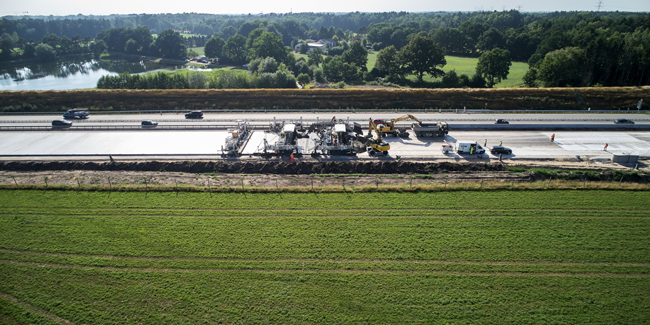
For widening the 60km stretch in the Schleswig-Holstein region, consortium Via Solutions Nord and joint venture
Meanwhile, contractor BT Beton-Technik was commissioned with the job. The company, which has specialised in concrete pavement construction for many years, has been relying on technologies and machines from
Dowel bars were inserted into the fresh, pre-compacted bottom-layer concrete at 25cm intervals and parallel to the direction of travel. Tie bars were inserted transverse to the pavement. The top-layer concrete was simultaneously loaded by excavator into the receiving hopper of the belt conveyor, transported over the top of the first SP 1500 and deposited directly on the bottom-layer concrete in front of the second SP 1500.
The second machine compacted the material by means of 29 electric T-vibrators, as they are known, while paving it in a 5cm-thick layer. In this way, the duo from Wirtgen paved around 4,000m³ of concrete each day.
The retarder enables the surface mortar to be swept off, exposing the high-grade broken aggregate in the top-layer concrete. Depending on weather conditions, this can be done around four hours or more after paving. This gives the concrete pavement the required peak-to-valley depth and lasting grip. A curing agent is once again sprayed over the exposed aggregate.
Unlike in the process selected for the A7 in other countries, a
Meander spraying is a special option. This method permits transverse spraying during uninterrupted travel. What is more, Wirtgen are continually advancing the associated components to ensure an optimum surface texture. The brush-cleaning unit of the TCM 180i is one prime example.
Cleaning the spray systems of curing machines economically is something of a challenge. With this in mind, Wirtgen has integrated into the TCM 180i a hot-water system with a 90-litre tank. With this system, any amounts of curing agent adhering to the inside of the pipes can be completely removed with water up to 60°C. The entire spray system is quickly and reliably cleaned – all at the push of a button and by shifting two ball cocks.
The hot water system has impressed Deni Pokrajcic, site manager BT Beton-Technik. “Wirtgen have struck gold with the new hot-water system of the TCM 180i. This added practical benefit will be a great asset to us in the future, too.”