The demand for bitumen additives is set to increase. Kristina Smith reports on some of the companies who are preparing to meet that increased demand. The variation in quality and composition of bitumen around the world is something that has been well-documented in these pages. Processing technologies for crude oil are changing, the way bitumen is traded is changing, and the final result can be a product that may not be all it seems – or huge variations from one shipment to another. Help is at hand, however,
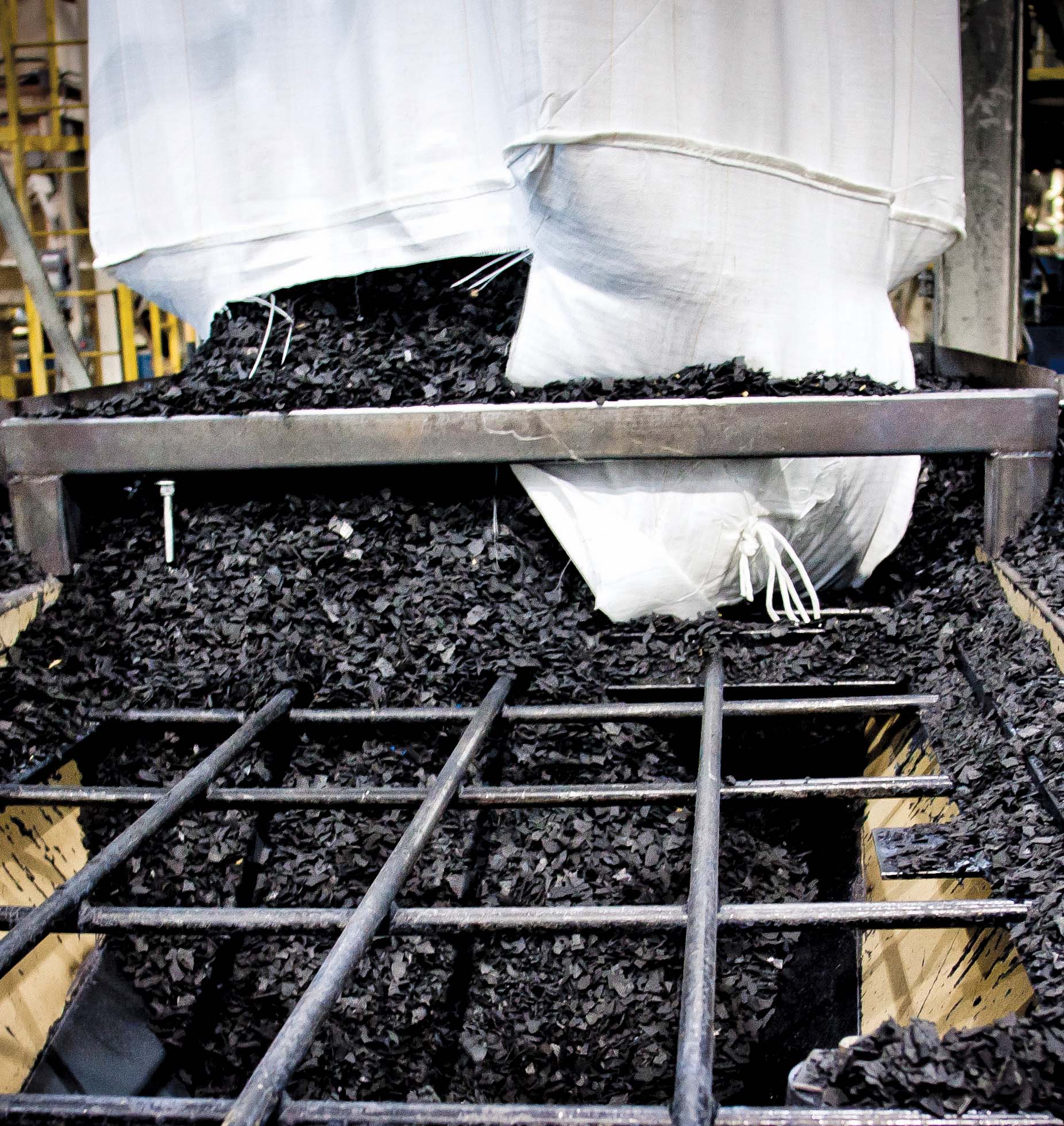
Lehigh is developing its worldwide presence
The demand for bitumen additives is set to increase. Kristina Smith reports on some of the companies who are preparing to meet that increased demand
The variation in quality and composition of bitumen around the world is something that has been well-documented in these pages. Processing technologies for crude oil are changing, the way bitumen is traded is changing, and the final result can be a product that may not be all it seems – or huge variations from one shipment to another.
Help is at hand, however, in the form of additives. There’s evidence this month that there is huge potential for growth in this specialist sector of bitumen technology, with companies in this niche gearing up to expand and develop.
US firm7875 Lehigh Technologies, which supplies micronised rubber powder and additives, is investing in order to kick-start its business in Europe. Italian specialist 252 Iterchimica, which has pioneered many new additives over the years, is using an injection of cash to increase its overseas presence. And 7937 MWV Speciality Chemicals is preparing to break away from its parent group to become a company in its own right.
Meanwhile, a smell-busting additive from763 Shell has won an award.
“We will be bringing a few technologies that have not been seen in Europe before,” said Tom Rosenmeyer, Lehigh’s VP technology. Lehigh is planning to promote and sell its MRP MicroDyne MD-105 and Rheopave technologies from its new Spanish base.
MicroDyne 105 is a very fine powder, which provides stability to rubber-modified bitumen, which has historically been a challenge to achieve, said Rosenmeyer. Rheopave, which sees an additive added to rubber-modified bitumen, provides identical characteristics to polymer-modified bitumen, according to Lehigh.
“The Rheopave technology is a cost-effective polymer-modifed asphalt solution,” said Rosenmeyer. “We call it a hybrid solution because it combines polymer and rubber.”
Lehigh, which supplies its micronised rubber powder to the tyre and industrial rubber industries as well as to road construction, uses only truck tyres to produce its product. In Spain, it is joining forces with Hera Holdings, which converts used tyres to rubber granules.
Though investment in road building in Spain, as in many other European countries, is limited at the moment, maintenance is still ongoing said Lehigh CEO Alan Barton. “Usually rubber-modified asphalt is used in the top layer of road construction,” Barton explained. “It’s a very good choice for maintenance and resurfacing applications.”
Lehigh chose Spain because it is already working with three major asphalt companies there, as well as with some smaller ones in that country. The company’s market development team of Lluis Molina and Josep Freixas, will lead the Spanish subsidiary.
Currently, Lehigh mostly sells into asphalt markets in the US, North Asia, Australia and New Zealand. “We are targeting Southeast Asia, but they are somewhat like Europe in that they are still investigating the use of rubber in pavements,” said Barton.
Next steps for Lehigh will see it forming links with technical universities in Europe in order to conduct trials and prove the properties of its products.
“We think that the time is right for bitumen additives to be seen as a ‘must-have’ technology at all levels in all road construction processes,” said Iterchimica CEO Federica Giannattasio, “and we want to be one of the main actors in this niche in the coming years.”
Entrepreneur and investor Gamberale has chosen Iterchimica because he sees it has the potential to expand its activities globally. “I believe Iterchimica has the typical potential of a niche company, as a leader in the field of asphalt additives, producing products that can improve safety, increase performance, reduce energy costs and that do not pollute the environment,” said Gamberale.
Based in Bergamo in Italy, Iterchimica was founded by Gabriele Giannattasio in 1967 who now runs the firm with daughters Federica and Mariella and son Alessandro. “I was positively impressed by the Giannattasio family: they combine Gabriele's technology and product insight with his young offspring's managerial and entrepreneurial engagement,” said Gamberale.
Iterchimica has a strong tradition of research and development. Over recent years it has launched new products and improved existing ones, particularly in the fields of anti-stripping agents, rejuvenators and cold binders.
The manufacturer has also been keen to promote the idea that additives, though chemicals, should be as environmentally friendly as possible. “All Iterchimica’s efforts are directed towards developing high-performance products combined with great attention to environmental protection,” said Federica Giannattasio. “Developing a ‘green product’ is not only producing a product based on natural raw materials, but it is also thinking about the whole environmental impact of producing and maintaining a road.”
A recent addition to Iterchimica’s product range comes as Iterlene ACF HP GREEN, which it developed to allow the production of plastic and workable cold asphalt mix using 100 percent RAP. Its Iterlow RS additive allows the workability of mix also at much lower temperatures, which reduces carbon dioxide emissions, even with a high percentage of RAP.
Future developments will see the improvement to the firm’s IterPPS technology - a customisable compound of structural modifiers, mainly polymers and fibers – that Iterchimica said can almost double the life-cycle of high-performances pavements. The manufacturer works extensively with universities in Italy and other countries and is currently finalising a new project with a research centre in the US.
Rather than mask the smell of bitumen, Bitufresh neutralises the substances that cause odour to be released from the bitumen. This reduces the odours at an asphalt plant and also during the laying process, reducing environmental nuisance for neighbours and workers with the odour-reducing effect lasting two weeks.
Shell launched Bitufresh in 2009, although it was not available commercially until 2012. Currently its customer base is in Europe and Asia, although there is interest from other markets, according to Shell. “Given that it is an innovative product, progressive customers have adopted it first and we expect the demand to increase in future,” said Shell’s global external relations manager Oliver Lim.
As well as supplying Bitufresh as an additive, Shell can also supply it ready-mixed into the binder as Shell Bitumen Fresh.
8226 Ingevity. Parent group WestRock Company has stated its intention to spin the business off as an independent, publicly traded company by the end of the year.
The specialty chemicals division produces a range of chemicals for the energy, infrastructure and transportation industries, including additives for bitumen. Its new name is said to be a combination of words that describe the oranisation’s characteristics: innovation, ingenuity, longevity and genuine.
Australia moves towards national asphalt specification as harmonised mix design debuts on the Gateway Project. The Australian road construction industry has made a huge step forwards towards a national asphalt specification. One of the country’s biggest road projects, the Gateway Project, has trialled an asphalt mix design that will form the basis of a harmonised national asphalt specification.
The Aus$1bn Gateway Projects is Western Australia’s largest ever road project and involves the widening of Tonkin Highway to six lanes, upgrading Leach Highway to an expressway, four new grade separated interchanges and an upgraded interchange.
Currently, each of the six states in Australia has its own specification for asphalt mix design and production. “National companies that operate across states are doing different things for different people every single day of the week at enormous cost,” said chief executive officer of the Australian Asphalt Pavement Association (AAPA) Michael Caltabiano.
The AAPA, whose members include both road contractors and authorities, is spearheading the drive towards a national specification because it will create longer-lasting, better performing roads at a lower cost to the tax payer, said Caltabiano. After the states of Queensland and New South Wales had been working for 18 months to produce a joint specification for asphalt, the Gateway Project offered the opportunity to further develop the specification and actually put it into practice on a short-length road. “In Western Australia they were having a particular problem with the durability of their mixes,” explained Caltabiano. “They needed a full-depth asphalt pavement, but were using a mix developed for surfacing which had 9% air voids and 4.5% bitumen. When you use that for a full-depth pavement you tend to get water infiltration and stripping.”
To counter these problems, the Western Australia road authority Main Roads set clauses in its contracts that said that asphalt could not be laid during wet weather and that if it rained during laying, the road had to be ripped up. Consequently, contractors were spending days waiting to work as they watched weather forecasts.
“Around 12 months ago Main Roads said that they wanted to do things fundamentally differently,” said Caltabiano. “They wanted to take the best of the best which is why they picked up on the work that had already been done by Queensland and New South Wales.”
Fulton Hogan designed the mix for the Gateway Project and Boral laid it. The demonstration section was laid about two months ago, with AAPA now developing a national version of the specification that Caltabiano expects could be rolled out across the country within a couple of years.
“Once we have the national specification, contractors will start to propose it as an alternative during the tender process and the road authorities will see the difference it makes to the cost,” said Caltabiano. “The consequence of the new harmonised standard will be that the industry can be much more efficient, productivity will go up and the road authorities will get more road for the same dollar.”
The variation in quality and composition of bitumen around the world is something that has been well-documented in these pages. Processing technologies for crude oil are changing, the way bitumen is traded is changing, and the final result can be a product that may not be all it seems – or huge variations from one shipment to another.
Help is at hand, however, in the form of additives. There’s evidence this month that there is huge potential for growth in this specialist sector of bitumen technology, with companies in this niche gearing up to expand and develop.
US firm
Meanwhile, a smell-busting additive from
Lehigh Technologies
Micronised rubber powder specialist Lehigh Technologies has signalled its intent to increase its presence in Europe with the opening of Lehigh Spain in Barcelona. The US firm, which is headquartered in Georgia, also plans to build a manufacturing facility between Barcelona and Bilbao, which it intends to open in mid-2016.“We will be bringing a few technologies that have not been seen in Europe before,” said Tom Rosenmeyer, Lehigh’s VP technology. Lehigh is planning to promote and sell its MRP MicroDyne MD-105 and Rheopave technologies from its new Spanish base.
MicroDyne 105 is a very fine powder, which provides stability to rubber-modified bitumen, which has historically been a challenge to achieve, said Rosenmeyer. Rheopave, which sees an additive added to rubber-modified bitumen, provides identical characteristics to polymer-modified bitumen, according to Lehigh.
“The Rheopave technology is a cost-effective polymer-modifed asphalt solution,” said Rosenmeyer. “We call it a hybrid solution because it combines polymer and rubber.”
Lehigh, which supplies its micronised rubber powder to the tyre and industrial rubber industries as well as to road construction, uses only truck tyres to produce its product. In Spain, it is joining forces with Hera Holdings, which converts used tyres to rubber granules.
Though investment in road building in Spain, as in many other European countries, is limited at the moment, maintenance is still ongoing said Lehigh CEO Alan Barton. “Usually rubber-modified asphalt is used in the top layer of road construction,” Barton explained. “It’s a very good choice for maintenance and resurfacing applications.”
Lehigh chose Spain because it is already working with three major asphalt companies there, as well as with some smaller ones in that country. The company’s market development team of Lluis Molina and Josep Freixas, will lead the Spanish subsidiary.
Currently, Lehigh mostly sells into asphalt markets in the US, North Asia, Australia and New Zealand. “We are targeting Southeast Asia, but they are somewhat like Europe in that they are still investigating the use of rubber in pavements,” said Barton.
Next steps for Lehigh will see it forming links with technical universities in Europe in order to conduct trials and prove the properties of its products.
Iterchimica
Italian additive specialist Iterchimica is embarking on ambitious expansion plans, funded by the arrival of minority shareholder and new chairman Vito Gamberale. New laboratories are under construction, a new marketing department is being created and improvements to the production and logistics processes are underway.“We think that the time is right for bitumen additives to be seen as a ‘must-have’ technology at all levels in all road construction processes,” said Iterchimica CEO Federica Giannattasio, “and we want to be one of the main actors in this niche in the coming years.”
Entrepreneur and investor Gamberale has chosen Iterchimica because he sees it has the potential to expand its activities globally. “I believe Iterchimica has the typical potential of a niche company, as a leader in the field of asphalt additives, producing products that can improve safety, increase performance, reduce energy costs and that do not pollute the environment,” said Gamberale.
Based in Bergamo in Italy, Iterchimica was founded by Gabriele Giannattasio in 1967 who now runs the firm with daughters Federica and Mariella and son Alessandro. “I was positively impressed by the Giannattasio family: they combine Gabriele's technology and product insight with his young offspring's managerial and entrepreneurial engagement,” said Gamberale.
Iterchimica has a strong tradition of research and development. Over recent years it has launched new products and improved existing ones, particularly in the fields of anti-stripping agents, rejuvenators and cold binders.
The manufacturer has also been keen to promote the idea that additives, though chemicals, should be as environmentally friendly as possible. “All Iterchimica’s efforts are directed towards developing high-performance products combined with great attention to environmental protection,” said Federica Giannattasio. “Developing a ‘green product’ is not only producing a product based on natural raw materials, but it is also thinking about the whole environmental impact of producing and maintaining a road.”
A recent addition to Iterchimica’s product range comes as Iterlene ACF HP GREEN, which it developed to allow the production of plastic and workable cold asphalt mix using 100 percent RAP. Its Iterlow RS additive allows the workability of mix also at much lower temperatures, which reduces carbon dioxide emissions, even with a high percentage of RAP.
Future developments will see the improvement to the firm’s IterPPS technology - a customisable compound of structural modifiers, mainly polymers and fibers – that Iterchimica said can almost double the life-cycle of high-performances pavements. The manufacturer works extensively with universities in Italy and other countries and is currently finalising a new project with a research centre in the US.
Shell
An additive that removes the smell of bitumen has been recognised by the International Road Federation (IRF) in its 2015 Global Road Achievement Awards (GRAA). Shell Bitufresh won the research category, one of the 12 winning projects announced at the end of June.Rather than mask the smell of bitumen, Bitufresh neutralises the substances that cause odour to be released from the bitumen. This reduces the odours at an asphalt plant and also during the laying process, reducing environmental nuisance for neighbours and workers with the odour-reducing effect lasting two weeks.
Shell launched Bitufresh in 2009, although it was not available commercially until 2012. Currently its customer base is in Europe and Asia, although there is interest from other markets, according to Shell. “Given that it is an innovative product, progressive customers have adopted it first and we expect the demand to increase in future,” said Shell’s global external relations manager Oliver Lim.
As well as supplying Bitufresh as an additive, Shell can also supply it ready-mixed into the binder as Shell Bitumen Fresh.
Ingevity
From 1 September MWV Specialty Chemicals will be known asThe specialty chemicals division produces a range of chemicals for the energy, infrastructure and transportation industries, including additives for bitumen. Its new name is said to be a combination of words that describe the oranisation’s characteristics: innovation, ingenuity, longevity and genuine.
Australia moves towards national asphalt specification as harmonised mix design debuts on the Gateway Project. The Australian road construction industry has made a huge step forwards towards a national asphalt specification. One of the country’s biggest road projects, the Gateway Project, has trialled an asphalt mix design that will form the basis of a harmonised national asphalt specification.
The Aus$1bn Gateway Projects is Western Australia’s largest ever road project and involves the widening of Tonkin Highway to six lanes, upgrading Leach Highway to an expressway, four new grade separated interchanges and an upgraded interchange.
Currently, each of the six states in Australia has its own specification for asphalt mix design and production. “National companies that operate across states are doing different things for different people every single day of the week at enormous cost,” said chief executive officer of the Australian Asphalt Pavement Association (AAPA) Michael Caltabiano.
The AAPA, whose members include both road contractors and authorities, is spearheading the drive towards a national specification because it will create longer-lasting, better performing roads at a lower cost to the tax payer, said Caltabiano. After the states of Queensland and New South Wales had been working for 18 months to produce a joint specification for asphalt, the Gateway Project offered the opportunity to further develop the specification and actually put it into practice on a short-length road. “In Western Australia they were having a particular problem with the durability of their mixes,” explained Caltabiano. “They needed a full-depth asphalt pavement, but were using a mix developed for surfacing which had 9% air voids and 4.5% bitumen. When you use that for a full-depth pavement you tend to get water infiltration and stripping.”
To counter these problems, the Western Australia road authority Main Roads set clauses in its contracts that said that asphalt could not be laid during wet weather and that if it rained during laying, the road had to be ripped up. Consequently, contractors were spending days waiting to work as they watched weather forecasts.
“Around 12 months ago Main Roads said that they wanted to do things fundamentally differently,” said Caltabiano. “They wanted to take the best of the best which is why they picked up on the work that had already been done by Queensland and New South Wales.”
Fulton Hogan designed the mix for the Gateway Project and Boral laid it. The demonstration section was laid about two months ago, with AAPA now developing a national version of the specification that Caltabiano expects could be rolled out across the country within a couple of years.
“Once we have the national specification, contractors will start to propose it as an alternative during the tender process and the road authorities will see the difference it makes to the cost,” said Caltabiano. “The consequence of the new harmonised standard will be that the industry can be much more efficient, productivity will go up and the road authorities will get more road for the same dollar.”