Most of the dual layer paving in Japan is performed by the Multi-Asphalt Paver, manufactured by SUMITOMO (S.H.I.) CONSTRUCTION MACHINERY CO., LTD (SUMITOMO) As per the introduction report to follow, this machine can simultaneously handle two different types of asphalt mixtures and can perform two kinds of paving methods.
First one is Dual layer paving (it is called Dual Asphalt Pavement method), and the second is Multi Lane Pavement method. Hereinafter, paving methods using the Multi-Asphalt Paver will be
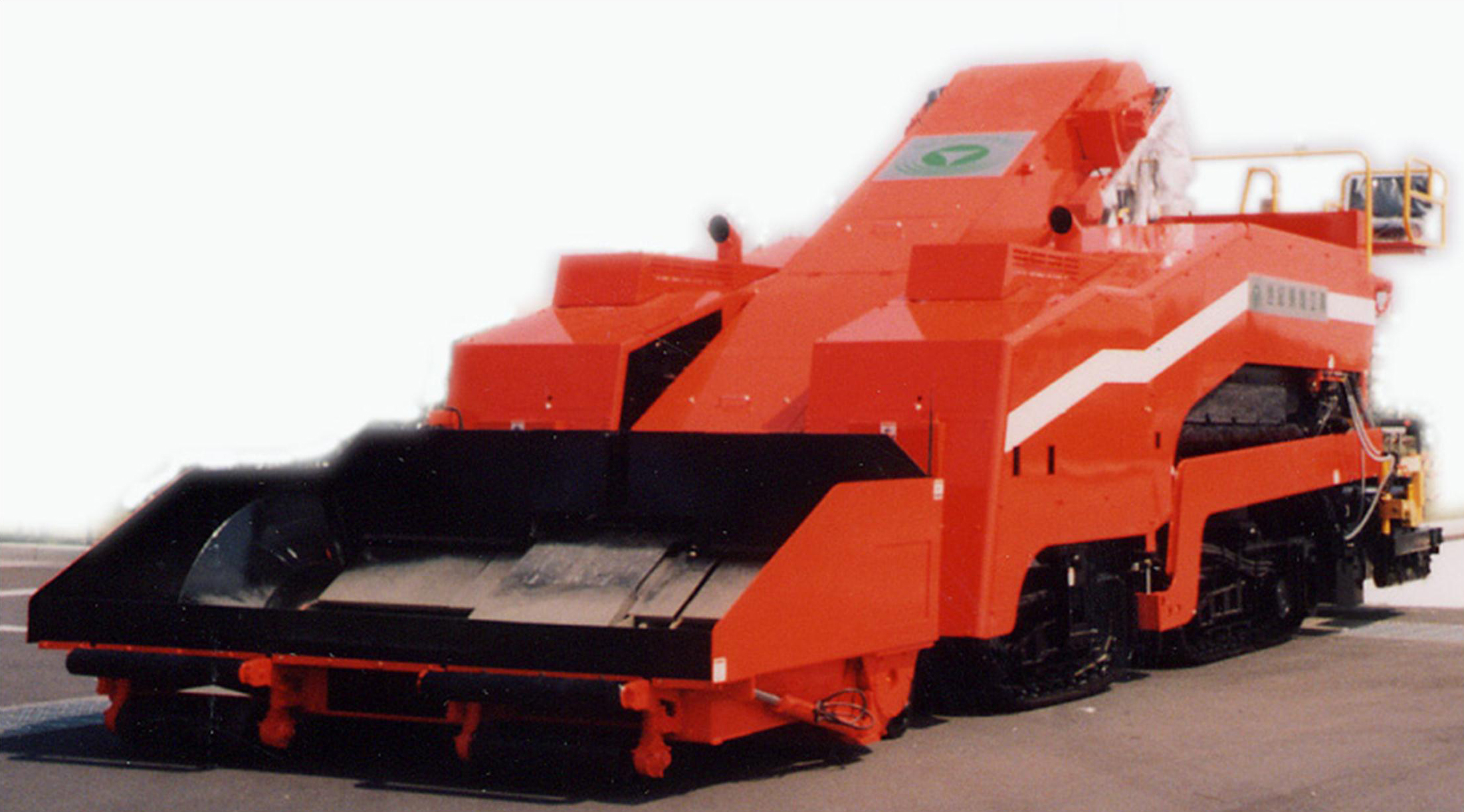
Appearance of MAP
Most of the dual layer paving in Japan is performed by the Multi-Asphalt Paver, manufactured by SUMITOMO (S.H.I.) CONSTRUCTION MACHINERY CO., LTD (SUMITOMO)
Against such a background, the MAP Technical Research Group in Japan composed of eight companies (six machine owners, a trading company and2714 SUMITOMO) has developed a MAP which serves to make paving work more efficient and rational and thereby to enable shortening of work periods and efficient use of expensive materials for functional pavements and has made a study on the construction by the MAP of low-noise pavements, color pavements and landscape pavements. This paper presents the mechanism and features of the MAP and the characteristics of the paving methods using the MAP together with case examples of pavement construction.
2. MULTI ASPHALT PAVER
2.1 Description
The MAP, an asphalt paver with two sets of hoppers and screeds, is capable of paving two layers, upper and lower, or plural lanes with two types of asphalt mixtures concurrently. The method of paving the upper and lower layers with two types of asphalt mixtures concurrently is referred to as the DAP method, and the method of paving plural lanes with two types of asphalt mixtures concurrently is referred to as the MLP method. The DAP method was also in Europe. However, its practical use proceeded in Japan. The MLP method was implemented for the first time in the world. The appearance of the MAP in the process of paving by the DAP method is shown in Photo 1.
The MAP specifications are listed in Table 1. In this table, the Nos. 1-8 machines produced so far are classified into three types by machine specifications.
Table 1: Specifications of the MAP
2.2 Features of the MAP
The features of the MAP are as follows:
1) The MAP is a machine equipped with a charger and two sets of hoppers and screeds.
2) Two screeds are attached to a pair of leveling arms, so the paving thickness is easily changeable.
3) The leveling arm is longer than that of an conventional paver, so surface smoothness can be expected to be ensured.
4) When replaced with the screed for lower layers, and with the attachment for MLP, it will become MLP method specification.
The No. 8 machine shown in Photo 2 is a new type brought to completion in December 2008, which is designed to be smaller in size than conventional machines as shown in Table 1. Different from the conventional type with two engines, the No. 8 machine (Type Ⅲ) has one engine, but is equivalent to the former in working capability. Therefore, it satisfies the standard values for both exhaust gas and noise of construction machines designated by the Ministry of Land, Infrastructure and Transport and enables 50% reduction of fuel consumption and CO2 emissions.
A transfer flow of the asphalt mixture fed to the MAP is shown below and a transfer route in Figure1.
1) The asphalt mixture for the lower layer or for the upper layer is fed to the charging hopper.
2) A flight conveyor is used to transfer the asphalt mixture for the upper layer to the hopper for the upper layer and the asphalt mixture for the lower layer to the hopper for the lower layer. The damper positions are changed to switch between the hoppers to which to transfer the asphalt mixture.
3) The asphalt mixture for the lower layer is transferred to the lower layer screed by a bar feeder, and the asphalt mixture for the upper layer is transferred to the upper layer screed by a spread roll or screw.
4) The asphalt mixture fed to the upper/lower layer screed is compacted by the action of a tamper vibrator. In the case of the Type Ⅲ and Type Ⅰ machines, the asphalt mixture fed to the lower layer screed is compacted by the action of the tamper only.
3.2 Characteristics of the Method
The characteristics of the DAP method are as follows:
1) When designing pavements such as cooler pavement that uses a pigment or decolorized asphalt, the paving cost can be reduced by dividing the surface course into two layers, upper and lower, and applying the higher-cost asphalt mixture for the upper layer only.
2) The two layers can be paved concurrently by feeding the mixture for the surface course and the mixture for the base course to the MAP, so it is clear that a tack coat between the layers is not necessary. Therefore, the paving cost can be reduced.
3) The maximum spreading thickness of the upper layer is 60 mm, the minimum spreading thickness of the upper layer is 20 mm and the maximum spreading thickness of the two layers is 120 mm.
4) One layer placement by using the upper layer screed enables the maximum spreading thickness of 200 mm.
3.3 Pavement Applying the DAP Method
Figure 1 shows an example of the pavement structure applying this method. As shown in Figure 1, the DAP method can be classified broadly into a method of dividing the surface course (4-7 cm thick) into two layers, upper and lower, and paving them concurrently and a method of paving the surface and base courses (8-12 cm thick in total) concurrently. The method of dividing the surface course into the upper and lower layers can be classified broadly into a dual-layer low-noise pavement method applying a porous mixture for the upper and lower layers and a thin-layer pavement method applying a mixture with a specific feature such as color mixture and anti-freezing mixture, for the surface course.
A description is made here of special techniques for controlling workmanship and quality which are different from those used for ordinary pavement construction.
1) Workmanship control (thickness control)
In the case of paving by the MAP, a paving thickness is set for the upper layer and the whole layers. so the lower layer serves as a leveling layer to correct the unevenness of the paving foundation. For the sake of paving thickness control, therefore, the upper layer thickness and total layer thickness of a specimen are determined by a measuring device such as caliper and the lower layer thickness is calculated by subtracting the upper layer thickness from the whole layer thickness.
2) Quality control (degree of compaction)
The standard density of a combination of the upper and lower layer sections of the specimen (hereinafter referred to as the combined standard density) is calculated by equation(1) and the degree of compaction of the specimen is determined by equation(2)applying its density:
Combined standard density = (standard density of upper layer mixture)
×(upper layer thickness) / (whole layer thickness)
+(standard density of lower layer mixture)
×(lower layer thickness) / (whole layer thickness) (1)
Degree of compaction = (density of specimen) / (combined standard density)×100 (2)
(1) Dual-layer low-noise pavement
1) Description
The dual-layer low-noise pavement by the DAP method is a pavement in which the surface course is divided into the upper and lower layers and porous asphalt mixtures different in maximum aggregate grain size are applied for them. Usually, the surface course is formed of two layers by using a porous asphalt mixture 5-10 mm in maximum aggregate grain size (hereinafter referred to as the small grain size porous asphalt mixture) for the upper layer and a porous asphalt mixture 13 mm in maximum aggregate grain size (hereinafter referred to as the ordinary porous asphalt mixture) for the lower layer.
2) Performance and effect
Figure 2 shows the results of the tire/road noise measured on various pavements including dual-layer and single-layer low-noise pavements on selected Tokyo metropolitan highways.
According to the results of tire/road noise measured by a pavement surface noise level measuring vehicle, a noise reduction effect of about 10 dB as compared with dense grade asphalt pavements is obtained though the degree of noise reduction varies with such conditions as the roadside and traffic volume.
The small grain-size porous asphalt mixture is inferior to the ordinary porous asphalt mixture in rutting resistance.
However, it can be confirmed that its dynamic stability is expected to improve by adopting the dual-layer structure in which an aggregate larger than that of the upper layer is used for the lower layer as shown in Table 2.
(2) Thin-layer porous asphalt
1) Description
The porous asphalt mixture and the impermeable layer beneath it are placed concurrently to make the porous pavement into a thin-layer structure.
2) Performance and effect
The consumption of the expensive porous asphalt mixture can be decreased, so the paving cost can be reduced by 10% as compared with the cost of paving with a thickness of 5 cm.
(3) Color pavement
1) Description
The mixture used for color pavement is a very expensive material because it uses a color aggregate, decolorized binder or pigment. The color pavement is made into a thin-layer structure by placing the color mixture and ordinary mixture beneath it concurrently.
2) Performance and effect
The consumption of the expensive porous asphalt mixture can be decreased, so the paving cost is reduced by 20-40% as compared with the cost of paving with a thickness of 5 cm. The degree of cost reduction varies with the type of mixture used.
(4) Concurrent paving of the surface and base courses
1) Description
Different from the usual practice of paving the surface course after paving the base course, the surface course and base course mixtures are placed concurrently.
2) Performance and effect
The two layers can be paved concurrently, so it is possible to shorten the process and lessen the effects on the traffic around the work site.
Table 2:Dynamic Stability (DS) of Dual Layer Porous Asphalt
The flow of the mixture from the point of feeding to the MAP to that of the hoppers for the upper and lower layers is the same as that described in Items 1),2) and 3), Paragraph (1) of Section 3.1 “Mechanism (transfer and compaction of mixture).”
4) The mixture for the sections of wheel paths is stored in the hopper for the lower layer and the mixture for the section of between them in the hopper for the upper layer.
5) As the lower layer screed is removed at the time of unit change, the mixtures for wheel paths and the section of between them are compacted by the action of the tamper vibrator by the upper layer screed.
4.2 Characteristics of the Method
The characteristics of the MLP method are as follows:
(1) The width of each wheel paths 1,000 mm and the width of the middle 710 mm.
(2) Two wheel paths and the middle can be shifted 80 mm horizontally at the time of paving.
(3) As this method applies a mixture for specified purposes, for the section of wheel paths only, pavement construction can be done inexpensively as compared with the method of applying the mixture over the entire width.
4.3 Pavements Applying the MLP Method
(1) Rutting resistance and wear resistance pavements
1) Description
Rutting-resistant and wear-resistant pavements can be constructed at a reduced cost by applying a rutting resistance and a wear resistance asphalt mixtures for the sections of wheel path and an ordinary asphalt mixture for the section between them.
Photo 3 shows an appearance of the pavement after put into service. The paving thickness is 4 cm.
A dense-graded asphalt mixture using polymer-modified asphalt is applied for the section of wheel path (the section deep in color in Photo 3) and a recycled mixture for the middle section (Photo 3) .
2) Performance and effect
The consumption of the expensive material can be decreased by using a rutting-resistant or wear-resistant mixture for the sections between the wheel paths, so that it becomes possible to achieve a cost reduction of about 10%.
(2) Landscape pavement
1) Description
A pavement excellent in appearance is constructed by using two types of mixtures of different colors alternately for five paths.
2) Performance and effect
The consumption of the expensive material when combined with an ordinary mixture can be decreased as compared with that in the case of full-width color pavement so that it becomes possible to achieve a cost reduction of about 10%.
Rutting-resistant and wearing-resistant pavements can be constructed economically.
Concerning low-noise pavements using the DAP method, a confirmation was made of a tire/road noise reduction effect of about 10 dB as compared with dense grade asphalt pavements using the general paver. Rutting-resistant and wearing-resistant pavements only applied for wheel paths by using the MLP method, can achieve a cost reduction of about 10%.
Furthermore, inquiry from overseas has been increasing since the introduction of MAP at I.S.A.P. in 2010.
Although it was considered as a Japan domestic exclusive model due to the complexity of MAP, from now on we will be moving on to spread sales to the other countries outside of Japan.
1) T. Sekiguchi, A. Hirano, and T. Fujieda: Development of a New Asphalt Finisher Capable of Paving Two Layers Concurrently, Proceedings of the 64th Annual Academic Lecture Meeting, Society of Civil Engineering, Japan.2009
2) T. Takeda, J. Minegishi, and T. Matsumura: A Study on Noise Reduction Effect and Applicability of Various Low Noise Pavements, Proceedings of 23rd Japan Road Conference, 1999.
3) T. Matsuda: Paving Method using a Multi Asphalt Paver, Proceeding of I.S.A.P., 2010
As per the introduction report to follow, this machine can simultaneously handle two different types of asphalt mixtures and can perform two kinds of paving methods. First one is Dual layer paving (it is called Dual Asphalt Pavement method), and the second is Multi Lane Pavement method.
Hereinafter, paving methods using the Multi-Asphalt Paver will be explained.
1. INTRODUCTION
In Japan, the percentage of paved roads can be said to have increased with the development of proportion of the auto industry in the transport of goods and people. And sophisticated pavements have been developed and established which can respond to increases in size, speed and traffic volume of motor vehicles due to the industry’s development. In recent years, needs for pavements have been diversified as is evident from increasing construction of porous pavements for the safety of motor vehicles, low-noise pavements for the benefit of roadside residents, functional pavements such as colorized bus lanes, growing demands for construction cost reduction and CO2 emission reduction for global environment protection.Against such a background, the MAP Technical Research Group in Japan composed of eight companies (six machine owners, a trading company and
2. MULTI ASPHALT PAVER
2.1 DescriptionThe MAP, an asphalt paver with two sets of hoppers and screeds, is capable of paving two layers, upper and lower, or plural lanes with two types of asphalt mixtures concurrently. The method of paving the upper and lower layers with two types of asphalt mixtures concurrently is referred to as the DAP method, and the method of paving plural lanes with two types of asphalt mixtures concurrently is referred to as the MLP method. The DAP method was also in Europe. However, its practical use proceeded in Japan. The MLP method was implemented for the first time in the world. The appearance of the MAP in the process of paving by the DAP method is shown in Photo 1.
The MAP specifications are listed in Table 1. In this table, the Nos. 1-8 machines produced so far are classified into three types by machine specifications.
Table 1: Specifications of the MAP
Item | Unit | Type 1 - Nos. 1-4 machines | Type 2 - Nos. 5-7 machines | Type 3 - No.8 Machine | |
---|---|---|---|---|---|
Total Length (at work) | mm | 10,200 | 10,470 | 9,760 | |
Total Width (at work) | mm | 2990 | 3,000 | ||
Total Height (at work) | mm | 3,800 | 4,220 | 4,250 | |
Total weight | kg | 25,000 | 27,500 | 23,500 | |
Paving width | m | 2.5-6.0 | 2.5-4.5 | ||
Engine output | kw | 96 x 2 units | 138 x 2 units | 132.1 | |
Running speed (at work) | m/min | 1-10 | 1.5-12 | ||
Screed | Upper layer | | | | |
| Lower layer | Tamper type | Tamper vibrator type | Tamper type | |
Hopper Capacity | Upper and Lower layers | m3 | Upper and Lower layers: 6.5 each | Upper and Lower layers: 6.5 each | Upper Layer: 6.5 Lower Layer: 2.8 |
2.2 Features of the MAP
The features of the MAP are as follows:
1) The MAP is a machine equipped with a charger and two sets of hoppers and screeds.
2) Two screeds are attached to a pair of leveling arms, so the paving thickness is easily changeable.
3) The leveling arm is longer than that of an conventional paver, so surface smoothness can be expected to be ensured.
4) When replaced with the screed for lower layers, and with the attachment for MLP, it will become MLP method specification.
The No. 8 machine shown in Photo 2 is a new type brought to completion in December 2008, which is designed to be smaller in size than conventional machines as shown in Table 1. Different from the conventional type with two engines, the No. 8 machine (Type Ⅲ) has one engine, but is equivalent to the former in working capability. Therefore, it satisfies the standard values for both exhaust gas and noise of construction machines designated by the Ministry of Land, Infrastructure and Transport and enables 50% reduction of fuel consumption and CO2 emissions.
In addition, this new type model is based on the general paver, HA90C manufactured by SUMITOMO.
3. DAP METHOD
3.1 Mechanism (transfer and compaction of asphalt mixture)A transfer flow of the asphalt mixture fed to the MAP is shown below and a transfer route in Figure1.
1) The asphalt mixture for the lower layer or for the upper layer is fed to the charging hopper.
2) A flight conveyor is used to transfer the asphalt mixture for the upper layer to the hopper for the upper layer and the asphalt mixture for the lower layer to the hopper for the lower layer. The damper positions are changed to switch between the hoppers to which to transfer the asphalt mixture.
3) The asphalt mixture for the lower layer is transferred to the lower layer screed by a bar feeder, and the asphalt mixture for the upper layer is transferred to the upper layer screed by a spread roll or screw.
4) The asphalt mixture fed to the upper/lower layer screed is compacted by the action of a tamper vibrator. In the case of the Type Ⅲ and Type Ⅰ machines, the asphalt mixture fed to the lower layer screed is compacted by the action of the tamper only.
3.2 Characteristics of the Method
The characteristics of the DAP method are as follows:
1) When designing pavements such as cooler pavement that uses a pigment or decolorized asphalt, the paving cost can be reduced by dividing the surface course into two layers, upper and lower, and applying the higher-cost asphalt mixture for the upper layer only.
2) The two layers can be paved concurrently by feeding the mixture for the surface course and the mixture for the base course to the MAP, so it is clear that a tack coat between the layers is not necessary. Therefore, the paving cost can be reduced.
3) The maximum spreading thickness of the upper layer is 60 mm, the minimum spreading thickness of the upper layer is 20 mm and the maximum spreading thickness of the two layers is 120 mm.
4) One layer placement by using the upper layer screed enables the maximum spreading thickness of 200 mm.
3.3 Pavement Applying the DAP Method
Figure 1 shows an example of the pavement structure applying this method. As shown in Figure 1, the DAP method can be classified broadly into a method of dividing the surface course (4-7 cm thick) into two layers, upper and lower, and paving them concurrently and a method of paving the surface and base courses (8-12 cm thick in total) concurrently. The method of dividing the surface course into the upper and lower layers can be classified broadly into a dual-layer low-noise pavement method applying a porous mixture for the upper and lower layers and a thin-layer pavement method applying a mixture with a specific feature such as color mixture and anti-freezing mixture, for the surface course.
A description is made here of special techniques for controlling workmanship and quality which are different from those used for ordinary pavement construction.
1) Workmanship control (thickness control)
In the case of paving by the MAP, a paving thickness is set for the upper layer and the whole layers. so the lower layer serves as a leveling layer to correct the unevenness of the paving foundation. For the sake of paving thickness control, therefore, the upper layer thickness and total layer thickness of a specimen are determined by a measuring device such as caliper and the lower layer thickness is calculated by subtracting the upper layer thickness from the whole layer thickness.
2) Quality control (degree of compaction)
The standard density of a combination of the upper and lower layer sections of the specimen (hereinafter referred to as the combined standard density) is calculated by equation(1) and the degree of compaction of the specimen is determined by equation(2)applying its density:
Combined standard density = (standard density of upper layer mixture)
×(upper layer thickness) / (whole layer thickness)
+(standard density of lower layer mixture)
×(lower layer thickness) / (whole layer thickness) (1)
Degree of compaction = (density of specimen) / (combined standard density)×100 (2)
(1) Dual-layer low-noise pavement
1) Description
The dual-layer low-noise pavement by the DAP method is a pavement in which the surface course is divided into the upper and lower layers and porous asphalt mixtures different in maximum aggregate grain size are applied for them. Usually, the surface course is formed of two layers by using a porous asphalt mixture 5-10 mm in maximum aggregate grain size (hereinafter referred to as the small grain size porous asphalt mixture) for the upper layer and a porous asphalt mixture 13 mm in maximum aggregate grain size (hereinafter referred to as the ordinary porous asphalt mixture) for the lower layer.
2) Performance and effect
Figure 2 shows the results of the tire/road noise measured on various pavements including dual-layer and single-layer low-noise pavements on selected Tokyo metropolitan highways.
According to the results of tire/road noise measured by a pavement surface noise level measuring vehicle, a noise reduction effect of about 10 dB as compared with dense grade asphalt pavements is obtained though the degree of noise reduction varies with such conditions as the roadside and traffic volume.
The small grain-size porous asphalt mixture is inferior to the ordinary porous asphalt mixture in rutting resistance.
However, it can be confirmed that its dynamic stability is expected to improve by adopting the dual-layer structure in which an aggregate larger than that of the upper layer is used for the lower layer as shown in Table 2.
(2) Thin-layer porous asphalt
1) Description
The porous asphalt mixture and the impermeable layer beneath it are placed concurrently to make the porous pavement into a thin-layer structure.
2) Performance and effect
The consumption of the expensive porous asphalt mixture can be decreased, so the paving cost can be reduced by 10% as compared with the cost of paving with a thickness of 5 cm.
(3) Color pavement
1) Description
The mixture used for color pavement is a very expensive material because it uses a color aggregate, decolorized binder or pigment. The color pavement is made into a thin-layer structure by placing the color mixture and ordinary mixture beneath it concurrently.
2) Performance and effect
The consumption of the expensive porous asphalt mixture can be decreased, so the paving cost is reduced by 20-40% as compared with the cost of paving with a thickness of 5 cm. The degree of cost reduction varies with the type of mixture used.
(4) Concurrent paving of the surface and base courses
1) Description
Different from the usual practice of paving the surface course after paving the base course, the surface course and base course mixtures are placed concurrently.
2) Performance and effect
The two layers can be paved concurrently, so it is possible to shorten the process and lessen the effects on the traffic around the work site.
Table 2:Dynamic Stability (DS) of Dual Layer Porous Asphalt
No | Name of Mixture | Max. Aggregate grain size (mm) | Void Ratio (%) | Layer thickness (cm) | DS of layer(cycles/mm) | DS of dual-layer specimen (cycles/mm) | |
---|---|---|---|---|---|---|---|
1 | Upper Layer - Small grain size porous asphalt mixture | 5 | 22.6 | 2 | 3,316 | 5,250 | |
Lower layer - Ordinary porous asphalt mixture | 13 | 20.3 | 3 | 7,000 | |||
| |||||||
2 | Upper layer - Small grain size porous asphalt mixture | 8 | 23.1 | 2 | 4,900 | 7,000 | |
Lower Layer - Ordinary porous asphalt mixture | 13 | 19.3 | 3 | 8,800 |
4 MLP METHOD
4.1 Mechanism (transfer and compaction of mixture)The flow of the mixture from the point of feeding to the MAP to that of the hoppers for the upper and lower layers is the same as that described in Items 1),2) and 3), Paragraph (1) of Section 3.1 “Mechanism (transfer and compaction of mixture).”
4) The mixture for the sections of wheel paths is stored in the hopper for the lower layer and the mixture for the section of between them in the hopper for the upper layer.
5) As the lower layer screed is removed at the time of unit change, the mixtures for wheel paths and the section of between them are compacted by the action of the tamper vibrator by the upper layer screed.
4.2 Characteristics of the Method
The characteristics of the MLP method are as follows:
(1) The width of each wheel paths 1,000 mm and the width of the middle 710 mm.
(2) Two wheel paths and the middle can be shifted 80 mm horizontally at the time of paving.
(3) As this method applies a mixture for specified purposes, for the section of wheel paths only, pavement construction can be done inexpensively as compared with the method of applying the mixture over the entire width.
4.3 Pavements Applying the MLP Method
(1) Rutting resistance and wear resistance pavements
1) Description
Rutting-resistant and wear-resistant pavements can be constructed at a reduced cost by applying a rutting resistance and a wear resistance asphalt mixtures for the sections of wheel path and an ordinary asphalt mixture for the section between them.
Photo 3 shows an appearance of the pavement after put into service. The paving thickness is 4 cm.
A dense-graded asphalt mixture using polymer-modified asphalt is applied for the section of wheel path (the section deep in color in Photo 3) and a recycled mixture for the middle section (Photo 3) .
2) Performance and effect
The consumption of the expensive material can be decreased by using a rutting-resistant or wear-resistant mixture for the sections between the wheel paths, so that it becomes possible to achieve a cost reduction of about 10%.
(2) Landscape pavement
1) Description
A pavement excellent in appearance is constructed by using two types of mixtures of different colors alternately for five paths.
2) Performance and effect
The consumption of the expensive material when combined with an ordinary mixture can be decreased as compared with that in the case of full-width color pavement so that it becomes possible to achieve a cost reduction of about 10%.
5. CONCLUSION
Various paving methods using MAP have been described here, by which low-noise pavements or thin layer pavements can be constructed.Rutting-resistant and wearing-resistant pavements can be constructed economically.
Concerning low-noise pavements using the DAP method, a confirmation was made of a tire/road noise reduction effect of about 10 dB as compared with dense grade asphalt pavements using the general paver. Rutting-resistant and wearing-resistant pavements only applied for wheel paths by using the MLP method, can achieve a cost reduction of about 10%.
Furthermore, inquiry from overseas has been increasing since the introduction of MAP at I.S.A.P. in 2010.
Although it was considered as a Japan domestic exclusive model due to the complexity of MAP, from now on we will be moving on to spread sales to the other countries outside of Japan.
REFERENCES
1) T. Sekiguchi, A. Hirano, and T. Fujieda: Development of a New Asphalt Finisher Capable of Paving Two Layers Concurrently, Proceedings of the 64th Annual Academic Lecture Meeting, Society of Civil Engineering, Japan.2009
2) T. Takeda, J. Minegishi, and T. Matsumura: A Study on Noise Reduction Effect and Applicability of Various Low Noise Pavements, Proceedings of 23rd Japan Road Conference, 1999.
3) T. Matsuda: Paving Method using a Multi Asphalt Paver, Proceeding of I.S.A.P., 2010