varieties of oil and binder, performance tests will always be necessary before any type of vegetable oil is used. The amount of oil also seems significant: Bailey and Zoorob were working with higher proportions than Nynas on their rejuvenator trials. And, as highlighted by Nynas’ work, long-term performance should be carefully investigated in any testing regime.
From wheel to road
There’s nothing new about using waste tyre rubber in pavements – people have been doing it for over 50 years. But the drive now is to find a process which requires standard rather than specialist mixing plants and which doesn’t require the high temperatures traditionally needed.The use of used tyre rubber began in the States as early as the 1950s and is far more widespread there – and in Australia and South Africa - than in most of Europe.
One of the main reasons for this is political will, argues Dr David Lo Presti, a research fellow at Nottingham Transportation Engineering Centre has carried out a wide range of research into the factors which help get the best from tyre rubber modified bitumen (TR-MB).
“The States was similar to Europe, with hotspots of use in certain areas, until the 1990s when there was a mandate encouraging people to use tyre rubber in pavements,” said Lo Presti. “This was a boom time for rubber, which encouraged the development of technologies.”
The other barrier to more widespread takeup of TR in bitumen in Europe is that it requires modification of existing plants, which adds cost. There are two main ways in which ground tyre rubber can be used in asphalt mixes; dry mixes and wet mixes. There are several versions of wet mix technology.
The ‘dry’ process involves using the ground tyre granules as you would an aggregate. The resulting pavement shows some improvements in properties over conventional mixes, but the reaction between the rubber and the bitumen is limited.
The original ‘wet’ process involved adding the ground tyre rubber to hot bitumen, at around 200°C, and mixing intensively for around an hour. This process creates a new, modified binder with resulting improvements in the asphalt’s properties.
However this wet mix process has its drawbacks. First, it requires very high temperatures with the resulting carbon and other harmful emissions; second it requires specialist equipment to continuously agitate the bitumen, otherwise the rubber particles can settle out; and thirdly, rubber modified bitumen has high viscosity which means it needs to be stored, transported and laid at high temperatures too.
The reason for rubber modified bitumen’s high viscosity is that, when heated with the bitumen, it absorbs some of the oily phase – or maltenes – from the bitumen and swells up. So with swollen rubber particles and less oil in the bitumen, the result is a stickier mix.
The solution to this problem saw the development of terminal blends – so called because the TR-MB are often produced at the refinery – were first introduced in the US in the 1980s, although only recently have seen more widespread use there.
Sometimes called ‘wet process-no agitation’ technology, the process uses very fine rubber crumbs which are totally dissolved in the bitumen and can be stored, transported and used in the same way as polymer modified bitumens. They can also be produced at asphalt plants. However, there are many variables to be considered before the right formulation can be reached, says Lo Presti: temperature, time, how it is stirred, oil extenders used; and the tyre rubber properties including how it is processed, particle size and content. In the last five to six years, many variations have been developed. “Everyone is patenting them,” said Lo Presti.
Sasol Wax reported on its solution to the viscosity problem which involves a pre-treatment phase to pre-swell the rubber particles. It pre-treated the rubber crumbs by mixing them with a swelling agent, together with Fischer-Tropsch wax, a warm mix additive, and heating at 110°C for six minutes. The pre-treated particles can be stored at ambient temperature and then can be added to a mix at lower temperatures than would normally be required.
Sasol Wax has trialled this new pre-treated particle on roads in Hamburg. The company reports that combination of this wax additive and swelling agent decreases the viscosity of the binder intensely, improves the handling and compaction behaviour of the asphalt mix and allows lower production and paving temperatures.
Iterchmica also developed a microwave treatment for tyre rubber which converts the waste rubber into a weak modifier which can be used to partially replace SBS. Although this treated rubber can be added at lower temperatures, there are still environmental impacts to consider, said Federica Giannattasio of Iterchimica, “If you add it to the bitumen, the problem is that you need very high temperatures with the consequences of carbon dioxide emissions, smoke, etc.” In Italy Iterchimica has had success with the dry system for used tyre rubber where the granules are added with the aggregate to the mix. These mixes have noise-reducing properties and have been used in built-up areas of Italy’s cities with great success, says Giannattasio. “
Polymer additives made from plastic materials are an alternative to the standard polymers ones which come from the petrochemical industry, according to Giannattasio “They can be obtained by using recycled plastic materials of various origin, providing that they are correctly blended,” she said.
These ‘green’ polymer compounds are a mix of selected recycled polymers, which are made of smooth and flexible granules. They can be added directly to the plant's mixer and there is no need to increase the production temperatures compared to traditional mixes. Two papers published at Eurasphalt & Eurobitume 2012 looked at recycling plastics. One investigated replacing part of the aggregate in a mix with granular Poly-Ethylene Terephthalate (PET) with the researchers from the Turkish Associaction of Contracors and Dokuz Eylul University concluding that PET modified asphalt can increase the mixture toughness and resistance to tensile stresses. Another paper from researchers in Costa Rica and Colombia looked at using polyethylene banana bags. The bag modified bitumen showed some improvement in properties when compared to a standard mix but the biggest benefit would be in preventing such huge amounts of plastic being dumped in open pits or burnt, say the researchers.
Giannatassio does not anticipate a huge additional demand for Iterchimica’s new line of green products, but she predicts that for some clients it may be a differentiator. “For some people and for some jobs, they will prefer the green additives instead of the traditional ones,” she said.
Ironically, having set out on this journey in the face of traditional product shortages, the same issue is now impacting on the availability of waste products. “Do you know what is happening now?” asked Giannatassio. “There’s a lack of waste. You cannot find waste!”
Safe deliveries
Bitumen can be a hazardous product if it comes into contact with skin, due to the high temperatures required for storage, handling and transportation. And without proper training and procedures in place, bitumen deliveries can be a high risk activity.
Accidents can happen when customers have not checked the safe working capacity they have in their storage tanks, or when delivery procedures are not followed correctly. Nynas is hoping to combat these problems with the release of an updated version of its safety toolkit, called ‘Safety is No Accident – Observe, think and act’. “The safety of employees and the Partnership in Safety Nynas has with its customers is taken very seriously,” said Nynas’ UK HSSE Manager Paul Lamb.
Nynas first launched safety documentation and an accompanying video back in 1996, revising it in 2006. In 2011 Nynas decided to replace the video with a brand new DVD to show best practice. The DVD, together with a handbook, Eurobitume Bitumen burns card, two posters and three quick guides makes up the new toolkit.
All the new material will be available in Danish, Dutch, English, Estonian, Finnish, French, German, Polish, Norwegian, Spanish and Swedish. The DVD has also been translated into each of these languages.
As well as updating guidance in line with best practice according to Eurobitume and the UK’s Refined Bitumen Association, the new toolkit has also taken on board a flurry of recent updates to legislation. These include REACH (Regulation, Evaluation and Authorisation of Chemicals) which came into force in 2007 and CLP (Classification, Labelling and Packaging of hazardous substances and mixtures) which came into force in 2009, with a transition period up to 2015. The kit will also raise awareness on the latest Personal Protective Equipment and hydrogen sulphide (H2S) precautions.
“Safety is high on our customers’ agendas and so it is on ours,” said Nynas Bitumen vice president Russell Childs. “Nynas feels it has a responsibility to encourage safe practices relating to bitumen, both within our company and beyond.”