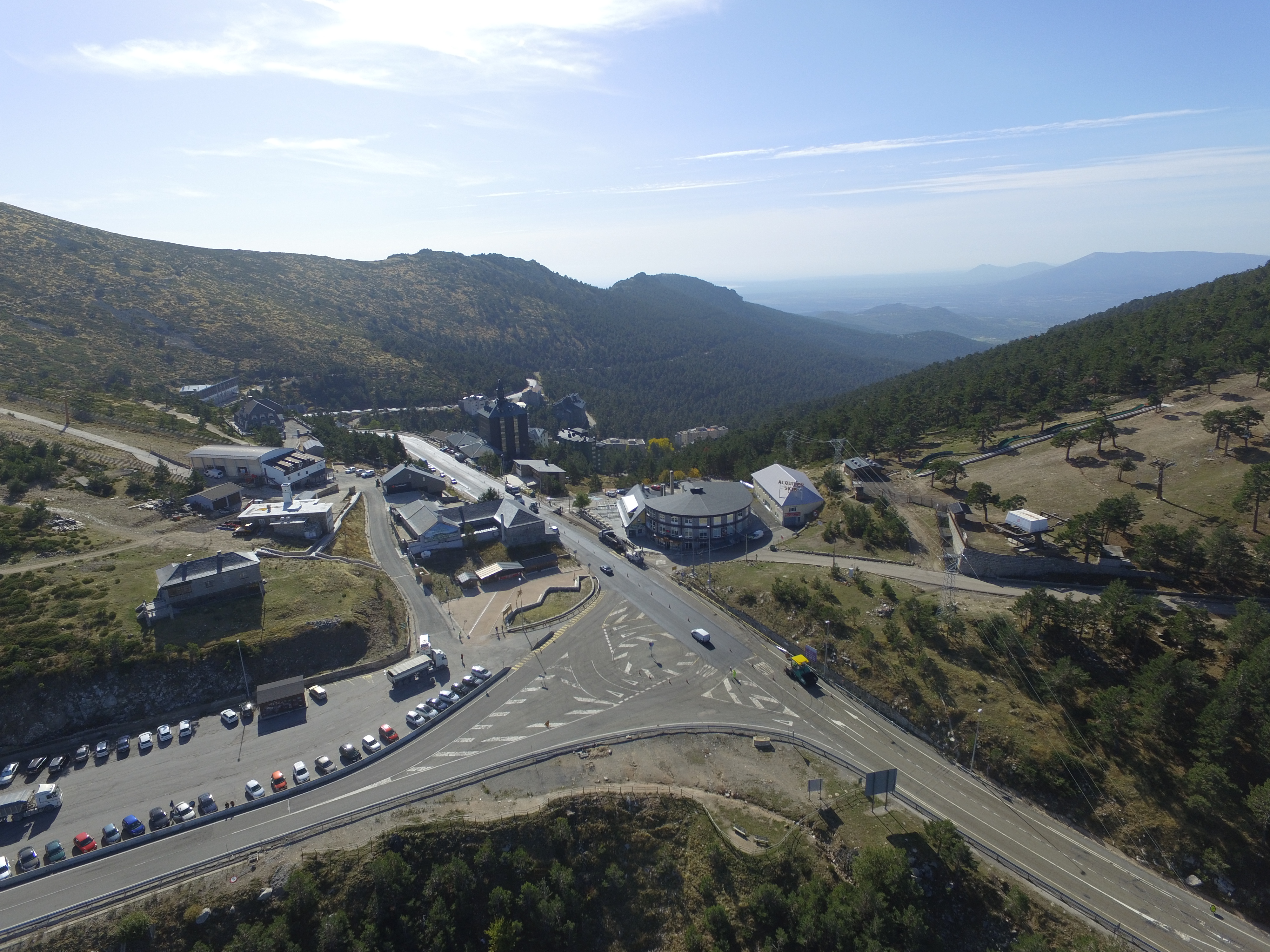
This month we hear how additives can bring RAP back from the dead and fight the ravages of salt damage, how pellets reach parts that PMB can’t and how Shell and WeedsWest are expanding their respective businesses - Kristina Smith writes
The challenges faced by roads and those who build and maintain them vary significantly in different parts of the world, with specialist companies developing a range of solutions to meet these challenges.
In China,
Arizona Chemical
Reclaimed asphalt which is so hard that it is out of specification, can be used again in high proportions and for the upper layers of a road. This is the claim from Arizona Chemical, a Kraton Corporation company, using its SYLVAROAD RP1000 additive which is made from pine chemicals.
Contractor
“The full evaluation will take a few more months, but once we have all the test results, we believe that we can prove that very old RAP can be recycled and reused for surface layers in relevant quantities,” said Maria Di Nolfo, business unit manager, roads and construction. “This will open up further discussions for us.”
The trial section of road runs up to Arizona Chemical’s Niort plant which produces a range of products from pine chemicals. It will be trafficked by heavy vehicles travelling at slow speeds as they deliver materials to the plant.
Arizona Chemical and
The trial also saw Arizona Chemical change the mixing process so that the rejuvenator was added earlier in the process: RAP travelling on a conveyor was sprayed with SYLVAROAD RP1000 before it entered the heating drum. “The idea is to treat the RAP so that you can start to soften the bitumen in the RAP before you get it in the mixer so you can get a much more homogeneous mix,” said Di Nolfo.
This way, the capacity of the asphalt plant can be maintained because a longer mixing time is not required.
According to Arizona Chemical senior staff scientist, roads and construction, Laurent Porot, when the additive is sprayed onto the RAP, it starts to break the RAP down into its constituent parts and to soften the binder in the RAP.
Introducing the additive at this point wouldn’t be possible with other types of rejuvenator, said Porot: “Petrol-based flux oil or other oils cannot be added before the heating drum because the flash point is too low.
“When we add the rejuvenator to the virgin bitumen, we make the virgin bitumen softer. The overall viscocity of the final is reduced, but we are not doing anything to the RAP.”
Eurovia was keen to check that the mix would have sufficient compactability and workability, said Porot: “Compactability can be tested with normal standards, workability is more difficult to assess,” he said. So Eurovia developed a new workability test, based on the Nynas Workability Device.
Using 1.5kg of SYLVAROAD RP1000/tonne of asphalt mix, and with a RAP percentage of 40, Eurovia laid a 60mm-deep layer of asphalt on top of an unbound sub-base layer.
The air temperature was around 5°C, and the operation ran smoothly, according to Porot.
It was a little too early for Eurovia to talk about the trial, but the contractor said in a statement: "We value the environmental benefits of preserving natural resources and using less material. There is also an economic advantage as we can use less bitumen.”
Monitoring and testing of the road will continue for between two and five years, says Arizona Chemical.
PR Industrie
Contractor BUTEC/Ahmad Al Tarawneh joint venture used an asphalt mixture modified with special pellets to rehabilitate the North Runway at Queen Alia International Airport in Amman, Jordan between September and December last year.
Manufactured by PR Industrie at its headquarters and factory in France, the pellets allow contractors and owners to benefit from the improved pavement performance in locations where polymer modified bitumen is not available.
“We have a different technology to most PMB (polymer modified bitumen) producers,” said Michael Lecomte, business development manager for PR Industrie which makes the pellets. “We don’t sell additives to companies such as Total or Shell, we sell directly to the contractors, the people building the roads.”
For the Amman project, 60/70 bitumen from Jordanian Petroleum Refinery was used, with PR FLEX 20 pellets. The works to an area of around 297,000m2 included crack repair, milling and full reconstruction of the top course, with a fresh layer around 60 to 75mm laid.
Transporting PMB over long distances is expensive and difficult. One solution is to create solid blocks of PMB but these require large amounts of heat to melt them down once they have reached the project location, a process which can lead to some product being wasted or damaged through overheating.
The majority of PR Industrie’s projects are in developing regions, particularly Africa and China. Others do produce similar products, although PR Industrie claims that it was the first to do it, starting 30 years ago, and that it is the world leader in this particular niche.
PR Industrie has developed the formulation of its pellets since it began making them in 1989. It now produces a range of six pellet types, designed to do different things in different layers of a pavement. Its most popular products are PR PLAST S, aimed to prevent rutting in the wearing course and binder layers; PR PLAST MODULE to give high modulus mixes for the base layer; PR FLEX 20, based on SBS (Styrene Budateine Styrene), for the wearing course; and PR PLAST AK for areas where fuel will be present.
Later additions to the range include PR PLAST LT to be used with lower temperature mixes and PR PLAST FIBRES to create porous asphalt for wearing courses.
“In general, we will not describe the properties of a product in terms of the PMB specification, we focus more on the asphalt concrete properties,” says Lecomte. “We believe that it is the properties of the final product that are important. We know that sometimes the properties of the modified bitumen do not always correlate with the performance of the asphalt mixture.”
PR Industrie’s growth in Africa has been achieved through links with French-speaking countries there. And with the growing presence of Chinese contractors in Africa, the manufacturer also has an office in China. “That means we can approach the road authorities from here and the contractors for our Chinese office,” says Lecomte.
With an in-house R&D facility, PR Industrie provides supports to its customers on mix design, testing and evaluation. “In some developing countries the testing facilities are not always available, especially the most complex equipment like fatigue testing,” said Lecomte.
Ditecpesa
In October last year contractor Asfaltos y Pavimentos laid a section of road on the top of the Navacerrada mountain pass near Madrid using a new type of bitumen, Extreme Climate Bitumen. It has been designed for areas such as the pass, where it snows regularly and large quantities of salt are applied, and also for coastal areas with warm climates and high levels of humidity and salt.
Extreme Climate Bitumen is one of a number of technologies that Ditecpesa is developing, in a bid to reduce the cost and resource required to maintain roads. On long-term maintenance contracts, such developments could mean that less resurfacing is required over the contract period.
“As part of Ferrovial, Ditecpesa is aware of the impact that winter maintenance has on a pavement. Focussing on this idea, we are working on several solutions, this being the first achieved,” said José Javier García Pardenilla, manager director at Ditecpesa.
“As far as we know this is the first bitumen worldwide to be designed to give a solution to salt, ice and water attack on the pavement.” Extreme Climate Bitumen contains small amounts of nanomaterials, chemical additives and special polymers which give it reduced sensitivity to water. Ditecpesa says that it has improved the bond between the bitumen and aggregate, improving the performance of the pavement.
“We are working hard to know and deeply understand the chemical interactions between aggregates and bitumen. That is the way to get a technology jump in a very competitive market, bringing a huge improvement in performance,” said Pardenilla.
The next steps will see the Madrid regional government and Ditecpesa carrying out ongoing testing and monitoring of the trial section of road. Ditecpesa sees the use of Extreme Climate Bitumen in parts of the US, Canada, Northern Europe and in the Mediterranean, South America, Asia and Pacific Oceania.
Shell
Shell has underlined its ambitions to further expand its activities in India with the opening of its newest solutions centre in the Hongyi Technology Industrial Area in Shanghai's Songjiang District. The Bitumen China Solutions Centre, officially opened in November last year, replaces an existing facility in Beijing, China.
“This new facility is geared towards supporting our customers’ technical needs, providing advice and customised technical solutions tailored to fit their varied paving needs,” said John Read, general manager for technology, Shell Bitumen. “This centre will also help us develop new bitumen and asphalt technologies, in collaboration with our other solution centres globally and our R&D centre in Bangalore, India,”
The new centre is equipped with advanced bitumen and asphalt testing equipment, and is staffed by specially trained bitumen experts. The team there will support Shell Bitumen’s planned growth in China, including testing of new technologies.
The move means that the solutions centre is now in the same location as other Shell research facilities. Shell’s regional technology centre, for research into lubricants and oils, opened in Shanghai in March 2014 and its China commercial centre opened there in June 2015.
Shell Bitumen has other solutions centres globally in both Europe and Asia. Its global bitumen R&D centre is in Bangalore, India. Shell Bitumen claims to be the ‘leading international supplier of bitumen’ in China, having supplied projects including the Guangzhou-Shaoguang Expressway and the longest expressway project in Chinese history; bridges along the Yangtze River; the Maijishan Tunnel, China’s longest tunnel; runways at airports in Hubei, Kunming, Liaoning, Shanghai, Shanxi, Sichuan, Wenzhou and Xiamen; and high-speed rail projects in Shanghai.
WeedsWest
WeedsWest Group has announced a number of new ventures, aimed to diversify its offering and boost turnover: a distribution agreement; a logistics service; and a new bitumen bag filling machine.
WeedsWest, perhaps best known for its bitumen emulsion and PMB plants, is now an official distributor of Jotex equipment. The Jotex range includes boilers, bitumen emulsion distributors and sprayers, chip spreaders, compact sprayers, asphalt maintenance and service equipment, aeronautical handling equipment, steam and thermal fluid boilers. B2bag Logistics is a new venture between WeedsWest Group and BituBag. Dealing with both hot bitumen and bitumen in bags, B2Bag Logistics aims to provide a logistics service ‘from the refinery to the road’.
WeedsWest has also developed a new filling machine for big bags, the B-Filling Unit. A unit has recently been delivered and commissioned for the Lagan Asphalt Group in Ireland at its terminal in Dublin. The unit comes in two 40-foot containers, accommodating the filling and cooling processes.
Advocate for Asphalt
An online campaign which aims to give road builders and materials suppliers tools to explain the benefits of asphalt for road maintenance celebrated its second birthday at the end of last year. Launched in October 2014, Asphalt Advantages is the brain child of
Last year saw the campaign’s website expand to offer resources and advice in four languages: English, French, German and Turkish. And a ‘how to’ video, giving step-by-step instructions has also been added.
“The new video is aimed at encouraging as many asphalt stakeholders as possible to join the campaign and become an active advocate for Asphalt Advantages,” said Siobhan McKelvey, President, Eurobitume. “If we can mobilise new advocates with the tools available in the online toolkit then the important key messages about the benefits of asphalt can be shared to a wider audience. Advocates will have access to a wealth of valuable information sup-porting general, technical, health, safety and environmental advantages.”