This month we look at two additives from natural sources: a rejuvenator derived from pine trees and naturally occurring asphalt - Kristina Smith writes
One of the problems experienced with pavements containing RAP is that, although they exhibit good rutting resistance, they often fail early due to fatigue cracking. Biorefiner Arizona Chemical has just unveiled independent test results for its SYLVAROAD RP1000 Performance Additive that it says demonstrate that the rejuvenator can help create mixes that ar
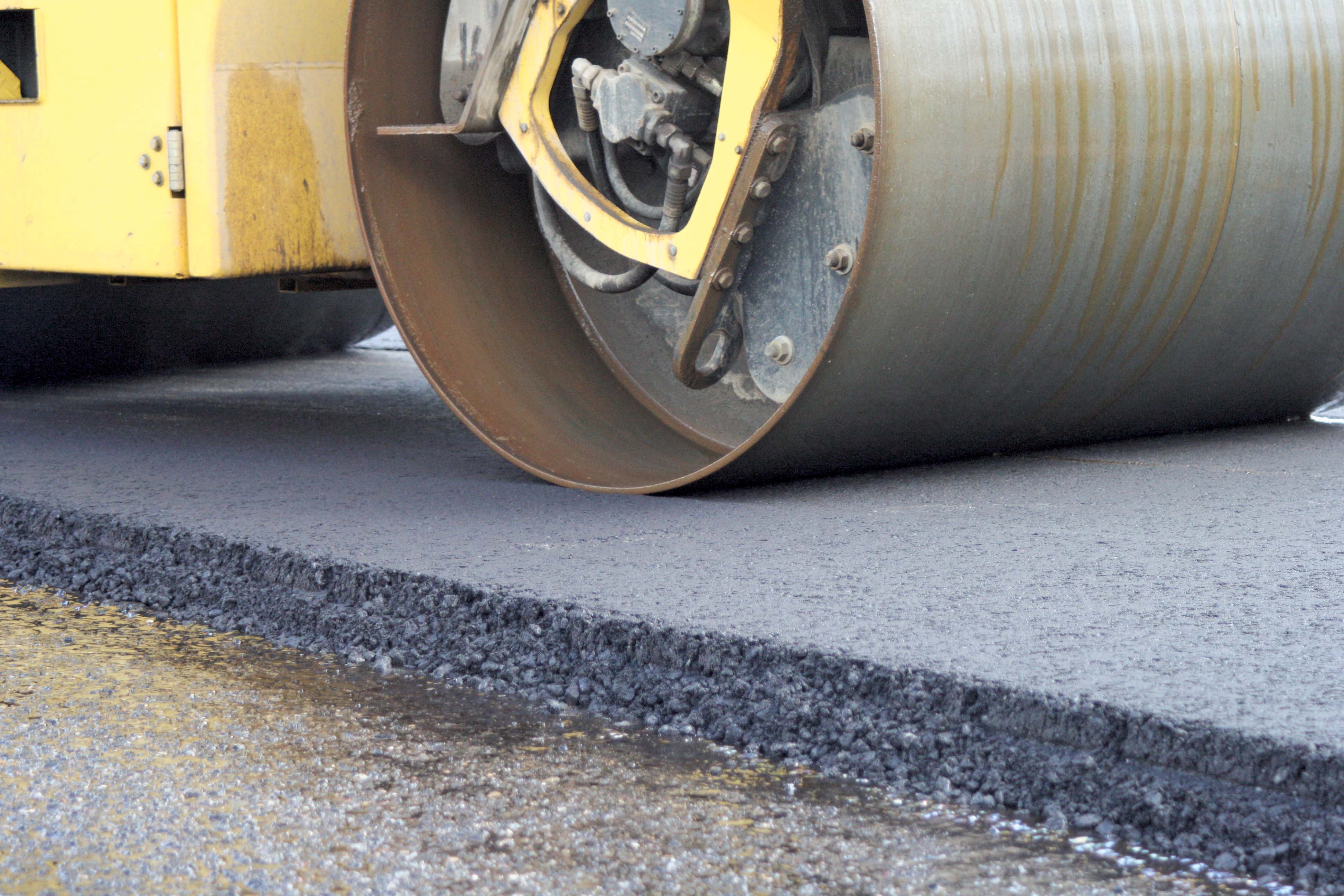
Arizona Chemical claimed that its innovative additive can deliver high-performance mixes resistant to rutting
This month we look at two additives from natural sources: a rejuvenator derived from pine trees and naturally occurring asphalt - Kristina Smith writes
One of the problems experienced with pavements containing RAP is that, although they exhibit good rutting resistance, they often fail early due to fatigue cracking. Biorefiner7856 Arizona Chemical has just unveiled independent test results for its SYLVAROAD RP1000 Performance Additive that it says demonstrate that the rejuvenator can help create mixes that are resistant to both rutting and cracking.
“The tests show that the SYLVAROAD RP1000 additive is effective across an entire range of temperatures, whereas most rejuvenators are only active in the high temperature range,” said Bas Hennissen, business unit director, roads and construction at Arizona Chemical.
NCAT – the National Center for Asphalt Technology - in Auburn in the US carried out laboratory tests, including binder performance grading and Superpave mix design. The aim was to compare the performance of RAP mixtures containing SYLVAROAD RP1000 with RAP mixtures without a rejuvenator and with mixes made with virgin binders.
“We chose NCAT because they are recognised as a leading authority on asphalt technology,” said Hennissen.
SYLVAROAD RP1000 is made from Crude Tall Oil and Crude Sulphate Turpentine, pine chemicals produced by the pulp and paper industry. Arizona Chemical’s researchers spent three years developing the additive. “It has been designed to interact with the RAP binder at a molecular level, rather than acting like an oil - which just reduces the viscosity,” said Hennissen. “The big difference between oils and our product is that ours builds a bridge between the virgin bitumen and the aged bitumen.”
The materials that NCAT worked with required an optimum dose of 6.88% rejuvenator for a mix with 50% RAP. “We take RAP from the customer and tailor the dosage depending on a number of factors: the source and nature of the RAP, the type of plant it will be produced in, the region of the world,” said Chris Holmes, scientist at Arizona Chemical. “There’s no blanket approach. It’s very targeted.”
Arizona Chemical said that it is involved in testing programmes in the US, Europe and Asia. In each market, it is looking to convince contractors and road authorities that SYLVAROAD RP1000 can allow a higher proportion of RAP to be used. In the US, that could mean 50% rather than 20%, whereas in some parts of Europe, the standard 50% RAP could be pushed to 70% or even 100%.
In parallel with the NCAT tests, Arizona Chemical carried out an internal benchmarking study to compare its product with other rejuvenators. “In general the SYLVAROAD additive is two to three times more effective than other products; that is you need twice or three times as much of another product to have the same effect,” said Hennisen.
“It is more expensive than oil,” he admitted. “But because you require less dosage and have additional advantages, we think it’s a price that’s justified.”
Arizona Chemical is now working with reclaimed asphalt shingles in the US, which contain up to 29% bitumen, rather than 4-7% bitumen for RAP. “We’re taking our technology and extending it into that area,” said Holmes.
8272 Selenice Bitumi, which extracts and supplies natural bitumen from Albania.
“Natural asphalts may represent a useful and economic alternative to polymeric materials and other traditionally used modifiers,” said Edith Tartari, marketing manager for Selenice Bitumi, in a paper which references research Sapienza University of Rome.* “They provide superior performing asphalt pavements with higher values of stiffness and greater resistance to rutting and fatigue.”
The university tested three types of naturally occurring bitumen: Gilsonite from Utah in the US, Selenizza from Albania and Trinidad Lake Asphalt from Central America. Selenice Bitumi extracts and supplies natural bitumen from Albania.
Researchers added 10% by weight of each to a standard 80-100 penetration grade bitumen and carried out tests to assess the modified bitumens’ viscoelastic behaviour at high temperatures and at low temperatures. All three behaved similarly at high temperatures, but there was a difference in behaviours at low temperatures.
The paper also references the use of Selenizza asphalt on a number of road projects.
In the mix for the binder course for the A150 in France 20/30 penetration grade bitumen was replaced by 50/70 grade bitumen with 1.5% Selenizza. Selenice Bitumi notes that although the same penetration grade and softening point were obtained through the addition of Selenizza, the modified mix achieved better resistance to fatigue and rutting.
For the Fier to Tepelene highway in Albania, the use of Selenizza as an additive meant that the total thickness of the road’s bituminous layers could be reduced by 4cm. Selenizza was added at a rate of 8% by weight to the 9cm-deep base course, the 6cm-deep binder course and a 4cm wearing course.
Road thickness was also reduced by 4cm for Highway A8 in Greece. Several trial mixes were tested with binders, including bitumen 50/70, bitumen 50/70 with 8 Selenizza and bitumen 30/50 with PR PLAST modified bitumen, with the Selenizza mix affording greater stiffness and fatigue resistance and a reduction in road depth.
A new approach to Perpetual Pavements
NCAT has just published the findings of a research project on Perpetual Pavement design, Report 15-05, ‘Refined Limiting Strain Criteria and Approximate Ranges of Maximum Thicknesses for Designing Long-Life Asphalt Pavements’. The aim of the research, which was sponsored by the National Asphalt Pavement Association (NAPA), was to improve the cost-effectiveness of perpetual pavements, by establishing some new critical design thresholds and some ranges of maximum thicknesses.
The theory behind perpetual pavements, a concept introduced by the Asphalt Pavement Alliance in 2000, is that they are constructed in such a way that they will last for 50 years or more with only periodic resurfacing. NCAT believes that some perpetual pavements are being designed with a greater depth than required, so that it may be possible to achieve efficiencies and cost savings by reducing pavement thickness – and encourage wider use of the method.
“Our findings mean that it is possible to achieve a more economical pavement design,” said Dr Nam Tran, one of five NCAT researchers involved in the study. “Our method is more reliable [than existing methods] and it has also been validated with the field performance data.”
Perpetual pavement design looks to conquer bottom-up fatigue cracking and structural rutting. Bottom-up fatigue cracking typically forms in wheel paths and starts at the very bottom of the asphalt concrete layers. Structural rutting can occur in the aggregate base, the subgrade layer or in both.
Current perpetual pavement design methods look to achieve tensile strains in the bottom asphalt layer that are less than the fatigue endurance limit (FEL) in order to prevent bottom-up cracking, with recent FEL values of about 200 microstrain used. Vertical strain limits of 200 microstrain at the top of the subgrade layer aim to limit permanent deformation.
When the researchers looked at data from six test sections at the NCAT Test Track they found no correlation between laboratory FELs and field fatigue cracking performance or field-measured strains. Instead, they discovered that cumulative field-measured strain distributions were a better predictor of bottom-up field cracking, so they were able to develop a limiting cumulative strain distribution curve.
“We found that the cracking initiated from the lower asphalt layer does not only depend on the endurance limit of the asphalt layer, it also depends on the structural capacity of the whole pavement,” said Tran.
NCAT suggests that its new methodology can be used to develop ranges of maximum asphalt thicknesses for achieving perpetual pavements, tailored to the specific conditions of each State. When a ‘standard’ pavement is designed, road agencies can check how the proposed asphalt thickness compares to the perpetual pavement maximum thicknesses; if it is greater, designers should look to the perpetual pavement design approach.
“We hope that in the future more and more States will use perpetual design methods,” said Tran. Currently California, Illinois and Texas use perpetual pavement design.
One of the problems experienced with pavements containing RAP is that, although they exhibit good rutting resistance, they often fail early due to fatigue cracking. Biorefiner
“The tests show that the SYLVAROAD RP1000 additive is effective across an entire range of temperatures, whereas most rejuvenators are only active in the high temperature range,” said Bas Hennissen, business unit director, roads and construction at Arizona Chemical.
NCAT – the National Center for Asphalt Technology - in Auburn in the US carried out laboratory tests, including binder performance grading and Superpave mix design. The aim was to compare the performance of RAP mixtures containing SYLVAROAD RP1000 with RAP mixtures without a rejuvenator and with mixes made with virgin binders.
“We chose NCAT because they are recognised as a leading authority on asphalt technology,” said Hennissen.
SYLVAROAD RP1000 is made from Crude Tall Oil and Crude Sulphate Turpentine, pine chemicals produced by the pulp and paper industry. Arizona Chemical’s researchers spent three years developing the additive. “It has been designed to interact with the RAP binder at a molecular level, rather than acting like an oil - which just reduces the viscosity,” said Hennissen. “The big difference between oils and our product is that ours builds a bridge between the virgin bitumen and the aged bitumen.”
The materials that NCAT worked with required an optimum dose of 6.88% rejuvenator for a mix with 50% RAP. “We take RAP from the customer and tailor the dosage depending on a number of factors: the source and nature of the RAP, the type of plant it will be produced in, the region of the world,” said Chris Holmes, scientist at Arizona Chemical. “There’s no blanket approach. It’s very targeted.”
Arizona Chemical said that it is involved in testing programmes in the US, Europe and Asia. In each market, it is looking to convince contractors and road authorities that SYLVAROAD RP1000 can allow a higher proportion of RAP to be used. In the US, that could mean 50% rather than 20%, whereas in some parts of Europe, the standard 50% RAP could be pushed to 70% or even 100%.
In parallel with the NCAT tests, Arizona Chemical carried out an internal benchmarking study to compare its product with other rejuvenators. “In general the SYLVAROAD additive is two to three times more effective than other products; that is you need twice or three times as much of another product to have the same effect,” said Hennisen.
“It is more expensive than oil,” he admitted. “But because you require less dosage and have additional advantages, we think it’s a price that’s justified.”
Arizona Chemical is now working with reclaimed asphalt shingles in the US, which contain up to 29% bitumen, rather than 4-7% bitumen for RAP. “We’re taking our technology and extending it into that area,” said Holmes.
Adding naturally occurring asphalts to bitumen increases the content of asphaltenes which reduces the penetration value and increases the softening point (R&B temperature)
Type of bitumen | Penetration at 25° (1/10 mm) | R&B Temperature °C | Asphaltenes content (%) |
---|---|---|---|
Original bitumen | 96 | 44 | 9.8 |
+10% Gilsonite | 38 | 58 | 15.8 |
+10% Selenizza | 67 | 52 | 13.0 |
+10% Trinidad | 78 | 51 | 12.3 |
Selenice Bitumi
Naturally occurring bitumen is a good alternative to polymer-based additives, according to“Natural asphalts may represent a useful and economic alternative to polymeric materials and other traditionally used modifiers,” said Edith Tartari, marketing manager for Selenice Bitumi, in a paper which references research Sapienza University of Rome.* “They provide superior performing asphalt pavements with higher values of stiffness and greater resistance to rutting and fatigue.”
The university tested three types of naturally occurring bitumen: Gilsonite from Utah in the US, Selenizza from Albania and Trinidad Lake Asphalt from Central America. Selenice Bitumi extracts and supplies natural bitumen from Albania.
Researchers added 10% by weight of each to a standard 80-100 penetration grade bitumen and carried out tests to assess the modified bitumens’ viscoelastic behaviour at high temperatures and at low temperatures. All three behaved similarly at high temperatures, but there was a difference in behaviours at low temperatures.
The paper also references the use of Selenizza asphalt on a number of road projects.
In the mix for the binder course for the A150 in France 20/30 penetration grade bitumen was replaced by 50/70 grade bitumen with 1.5% Selenizza. Selenice Bitumi notes that although the same penetration grade and softening point were obtained through the addition of Selenizza, the modified mix achieved better resistance to fatigue and rutting.
For the Fier to Tepelene highway in Albania, the use of Selenizza as an additive meant that the total thickness of the road’s bituminous layers could be reduced by 4cm. Selenizza was added at a rate of 8% by weight to the 9cm-deep base course, the 6cm-deep binder course and a 4cm wearing course.
Road thickness was also reduced by 4cm for Highway A8 in Greece. Several trial mixes were tested with binders, including bitumen 50/70, bitumen 50/70 with 8 Selenizza and bitumen 30/50 with PR PLAST modified bitumen, with the Selenizza mix affording greater stiffness and fatigue resistance and a reduction in road depth.
A new approach to Perpetual Pavements
NCAT has just published the findings of a research project on Perpetual Pavement design, Report 15-05, ‘Refined Limiting Strain Criteria and Approximate Ranges of Maximum Thicknesses for Designing Long-Life Asphalt Pavements’. The aim of the research, which was sponsored by the National Asphalt Pavement Association (NAPA), was to improve the cost-effectiveness of perpetual pavements, by establishing some new critical design thresholds and some ranges of maximum thicknesses.
The theory behind perpetual pavements, a concept introduced by the Asphalt Pavement Alliance in 2000, is that they are constructed in such a way that they will last for 50 years or more with only periodic resurfacing. NCAT believes that some perpetual pavements are being designed with a greater depth than required, so that it may be possible to achieve efficiencies and cost savings by reducing pavement thickness – and encourage wider use of the method.
“Our findings mean that it is possible to achieve a more economical pavement design,” said Dr Nam Tran, one of five NCAT researchers involved in the study. “Our method is more reliable [than existing methods] and it has also been validated with the field performance data.”
Perpetual pavement design looks to conquer bottom-up fatigue cracking and structural rutting. Bottom-up fatigue cracking typically forms in wheel paths and starts at the very bottom of the asphalt concrete layers. Structural rutting can occur in the aggregate base, the subgrade layer or in both.
Current perpetual pavement design methods look to achieve tensile strains in the bottom asphalt layer that are less than the fatigue endurance limit (FEL) in order to prevent bottom-up cracking, with recent FEL values of about 200 microstrain used. Vertical strain limits of 200 microstrain at the top of the subgrade layer aim to limit permanent deformation.
When the researchers looked at data from six test sections at the NCAT Test Track they found no correlation between laboratory FELs and field fatigue cracking performance or field-measured strains. Instead, they discovered that cumulative field-measured strain distributions were a better predictor of bottom-up field cracking, so they were able to develop a limiting cumulative strain distribution curve.
“We found that the cracking initiated from the lower asphalt layer does not only depend on the endurance limit of the asphalt layer, it also depends on the structural capacity of the whole pavement,” said Tran.
NCAT suggests that its new methodology can be used to develop ranges of maximum asphalt thicknesses for achieving perpetual pavements, tailored to the specific conditions of each State. When a ‘standard’ pavement is designed, road agencies can check how the proposed asphalt thickness compares to the perpetual pavement maximum thicknesses; if it is greater, designers should look to the perpetual pavement design approach.
“We hope that in the future more and more States will use perpetual design methods,” said Tran. Currently California, Illinois and Texas use perpetual pavement design.