Choosing the correct high performance binder material for use in asphalt applications has been made easier following a product rebranding exercise by one company. Awareness among highway maintenance contractors of the benefits of selecting polymer modified bitumens when specifying road surfacing materials has risen markedly in the last few years.
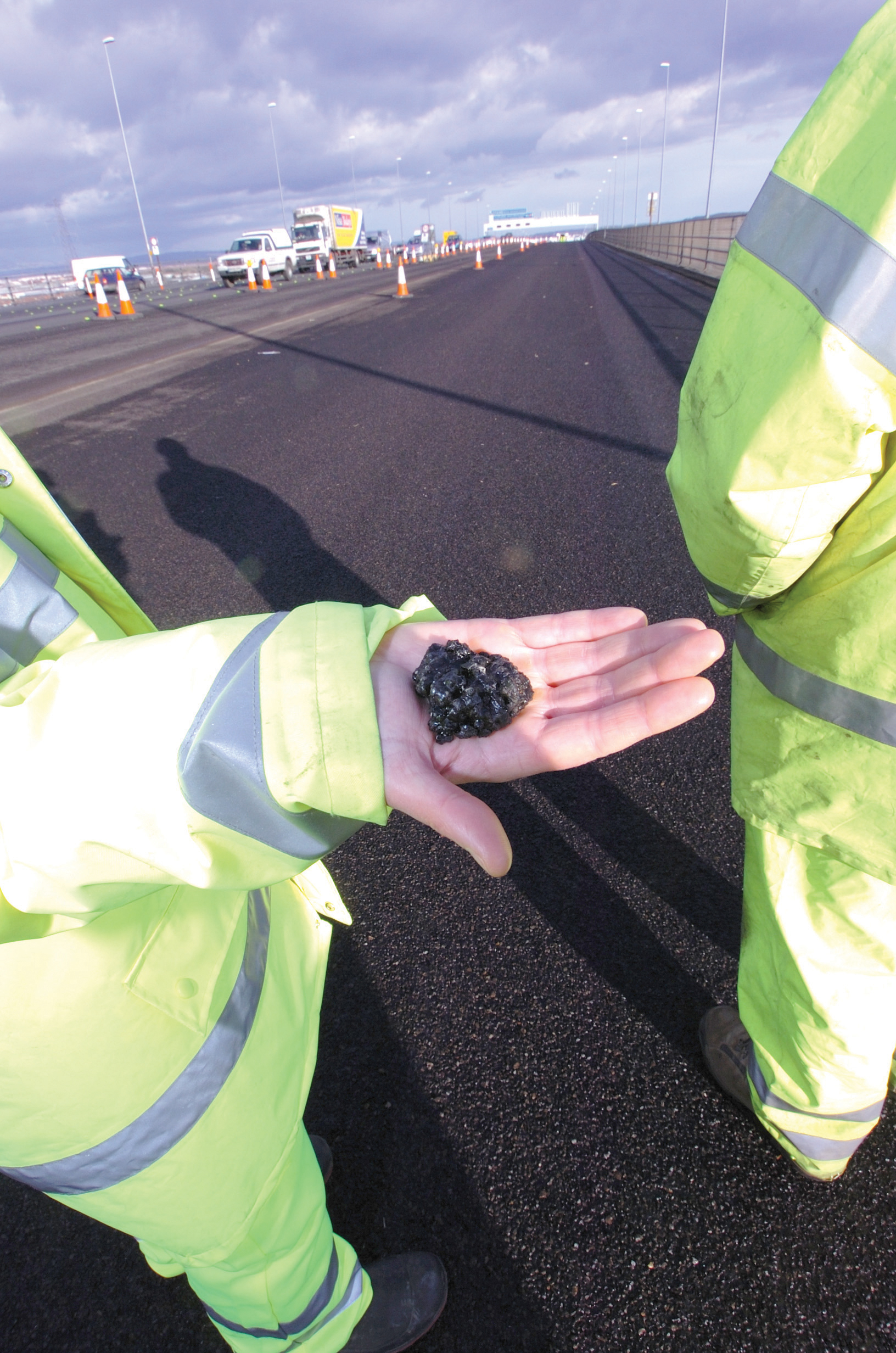
Ashpalt with a high-tech bitumen binder being laid as surfacing on the 'lively' Avonmouth bridge
Choosing the correct high performance binder material for use in asphalt applications has been made easier following a product rebranding exercise by one company
Awareness among highway maintenance contractors of the benefits of selecting polymer modified bitumens when specifying road surfacing materials has risen markedly in the last few years.Additives within these special binders are designed to make asphalt more workable during application and resistant to deformation, fatigue or cracking when laid.
Advances in materials technology have also increased the range of polymer modified binders (PMBs) available from Nynas Bitumen and led to their greater use at road resurfacing sites across the United Kingdom.
But the ever-growing suite of products offered by
The first category of binders, Regular, do not contain special additives, and include penetration grade bitumens which meet European specifications and are designed to suit conventional asphalt mixes for road construction and maintenance applications.
The Extra range includes PMBs such as Nypave and Nypol, binders that tend to give an asphalt mix a greater degree of elasticity, helping to improve the material's durability. Products in the Extra range also feature those which provide a greater resistance to shearing stresses, which is important when, for example, racing cars corner at high speeds on a track.
Nynas Bitumen's Premium binders include far more complex polymers designed to offer a superior level of performance. Premium binders such as the Nynas Endura range are suitable for sites where heavy stresses are placed on a road surfacing, such as docks and bus depots.
Rebranding of the company's binders has been a thoroughly worthwhile exercise, says Jukka Laitinen, who is Nynas Bitumen's asphalt engineering support manager in the UK. "The Performance Programme has been launched so that we can clearly explain to customers from all across Europe the benefits of each binder within our entire product range. Not all products are available in each country and some have been developed specifically for local markets, but each binder is now named and ranked in a consistent manner." A key driver on many projects is the need for speed, and using polymers is seen by those in the know as a great way of allowing roads to be reopened sooner, as PMBs can allow materials to be laid at cooler temperatures.
"Workability can be an issue with asphalt when time is tight due to restricted closures of roads for surfacing works. Contractors need materials that can be used at lower temperatures and be fully compacted quickly, yet still have the vital high performance characteristics and offer environmental benefits," says Laitinen.
He adds that PMBs tend to be used within surface courses, but there is much to be gained from using them in base layers. Major schemes have just been carried out where both the surface and base layers contain PMBs to ensure maximum longevity and minimum intervention.
Indeed, PMBs covered by Nynas Bitumen's Performance Programme have been used to great effect at a series of high profile road renewal sites around Europe.
The company's Endura Z2 (one of the Premium range of hot mix materials) was used in the resurfacing of Oxford Circus, a busy traffic interchange in central London. It was specified for a new binder course material, designed to reduce both deformation of the road surface and wheel rutting caused by the passing of slow moving, heavy vehicles.
A variation of the binder, Nynas Endura N5, was specified in the resurfacing of the Avonmouth Bridge near Bristol, south-west England, where Gussasphalt, a dense mastic asphalt, was laid for its immense qualities of durability.
Nynas Bitumen's Extra range includes the Nypol binder, and one of its best selling and longest established products, Nypol S89, is being used by Midland Quarry Products within a new thin surfacing material, specified for road renewal projects with local authorities in the Midlands. Another product in the Extra range, Nypave PX, designed to be mixed at temperatures up to 30o less than conventional binders, contains polymers that improve the workability of an asphalt. This cooler binder allows a road to be trafficked sooner, and was recently used on the M8 in Scotland during overnight closures of the motorway.
Meanwhile,
The production temperature of WAM Foam Asphalt is 115°C, and this is achieved by first adding all aggregate with a diameter of more than 4mm to the mixer. Soft bitumen is then added to coat the rough additive. The hard bitumen is then processed into foam during the third and most important step. Sand and a very fine filler substance are then added to the drum, and a bitumen foaming ramp generates a precisely balanced and homogeneous foam that meets the high demands on quality.
The properties of the ensuing warm mix asphalt are similar to those of the hot mix asphalt produced at higher temperatures, says Ammann.
"Long-standing trials in the field have verified outstanding road surface properties. This technology puts asphalt producers in a position to reduce their CO2 emissions without having to compromise the high quality of their products," says the company.
Hot Mix Applications | Cold & Semi - Warm Applications: BITUMEN | Cold & Semi - Warm Applications: EMULSIONS | Cold & Semi - Warm Applications: CUT BACKS | Industrial Applications | |
Regular | Nynas (EN spec) | Nynas (EN spec) | Nynas (EN spec) | Nynas (EN spec) | Nynas (EN spec) |
Extra | Nypave Nypol Nybit | Nybit E Nyfoam | Nymuls | Nyflow | |
Premium | Nynas Endura | Nynas Endurabit | Nynas Enduramuls | Nynas Enduraflow | Nynas Enduratop |
Special technique
In Holland, engineering and consulting companyA special technique to produce a bitumen foam with adjustable foam stability was developed and patented. The basis of the procedure is the introduction of air into a liquid bitumen stream. The result is a bitumen binder containing 30-40% of air. The bitumen content of such foam is comparable to the binder content in a bitumen emulsion, and the stability of the foam can be adjusted to allow some delay between spraying and chipping.
The difference with bitumen emulsions and fluxed binders is that the applied amount of binder in a foam is identical to the residual amount of binder. So there are no losses and the layer thickness is the same as a layer of bitumen emulsion, providing the required embedding of the subsequently applied mineral aggregate chippings.
According to Altravie, compared to bitumen emulsions the savings on the applied product is at least 30%.
Another advantage compared to fluxed and cut-back bitumen is the absence of diluents and the relatively low application temperature (110°C for bitumen, 130° C for PMBs).
"The logistic advantage is obvious: as the binder is 100% residual, transportation is 100% efficient," says Altravie.
After the application of chippings and compaction, the aggregate can be removed leaving a safer driving surface and preventing windscreen damage.
The method has been tested successfully on a small scale, and larger trials are scheduled to determine the influence of cleanliness of the aggregate.
It is expected that the technique will be technically available in the next few months.