Four job sites, four contractors, four German states, one paving method: Dual-layer concrete paving with the slipform paver SP 1500 from Wirtgen is on the road to success in Germany. Swayed by the numerous economic and technical advantages, more and more planning engineers are opting for this technology when rehabilitating concrete highways.
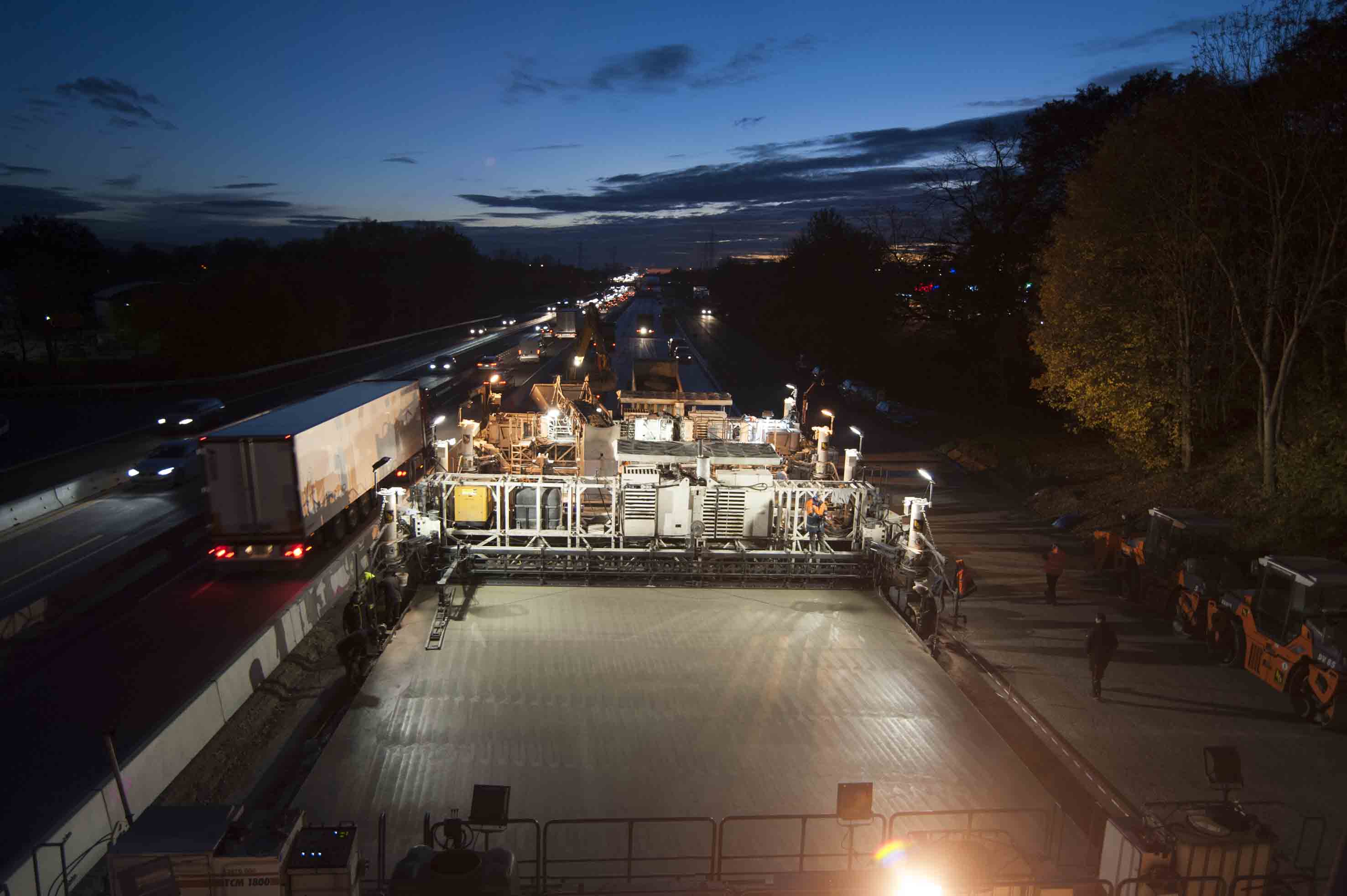
Round-the-clock paving by the Bickhardt Bau team on the A5 near Karlsruhe-Durlach. The Wirtgen SP 1500 really hit the mark on this job: its great flexibility enabled the concrete paver to quickly be reconfigured as required after 1 km
Dual-layer paving is first choice: Wirtgen SP 1500 efficiently paves exposed aggregate concrete on four job sites
Four job sites, four contractors, four German states, one paving method: Dual-layer concrete paving with the slipform paver %$Linker:2 External <?xml version="1.0" encoding="utf-16"?><dictionary /> 0 0 0 oLinkExternal SP 1500 Visit Wirtgen website false http://www.wirtgen.de/en/line-products/slipform-pavers/inset-slipform-pavers/sp1500.php false false %> from 2395 Wirtgen is on the road to success in Germany. Swayed by the numerous economic and technical advantages, more and more planning engineers are opting for this technology when rehabilitating concrete highways.
Attentive observers will notice that dual-layer concrete paving is currently being used in the rehabilitation of many German highways. This is because noise-reducing non-skid exposed aggregate concrete pavements can be placed most economically with this method. The concept: Bottom-layer concrete is paved on a high-grade subbase with a high load-bearing capacity. This layer is normally 20 – 24 cm thick. It is overlaid with a top layer of exposed aggregate concrete which is normally between 5 and 8 cm thick.
Coarse aggregate, i.e. material > 2 mm in size, is particularly important in the top layer of exposed aggregate concrete. Only double broken and double screened chippings which meet high demands in terms of angularity, grain shape and resistance to polishing are used in order to ensure that the concrete surfacing retains its noise-reducing properties and remains skid-resistant and durable in the long term.
When the two layers of concrete have been paved, a surface retarding agent is uniformly applied to the freshly smoothed surface by a texture curing machine (TCM) which matches the SP 1500 and is also built by Wirtgen. Depending on the prevailing climatic conditions, the coarse aggregate is exposed by brooming the surface just a few hours after placing the concrete pavement. The result is a non-skid surface with a large number of profile peaks and a texture which durably minimizes tire noise.
Four typical projects highlight the advantages of this method and show which features of the SP 1500 (four-crawler model) / %$Linker:2 External <?xml version="1.0" encoding="utf-16"?><dictionary /> 0 0 0 oLinkExternal SP 1500L Visit Wirtgen SP 1500L machine false http://www.wirtgen.de/en/line-products/slipform-pavers/inset-slipform-pavers/sp1500l.php false false %> (two-crawler model) from Wirtgen have a decisive impact on success. Three of the projects concerned the rehabilitation of concrete roadways between 30 and 40 years old. The fourth project, in Saxony-Anhalt, involved the rehabilitation of a stretch of highway with alkali-silica reaction (ASR).
• 4.5-km rehabilitation of the A1 near Trier (Rhineland-Palatinate) by8553 Berger Bau
• 4.8-km rehabilitation of a section of the A9 with ASR near Weissenfels (Saxony-Anhalt) by8554 Max Bögl
• 2.3-km rehabilitation of the A5 near Karlsruhe (Baden-Württemberg) by3357 Bickhardt Bau
• 5.3-km rehabilitation of the A1 near Lübeck (Schleswig-Holstein) by3281 Eurovia Beton
The technical procedure is as follows: The bottom-layer concrete is dumped directly in front of the paver. The top-layer concrete is delivered to the second machine via a conveyor. To this end, the concrete is either filled directly from the truck into a material hopper or intermediate container – each contractor uses its own process here. The further procedure is then the same in all cases: Conveyors and a chute at the end of the conveyor dump the top-layer concrete on the fully compacted bottom-layer concrete behind the first paver.
A sufficient supply of both concrete grades is essential to assure the success of the paving work. Little wonder that Christoph Hofmeister, Head of Division at Max Bögl, sees logistics as the biggest challenge when paving concrete in two layers: "For the project on the A9, we had a steady stream of 45 articulated trucks carrying between 6,500 t and 7,000 t of sand, gravel and chippings every day during the paving phase, in addition to 27 trainloads of cement. This is equivalent to roughly 750 t of binder. It is currently the largest mobile plant in the world. Building this concrete roadway meant orchestrating a complex system of machines, material, weather, ambient conditions – and people. To assure the project's success, not only did the technical equipment need to operate faultlessly, but the team had to work hand-in-hand, communicating swiftly and clearly."
The sophisticated proportional control system which has proved its value over many years is another quality feature of concrete paving with the SP 1500. The machine operator can see all the parameters required for the paving process on the main control panel. The control system then adapts the height quickly and precisely without overshooting. This results in level roadways – a quality feature which ensures driving comfort and also helps to reduce noise, as recent studies have shown.
In this case, a combination of surface retarding agent and dispersion is applied to the finished and smoothed surface in precisely metered quantities. The retarding agent delays the setting and initial hardening of the concrete surface (approx. 1 mm) for a limited time, while the dispersion prevents the concrete surface from drying out and cracking. As soon as the concrete has cured sufficiently to be driven over, the surface is brushed to expose the coarse aggregate. An additional dispersion is then applied to the brushed surface. Exposing the coarse aggregate gives the concrete pavement the required non-skid properties which are subsequently of high importance for traffic safety.
This is confirmed by Jörg Ackermann, Paving Foreman at Bickhardt Bau: "The SP 1500 was needed on different sections here on the A5. The paver also had to be moved across bridges. The very narrow transport width is a great aid, as it allows the machine to be relocated rapidly, with little assembly and disassembly effort."
Christoph Hofmeister from Max Bögl mentioned two further points in favor of the four-crawler machines: "In a four-crawler bottom-layer paver, the dowel bar inserter is located between the crawler tracks. As a result, it can be monitored and reached more easily. Last but not least, the top-layer paver, in particular, displays greater stability as a four-crawler model because the geometry of the swivel arms results in a more advantageous lever spacing and an optimum balance of forces and torsion."
In addition, Wirtgen offers numerous optional extras with which contractors can individually configure their specific SP 1500. Eurovia Beton, for instance, equipped its top-layer paver with cameras which ensure that the paver operator always has a clear view of the finished concrete.
The vibrators also come in several different versions. To compact the top-layer concrete, for instance, three of the contractors chose electric T-vibrators which are particularly suitable for paving thin layers. Bickhardt Bau preferred a different solution and uses vibrating frames with external vibrators.
Corporate Communications
Michaela Adams, Mario Linnemann
Reinhard-Wirtgen-Straße 2
53578 Windhagen
Germany
Phone: +49 (0) 2645 131 – 0
Fax: +49 (0) 2645 131 – 499
E-mail: %$Linker:2 Email <?xml version="1.0" encoding="utf-16"?><dictionary /> 0 0 0 oLinkEmail [email protected] email: [email protected] false mailto:[email protected] true false %>
%$Linker:2 External <?xml version="1.0" encoding="utf-16"?><dictionary /> 0 0 0 oLinkExternal www.wirtgen.com website www.wirtgen.com false http://www.wirtgen.com/ false false %>
Four job sites, four contractors, four German states, one paving method: Dual-layer concrete paving with the slipform paver %$Linker:
Attentive observers will notice that dual-layer concrete paving is currently being used in the rehabilitation of many German highways. This is because noise-reducing non-skid exposed aggregate concrete pavements can be placed most economically with this method. The concept: Bottom-layer concrete is paved on a high-grade subbase with a high load-bearing capacity. This layer is normally 20 – 24 cm thick. It is overlaid with a top layer of exposed aggregate concrete which is normally between 5 and 8 cm thick.
There are different types of concrete
The slipform paver places the two concrete grades wet-in-wet in a fully automated process. The requirements in respect of compressive strength, bending tensile strength and indirect tensile strength are the same for both the bottom layer and the top layer of exposed aggregate concrete. The composition of the concrete can, however, differ with regard to the grading curve, maximum aggregate size, cement content and requirements to be met by the mineral aggregate. While around 350 kg cement suffice per m³ in the bottom-layer concrete, 420 kg cement per m³ are required in the top layer of exposed aggregate concrete.Coarse aggregate, i.e. material > 2 mm in size, is particularly important in the top layer of exposed aggregate concrete. Only double broken and double screened chippings which meet high demands in terms of angularity, grain shape and resistance to polishing are used in order to ensure that the concrete surfacing retains its noise-reducing properties and remains skid-resistant and durable in the long term.
When the two layers of concrete have been paved, a surface retarding agent is uniformly applied to the freshly smoothed surface by a texture curing machine (TCM) which matches the SP 1500 and is also built by Wirtgen. Depending on the prevailing climatic conditions, the coarse aggregate is exposed by brooming the surface just a few hours after placing the concrete pavement. The result is a non-skid surface with a large number of profile peaks and a texture which durably minimizes tire noise.
Four typical projects highlight the advantages of this method and show which features of the SP 1500 (four-crawler model) / %$Linker:
• 4.5-km rehabilitation of the A1 near Trier (Rhineland-Palatinate) by
• 4.8-km rehabilitation of a section of the A9 with ASR near Weissenfels (Saxony-Anhalt) by
• 2.3-km rehabilitation of the A5 near Karlsruhe (Baden-Württemberg) by
• 5.3-km rehabilitation of the A1 near Lübeck (Schleswig-Holstein) by
Dual-layer paving – High quality at lower material costs
Cost-efficiency is one of the factors fueling the boom in dual-layer concrete paving with the SP 1500 train from Wirtgen. This method tangibly reduces the cost of construction, as the bottom-layer concrete and the top layer of exposed aggregate concrete are designed to meet different requirements. On the A1 near Trier, Berger Bau used the SP 1500 to pave a 20 cm-thick bottom-layer concrete pavement with 360 kg cement per m³ concrete and a maximum aggregate size of 22. Meanwhile, the 6 cm-thick top-layer concrete comprised a high-grade material mix with 420 kg cement per m³ concrete and 2/8 double broken and double screened chippings.Material logistics is a challenge
The biggest challenge with this method lies in the logistics: Two different materials are needed and must be available in the right place at the right time and in the right quantities, since they need to be placed wet-in-wet.The technical procedure is as follows: The bottom-layer concrete is dumped directly in front of the paver. The top-layer concrete is delivered to the second machine via a conveyor. To this end, the concrete is either filled directly from the truck into a material hopper or intermediate container – each contractor uses its own process here. The further procedure is then the same in all cases: Conveyors and a chute at the end of the conveyor dump the top-layer concrete on the fully compacted bottom-layer concrete behind the first paver.
A sufficient supply of both concrete grades is essential to assure the success of the paving work. Little wonder that Christoph Hofmeister, Head of Division at Max Bögl, sees logistics as the biggest challenge when paving concrete in two layers: "For the project on the A9, we had a steady stream of 45 articulated trucks carrying between 6,500 t and 7,000 t of sand, gravel and chippings every day during the paving phase, in addition to 27 trainloads of cement. This is equivalent to roughly 750 t of binder. It is currently the largest mobile plant in the world. Building this concrete roadway meant orchestrating a complex system of machines, material, weather, ambient conditions – and people. To assure the project's success, not only did the technical equipment need to operate faultlessly, but the team had to work hand-in-hand, communicating swiftly and clearly."
Wirtgen SP 1500: One train – two machines
Once the logistics is well organized, precise high-grade paving is assured by the intelligent technology of the Wirtgen machines. The sub-processes are divided between two machines. The bottom-layer paver is equipped with dowel bar and tie bar inserters, while the top-layer paver uses a finishing beam and super smoother to produce a level surface. Both slipform pavers feature an intelligent control system ensuring a perfect paved result. The surface is subsequently finished as desired by a texture curing machine of type TCM 1800.Intelligent dowel bar and tie bar inserter
The integrated dowel bar and tie bar inserter is one of the technical highlights of the SP 1500 from Wirtgen. Dowel bars and tie bars are inserted in the pre-compacted wet concrete at freely determined intervals by these two fully automatic vibrating components. The process for inserting the dowel bars is quite ingenious: Because the dowel bar inserter can move in the direction of paving, it can remain in position over the transverse joint until the vibratory insertion process is complete, while the slipform paver continues to advance uniformly. The entire procedure is monitored electronically to assure that the dowel bars are positioned correctly. For the projects described here, the dowel bars were typically positioned in the middle of the finished concrete surfacing, i.e. at intervals of 14-15 cm and exactly as specified by the regulation ZTV Beton (Additional technical contract conditions and guidelines for the construction of roadway surfacings made of concrete). A closed, even and homogeneous surface was then assured by a finishing beam and super smoother integrated in the top-layer paver.Surface accuracy thanks to sensors in the front metering screed and proportional control system
So that roadways can be paved with maximum surface accuracy, three of the four contractors use specially developed sensors to adjust the height of the front metering screed. These sensors continuously measure the filling level of the concrete in the compaction zone and adjust the height of the front metering screed accordingly. This ensures that the amount of concrete delivered to the compaction zone is exactly as required. Dirk Böttcher, Project Manager for Eurovia Beton, explains the advantage: "This relieves the paver operator, particularly when the top-layer concrete is to be paved as a thin layer."The sophisticated proportional control system which has proved its value over many years is another quality feature of concrete paving with the SP 1500. The machine operator can see all the parameters required for the paving process on the main control panel. The control system then adapts the height quickly and precisely without overshooting. This results in level roadways – a quality feature which ensures driving comfort and also helps to reduce noise, as recent studies have shown.
Curing with the TCM 1800
Curing is a further aspect of great importance when paving exposed aggregate concrete. The TCM, Wirtgen's texture curing machine, can be fitted with brooms or combs to give the concrete a defined texture. This is unnecessary when placing exposed aggregate concrete.In this case, a combination of surface retarding agent and dispersion is applied to the finished and smoothed surface in precisely metered quantities. The retarding agent delays the setting and initial hardening of the concrete surface (approx. 1 mm) for a limited time, while the dispersion prevents the concrete surface from drying out and cracking. As soon as the concrete has cured sufficiently to be driven over, the surface is brushed to expose the coarse aggregate. An additional dispersion is then applied to the brushed surface. Exposing the coarse aggregate gives the concrete pavement the required non-skid properties which are subsequently of high importance for traffic safety.
Different paving kits can be used
The SP 1500 from Wirtgen is an exceedingly variable slipform paver which can be used to meet very different road construction requirements. Take the paving kits, for instance. In three of the projects, the roadway was freely produced by slipform paving on the subbase. On the A5, the first part was also produced in this manner, but then after 1 km, the roadway had to be tied in to pre-installed slot channels. The Bickhardt Bau team converted the hydraulic side header in no time at all as the work continued non-stop. The SP 1500 owes its flexibility to the fact that Wirtgen developed it as a modular system with intelligent interfaces.Flexible paving width
This modularity also gives users of the SP 1500 maximum flexibility as regards the paving width. On the A1, for example, Berger Bau paved an 11.50 m-wide roadway. On the A5 near Karlsruhe-Durlach, Bickhardt Bau used the SP 1500 to pave sections measuring 12.50 m and 15.00 m in width, while Max Bögl paved a three-lane concrete roadway 15.00 m wide, including the hard shoulder. Eurovia Beton extended the SP 1500 to its maximum width on the A1 near Lübeck, where a width of fully 15.25 m was required.Optionally with two or four crawler tracks
The SP 1500 is available from Wirtgen as a two-crawler and as a four-crawler model. Michael Niedermaier, Site Supervisor for Concrete Road Construction at Berger Bau, explains why he chose the version with four crawler tracks: "In Germany, tenders are invited for several small construction lots. Our SP 1500 therefore frequently needs to be relocated and transported, and this is where a four-crawler machine delivers the necessary flexibility. Compared to two-crawler versions, such machines are also easier to relocate in a longitudinal direction at the end of the concreting work, for instance above structures."This is confirmed by Jörg Ackermann, Paving Foreman at Bickhardt Bau: "The SP 1500 was needed on different sections here on the A5. The paver also had to be moved across bridges. The very narrow transport width is a great aid, as it allows the machine to be relocated rapidly, with little assembly and disassembly effort."
Christoph Hofmeister from Max Bögl mentioned two further points in favor of the four-crawler machines: "In a four-crawler bottom-layer paver, the dowel bar inserter is located between the crawler tracks. As a result, it can be monitored and reached more easily. Last but not least, the top-layer paver, in particular, displays greater stability as a four-crawler model because the geometry of the swivel arms results in a more advantageous lever spacing and an optimum balance of forces and torsion."
In addition, Wirtgen offers numerous optional extras with which contractors can individually configure their specific SP 1500. Eurovia Beton, for instance, equipped its top-layer paver with cameras which ensure that the paver operator always has a clear view of the finished concrete.
The vibrators also come in several different versions. To compact the top-layer concrete, for instance, three of the contractors chose electric T-vibrators which are particularly suitable for paving thin layers. Bickhardt Bau preferred a different solution and uses vibrating frames with external vibrators.
Intelligent high-performance machine
Regardless of the individual pavers' equipment configuration, all four contractors achieved daily outputs of 550 m in single-shift operation and up to 1,100 m in 24-hour operation, depending on the paving width and layer thickness. Jörg Ackermann, Paving Foreman at Bickhardt Bau, who has worked in concrete construction for 25 years, used a celestial image to describe this remarkable performance: "This paving method can be compared to a planetary gear: it has many parts, all of which are important to the successful functioning of the whole, but the Wirtgen paver sets the pace. It is our sun gear." Berger Bau | Bickhardt | Max Bögl | Eurovia | ||
---|---|---|---|---|---|
Highway | A1 near Trier | A5 near Karlsruhe-Durlach | A9 near Weissenfels | A1 near Lübeck | |
Length | 4,5 km | 2,3 km | 4,8 km | 5,3 km
| |
Width | 11,50 m | 12.50 m / 15.00 m | 15,00 m | 15,25 m | |
Subbase | 10 cm asphalt TS | 20 cm stabilization, non-woven material for bridging cracks | Stabilized layer, 30 cm gravel TS, 20 cm asphalt TS | Stabilization, 20 cm, placed by bottom-layer paver, compacted by compactors | |
Bottom-layer concrete, thickness | 20 cm | 22 cm | 24 cm | 22 cm | |
Bottom-layer concrete, grade | C30 / 37 | C 30 / 37 | C 30 / 37 | C 30 / 37 | |
Bottom-layer concrete, maximum aggregate size | 0/22 | 0/32 | 0/22 | 0/32 | |
Top-layer concrete, thickness | 6 cm | 5 cm | 5 cm | 5 cm | |
Top-layer concrete, grade | C 30 / 37 | C 30 / 37 | C 30 / 37 | C 30 / 37 | |
Top layer concrete, maximum aggregate size | 0/8 | 0/8 | 0/8 | 0/8 | |
Approx. paving rate | 500 m per shift | 1,100 m per 24h | 550 m per shift | 450 m per shift |
For further information please contact:
WIRTGEN GmbHCorporate Communications
Michaela Adams, Mario Linnemann
Reinhard-Wirtgen-Straße 2
53578 Windhagen
Germany
Phone: +49 (0) 2645 131 – 0
Fax: +49 (0) 2645 131 – 499
E-mail: %$Linker:
%$Linker: